Scansione
I professionisti della metrologia industriale sono alla continua ricerca del metodo migliore per verificare i componenti prodotti.
Contattateci
I professionisti della metrologia industriale sono alla continua ricerca del metodo migliore per verificare i componenti prodotti. Quando si effettuano ricerche nell'ambito delle macchine di misura a coordinate (CMM) o si valutano le capability di macchine esistenti, la discussione volge naturalmente sugli accessori che completeranno la CMM. Esistono diverse soluzioni, ciascuna con i suoi lati positivi e negativi. La scelta migliore consiste nel trovare l'opzione giusta che non sia né eccessiva né insufficiente.
Quando si misurano componenti di dimensioni medio-piccole, vi sono quattro categorie di accessori di misura. La prima è quella dei tastatori a contatto che rilevano punti discreti sul componente. La seconda è quella dei sensori di scansione analogici che scorrono sulla superficie del componente rilevando migliaia di singoli punti. Gli scanner laser 3D impiegano un fascio laser per rilevare migliaia o addirittura milioni di punti su di una superficie. Infine i sensori cromatici a luce bianca (CWS) eseguono una verifica non-contatto di alta precisione.
Quando si deve decidere se scansionare un componente si tende naturalmente a scegliere la scansione analogica, in grado di rilevare una gran quantità di dati 3D di alta precisione con facilità di accesso alla maggior parte delle aree. È ideale anche perché con maggior probabilità riesce a rilevare tutte le caratteristiche critiche. L'impiego della scansione analogica migliora la ripetibilità dei risultati riducendo l'incertezza di misura. Nella realtà, però, la decisione di scansionare o no un componente è più complessa e dipende dall'applicazione.
Inoltre quando si valuta il processo, si dovrebbe considerare l'uso del componente. Un connettore di plastica per componenti automotive come quello illustrato qui sopra richiede una chiusura ermetica per escludere la possibilità di infiltrazione dell'acqua. Sebbene il connettore abbia caratteristiche semplici che possono essere facilmente rilevate a contatto, il bordo in cui forma la chiusura avrà probabilmente tolleranze più strette che richiederanno la scansione analogica.
Un professionista della misura esperto esaminerà il processo di produzione dall'inizio alla fine per determinare l'approccio migliore. Illustriamo qui una pistola sparachiodi che ha alcune caratteristiche interessanti sul componente pressofuso originale. Vi sono inoltre dei processi di lavorazione di cui tener conto quando si deve decidere se scansionare. Su questo componente particolare, l'azienda può controllare il profilo dell'alloggiamento in alluminio pressofuso con la scansione laser 3D. Quando si controllano altre caratteristiche, soprattutto quelle localizzate sotto la superficie del componente, è opportuno eseguire la scansione analogica o anche il rilevamento a contatto. Un'altra caratteristica da controllare è rappresentata dalle superfici di accoppiamento del componente. Poiché ci potrebbe essere un problema di accoppiamento, su queste superfici la scansione analogica potrebbe essere una scelta migliore.
Quando si misurano componenti di dimensioni medio-piccole, vi sono quattro categorie di accessori di misura. La prima è quella dei tastatori a contatto che rilevano punti discreti sul componente. La seconda è quella dei sensori di scansione analogici che scorrono sulla superficie del componente rilevando migliaia di singoli punti. Gli scanner laser 3D impiegano un fascio laser per rilevare migliaia o addirittura milioni di punti su di una superficie. Infine i sensori cromatici a luce bianca (CWS) eseguono una verifica non-contatto di alta precisione.
Quando si deve decidere se scansionare un componente si tende naturalmente a scegliere la scansione analogica, in grado di rilevare una gran quantità di dati 3D di alta precisione con facilità di accesso alla maggior parte delle aree. È ideale anche perché con maggior probabilità riesce a rilevare tutte le caratteristiche critiche. L'impiego della scansione analogica migliora la ripetibilità dei risultati riducendo l'incertezza di misura. Nella realtà, però, la decisione di scansionare o no un componente è più complessa e dipende dall'applicazione.
Che cosa potrebbe non funzionare?
Il primo passo nella valutazione delle tecniche di verifica consiste nell'esaminare il processo di produzione nel suo insieme e pensare a che cosa potrebbe andare storto. Se il componente ad esempio è in plastica, esiste un'area più spessa soggetta a cedimento quando il materiale si raffredda e si assesta. Se la risposta è sì, e si tratta di un elemento critico con tolleranze ristrette, dovrebbe essere scansionato. Se l'elemento non è critico e ha tolleranze blande, è probabile che il rilevamento a contatto sia sufficiente.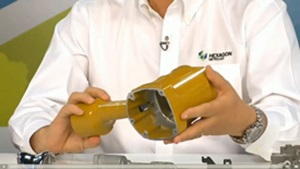
Inoltre quando si valuta il processo, si dovrebbe considerare l'uso del componente. Un connettore di plastica per componenti automotive come quello illustrato qui sopra richiede una chiusura ermetica per escludere la possibilità di infiltrazione dell'acqua. Sebbene il connettore abbia caratteristiche semplici che possono essere facilmente rilevate a contatto, il bordo in cui forma la chiusura avrà probabilmente tolleranze più strette che richiederanno la scansione analogica.
Un professionista della misura esperto esaminerà il processo di produzione dall'inizio alla fine per determinare l'approccio migliore. Illustriamo qui una pistola sparachiodi che ha alcune caratteristiche interessanti sul componente pressofuso originale. Vi sono inoltre dei processi di lavorazione di cui tener conto quando si deve decidere se scansionare. Su questo componente particolare, l'azienda può controllare il profilo dell'alloggiamento in alluminio pressofuso con la scansione laser 3D. Quando si controllano altre caratteristiche, soprattutto quelle localizzate sotto la superficie del componente, è opportuno eseguire la scansione analogica o anche il rilevamento a contatto. Un'altra caratteristica da controllare è rappresentata dalle superfici di accoppiamento del componente. Poiché ci potrebbe essere un problema di accoppiamento, su queste superfici la scansione analogica potrebbe essere una scelta migliore.
Quali sono le tolleranze?
Come menzionato in precedenza, la tolleranza per un determinato valore teorico avrà un ruolo nella determinazione del metodo di verifica ideale. Sebbene la scansione laser abbia fatto parecchia strada dalla sua comparsa, è tuttora relativamente carente in termini di precisione se paragonato ad altri metodi. Non si dovrebbe impiegare la scansione laser quando le tolleranze sono più strette di ± 0,01” ma questa è ideale per tolleranze più ampie su componenti con numerose superfici delimitate da profili. Il rilevamento punto a punto offre maggiore precisione ma ha minore ripetibilità se paragonato a sensori di scansione analogica. La scansione analogica è considerata il metodo più preciso di verifica di un componente e può rispettare tolleranze fino a ± 0,0005”. I sensori cromatici a luce bianca (CWS) sono un metodo di verifica non a contatto di alta precisione che ha la capacità di misurare fino a 10 millesimi di micron. I CWS vengono usati per caratteristiche troppo piccole per essere misurate con un tastatore a contatto o per oggetti flessibili che richiedono la misura non-contatto.
Nel caso di alcuni componenti medicali, ad esempio il femorale illustrato qui, la scansione analogica sarà l'opzione migliore. Questo è dovuto al fatto che il profilo dev'essere verificato con un alto livello di precisione. In alcuni casi, la scansione non-contatto con un CWS è preferibile se il componente non può essere toccato. Il CWS è ideale anche per superfici trasparenti e opache molto riflettenti.
All'altro capo dello spettro, alcuni componenti si prestano al rilevamento di punti discreti. Per un componente stampato con tolleranze ampie, in cui la forma non sia un problema e sia necessario rilevare il profilo e le posizioni dei fori, sarà particolarmente adatto il rilevamento punto a punto. Anche se il componente può avere più elementi, la scansione è eccessiva e dispendiosa in termini di tempo.
Alcuni componenti potrebbero avere diverse indicazioni di tolleranza con una gran varietà di requisiti da verificare. In questo esempio, una CMM multisensore sarebbe la scelta ideale poiché i componenti potrebbero essere misurati con diversi sensori all'interno dello stesso programma. Ad esempio sulla piastra superiore stampata di una trasmissione automatica che vediamo di seguito vi sono caratteristiche lavorate con fori di tolleranze generali. Internamente però vi sono caratteristiche di alta precisione. Per la varietà di elementi sul componente, la fusione iniziale potrebbe essere sottoposta a scansione laser quando la si riceve dal fornitore. Dopo la lavorazione, si consiglia la scansione analogica della faccia perché è molto probabile che ci siano indicazioni di tolleranza molto strette per ottenere l'isolamento della trasmissione. Anche i fori potrebbero essere scansionati o, a seconda delle loro tolleranze, rilevati a contatto per risparmiare tempo.
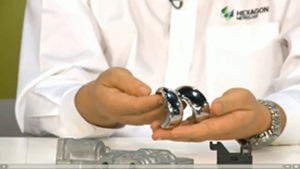
Nel caso di alcuni componenti medicali, ad esempio il femorale illustrato qui, la scansione analogica sarà l'opzione migliore. Questo è dovuto al fatto che il profilo dev'essere verificato con un alto livello di precisione. In alcuni casi, la scansione non-contatto con un CWS è preferibile se il componente non può essere toccato. Il CWS è ideale anche per superfici trasparenti e opache molto riflettenti.
All'altro capo dello spettro, alcuni componenti si prestano al rilevamento di punti discreti. Per un componente stampato con tolleranze ampie, in cui la forma non sia un problema e sia necessario rilevare il profilo e le posizioni dei fori, sarà particolarmente adatto il rilevamento punto a punto. Anche se il componente può avere più elementi, la scansione è eccessiva e dispendiosa in termini di tempo.
Alcuni componenti potrebbero avere diverse indicazioni di tolleranza con una gran varietà di requisiti da verificare. In questo esempio, una CMM multisensore sarebbe la scelta ideale poiché i componenti potrebbero essere misurati con diversi sensori all'interno dello stesso programma. Ad esempio sulla piastra superiore stampata di una trasmissione automatica che vediamo di seguito vi sono caratteristiche lavorate con fori di tolleranze generali. Internamente però vi sono caratteristiche di alta precisione. Per la varietà di elementi sul componente, la fusione iniziale potrebbe essere sottoposta a scansione laser quando la si riceve dal fornitore. Dopo la lavorazione, si consiglia la scansione analogica della faccia perché è molto probabile che ci siano indicazioni di tolleranza molto strette per ottenere l'isolamento della trasmissione. Anche i fori potrebbero essere scansionati o, a seconda delle loro tolleranze, rilevati a contatto per risparmiare tempo.
Pennello o penna?
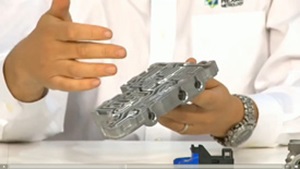
Raccogliere dati in modo rapido e preciso è un'ottima caratteristica ma non ci sono vantaggi a meno che vengano presentati in modo comprensibile. Attualmente la tendenza è a favore dell'impiego della scansione laser perché è rapida, piuttosto precisa e tutti gli elementi richiesti vengono rilevati contemporaneamente. Questa capacità tuttavia può non essere sufficiente per rilevare i dati necessari su caratteristiche critiche.
Rilevati i dati, si presenta il problema della loro gestione, cioè come utilizzarli. L'obiettivo è quello di paragonare semplicemente il componente fisico con il suo modello CAD? Se è così, quali sono le principali aree di interesse? Con un sensore laser si possono rilevare milioni di punti. Se con quei dati si intende conoscere l'aspetto del componente, l'azienda ha perso di vista il vero scopo della verifica degli elementi critici del componente stesso. In molti casi una quantità eccessiva di punti può essere uno svantaggio anziché un vantaggio, poiché sovraccarica il software e i processi di calcolo, o concentra inutilmente l'attenzione su aree non critiche.
Quanto costa?
La preoccupazione finale quando si esaminano diverse opzioni di rilevamento è il budget disponibile. C'è un motivo per il quale questo è l'ultimo fattore anziché essere il punto di partenza. L’utilizzatore dovrebbe prima identificare la migliore tecnologia per la sua applicazione. Poi dovrebbe analizzare i vantaggi e i risparmi relativi, e calcolare il ritorno previsto sull'investimento. Solo a questo punto si dovrebbe affrontare il fattore economico.
Scansione
Le aziende sono sempre alla ricerca della grande novità che permetta loro di ridurre i costi, aumentare la produzione o le vendite. Questo porta alcuni a seguire le tendenze nel settore e a saltare sul carro di ogni nuova tecnologia presentata. Solo perché lo fa la concorrenza, ciò non significa necessariamente che questo sia giusto per tutte le aziende. C'è una differenza tra il fare le cose e farle bene. Restringere la ricerca fino a identificare la scelta migliore richiede lavoro ma con la giusta lungimiranza e indagine, emerge la soluzione migliore.
Pronti per ottimizzare i tempi
Il passaggio del settore verso soluzioni di scansione 3D è dovuto parzialmente alla migliore produttività ma anche al modo in cui vengono creati i disegni costruttivi dei componenti. In passato i componenti venivano identificati con le dimensioni di larghezza e lunghezza. Oggi la vita dei prodotti continua a ridursi. L'iterazione di un componente esistente impiegando larghezza e lunghezza come dimensioni di riferimento è troppo complessa e richiede troppo tempo per la modifica. Quando l'intera forma del componente è controllata dal profilo, il tempo richiesto per cambiare il modello CAD cala drasticamente. Un componente che sia controllato dal profilo si presta anche a controlli del profilo GD&T integrati. La scansione è ideale quando la posizione degli elementi è contenuta nel profilo del componente.