Scannen oder nicht scannen – das ist hier die Frage
Kontakt
Industriemesstechniker sind auf der ewigen Suche nach dem besten Verfahren zur Inspektion des jeweiligen Werkstücks. Bei der Evaluierung neuer Koordinatenmessgeräte (KMG) und beim Experimentieren mit den Funktionen der vorhandenen Systeme ist natürlich auch Zubehör ein Thema. Es gibt mehrere Möglichkeiten, die alle ihre ganz individuellen Vor- und Nachteile aufweisen. Der Trick liegt in der Wahl der richtigen Option, die alles Erforderliche bietet.
Das für die Messung kleiner bis mittelgroßer Werkstücke verfügbare Zubehör lässt sich in vier Hauptkategorien untergliedern. Da sind zum ersten schaltende Taster zur Messung von Einzelpunkten auf einem Werkstück. Zum zweiten gibt es analoge scannende Sensoren, die sich die Oberfläche eines Werkstücks entlang bewegen und dabei Tausende von Einzelpunkten gleichzeitig sammeln. Drittens können 3D-Laserscanner eingesetzt werden, die einen Laserstreifen zur Erfassung von Tausenden oder sogar Millionen Punkten einer Oberfläche nutzen. Und viertens sind chromatische Weißlicht-Sensoren (CWS), die hochgenaue berührungslose Inspektionen erlauben, eine Option.
Bei der Überlegung, ob es sinnvoll ist, ein Werkstück zu scannen, neigen Fachleute dazu, sich für analoges Scanning zu entscheiden, da bei einfacher Zugänglichkeit der meisten Bereiche mit diesem Verfahren große Mengen hochgenauer 3D-Koordinatendaten gesammelt werden können. Es ist außerdem eine gute Lösung, weil mit dieser Messstrategie am wahrscheinlichsten ist, dass alle kritischen Elemente erfasst werden. Durch analoges Scanning erhöht sich die Wiederholgenauigkeit der Messergebnisse. Dabei sinkt gleichzeitig die Messunsicherheit. In Wirklichkeit gehen der Entscheidung, ein Werkstück zu scannen, jedoch sehr differenzierte Überlegungen voraus, deren Ergebnis von der jeweiligen Anwendung abhängt.
Das für die Messung kleiner bis mittelgroßer Werkstücke verfügbare Zubehör lässt sich in vier Hauptkategorien untergliedern. Da sind zum ersten schaltende Taster zur Messung von Einzelpunkten auf einem Werkstück. Zum zweiten gibt es analoge scannende Sensoren, die sich die Oberfläche eines Werkstücks entlang bewegen und dabei Tausende von Einzelpunkten gleichzeitig sammeln. Drittens können 3D-Laserscanner eingesetzt werden, die einen Laserstreifen zur Erfassung von Tausenden oder sogar Millionen Punkten einer Oberfläche nutzen. Und viertens sind chromatische Weißlicht-Sensoren (CWS), die hochgenaue berührungslose Inspektionen erlauben, eine Option.
Bei der Überlegung, ob es sinnvoll ist, ein Werkstück zu scannen, neigen Fachleute dazu, sich für analoges Scanning zu entscheiden, da bei einfacher Zugänglichkeit der meisten Bereiche mit diesem Verfahren große Mengen hochgenauer 3D-Koordinatendaten gesammelt werden können. Es ist außerdem eine gute Lösung, weil mit dieser Messstrategie am wahrscheinlichsten ist, dass alle kritischen Elemente erfasst werden. Durch analoges Scanning erhöht sich die Wiederholgenauigkeit der Messergebnisse. Dabei sinkt gleichzeitig die Messunsicherheit. In Wirklichkeit gehen der Entscheidung, ein Werkstück zu scannen, jedoch sehr differenzierte Überlegungen voraus, deren Ergebnis von der jeweiligen Anwendung abhängt.
Was kann potenziell schiefgehen?
Bei der Wahl des geeigneten Inspektionsverfahrens sollte man sich als erstes überlegen, wie der Fertigungsprozess des jeweiligen Werkstücks aussieht und was dabei potenziell schiefgehen kann. Ist das Werkstück zum Beispiel aus Kunststoff, stellt sich die Frage, ob es dickere Bereiche gibt, die sich beim Abkühlen des Materials setzen können. Lautet die Antwort ja, und handelt es sich dabei um kritische Elemente mit engen Toleranzen, sollte das Werkstück gescannt werden. Ist das Element dagegen nicht kritisch und weist grobe Toleranzen auf, reichen Einzelpunktantastungen vermutlich aus.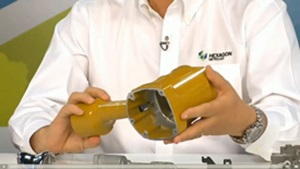
Um das beste Inspektionsverfahren zu ermitteln, wird sich ein erfahrener Messtechniker intensiv mit dem Fertigungsprozess beschäftigen. Das oben abgebildete Gussgehäuse einer Nagelpistole weist einige interessante Elemente auf. Aber auch die Bearbeitungsverfahren spielen bei der Entscheidung, ob ein Werkstück gescannt werden soll, eine Rolle. Das Profil dieses Werkstücks kann mittels 3D-Laserscan des Gehäuses aus Aluminiumguss geprüft werden. Zur Prüfung anderer Elemente, insbesondere solcher, die sich nicht an der Oberfläche des Werkstücks befinden, wären analoges Scanning oder Einzelpunktmessungen die Methoden der Wahl. Außerdem sollten die Fügeflächen des Werkstücks geprüft werden. Da es sich hier um eine Frage der Passgenauigkeit handelt, ist für solche Flächen analoges Scanning die beste Möglichkeit.
Welche Toleranzen gelten?
Wie bereits angedeutet, spielen auch die Toleranzen eines bestimmten Bezugselements eine Rolle bei der Ermittlung des optimalen Inspektionsverfahrens. Obwohl die Laserscanning-Technologie seit ihren Anfängen enorme Fortschritte gemacht hat, ist ihre Genauigkeit in Gegenüberstellung zu anderen Methoden noch immer rückläufig. Bei engeren Toleranzen als ±0,254 Millimeter ist Laserscanning nicht ideal. Es eignet sich dagegen gut bei Werkstücken mit größeren Toleranzen und mehreren durch Parameter definierten Oberflächen. Einzelpunktmessungen bieten eine höhere Genauigkeit, im Vergleich zu analogem Scanning jedoch eine geringere Wiederholbarkeit. Analoges Scanning gilt als das genaueste Inspektionsverfahren und erlaubt die Einhaltung von Toleranzen bis zu ±0,0127 Millimeter. Bei chromatischen Weißlicht-Sensoren (CWS) handelt es sich um ein hochpräzises berührungsloses Inspektionsverfahren, mit dem eine Messgenauigkeit von bis zu zehn Nanometern erzielt werden kann. CWS wird für Elemente eingesetzt, die für die Messung mit einem Taster zu klein sind, oder für empfindliche oder verformbare Komponenten, die ein berührungsloses Verfahren erfordern.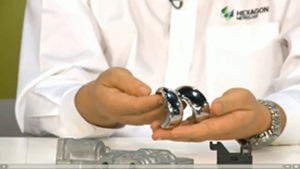
Am anderen Ende des Spektrums sind bestimmte Werkstücke besonders für Einzelpunktmessungen geeignet. Ein Stanzteil mit groben Toleranzen, bei dem die Form keine große Rolle spielt, aber das Profil der Lochpositionen erfasst werden muss, ist ein klarer Fall für die Einzelpunktantastung. Auch wenn das Werkstück mehrere zu messende Elemente enthält, wäre der Einsatz eines Scanners übertrieben und eine Zeit- und Geldverschwendung.
Manche Werkstücke weisen eine große Bandbreite an verschiedenen Toleranzen auf. Hier wäre ein Multisensor-KMG die beste Wahl, da Werkstücke innerhalb desselben Programms mit unterschiedlichen Sensoren gemessen werden können. Der unten abgebildete Gehäusedeckel eines Automatikgetriebes enthält beispielsweise spanabhebend bearbeitete Bohrungen, für die Allgemeintoleranzen gelten, doch im Inneren auch hochpräzise Elemente mit engen Toleranzen. Aufgrund der unterschiedlichen Arten von Elementen könnte das Gussteil mit einem Laserscanner gescannt werden, wenn es vom Lieferanten kommt. Nach der maschinellen Bearbeitung könnte die Oberfläche dann analog gescannt werden, weil zur Abdichtung des Getriebes wahrscheinlich enge Formtoleranzen beachtet werden müssen. Die Bohrungen können ebenfalls gescannt werden, oder – abhängig von ihren Toleranzen – einzeln angetastet werden, um Zeit zu sparen.
Bleistift oder Malerpinsel?
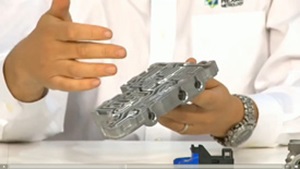
Die rasche, präzise Sammlung großer Mengen von Messdaten bietet allerdings nur dann einen Mehrwert, wenn diese Daten für die Nutzer auch entsprechend verständlich aufbereitet werden. Der Trend geht heute hin zum Laserscanning, weil alle Bezugselemente rasch, relativ genau und gleichzeitig erfasst werden. Doch zur Inspektion der kritischen Elemente ist dies möglicherweise gar nicht nötig.
Nach der Erfassung der Daten stellt sich sofort die Frage, wie diese weiterverarbeitet und genutzt werden können. Soll das physische Werkstück einfach mit seinem CAD-Modell abgeglichen werden, und wenn ja, welche Bereiche sind dabei von besonderer Bedeutung? Mit einem Lasersensor können Millionen von Datenpunkten aufgezeichnet werden. Sollen diese Daten nur dazu verwendet werden, sich ein Bild vom Aussehen des Werkstücks zu machen, wurde das wahre Ziel – nämlich die Inspektion seiner kritischen Elemente – aus den Augen verloren. In vielen Fällen erweisen sich riesige Mengen von Punktwolkendaten eher als Fluch denn als Segen, indem sie Software und Verarbeitungsprozesse verlangsamen oder unnötige Aufmerksamkeit auf nicht kritische Bereiche lenken.