Il primo processo di montaggio industriale basato su misure laser
Tecniche di assemblaggio futuristiche per l'AIRBUS A380
Contattateci

L’Airbus A380 è l’aero di linea più moderno, spazioso e capace di tutti i tempi. Sviluppato in cooperazione con i principali vettori aerei, aeroporti, ed autorità del traffico aereo internazionali, è stato ufficialmente presentato nel dicembre 2000, guadagnandosi subito l’appellativo di “Nave ammiraglia volante del XXI secolo”.
L’Airbus A380 viene prodotto con l’ausilio delle tecnologie più avanzate in termini di materiali, sistemi e processi industriali, tutto nel rispetto dei più rigorosi standard internazionali. Alla sua progettazione e costruzione concorrono i siti europei della Airbus Industries in Francia, Germania, Regno Unito e Spagna.
Nello stabilimento Jean-Luc Lagardère a Tolosa, appositamente costruito per la produzione dell’A380, viene completato l’assemblaggio finale dell’aereo. Lo stabilimento è articolato in tre unità operative. Una prima unità assembla le parti strutturali dell’aereo; la seconda unità esegue tutti i test sulla carlinga assiemata ed installa i sistemi di propulsione; infine la terza unità conduce i test all’aperto che preparano l’aereo per il suo primo volo.
Grazie alle prestazioni ed all’affidabilità dei Laser della Leica Geosystems, l’assemblaggio dell’intero aereo sulla base delle indicazioni fornite dalle misure laser si presenta come un processo tecnologicamente maturo, che può essere applicato con successo ad altri programmi all’interno della nostra organizzazione.La filosofia di base dell’innovativa procedura di assemblaggio adottata per la struttura dell’A340 consiste nella verifica geometrica diretta, che implica il controllo funzionale dei suoi singoli segmenti in accoppiamento fisico, cioè l’uno rispetto all’altro. Si tratta di una procedura alternativa rispetto al confronto dei singoli componenti eseguita all’interno di un sistema di riferimento esterno definito attraverso l’impiego di attrezzi di misura convenzionali. Questa filosofia permette tra l’altro di aggirare il problema della gestione di tolleranze incrociate e composte. Un ulteriore problema da risolvere concerneva la messa a punto di una soluzione operativa efficiente finalizzata all’accoppiamento di componenti caratterizzati da interfacce fisiche complesse, quali la fusoliera di forma ovale e la carlinga a due piani. Viste le problematiche tecnologiche implicite nel progetto A380, dirigenti responsabili del programma scelsero una filosofia di montaggio basata su misure con il laser.
Thierry Fabre, responsabile della metrologia a laser presso il sito di Tolosa, spiega: “La sfida rappresentata dall’esigenza di affrontare e risolvere in modo ottimale i problemi posti da queste complesse operazioni era andata molto al di là della soluzione delle problematiche di un processo di montaggio di tipo tradizionale. Avevamo bisogno di individuare un sistema di riferimento fisico comune per l’intero aereo applicabile ed utilizzabile da tutti i siti europei della Airbus Industries. I diversi siti adottavano infatti correntemente metodi di lavoro diversi, caratterizzati da standard operativi, obiettivi, e vincoli specifici. Si imponeva quindi la definizione di una fase preparatoria, fondamentale al fine di assicurare che i dati provenienti dai vari siti fossero congruenti e chiari gli uni per gli altri.”
Martial Charraud, che aveva precedentemente già lavorato nei siti di Nantes (RCT) e di Tolosa (A320), fa parte del team di Thierry Fabre per l’A380.
“I primi progetti relativi al montaggio della fusioliera dell’Airbus con il supporto di misure eseguite con il laser”, spiega Charraud, “ sono stati condotti in stretta collaborazione con la sede di Leica Geosystems in Svizzera. Considerati i risultati molto positivi ottenuti, abbiamo ovviamente deciso di rivolgerci ancora alla Leica Geosystems per la messa a punto di soluzioni operative ottimali focalizzate sui processi di assemblaggio dell’A380. Il nostro obiettivo era di mettere a frutto le esperienze precedenti maturate nella collaborazione con questa società e di applicarle al nuovo importante progetto. Inoltre devo dire che, conoscendo già molto bene i prodotti Leica Geosystems, sapevo di poter contare fin dall’inizio sulla assoluta affidabilità e funzionalità delle soluzioni che avremmo adottate.”
E’ previsto che la linea di montaggio dell’A380 rimanga in funzione per un periodo di circa 30 - 40 anni. Questa considerazione rende tanto più importante scegliere partner affidabili di lungo periodo. I sistemi usati, e soprattutto il software di elaborazione ed il software dei processi di automazione, sono soggetti ad una rapida obsolescenza. “La possibilità e la facilità di manutenzione dei sistemi in uso, anche a distanza di tempo dalla loro installazione, sono considerazioni che vanno ben ponderate e che rivestono un’importanza decisiva” Aggiunge Fabre.” Su questa base abbiamo quindi definito un programma di cooperazione di lungo periodo con Leica Geosystems. L’obiettivo è di garantire che anche in presenza di condizioni ambientali difficili, i nostri strumenti continueranno a funzionare come da specifiche”.
L’Airbus A380 viene prodotto con l’ausilio delle tecnologie più avanzate in termini di materiali, sistemi e processi industriali, tutto nel rispetto dei più rigorosi standard internazionali. Alla sua progettazione e costruzione concorrono i siti europei della Airbus Industries in Francia, Germania, Regno Unito e Spagna.
Nello stabilimento Jean-Luc Lagardère a Tolosa, appositamente costruito per la produzione dell’A380, viene completato l’assemblaggio finale dell’aereo. Lo stabilimento è articolato in tre unità operative. Una prima unità assembla le parti strutturali dell’aereo; la seconda unità esegue tutti i test sulla carlinga assiemata ed installa i sistemi di propulsione; infine la terza unità conduce i test all’aperto che preparano l’aereo per il suo primo volo.
Nuove tecnologie avanzate per il montaggio della struttura
La stazione 40 della prima unità esegue il montaggio finale dell’aereo (segmenti di carlinga ed ali). I singoli elementi vengono preventivamente confrontati fra loro per verificarne la compatibilità in sede di assemblaggio: in questa fase un esame completo e rigoroso delle caratteristiche geometriche dei singoli pezzi che compongono la struttura è di vitale importanza. Lo studio del processo di montaggio dell’A380 è iniziato nel 1998 ed ha implicato la risoluzione di numerosi problemi operativi principalmente determinati dalle dimensioni eccezionali dei singoli segmenti della fusoliera, dalla sezione ovale della carlinga (che normalmente è circolare sugli altri aerei), dalla struttura a due piani, e da altre caratteristiche funzionali dell’aeromobile. Un ulteriore problema da risolvere è stato poi quello dello sviluppo e della gestione fisica delle numerose complesse attrezzature che concorrono al montaggio finale dell’A340. Questi sofisticati strumenti che garantiscono il posizionamento corretto dei diversi segmenti dell’aereo nello spazio devono essere messi a punto con altissima precisione, e le loro caratteristiche geometriche e funzionali devono essere rigorosamente verificate con continuità.Grazie alle prestazioni ed all’affidabilità dei Laser della Leica Geosystems, l’assemblaggio dell’intero aereo sulla base delle indicazioni fornite dalle misure laser si presenta come un processo tecnologicamente maturo, che può essere applicato con successo ad altri programmi all’interno della nostra organizzazione.La filosofia di base dell’innovativa procedura di assemblaggio adottata per la struttura dell’A340 consiste nella verifica geometrica diretta, che implica il controllo funzionale dei suoi singoli segmenti in accoppiamento fisico, cioè l’uno rispetto all’altro. Si tratta di una procedura alternativa rispetto al confronto dei singoli componenti eseguita all’interno di un sistema di riferimento esterno definito attraverso l’impiego di attrezzi di misura convenzionali. Questa filosofia permette tra l’altro di aggirare il problema della gestione di tolleranze incrociate e composte. Un ulteriore problema da risolvere concerneva la messa a punto di una soluzione operativa efficiente finalizzata all’accoppiamento di componenti caratterizzati da interfacce fisiche complesse, quali la fusoliera di forma ovale e la carlinga a due piani. Viste le problematiche tecnologiche implicite nel progetto A380, dirigenti responsabili del programma scelsero una filosofia di montaggio basata su misure con il laser.
Thierry Fabre, responsabile della metrologia a laser presso il sito di Tolosa, spiega: “La sfida rappresentata dall’esigenza di affrontare e risolvere in modo ottimale i problemi posti da queste complesse operazioni era andata molto al di là della soluzione delle problematiche di un processo di montaggio di tipo tradizionale. Avevamo bisogno di individuare un sistema di riferimento fisico comune per l’intero aereo applicabile ed utilizzabile da tutti i siti europei della Airbus Industries. I diversi siti adottavano infatti correntemente metodi di lavoro diversi, caratterizzati da standard operativi, obiettivi, e vincoli specifici. Si imponeva quindi la definizione di una fase preparatoria, fondamentale al fine di assicurare che i dati provenienti dai vari siti fossero congruenti e chiari gli uni per gli altri.”
La scelta di Leica Geosystems: il passo logico
Numerose soluzioni basate sull’applicazione della tecnologia Laser Tracker di Leica Geosystems erano già state adottate con successo in processi produttivi avviati in vari siti Airbus, sia in Francia (RCT a Nantes, Erebus a Meaulte, la stazione di montaggio 15/21 a St. Nazaire, la misura delle interfacce tra i segmenti di carlinga nel progetto A320 a Tolosa), come pure a Brema in Germania ed a Broughton e Filton nel Regno Unito.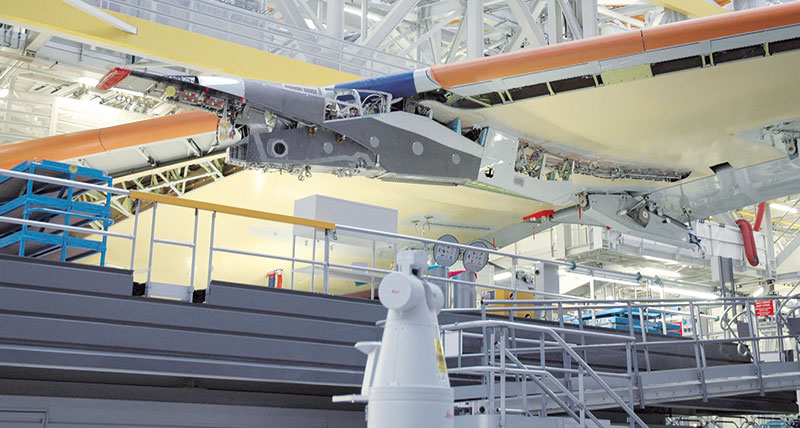
“I primi progetti relativi al montaggio della fusioliera dell’Airbus con il supporto di misure eseguite con il laser”, spiega Charraud, “ sono stati condotti in stretta collaborazione con la sede di Leica Geosystems in Svizzera. Considerati i risultati molto positivi ottenuti, abbiamo ovviamente deciso di rivolgerci ancora alla Leica Geosystems per la messa a punto di soluzioni operative ottimali focalizzate sui processi di assemblaggio dell’A380. Il nostro obiettivo era di mettere a frutto le esperienze precedenti maturate nella collaborazione con questa società e di applicarle al nuovo importante progetto. Inoltre devo dire che, conoscendo già molto bene i prodotti Leica Geosystems, sapevo di poter contare fin dall’inizio sulla assoluta affidabilità e funzionalità delle soluzioni che avremmo adottate.”
E’ previsto che la linea di montaggio dell’A380 rimanga in funzione per un periodo di circa 30 - 40 anni. Questa considerazione rende tanto più importante scegliere partner affidabili di lungo periodo. I sistemi usati, e soprattutto il software di elaborazione ed il software dei processi di automazione, sono soggetti ad una rapida obsolescenza. “La possibilità e la facilità di manutenzione dei sistemi in uso, anche a distanza di tempo dalla loro installazione, sono considerazioni che vanno ben ponderate e che rivestono un’importanza decisiva” Aggiunge Fabre.” Su questa base abbiamo quindi definito un programma di cooperazione di lungo periodo con Leica Geosystems. L’obiettivo è di garantire che anche in presenza di condizioni ambientali difficili, i nostri strumenti continueranno a funzionare come da specifiche”.
Pre-definizione dei percorsi ottici
Dopo aver installato gli strumenti ed aver definito i metodi di messa a punto, con il supporto di un software CAD, si è proceduto ad analizzare con molta precisione il percorso ottico del laser tracker lungo l’intero suo sviluppo. A causa dell’elevato numero di piattaforme e di strutture che compongono la linea di montaggio, era infatti molto difficile garantire l’effettiva continuità di un percorso ottico ininterrotto tra i vari punti di misura ed il laser tracker. “Abbiamo quindi dovuto sviluppare un approccio affidabile che ci consentisse di determinare il numero di laser tracker necessari e la posizione ottimale di ciascuno. É stato un processo particolarmente delicato e difficile”, continua Charraud.La soluzione ottimale: quattro Laser Tracker di Leica Geosystems
Sono stati quindi scelti quattro Laser Tracker Leica: due per la fusoliera e due per le ali. I quattro laser tracker sono collegati tra loro e interagiscono con un sistema di coordinate comune. Questa disposizione garantisce l’uniformità e l’intercambiabilità dei laser tracker. Il software di misura e di controllo sviluppato appositamente per l’applicazione, si interfaccia con il software EmScon della Leica Geosystems, la quale ha contributo anche alla fase di sviluppo delle specifiche. “Il supporto che abbiamo ricevuto dalla Leica Geosystems si è rivelato determinante ed ha permesso di garantire l’assoluta compatibilità del software ed il corretto utilizzo delle funzioni necessarie”, aggiunge Charraud.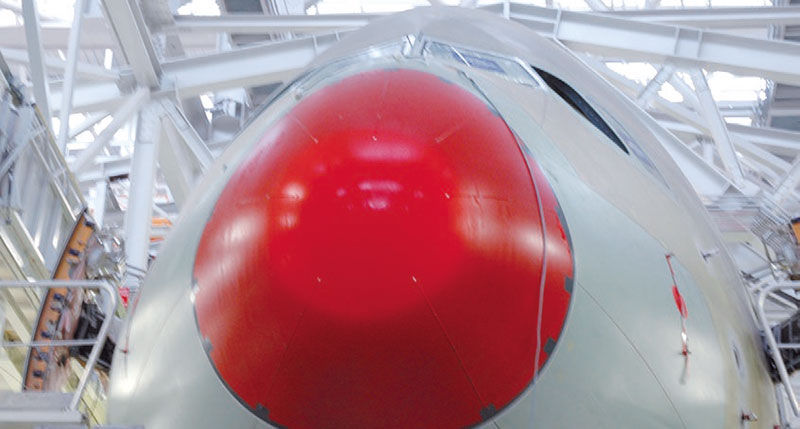