Optyczna kontrola jakości w precyzyjnych odlewach
Trzeci wymiary koła turbiny
Kontakt

Kontrola jakości jako metrologiczne wyzwanie: Jakość i precyzja wyrobów odlewanych sięgająca kilkudziesięciu mikronów może być oczekiwana dla wymiarów przestrzennych. Wiodący producent w przemyśle metalowym, podczas swojej 300-stu letniej działalności jako Zollern, opracował i doprowadził do perfekcji szerokie spectrum mieszanek metali i technik wytwarzania wszędzie tam, gdzie wymagana jest wysoka precyzja i najwyższa jakość: dzięki wysokiej precyzji trójwymiarowych danych generowanych przez StereoScan, woskowe szablony matryc i wyroby końcowe są kontrolowane z wystarczającą dokładnością.
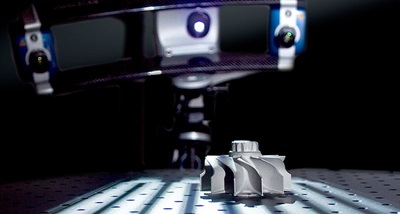
Obiekt i zadanie pomiarowe
Wyrażenie „precyzyjny odlew” (tożsame z „kosztowne odlewanie”), samo w sobie wskazuje na produkt wytworzony przez Zollern: Są oni przede wszystkim wiodącym producentem elementów o masie 1g-10kg, jak koła turbin, mieszalniki dla turbin gazowych, łopatek. Dysponują techniką, która pozwala wytworzyć produkt w wysokiej precyzji przy minimalnych kosztach, gdzie inne metody zawodzą i generują znacznie większe koszty.
W celu osiągnięcia produktu o najwyższej jakości, jakość elementu obrotowego w układzie wylotowym sprężarek jest definiowana w milimetrach: Wymiary są w bardzo wąskich tolerancjach i musza być powtarzalnie weryfikowane w czasie procesu produkcji. Przy stale rosnącym stopniu skomplikowania kształtu tych komponentów, stykowe metody inspekcji przy pomocy maszyny współrzędnościowej (CMM) nie są w stanie spełnić równocześnie dwóch wymogów tj czasu i jakości pomiaru. Ponadto wyniki z CMM muszą być interpretowane przez metrologów. To jest etap, kiedy to Jürgen Weber, koordynator inwestycji wydziału odlewów, podkreśla znacznie czytelnych i zrozumiałych raportów, pozwalając na łatwiejszą komunikację nie tylko wewnątrz firmy, ale i z klientem.
System pomiarowy i jego konfiguracja
W kontekście kontroli jakości w linii produkcyjnej, Zollern wykorzystuje system projekcji prążków referencyjnych firmy AICON o nazwie StereoScan. System ten charakteryzuje się dużą elastycznością: bazując na przygotowaniach wykonanych we współpracy z firmą AICON, pole pomiarowe oraz iluminacja, rozdzielczość oraz stopień automatyzacji zostały dopasowane do indywidualnych wymogów firmy Zollern.
Zadanie pomiarowe w zakresie odlewów jest zróżnicowane: oprócz zastosowania w badaniach i rozwoju, system pomiarowy 3D jest również wykorzystywane w kontroli w linii produkcyjnej w celu zapewnienia jakości. W tym przypadku woskowy model koła turbiny jest przychwytywany trójwymiarowo w celu porównania wartości nominalnych względem rzeczywistych w oparciu o model CAD, lub wykorzystując przecięty obiekt w celu weryfikacji geometrii wewnętrznej.
W dalszym etapie, wysokiej precyzji dane pomiarowe są wykorzystywane do pełnej pierwszej inspekcji oraz do korekt narzędzi. Po tym etapie, podczas masowej produkcji, kontrola 3D jest kluczowa w zachowaniu standardów jakościowych: to jest etap, na którym jest weryfikowana złożoność kształtu detalu.
Trójwymiarowa kontrola jakości łopatki turbiny jest realizowana z użyciem StereoScan o małym polu pomiarowym zapewniając najwyższą precyzję oraz rozdzielczość. Koło turbiny jest następnie digitalizowane w następujących krokach: Po skonfigurowaniu skanera 3D, obiekt pomiarowy oraz stolik są odpowiednio ustawiane, kalibrowane są kamery oraz jednostka projekcyjna.
W aktualnym procesie skanowania, pozyskiwane dane są generowane przez skaner, następnie dopasowane względem siebie i łączone w jeden obiekt. To wszystko odbywa się automatycznie za pomocą oprogramowania OptoCat firmy AICON. Miejsca mocno zagłębione nie pozwalają na dokonanie skanowania przy zachowaniu standardowych parametrów skanowania. Wykorzystując system trzech kątów triangulacyjnych tj 30°, 20°, i 10°, pomiar taki jest możliwy dla detali o zróżnicowanych wymiarach.
W drugim kroku, dane pozyskane skanerem są przetwarzane za pomocą oprogramowania metrologicznego (w tym przypadku PolyWorks/Inspector™ firmy InnovMetric Software Inc.), pozwalając na analizę wcześniej zdefiniowanych parametrów i geometrii, wykonywać przekroje i analizę deformacji. Ponadto dostępny jest raport pomiarowy, który stanowi kwintesencję pomiaru, pozwalając na wizualizację wyników między innymi za pomocą kolorowej mapy błędów.
Wnioski
Dzięki łatwej obsłudze systemu pomiarowego, dane wygenerowane przez skaner AICON pozwalają na optymalizację parametrów produkcji efektywnie i sprawnie w czasie procesu produkcji, wspierając tym samym Zollern w utrzymaniu wysokiej jakości swoich wyrobów. Przeprowadzania czasochłonnych badań w laboratorium przy użyciu maszyny współrzędnościowej, nie jest więcej wymagane. Wykorzystując trójwymiarowe dane nie tylko analizujemy całą geometrię, ale proces ten jest znacznie szybszy i wydajniejszy, pozwalając na redukcję kosztów produkcji.
Pan Weber podsumowuje:” W porównaniu do klasycznej CMM, pozyskiwanie danych z użyciem skanera AICON jest nieporównywalnie szybsze, pozwalając na na sprawne uzyskanie danych. Skaner ma również inne zastosowanie między innymi w jednoczesnej kontroli jakości 20 ceramicznych rdzeni odlewów łopatek. „
Wykorzystując odpowiednio dobraną konfigurację Pan Weber zaangażował posiadany system w kontrolę jakości dużych obiektów: sama technika projekcji prążków referencyjnych dostarcza nieporównywalnie lepszą jakość danych poniżej milimetra oraz w wyższej rozdzielczości niż ma to miejsce w przypadku maszyny współrzędnościowej lub systemów laserowych. Wynikiem tego są stale wysokiej jakości produkty pochodzące z firmy Zollern.