Libertà di misurare alla Volvo
Incremento della produttività a partire dalla prototipazione fino alla produzione con AT960, LAS-XL e T-Scan 5
Contattateci
Con i suoi 2.400 dipendenti, Volvo Car Body Components (VCBC) con sede a Olofström è uno stabilimento di produzione di automobili che fabbrica milioni di parti di carrozzeria ogni anno. Dai cofani e tettucci alle portiere e ai componenti secondari, l'attività principale dello stabilimento è lo stampaggio delle lamiere per la produzione di componenti essenziali per auto, che vengono spediti interi o parzialmente assemblati alle fabbriche automobilistiche Volvo di tutto il mondo per il montaggio finale e la finitura.
La moderna fabbrica di Olofström, tecnologicamente avanzata e attenta alle problematiche ambientali, ha una storia che risale a quasi 300 anni fa: nasce come fonderia di ferro nel 1735 e dal 1927 produce parti di carrozzeria per tutte le automobili Volvo. Da quando è stato acquistato da Volvo nel 1969, il sito negli ultimi 50 anni si è occupato dello stampaggio e dell'assemblaggio preliminare di parti di carrozzeria per la gamma completa di veicoli Volvo, oltre che per clienti esterni come Volvo Trucks, Ford e Land Rover.
In Volvo le prime fasi di produzione che riguardano il processo di progettazione di un'auto dipendono in gran parte dallo sviluppo degli stampi, progettati e prodotti dal team Tool and Die a Olofström. Il team è innanzitutto responsabile della produzione dei prototipi degli stampi, e visto che ne sono necessari fino a 80 per la progettazione di un veicolo, questo lavoro può durare da quattro a cinque mesi. In genere ciascun progetto dura un anno e il resto del tempo è dedicato alla produzione degli stampi finali che saranno impiegati per pressare centinaia di migliaia di componenti della carrozzeria.
Nel 2018 il team ha ritenuto che fosse giunto il momento di introdurre una soluzione di misura moderna per la prototipazione e la produzione degli stampi con l'obiettivo di migliorare la produttività. Ha identificato diversi passaggi fondamentali nel suo processo di progettazione, produzione e verifica in grado di beneficiare potenzialmente dell'introduzione di dispositivi di misura avanzati. Avendo già una grande e ben attrezzata sala di controllo qualità, il team conosceva bene un'ampia gamma di strumenti di misura, dalle CMM a braccio orizzontale agli scanner a luce strutturata. Era disponibile a prendere in considerazione un certo numero di sistemi diversi attualmente disponibili sul mercato, ma una delle sue principali priorità era individuare una soluzione che fosse adatta sia all'officina che alla sala di controllo qualità.
Con diversi sistemi Absolute Tracker già in uso nelle principali aree di produzione dello stabilimento di Olofström, l'esperienza già acquisita all'interno del sito unita alla ben nota portabilità e flessibilità dei sistemi Absolute Tracker ha reso per così dire obbligata la scelta di ulteriori sistemi laser tracker di Hexagon.
Un passaggio chiave nella predisposizione di una fusione per la fresatura consiste nell'assicurarsi che non avvengano collisioni tra la fresatrice e il pezzo quando entrambi sono portati in posizione prima dell'inizio della lavorazione. Una tale collisione può provocare alla fresatrice danni ingenti in termini di tempo e costi . Pertanto l'operatore deve introdurre un fattore di sicurezza in fase di preparazione, posizionando la macchina abbastanza lontano dal pezzo in modo da essere certo che non si verifichino collisioni. Non è semplice eseguire questa operazione a occhio e spesso implica che la fresatrice giri a vuoto per molto tempo all'inizio del suo programma.
"I dati iniziali di scansione permettono di evitare perdite di tempo", afferma Kim Tingstedt, Tool and Die Operator alla VCBC di Olofström. "Il grosso risparmio di tempo si ha quando si ottimizza il programma di fresatura in base alle dimensioni reali del pezzo, perché la velocità è la stessa che la macchina proceda a vuoto o a contatto con il materiale. Ora i tempi ciclo in fresatura sono più rapidi e ciò significa che possiamo lavorare più pezzi e stampi."
Già in precedenza avveniva questa ottimizzazione, ma con i dati di scansione completi forniti da LAS-XL, tutto è molto più semplice. "Quando eseguiamo la scansione, i nostri tecnici ottengono più informazioni rispetto alla nostra precedente soluzione di scansione che fornisce solo punti, quindi possono ottenere molte più informazioni", ha dichiarato Kim Tingstedt. "Il tecnico può trasferire i dati alla macchina CNC e può ottimizzare molto più facilmente il pezzo da fresare grazie alla visualizzazione fedele."
Ora possiamo contare su tempi di esecuzione migliori per quanto riguarda le fresatrici.Tali dati di scansione della fusione possono essere sfruttati anche in altri modi per migliorare la produzione. I getti sono estremamente pesanti e difficili da spostare, quindi qualsiasi possibilità di renderli più leggeri migliora la loro facilità d'uso e riduce la quantità di materiale necessario per produrli. Ciò significa che devono essere più piccoli possibile, anche se non troppo piccoli. Se non viene lasciato abbastanza materiale tra il blocco dello stampo e la sua forma interna, esso non risulterà abbastanza resistente da sopportare ripetuti cicli di stampaggio.
Utilizzando i dati di scansione rilevati sulla fusione, i prototipi successivi e gli stampi finali possono essere perfezionati per garantire il peso e l'impiego minimi di materiale senza ridurre l'integrità strutturale dello stampo. Inoltre si ha il vantaggio di permettere alla fresatrice di iniziare il lavoro più vicino alla forma finale del pezzo a ogni iterazione, risparmiando tempo in ogni passaggio.
Il Leica Absolute Scanner LAS-XL è lo strumento perfetto per questo processo di scansione. L'ampia linea di scansione e l’elevata distanza focale permettono di eseguire la scansione della fusione molto rapidamente, rendendo la scansione l'alternativa più rapida alla semplice applicazione di un importante fattore di sicurezza durante la fresatura.
Con la distanza focale del LAS-XL è possibile misurare punti nascosti all'interno delle cavità delle fusioni, al fine di risparmiare sul materiale utilizzato e ridurre il peso finale. Uno scanner con una grande distanza focale come il LAS-XL permette di misurare con precisione queste cavità consentendo al team di Tool and Die di economizzare notevolmente sui materiali e ridurre il peso, senza compromettere la funzionalità dello stampo.
Una volta completata la fase di fresatura è il momento di controllare la precisione dello stampo. Ciò richiede un livello di misura più elevato di quello offerto da LAS-XL. Ma con l'Absolute Tracker AT960, che propone una serie di soluzioni di scansione compatibili, il team ha dovuto investire solo in un altro scanner ad alta risoluzione per soddisfare questa esigenza.
Con il Leica T-Scan 5 sia l'area dello stampo fresato che le eventuali prove di stampaggio possono essere rapidamente verificate e confrontate con il CAD per garantirne la precisione. Si tratta di un processo molto più veloce di quanto non fosse in precedenza, in grado di ridurre notevolmente la produzione reiterata di prototipi, allineando il pezzo prodotto al progetto con un numero molto inferiore di iterazioni.
"Lo stampo va in produzione per lo stampaggio del primo pezzo", racconta Johanna Persson, del reparto qualità. "Il pezzo viene scansionato per controllare che sia corretto e se non lo è stabilirne le cause. Il tracker e lo scanner facilitano di molto l'identificazione del problema: si può verificare molto di più nei primi passaggi grazie a questi dati di scansione e non c'è bisogno di rifare tutto da capo."
Lo scanner si può utilizzare anche a valle della linea di produzione, sia per controllare la precisione dei pezzi che per la manutenzione degli stampi. Il team Tool and Die effettua periodicamente sui pezzi un controllo qualità che può essere eseguito facilmente con una scansione veloce utilizzando il T-Scan 5. E anche un altro team responsabile della manutenzione continua degli stampi ora si affida alla nuova attrezzatura del team Tool and Die per la diagnosi dei problemi: uno stampo che è già stato utilizzato sulla linea di produzione e non sta lavorando in modo soddisfacente può essere rapidamente verificato in officina grazie alla portabilità dell'Absolute Tracker e del T-Scan 5.
Tale rapida individuazione delle cause dei difetti di fabbricazione permette di risparmiare tempo rispetto a una soluzione di verifica legata alla sala di controllo qualità, in particolare quando si tratta di pezzi difficili da spostare come gli stampi per lamiera del settore automobilistico.
Questa possibilità di passare da uno scanner all'altro con diverse funzioni e di applicare questi sistemi a una gamma più ampia di applicazioni di verifica è stato uno dei fattori chiave che ha spinto il team Tool and Die di Olofström a investire in un sistema Absolute Tracker. "Abbiamo esaminato molti sistemi di scansione e la flessibilità di utilizzo non legata a un solo scopo è stata la discriminante", ha commentato Håkan Nilsson, Head IT Architect RnD and Purchasing di Volvo Group.
Il team di Tool and Die ha potuto anche utilizzare l'Absolute Tracker AT960 per l'allineamento iniziale della loro grande pressa. Tale procedura eseguita una tantum si è rivelata incredibilmente semplice utilizzando il tracker, i riflettori e la funzione orient-to-gravity dell'AT960.
"Hexagon ha fornito un po' di formazione di base, ma fin da subito sapevamo cosa stavamo facendo. Abbiamo già uno scanner manuale, con PolyWorks, e si trattava solo di un nuovo sistema, ma il concetto era già noto."
I nuovi membri del team sono stati facilmente istruiti all'impiego del dispositivo, ricorrendo solo a risorse interne di formazione. Il sistema è così semplice da usare che il team non ha bisogno di un sistema di formazione strutturato ma solo di una dimostrazione, inoltre i principianti imparano facendo pratica, lavorando sempre in collaborazione con i più esperti per la supervisione e i consigli.
Impiegano un certo numero di grandi CMM nella sala di controllo qualità e pensano di poter fare un upgrade utilizzando sistemi programmabili e automatizzati per un certo numero di applicazioni. Dagli scanner a luce strutturata ai sistemi robotici alimentati da un Absolute Tracker, hanno davvero a disposizione una vasta gamma di opzioni per continuare a incrementare la produttività con Hexagon.
La moderna fabbrica di Olofström, tecnologicamente avanzata e attenta alle problematiche ambientali, ha una storia che risale a quasi 300 anni fa: nasce come fonderia di ferro nel 1735 e dal 1927 produce parti di carrozzeria per tutte le automobili Volvo. Da quando è stato acquistato da Volvo nel 1969, il sito negli ultimi 50 anni si è occupato dello stampaggio e dell'assemblaggio preliminare di parti di carrozzeria per la gamma completa di veicoli Volvo, oltre che per clienti esterni come Volvo Trucks, Ford e Land Rover.
In Volvo le prime fasi di produzione che riguardano il processo di progettazione di un'auto dipendono in gran parte dallo sviluppo degli stampi, progettati e prodotti dal team Tool and Die a Olofström. Il team è innanzitutto responsabile della produzione dei prototipi degli stampi, e visto che ne sono necessari fino a 80 per la progettazione di un veicolo, questo lavoro può durare da quattro a cinque mesi. In genere ciascun progetto dura un anno e il resto del tempo è dedicato alla produzione degli stampi finali che saranno impiegati per pressare centinaia di migliaia di componenti della carrozzeria.
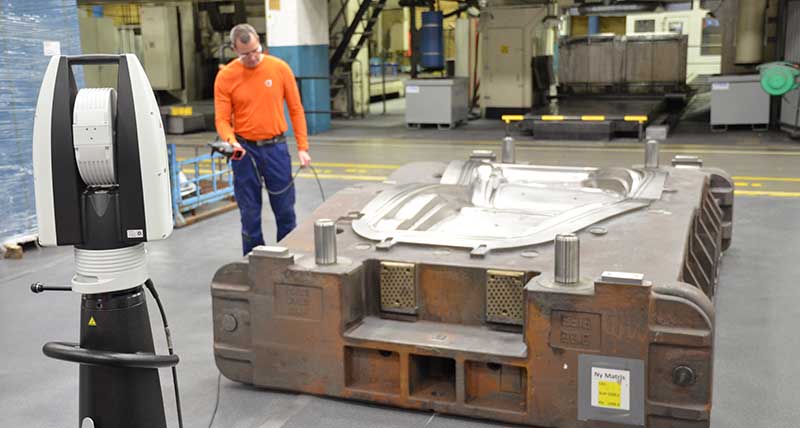
Con diversi sistemi Absolute Tracker già in uso nelle principali aree di produzione dello stabilimento di Olofström, l'esperienza già acquisita all'interno del sito unita alla ben nota portabilità e flessibilità dei sistemi Absolute Tracker ha reso per così dire obbligata la scelta di ulteriori sistemi laser tracker di Hexagon.
Miglioramento della fusione iniziale
Il primo passaggio nella produzione di un prototipo o di uno stampo finito è la fresatura di precisione di una fusione. La fusione non è un processo preciso e il pezzo grezzo presenta in genere molto materiale in eccesso che deve essere successivamente fresato per ottenere le giuste dimensioni e forme.Un passaggio chiave nella predisposizione di una fusione per la fresatura consiste nell'assicurarsi che non avvengano collisioni tra la fresatrice e il pezzo quando entrambi sono portati in posizione prima dell'inizio della lavorazione. Una tale collisione può provocare alla fresatrice danni ingenti in termini di tempo e costi . Pertanto l'operatore deve introdurre un fattore di sicurezza in fase di preparazione, posizionando la macchina abbastanza lontano dal pezzo in modo da essere certo che non si verifichino collisioni. Non è semplice eseguire questa operazione a occhio e spesso implica che la fresatrice giri a vuoto per molto tempo all'inizio del suo programma.
"I dati iniziali di scansione permettono di evitare perdite di tempo", afferma Kim Tingstedt, Tool and Die Operator alla VCBC di Olofström. "Il grosso risparmio di tempo si ha quando si ottimizza il programma di fresatura in base alle dimensioni reali del pezzo, perché la velocità è la stessa che la macchina proceda a vuoto o a contatto con il materiale. Ora i tempi ciclo in fresatura sono più rapidi e ciò significa che possiamo lavorare più pezzi e stampi."
Già in precedenza avveniva questa ottimizzazione, ma con i dati di scansione completi forniti da LAS-XL, tutto è molto più semplice. "Quando eseguiamo la scansione, i nostri tecnici ottengono più informazioni rispetto alla nostra precedente soluzione di scansione che fornisce solo punti, quindi possono ottenere molte più informazioni", ha dichiarato Kim Tingstedt. "Il tecnico può trasferire i dati alla macchina CNC e può ottimizzare molto più facilmente il pezzo da fresare grazie alla visualizzazione fedele."
Ora possiamo contare su tempi di esecuzione migliori per quanto riguarda le fresatrici.Tali dati di scansione della fusione possono essere sfruttati anche in altri modi per migliorare la produzione. I getti sono estremamente pesanti e difficili da spostare, quindi qualsiasi possibilità di renderli più leggeri migliora la loro facilità d'uso e riduce la quantità di materiale necessario per produrli. Ciò significa che devono essere più piccoli possibile, anche se non troppo piccoli. Se non viene lasciato abbastanza materiale tra il blocco dello stampo e la sua forma interna, esso non risulterà abbastanza resistente da sopportare ripetuti cicli di stampaggio.
Utilizzando i dati di scansione rilevati sulla fusione, i prototipi successivi e gli stampi finali possono essere perfezionati per garantire il peso e l'impiego minimi di materiale senza ridurre l'integrità strutturale dello stampo. Inoltre si ha il vantaggio di permettere alla fresatrice di iniziare il lavoro più vicino alla forma finale del pezzo a ogni iterazione, risparmiando tempo in ogni passaggio.
Il Leica Absolute Scanner LAS-XL è lo strumento perfetto per questo processo di scansione. L'ampia linea di scansione e l’elevata distanza focale permettono di eseguire la scansione della fusione molto rapidamente, rendendo la scansione l'alternativa più rapida alla semplice applicazione di un importante fattore di sicurezza durante la fresatura.
Con la distanza focale del LAS-XL è possibile misurare punti nascosti all'interno delle cavità delle fusioni, al fine di risparmiare sul materiale utilizzato e ridurre il peso finale. Uno scanner con una grande distanza focale come il LAS-XL permette di misurare con precisione queste cavità consentendo al team di Tool and Die di economizzare notevolmente sui materiali e ridurre il peso, senza compromettere la funzionalità dello stampo.
Verifica finale della qualità dello stampo
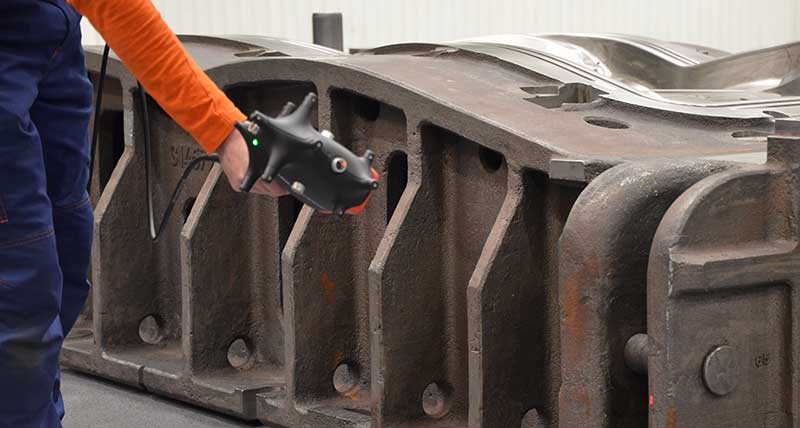
Con il Leica T-Scan 5 sia l'area dello stampo fresato che le eventuali prove di stampaggio possono essere rapidamente verificate e confrontate con il CAD per garantirne la precisione. Si tratta di un processo molto più veloce di quanto non fosse in precedenza, in grado di ridurre notevolmente la produzione reiterata di prototipi, allineando il pezzo prodotto al progetto con un numero molto inferiore di iterazioni.
"Lo stampo va in produzione per lo stampaggio del primo pezzo", racconta Johanna Persson, del reparto qualità. "Il pezzo viene scansionato per controllare che sia corretto e se non lo è stabilirne le cause. Il tracker e lo scanner facilitano di molto l'identificazione del problema: si può verificare molto di più nei primi passaggi grazie a questi dati di scansione e non c'è bisogno di rifare tutto da capo."
Lo scanner si può utilizzare anche a valle della linea di produzione, sia per controllare la precisione dei pezzi che per la manutenzione degli stampi. Il team Tool and Die effettua periodicamente sui pezzi un controllo qualità che può essere eseguito facilmente con una scansione veloce utilizzando il T-Scan 5. E anche un altro team responsabile della manutenzione continua degli stampi ora si affida alla nuova attrezzatura del team Tool and Die per la diagnosi dei problemi: uno stampo che è già stato utilizzato sulla linea di produzione e non sta lavorando in modo soddisfacente può essere rapidamente verificato in officina grazie alla portabilità dell'Absolute Tracker e del T-Scan 5.
Tale rapida individuazione delle cause dei difetti di fabbricazione permette di risparmiare tempo rispetto a una soluzione di verifica legata alla sala di controllo qualità, in particolare quando si tratta di pezzi difficili da spostare come gli stampi per lamiera del settore automobilistico.
Questa possibilità di passare da uno scanner all'altro con diverse funzioni e di applicare questi sistemi a una gamma più ampia di applicazioni di verifica è stato uno dei fattori chiave che ha spinto il team Tool and Die di Olofström a investire in un sistema Absolute Tracker. "Abbiamo esaminato molti sistemi di scansione e la flessibilità di utilizzo non legata a un solo scopo è stata la discriminante", ha commentato Håkan Nilsson, Head IT Architect RnD and Purchasing di Volvo Group.
Il team di Tool and Die ha potuto anche utilizzare l'Absolute Tracker AT960 per l'allineamento iniziale della loro grande pressa. Tale procedura eseguita una tantum si è rivelata incredibilmente semplice utilizzando il tracker, i riflettori e la funzione orient-to-gravity dell'AT960.
Imparare lavorando
Dopo aver ricevuto il tracker e il sistema di scansione, il team è diventato subito operativo solo con un piccolo aiuto da parte del team di supporto Hexagon. "[L'Absolute Tracker] è già conosciuto in Volvo, è presente in Volvo da molto tempo, perciò eravamo già esperti", ha detto Fredrik Sjöberg, tecnico della costruzione di prototipi alla Volvo Car.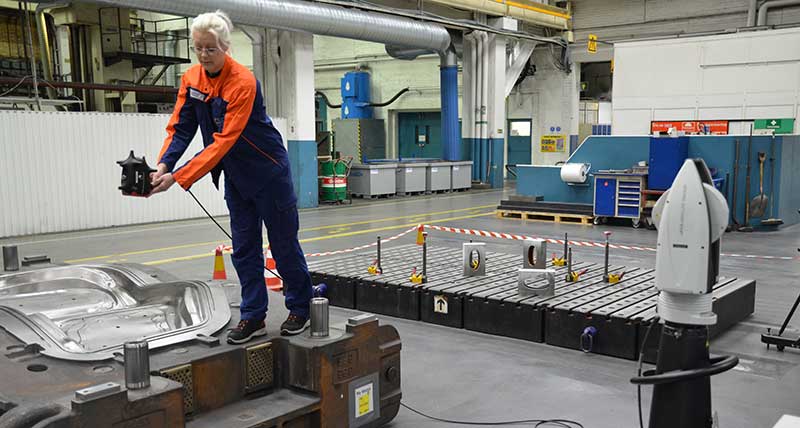
I nuovi membri del team sono stati facilmente istruiti all'impiego del dispositivo, ricorrendo solo a risorse interne di formazione. Il sistema è così semplice da usare che il team non ha bisogno di un sistema di formazione strutturato ma solo di una dimostrazione, inoltre i principianti imparano facendo pratica, lavorando sempre in collaborazione con i più esperti per la supervisione e i consigli.
Il futuro della misura
Il team Tool and Die del centro Volvo Car Body Components di Olofström è rimasto molto colpito dall'implementazione dei nuovi sistemi di scansione Hexagon e sono già in corso trattative per introdurre nel reparto dispositivi di misura più avanzati.Impiegano un certo numero di grandi CMM nella sala di controllo qualità e pensano di poter fare un upgrade utilizzando sistemi programmabili e automatizzati per un certo numero di applicazioni. Dagli scanner a luce strutturata ai sistemi robotici alimentati da un Absolute Tracker, hanno davvero a disposizione una vasta gamma di opzioni per continuare a incrementare la produttività con Hexagon.