モデルベースの測定で品質保証に多大な恩恵を
検査計画立案はMBD and GD&Tで大いに強化
お問い合わせ先
3D CADの長い進化の歴史で、現時点から革命的な進歩が可能とは考えにくいでしょう。モデルベースの測定、またはMBDを採用してください。ソフトウェア開発者と航空宇宙業界で長い間検討し尽くされた用語と方法論です。驚くべきことにこの分野では、活用が著しく、この技術は本物の数値を製造テーブルにもたらすことができます。
MBD “ゴールド”は、製品開発を合理化し、完全に定義し、部品と組み立ての仕様を提供する情報満載の3D CADモデルをべースに、図面なしの工程を構築する能力です。製品デザインへの次世代のアプローチは、製造作業の簡素化から検査工程の大幅な向上まで、時間とコスト削減の多くの派生効果があります。
MBD検査
設計と製造会社がますます、ソリッドとサ-フェスモデル技術を進んで利用する中、 3D CAD への移行は、近年加速しています。しかし3D モデルは、GD&T (幾何公差) 情報が欠けていました。よって部品の許容差に関して予測できないものでした。加えて、オリジナルデザインの意図のどんな変更も、時には何度も細部を変更、個々の変更は貴重な時間を費やし、エラーの要因を招くという、長い工程になってしまいました。これらの複雑さのすべてが、 品質検査係のデスクに舞い込んできます。
品質保証の世界では、典型的なCADモデルの一番の問題は、データ構造を決める別の設計図や、主要な特徴、検査プラン作成のための公差が必要なことです。このシナリオは、多国籍企業にとって必ずしも便宜を受ける訳でもないGD&Tの一部の理解をもとめ、製品デザイナーに、時折確認が必要なことです。
いくつかのCADソフトウェアが、内蔵のGD&Tに対応し、MBDはこの煩雑性の打開のために登場しました。関連するすべての製品情報と検査プラニングデータは、ひとつのバージョン管理可能な3D CADモデルに一体化されます。MPDは部品データ構造と改定レベルや、GD&T解釈、製品の詳細、その他のすべての必要寸法をモデルに統合します。品質保証の目的にはとても良い知らせです。
実際の利点
可能な事の感覚を得るには、情報満載のCADモデルの固有の利点を研究することは価値があります。まず第一に、MBDは初めてデザインと品質の正式な通信手段を、プリントの必要性なしで提供します。よって部品のプログラム作成時に、デザインの移行が自動的に判ります。CAD ソフトウェアツールで、部品メーカーは、シングルのCADファイルと与えられた部品の組み立てと検査を受け取ることができます。
二つ目に、MBDは検査ソフトの中に注記を転送することにより、ヒューマンエラーを解決します。GD&Tや部品票、その他の技術的構成などの書類の供給に、従来的な2D図面の仕様は、この情報の解釈でのヒューマンのエラーの内在的リスクに会社は直面してきました。モデルベースの測定は、ペーパレス検査に納得できる意義を提示して、定義や、部品や製品組み立ての供給には3Dデジタルデータのみに依存しています。
最後に、そして一番意義深く、MBDは3Dデザイン情報から直接、部品プログラム作成の自動かメカニズムを届けます。デザインの修正があれば、検査プログラムもかわります、そして依存状態も更新されます。ひとつの形状の公差が変更になれば、プログラムはすべての関係する形状の更新をします。この機能は特に込み入った形状の場合、貴重な時間削減機能です。例えば、同じ公差の80の穴のある部品で仕様が変わる場合、クリックだけでただちに追加のオペレータの介在なく、関係するすべての寸法を更新します。
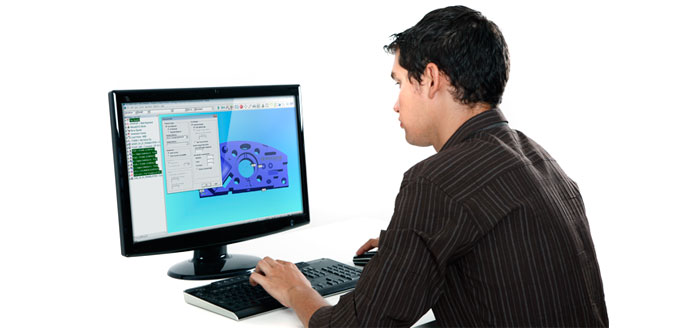
PC上で管理するPC-DMIS
進歩の自然な配列で、二三のCADベースの検査ソフトウェアがMBDとペースを合わせ、新しい内蔵のGD&Tデータの特権を独占しています。システムによっては、一回のマウスクリックで、形状や、データの定義、関連寸法を作成する基本機能があります。Hexagon Metrologyによって開発された検査ソフトウェアのPC-DMIS Plannerは、デザイン変更や内蔵GD&Tに基づく検査工程を自動化することで、一歩先を行きます。このソフトウェアはフルとサブの検査プログラムを作成します。そして中間機器であるプログラムを使用している間、すべての修正を制御します。利用の測定技術、例えば、接触やスキャン、連続アナログ、視覚、レーザーに関係なく使用できます。
この検査ソフトウェアが動的にCADにリンクされる場合、変更マネジャー機能が品質技術者にCADへの更新や変更を一報します。これらの変更は、必要な変更を一体化する一番効果的なルートに基づいた検査パスを自動的に修正するソフトウェアで、受け取り拒否もできます。形状や寸法の検査ルーチンは、測定効率に重点を置いて自動的に生成されますが、ユーザーは要望に合わせた測定レポートのカスタマイズを簡単にできます。
PC-DMIS Screenshots CADデータをインポートして、形状コントロールフレーム、または他の直線的寸法を3Dモデルから選択するのは単純なプロセスです。選択された個々の寸法は、検査員の解釈を排除し、デザイナーの意図に基づいた検査プランに対する 最新の形状と公差を加えます。最高レベルの測定受容精度を確実にするため、ソフトウェアは、ASME Y14.5 – 1994, ASME Y14.5 – 2009 および ISO 規格用のPTB認定アルゴリズムを使用します。 これは始めのプランが作成された時に、自動的に行われます。検査のソフトウェア、さらに複数の形状コントロールに参照される共通データ形状は、精度を保ちつつ検査時間の効率を保持する検査ルーチンでは複製されないことを確実にします。処理量と精度を確実にすることは、常に品質技師の責任でしたので、これはプロセスにおけるパラダイムシフトです。

PC-DMIS Plannerツールで、測定パスは自動的に最適化されます。ソフトウェアグループは、近接とプロービングアングルで、プローブの回転とチップの変更を最小限にし、形状を検査しました。複数測定プラン初期設定パラメータは、多様な顧客と内部検査要求にたいする取得点数と位置を明確にするため、検査員によって設定できます。また、ひとたびプランがインポートされると、PC-DMISのリアルタイムの機能性は、稼働中に変更して、測定プランを踏み込むか、あるいは心配な部位や主要な特徴部位のスポット編集のために利用できます。ほとんどの検査ルーチンはこのアプローチの採用で、処理量の30%増加が見られるでしょう。他のものは50%の増加を獲得できます。
効率は速度と一致し、速度は安全を要求します。もう一つのソフトウェアの進化は、PC-DMISモデルの本来的な境界ボックスを活用します。円形で不規則な形の部品(例えばタービンブレード、ハンドル制御アーム、人工装具/インプラントなど)境界ボックス内にも収納されます。この”力場“ がPC-DMISで稼働されると、進化したアルゴリズムがプローブチップを方向付けして、自動的に部品をクリアします。これはプローブが次の形状に移動前あるいは、プローブヘッド回転が完了する前に、安全に部品と固定具を避けることが必要です。
MBD – 何処に向かうのか?
3D情報の停止不能力を使用して、 MBD は、完全潜在能力に達する道を継続しています。会社は、製品開発工程の向上に自社のCADモデルを利用できます。それと同時に、MBDをフル活用するために、強化した検査ソフトを通じて品質保証の進歩を獲得できます。 CADモデル内に、すべての関連情報を組み込むことにより、企業は時間の節約とヒューマンエラーの潜在要因の削減を期待すべきです。
MBDは、変更や修正に関わるつらい仕事のいくつかを引き受けて、検査員のワークロードの削減を請け合います。検査員は計測の最善策や、固定具、顧客の要望、GD&Tの適用の専門知識を活用することにより、結果の操作をする必要がまだありますが、修正に対応する検査ルーチンの調整に費やされる時間の大半を、ソフトウェアに任せることで緩和されます。
ますます多くの会社がMBDという金鉱を発見し、品質保証部門は、生産性の向上を実現します。加えて、部品と組みたてのオリジナルの設計意図を、保持する傾向がさらに強くなります。このプロセス全体で品質技師が苦労することなく、部品検査の効率化をしている世界は想像に難くありません。