Требуется сканирование?
Профессионалы промышленной метрологии постоянно заняты поиском наилучших методик инспекции деталей.
Свяжитесь с нами
Профессионалы промышленной метрологии постоянно заняты поиском наилучших методик инспекции деталей. При изучении характеристик координатно-измерительных машин (КИМ) или оценке возможностей существующего оборудования дискуссия естественным образом сворачивает к аксессуарам, входящих в комплект этих КИМ. Существует несколько решений -- каждое с присущими им достоинствами и недостатками. Секрет заключается в том, чтобы найти правильный вариант, который не будет ни излишним, ни недостаточным.
При измерении деталей малого и среднего размера имеется четыре основные категории аксессуаров для проведения инспекции. Первая -- это контактные датчики, позволяющие получать дискретные точки измеренных параметров детали. Вторая -- это датчики аналогового сканирования, способные двигаться вдоль поверхности детали, регистрируя одновременно тысячи отдельных точек. Трехмерные лазерные сканеры используют полосу, образованную лазерным лучом, с помощью которой регистрируются тысячи, или даже миллионы, точек на поверхности. И наконец, датчики хроматического белого света (CWS), обеспечивающие сверхточное бесконтактное измерение.
Столкнувшись с решением сканировать деталь, профессионалы-метрологи, естественным образом, склоняются к аналоговому сканированию, поскольку оно позволяет захватывать большое количество сверхточных трехмерных данных координат, обеспечивая при этом легкий доступ к большинству участков. Оно также считается идеальным, поскольку с большой степенью вероятности будут регистрироваться все критически важные характеристики. Использование аналогового сканирования улучшает повторяемость результатов с одновременным снижением неопределенности измерений. В действительности же, решение сканировать деталь имеет больше нюансов и зависит от конкретного случая применения.
Что может пойти не так?
При оценке технологии инспекции прежде всего необходимо окинуть взглядом весь производственный процесс и подумать о том, что потенциально может пойти не так. Например, если проверяемая деталь выполнена из пластика, нужно посмотреть, нет ли у нее толстых краев, которые имеют склонность к проседанию по мере остывания и затвердевания материала. Если ответ будет положительным, и если этот параметр должен иметь малые допуски, его следует сканировать. Если этот параметр не критический и требует невысокой точности, возможно, будет достаточно проверить его контактным датчиком.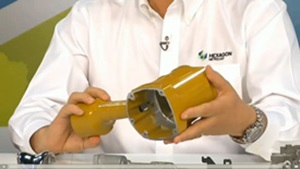
Корпус пневматического молотка из литого алюминия. Опытный метролог изучит производственный процесс от начала до конца, чтобы найти наилучший подход. На литой детали пневматического молотка имеется несколько интересных элементов, показанных здесь. Кроме того, существуют процессы механической обработки, которые оказывают влияние на решение, сканировать деталь или нет. В случае именно этой детали можно проверить ее профиль с помощью трехмерного сканирования литого алюминиевого корпуса. При проверке прочих параметров, особенно расположенных под поверхностью детали, будет достаточно аналоговое сканирование или даже контактное измерение. Другой проверяемой характеристикой является совмещение поверхностей детали. Поскольку при совмещении могут возникнуть проблемы, для этих поверхностей аналоговое сканирование, возможно, будет лучшим выбором.
Что такое допуски?
Как упоминалось ранее, допуски, требуемые для конкретного размера, играют роль при определении наиболее пригодного метода контроля. Хотя лазерное сканирование прошло долгий путь с момента своего возникновения, оно по-прежнему проигрывает в точности при сравнении с другими методами. Лазерное сканирование не следует использовать при допусках менее чем ± 0.01”, но оно идеально при более свободных допусках на деталях, имеющих множество поверхностей, контролируемых профилем. Контактные измерения дают более высокую точность, но имеют меньшую повторяемость в сравнении с датчиками аналогового сканирования. Аналоговое сканирование считается наиболее точным методом контроля; оно способно обеспечить допуски до ± 0.0005”. Датчики хроматического белого света (CWS) являются наиболее точными средствами бесконтактного измерения, имеющими возможность измерять с погрешностью до 10 нанометров. CWS используют для измерения параметров, которые невозможно измерить контактными датчиками, или для измерения деталей, требующих бесконтактного измерения, например, гибких деталей.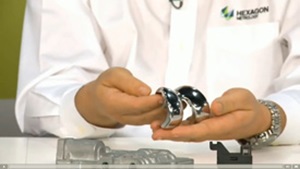
На другой стороне спектра находятся детали, поддающиеся измерению по отдельным точкам. Штампованные детали с большими допусками, для которых форма не является критически важной, а требуется соблюсти лишь положение отверстия, наиболее пригодны для точечных измерений. Даже если деталь имеет множество параметров, сканирование их будет излишеством и пустой тратой времени, и денег.
Некоторые детали могут иметь несколько позиций с самыми различными допусками. В этом случае идеальным выбором могла бы быть мультисенсорная КИМ, поскольку детали могли бы измеряться различными датчиками в рамках одной программы. Например, на литой крышке автоматической трансмиссии, показанной ниже, имеются элементы, полученные металлообработкой; отверстия с допусками общего уровня, но внутри имеются элементы, выполненные с более высокой точностью. Вследствие разнообразия элементов детали, исходная отливка после доставки ее от поставщика может быть проверена лазерным сканером. После механической обработки рекомендуется произвести аналоговое сканирование поверхностей, поскольку, вероятно, потребуется высокая точность сопрягаемой поверхности, которая может герметично сопрягаться с трансмиссией. Отверстия могут быть измерены сканированием или, в зависимости от допусков, контактным способом, что позволит сэкономить время.
Отливка верхней части автоматической трансмиссии
При оценке пригодного метода контроля для деталей следует учитывать требуемую пропускную способность. Имеется три основных категории. Измерение отдельных точек, обычно выполняемое с помощью контактных датчиков, получает одно измерение за один раз, но крайне медленно; примерно одну точку в секунду. Аналоговый датчик способен получить линейку данных, подобно перу, рисующему линию. Датчики, которые подпадают под эту категорию, -- аналоговые сканирующие датчики и CSW. В случае сбора больших объемов данных трехмерное лазерное строчечное сканирование обеспечивает высокую плотность точек, что более сравнимо с кистью.
Быстрое и точное получение данных является важным свойством, но оно не дает преимуществ, пока эти данные не будут представлены конечному пользователю в понятной форме. Сегодня тенденция состоит в использовании лазерного сканирования, поскольку этот метод быстр, достаточно точен, а все требуемые характеристики получаются за один прием. Тем не менее, эта возможность может оказаться необязательной для сбора данных, необходимых для контроля критически важных свойств.
После получения данных возникает вопрос их обработки: что же нужно делать с этой информацией. Является ли целью просто сравнить физическую деталь с ее 3D моделью и, если так, то каковы основные проблемные области? С помощью лазерного датчика могут быть получены миллионы точек данных. Если целью сбора данных является увидеть, как выглядит эта деталь, то это значит, что компания просто потеряла из виду истинную цель проверки критических характеристик детали. Во множестве случаев излишнее количество точек данных может быть вредным, а не полезным -- перегружая программное обеспечение и вычислительные процессы или сосредотачивая ненужное внимание на некритических участках.
Кисточка или перо?
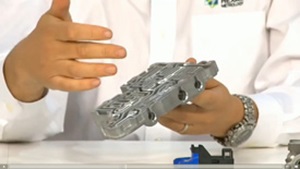
Быстрое и точное получение данных является важным свойством, но оно не дает преимуществ, пока эти данные не будут представлены конечному пользователю в понятной форме. Сегодня тенденция состоит в использовании лазерного сканирования, поскольку этот метод быстр, достаточно точен, а все требуемые характеристики получаются за один прием. Тем не менее, эта возможность может оказаться необязательной для сбора данных, необходимых для контроля критически важных свойств.
После получения данных возникает вопрос их обработки: что же нужно делать с этой информацией. Является ли целью просто сравнить физическую деталь с ее 3D моделью и, если так, то каковы основные проблемные области? С помощью лазерного датчика могут быть получены миллионы точек данных. Если целью сбора данных является увидеть, как выглядит эта деталь, то это значит, что компания просто потеряла из виду истинную цель проверки критических характеристик детали. Во множестве случаев излишнее количество точек данных может быть вредным, а не полезным -- перегружая программное обеспечение и вычислительные процессы или сосредотачивая ненужное внимание на некритических участках.