スキャンの選択
産業計測の専門家は、休む間もなくベストな部品検査方法の課題に取り組んでいます。
お問い合わせ先
部品のスキャンで決定される問題に直面した時、測定専門家は本来的にアナログスキャニングに傾く傾向があります。ほとんどのエリアに楽にアクセスできて、大量の高精度3D座標データを取得するからです。さらに適切な理由は、不可欠な形状は全て捉える可能性がより強いからです。アナログスキャニングの使用で結果の繰り返し性が向上、加えて測定不確実性を減らします。しかし現実でのスキャンの決定は、見解が微妙で用途次第です。
何が失敗をもたらすのか?
検査技術の評価の最初のステップは、全体の製造工程に目を向けて、何が潜在的に失敗を起すのかを考察することです。例として、部品がプラスチックの場合、部品が冷めて落ち着く時、沈下し易い厚みのあるエリアがありますか? ある場合、またそれが厳しい公差で、極めて大事な形状である場合はスキャンすべきです。とくに重要性がなく、公差も緩い場合は、おそらくタッチプローブで十分でしょう。
また、工程を評価する時に部品の用途を考慮すべきです。上記で記述した様な自動車部品用のプラスチックコネクタは水の侵入を防ぐしっかりしたシールが要求されます。コネクタは簡素な形状でタッチプローブが、やり易く思えますが、シールを形づくるエッジはアナログスキャニングが必要な厳しい公差の指定がある可能性があります。
ダイキャストアルミのネイルガン・ハウジングです。最良の方法を求め、ベテランの計測専門家が製造工程の始めから終わりまで見直します。ネイルガンは、ここに表示のある、オリジナルのダイキャスト部品の上は、興味深い形状になっています。加えてスキャンの是非を考慮すべき加工工程があります。特にこの部品に関し、会社はダイキャストアルミハウジングを3Dレーザースキャニングして輪郭のチェックをします。チェックすべきもう一つの形状は、部品のはめ合わせ表面でしょう。合わせの問題があるので、アナログスキャニングニングがそのような表面にはより適した選択です。
公差とは何か?
先ほど少し言及したように、一定のデータに要求されている公差は、適切な検査方法を決定するのに役割を果たします。レーザースキャニングは、導入以来長い道を歩んできましたが、他の方法と比較すると、まだ相対的に精度の面で劣っています。 公差が± 0.01”より厳しい場合、レーザースキャニングは使うべきでないですが、輪郭で制御した多くの表面を持った公差の緩い部品には、適しています。タッチプロービングは、高精度です。しかしアナログスキャニングと比べると、低い繰り返し精度です。アナログスキャニングは部品の検査には最も精度のある方法とされており、± 0.0005”まで公差を維持できます。 クロマチックホワイトライトセンサー(CWS)は、10ナノメートルまでの計測機能を持つ高精度、非接触検査方法です。CWSは、タッチプローブでは小さすぎる形状や、柔軟部品など、非接触測定が必要な部品用に使用されます。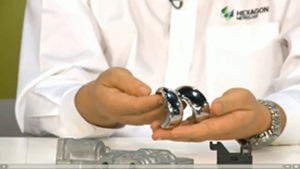
一方、個別のプロービングに向いている部品もあります。形が問題ではなく、穴の輪郭が要求される緩い公差の型打ちした部品は、ポイントプロービングにうってつけです。部品は多様な形状を持っているとはいえ、スキャニングは過剰な選択で、時間と予算の無駄です。
部品によっては、広範囲な内容の公差で、いろいろ付記が付けられる可能性があります。この例では、複数センサーCMMが理想的な選択です。部品が同じプログラム内で異なるセンサー により測定を受けられるからです。例えば、下方に示したような自動車トランスミッションのダイキャストのトッププレート上で、一般的な公差の穴付きの機械加工 を施した形状があります。しかし内在的には、高精度の形状があります。部品上の多様な形状のため、当初の鋳物は、業者から納入時にレーザースキャンするかも知れません。機械加工後に面をアナログスキャニングすることを推奨します。理由は厳しい公差の付記が予想され、よってトランスミッション のシールを形成することができます。掘削孔もスキャンされるかもしれませんが、公差次第で 内径タッチプローブがおそらく時間を節約します。
ペンキのハケ状、それともペン先状に?
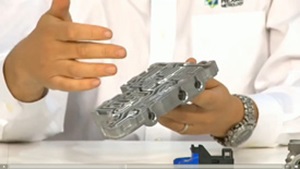
データを素早く、正確に取得できるのは、優れた性能ですが、対象とする聴衆に向けて判り易くプレゼンができないと、効果的になりません。今日のトレンドは、レーザースキャニングの採用です。速い、かなり正確、そして必要なデータを一度に捉えます。しかしこの性能は、重要な形状の検査に必要なデータ収集としては、必要ありません。 ひとたび、データが集まると、この情報をどう扱うかというデータ管理の問題が浮上します。目的は、単にCADモデルと物理的な部品を比較するだけなのか? そうだとしたらテーマの主な領域は? レーザーセンサーで百万単位のデータの収集ができます。もしそのデータのプランが、部品の外観を見るためでしたら、会社は、部品の重要な形状を検証するという実際の目的を見失っています。多くの場合、過剰な量の点データは、どうにもならないソフトウェアとコンピュータの処理で、利益ではなく不利益になる恐れがあります。
コストの検討
異なるプロービングの選択肢を精査した時、最後の関心事は、使える経費です。この要因は、出発点ではなく、最後の考察という理由があります。企業は、まず用途に対する最良のテクノロジーの導入検討をすべきです。それから利点に目を向け、同時に付随するコストセーブ、そして見込まれる投資の見返りの試算です。その時初めて予算の検討に取り組むべきです。
スキャンの選択
企業は常にコストを減らし、生産性を高め、受注を伸ばすことを追い求めています。流行を追い、新しい技術が導入されるといつも飛び乗ってしまう一部の会社もあります。しかし、競合他社が取り組むことが、どの会社にとっても正しい方向とは必ずしも言えません。物事を単にやるのと、物事をうまくやるには差があります。最善の選択まで煮詰めるのは手間がかかります。しかり適切な洞察力と検討で、理想のソリューションは、すぐに浮かび上がります。
ゴールデンタイムに備える
3Dスキャニングソリューションに向けた業界の動きは、ひとつには、処理数の向上によるものですが、部品の印刷ができる方法も原因です。過去は、部品の参照は幅と長さの寸法で行っていました。今日、製品寿命は縮まり続けています。現状の部品を幅と長さと使って反復するのは煩雑で変更に時間がかかり過ぎます。部品の全体の形が輪郭で制御される場合、CADモデルを変更する所要時間は極端に減ります。輪郭で制御される部品は、内蔵のGD&T輪郭制御に 適しています。測定形状の位置が 部品の輪郭の中に入っている場合には、スキャニングは最適です。