Freiheit genau nach Maß bei Volvo
Produktivitätssteigerungen vom Prototyping bis zur Produktion mit AT960, LAS-XL und T-Scan 5
Mit etwa 2.400 Mitarbeitern produziert das Automobilwerk Volvo Car Body Components (VCBC) in Olofström jedes Jahr mehrere Millionen Fahrzeugteile. Von Motorhauben und Dächern über Türen bis hin zu Unterbaugruppen ist der Betrieb unter anderem spezialisiert auf das Pressen und Stanzen von Blechen zur Herstellung dieser unverzichtbaren Fahrzeugkomponenten. Sie werden komplett oder teilweise vormontiert zur Endmontage bzw. Fertigbearbeitung an Volvo-Fahrzeugfabriken weltweit geliefert.
Das moderne, umweltfreundliche High-Tech-Werk in Olofström blickt auf eine nahezu 300-jährige Geschichte zurück – ursprünglich 1735 als Eisenhütte gegründet, liefert der Betrieb seit 1927 Karosserieteile für alle Volvo-Fahrzeuge. In den 50 Jahren seit dem Kauf des Werks durch Volvo im Jahr 1969 spezialisierte sich der Standort auf die Pressumformung und Vormontage von Karosserieteilen für das gesamte Volvo- Fahrzeugangebot sowie für externe Kunden wie Volvo Trucks, Ford und Land Rover.
Die ersten Produktionsphasen des Fahrzeugkonstruktionsprozesses bei Volvo basieren maßgeblich auf der Entwicklung der Blechstanzwerkzeuge, die vom Werkzeug- und Formenbau in Olofström konstruiert und gefertigt werden. Zunächst ist das Team für die Herstellung der Werkzeugprototypen verantwortlich. Bei bis zu 80 benötigten Werkzeugen für ein Fahrzeugprojekt kann diese Aufgabe vier bis fünf Monate in Anspruch nehmen. In aller Regel dauert jedes Projekt insgesamt etwa ein Jahr. Die verbleibende Zeit ist für die Produktion der endgültigen Werkzeuge reserviert, mit denen Hunderttausende von Karosseriekomponenten gepresst werden.
Mit dem Ziel der Produktivitätssteigerung entschied sich das Team im Jahr 2018, eine moderne Messtechniklösung für das Prototyping und die Fertigung der Werkzeuge einzuführen. Identifiziert wurden mehrere wesentliche Abschnitte im Konstruktions-, Produktions- und Validierungsprozess, die potentiell von der Einführung moderner Messgeräte profitieren würden. Da das Team schon über einen großen und umfangreich ausgestatteten Messraum verfügte, war es bereits mit einem breiten Spektrum an Messtechnik – von Horizontalarm-KMGs bis zum Streifenlichtscanner – vertraut. Die Teammitglieder zogen verschiedene aktuell auf dem Markt erhältliche Systeme in Betracht. Eine ihrer wichtigsten Anforderungen war dabei, eine Lösung zu finden, die sich sowohl für die Fertigungsumgebung als auch den Messraum eignet.
Da in den Hauptfertigungsbereichen des Werks in Olofström bereits verschiedene Absolute Tracker-Systeme zum Einsatz kamen, war die Entscheidung für zusätzliche Laser Tracker-Lösungen von Hexagon der logische nächste Schritt – vor allem aufgrund des intern bereits vorhandenen Fachwissens sowie der bekannten Mobilität und Flexibilität der Absolute Tracker-Systeme.
Ein wesentlicher Schritt beim Einrichten eines Gussteils für das Fräsen besteht darin, Kollisionen zwischen dem Bauteil und der Werkzeugmaschine beim Positionieren vor der Fräsbearbeitung zu vermeiden. Derartige Kollisionen können zu besonders kosten- und zeitintensiven Schäden an der CNC-Fräsmaschine führen. Aufgrund dessen muss das Bedienpersonal beim Einrichten darauf achten, die Maschinen so weit entfernt vom Material zu positionieren, dass es garantiert zu keiner Kollision kommt. Dies nach Augenmaß vorzunehmen ist nicht einfach und bedeutet oftmals erhebliche Leerlaufzeiten für die Fräsmaschine zu Beginn ihres Programms.
„Mit den Eingangsscandaten lässt sich an dieser Stelle erheblich Zeit sparen“, erklärt Kim Tingstedt, Bediener im Werkzeug- und Formenbau bei VCBC Olofström. „Wird das Fräsprogramm auf die tatsächlichen Abmaße des Materials hin optimiert, führt das zu enormen Zeitersparnissen, denn die Geschwindigkeit der Maschine bleibt dieselbe – ob sie nun durch Luft oder Material fährt. Die Durchlaufzeit unserer Fräsmaschinen hat sich deutlich verbessert, sodass wir nun eine größere Anzahl an Teilen und Werkzeugen bearbeiten können.”
Obwohl diese Optimierung auch vorher schon durchgeführt wurde, gestalten sich die Abläufe dank der umfassenden Scandaten des LAS-XL nun wesentlich einfacher. „Mit dem jetzigen Scanvorgang stehen unseren Konstrukteuren entscheidend mehr Informationen als bisher zur Verfügung. Unsere vorherige KMG-Lösung lieferte lediglich Punkte“, sagt Kim Tingstedt. „Der Konstrukteur kann diese Daten direkt mit an der CNCMaschine nutzen und das Frästeil wesentlich einfacher optimieren, weil er das Teil praktisch sieht.”
Die Durchlaufzeit der Fräsmaschinen verbesserte sich entscheidend.Diese Gussteil-Scandaten sind darüber hinaus noch auf andere Weise für Produktionssteigerungen nutzbar. Gegossene Werkzeuge sind extrem schwer und lassen sich nur eingeschränkt bewegen. Daher erleichtert jede Gewichtsreduzierung ihre Verwendung und verringert gleichzeitig den Rohmaterialbedarf. Das bedeutet, die Menge an Rohmaterial muss so klein wie möglich sein – jedoch auch nicht zu gering. Bleibt zu wenig Material zwischen der Außenseite des Werkzeugs und der Innenseite seiner Präzisionsform übrig, ist es nicht mehr widerstandsfähig genug, um wiederholten Hochleistungspresskräften standzuhalten.
Mithilfe der Scandaten des ersten Gussteils lässt sich der Gießvorgang der nachfolgenden Prototypen und Werkzeuge präzisieren, um das geringstmögliche Gewicht und minimalen Materialverbrauch zu gewährleisten, ohne die strukturelle Integrität des Werkzeugs zu beeinträchtigen. Ein weiterer Vorteil hierbei ist, dass jeder Fräsdurchlauf näher an der endgültigen Teileform beginnen kann – das vergrößert zusätzlich die Zeitersparnis bei jedem Schritt.
Der Leica Absolute Scanner LAS-XL ist die perfekte Lösung für diesen Scanningprozess. Dank seiner breiten Scanlinie und dem großen Messabstand lassen sich Gussteile rasch scannen. Damit bietet sich das Scannen als zeitsparende Alternative gegenüber einem großen Sicherheitsfaktor beim Fräsen an.
Mit dem marktführenden Messabstand des LAS-XL lassen sich sogar verborgene Punkte in den Hohlräumen messen, die sich konstruktionsbedingt innerhalb der Werkzeuge befinden, um sowohl den Materialverbrauch als auch das endgültige Gewicht zu verringern. Ein Scanner mit großem Messabstand wie der LAS-XL vermisst diese Hohlräume hochpräzise. So kann das Team im Werkzeug- und Formenbau bei Materialeinsparungen und Gewichtsreduzierungen bis an die Grenzen gehen, ohne die Funktionalität des Werkzeugs zu beeinträchtigen.
Mit dem Leica T-Scan 5 lassen sich sowohl die Genauigkeit der Formfläche des gefrästen Werkzeugs als auch alle gepressten Testbauteile rasch prüfen sowie mit dem CADModell vergleichen. Dieser Prozess verläuft wesentlich schneller als bisher, da er das Hin und Her bei der wiederholten Herstellung von Prototypen reduziert und das produzierte Teil in weit weniger Prototypen-Iterationen mit dem Design in Einklang bringt.
„Das Werkzeug geht in die Produktion, um das erste Teil zu stanzen“, beschreibt Johanna Persson aus der Qualitätsabteilung. „Das Bauteil wird gescannt und auf seine Genauigkeit hin geprüft. Weicht es von den Vorgaben ab, stellt sich die Frage nach dem Warum. Der Tracker und der Scanner erleichtern es uns, das jeweilige Problem zu erkennen – bereits in den frühen Prozessphasen wissen wir dank der Scandaten wesentlich mehr und das Werkzeug muss nicht erneut gefertigt werden.”
Der Scanner kommt auch später in der Fertigungslinie zum Einsatz: sowohl für die Genauigkeitsprüfung der Teile als auch in der Werkzeuginstandhaltung. Regelmäßig werden Teile zur Qualitätsprüfung in den Werkzeug- und Formenbau gebracht. Dort erledigt das Personal mithilfe eines einfachen raschen Scans mit dem T-Scan 5 diese wichtige Aufgabe. Ein weiteres Team ist für die laufende Werkzeugwartung zuständig – und verlässt sich jetzt bei der Fehlerdiagnose ebenfalls auf die neue Ausrüstung der Kollegen vom Werkzeugbau: Ein in der Fertigung bereits eingesetztes Werkzeug, das jedoch mangelhafte Teile produziert, ist nun dank der Mobilität des Absolute Trackers mit dem T-Scan 5 rasch vor Ort überprüfbar.
Diese schnelle Identifizierung der Ursachen von Fertigungsfehlern sorgt für deutliche Zeitersparnisse im Vergleich zu einer Prüflösung, die ausschließlich im Messraum einsetzbar ist – insbesondere bei schwierig transportierbaren Teilen wie Blechstanzwerkzeugen in der Fahrzeugfertigung.
Die Möglichkeit, zwischen Scannern mit unterschiedlichen Funktionen wechseln und diese Systeme für ein breites Spektrum an Prüfanwendungen nutzen zu können, war einer der ausschlaggebenden Vorteile, der das Werkzeugbauteam in Olofström dazu bewegte, in ein Absolute Tracker-System zu investieren. „Wir haben eine ganze Reihe von Scanningsystemen geprüft. Die Anwendungsflexibilität war für uns der wichtigste Faktor, der uns letztendlich auch überzeugt hat“, berichtet Håkan Nilsson, Leitender ITArchitekt F&E und Einkauf bei der Volvo Group.
Das Werkzeug- und Formenbauteam nutzte den Absolute Tracker AT960 darüber hinaus sogar für die Erstausrichtung seiner großen Umformpresse. Dieser einmalig durchzuführende Prozess verlief mithilfe des Trackers und der Reflektoren sowie der Nivellierfunktion des AT960 unglaublich einfach.
„Hexagon unterstützte uns zwar noch mit einigen Grundlagenschulungen, aber eigentlich kannten wir uns mit der Handhabung schon aus. Wir arbeiten mit einem handgeführten Scanner inklusive PolyWorks. Daher handelte es sich zwar um ein neues System, aber das Konzept war uns bereits vertraut.”
Seitdem arbeiteten sich auch neue Teammitglieder problemlos in die aktuelle Ausrüstung ein. Hierbei kamen ausschließlich interne Schulungsressourcen zum Einsatz. Das System ist so einfach zu bedienen, dass die Teammitglieder keinen festgeschriebenen Schulungsablauf benötigen: Sie demonstrieren neuen Nutzern einfach die Handhabung des Systems und dann lernen die Neulinge am Objekt – immer an ihrer Seite ein erfahrener Nutzer, der sie beaufsichtigt und bei Fragen unterstützt.
Die Werkzeug- und Formenbauer betreiben eine ganze Reihe großer KMGs im Messraum und sehen für einige ihrer Anwendungen erneut Potential in der Aufrüstung mit programmierbaren, automatisierten Systemen. Von Streifenlichtscannern bis hin zu Robotersystemen auf Basis eines Absolute Trackers: Hexagon bietet auf jeden Fall eine breite Palette an Optionen für weitere Produktivitätssteigerungen an.
Das moderne, umweltfreundliche High-Tech-Werk in Olofström blickt auf eine nahezu 300-jährige Geschichte zurück – ursprünglich 1735 als Eisenhütte gegründet, liefert der Betrieb seit 1927 Karosserieteile für alle Volvo-Fahrzeuge. In den 50 Jahren seit dem Kauf des Werks durch Volvo im Jahr 1969 spezialisierte sich der Standort auf die Pressumformung und Vormontage von Karosserieteilen für das gesamte Volvo- Fahrzeugangebot sowie für externe Kunden wie Volvo Trucks, Ford und Land Rover.
Die ersten Produktionsphasen des Fahrzeugkonstruktionsprozesses bei Volvo basieren maßgeblich auf der Entwicklung der Blechstanzwerkzeuge, die vom Werkzeug- und Formenbau in Olofström konstruiert und gefertigt werden. Zunächst ist das Team für die Herstellung der Werkzeugprototypen verantwortlich. Bei bis zu 80 benötigten Werkzeugen für ein Fahrzeugprojekt kann diese Aufgabe vier bis fünf Monate in Anspruch nehmen. In aller Regel dauert jedes Projekt insgesamt etwa ein Jahr. Die verbleibende Zeit ist für die Produktion der endgültigen Werkzeuge reserviert, mit denen Hunderttausende von Karosseriekomponenten gepresst werden.
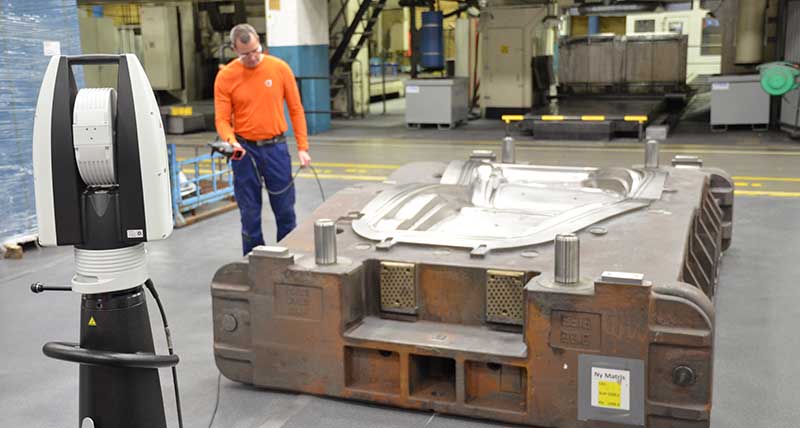
Da in den Hauptfertigungsbereichen des Werks in Olofström bereits verschiedene Absolute Tracker-Systeme zum Einsatz kamen, war die Entscheidung für zusätzliche Laser Tracker-Lösungen von Hexagon der logische nächste Schritt – vor allem aufgrund des intern bereits vorhandenen Fachwissens sowie der bekannten Mobilität und Flexibilität der Absolute Tracker-Systeme.
Verbesserung des ersten Gussteils
Der erste Herstellungsschritt bei konstruierten Prototypen oder fertigen Werkzeugen ist das Feinfräsen eines gegossenen Blocks aus dem Rohmaterial. Das Gießen selbst ist kein präziser Vorgang. Gegossene Teile werden daher in aller Regel mit einem hohen Anteil an überschüssigem Material geliefert, das im Nachgang mit einer CNC-Fräsmaschine auf die genauen Maße und die gewünschte Form gebracht wird.Ein wesentlicher Schritt beim Einrichten eines Gussteils für das Fräsen besteht darin, Kollisionen zwischen dem Bauteil und der Werkzeugmaschine beim Positionieren vor der Fräsbearbeitung zu vermeiden. Derartige Kollisionen können zu besonders kosten- und zeitintensiven Schäden an der CNC-Fräsmaschine führen. Aufgrund dessen muss das Bedienpersonal beim Einrichten darauf achten, die Maschinen so weit entfernt vom Material zu positionieren, dass es garantiert zu keiner Kollision kommt. Dies nach Augenmaß vorzunehmen ist nicht einfach und bedeutet oftmals erhebliche Leerlaufzeiten für die Fräsmaschine zu Beginn ihres Programms.
„Mit den Eingangsscandaten lässt sich an dieser Stelle erheblich Zeit sparen“, erklärt Kim Tingstedt, Bediener im Werkzeug- und Formenbau bei VCBC Olofström. „Wird das Fräsprogramm auf die tatsächlichen Abmaße des Materials hin optimiert, führt das zu enormen Zeitersparnissen, denn die Geschwindigkeit der Maschine bleibt dieselbe – ob sie nun durch Luft oder Material fährt. Die Durchlaufzeit unserer Fräsmaschinen hat sich deutlich verbessert, sodass wir nun eine größere Anzahl an Teilen und Werkzeugen bearbeiten können.”
Obwohl diese Optimierung auch vorher schon durchgeführt wurde, gestalten sich die Abläufe dank der umfassenden Scandaten des LAS-XL nun wesentlich einfacher. „Mit dem jetzigen Scanvorgang stehen unseren Konstrukteuren entscheidend mehr Informationen als bisher zur Verfügung. Unsere vorherige KMG-Lösung lieferte lediglich Punkte“, sagt Kim Tingstedt. „Der Konstrukteur kann diese Daten direkt mit an der CNCMaschine nutzen und das Frästeil wesentlich einfacher optimieren, weil er das Teil praktisch sieht.”
Die Durchlaufzeit der Fräsmaschinen verbesserte sich entscheidend.Diese Gussteil-Scandaten sind darüber hinaus noch auf andere Weise für Produktionssteigerungen nutzbar. Gegossene Werkzeuge sind extrem schwer und lassen sich nur eingeschränkt bewegen. Daher erleichtert jede Gewichtsreduzierung ihre Verwendung und verringert gleichzeitig den Rohmaterialbedarf. Das bedeutet, die Menge an Rohmaterial muss so klein wie möglich sein – jedoch auch nicht zu gering. Bleibt zu wenig Material zwischen der Außenseite des Werkzeugs und der Innenseite seiner Präzisionsform übrig, ist es nicht mehr widerstandsfähig genug, um wiederholten Hochleistungspresskräften standzuhalten.
Mithilfe der Scandaten des ersten Gussteils lässt sich der Gießvorgang der nachfolgenden Prototypen und Werkzeuge präzisieren, um das geringstmögliche Gewicht und minimalen Materialverbrauch zu gewährleisten, ohne die strukturelle Integrität des Werkzeugs zu beeinträchtigen. Ein weiterer Vorteil hierbei ist, dass jeder Fräsdurchlauf näher an der endgültigen Teileform beginnen kann – das vergrößert zusätzlich die Zeitersparnis bei jedem Schritt.
Der Leica Absolute Scanner LAS-XL ist die perfekte Lösung für diesen Scanningprozess. Dank seiner breiten Scanlinie und dem großen Messabstand lassen sich Gussteile rasch scannen. Damit bietet sich das Scannen als zeitsparende Alternative gegenüber einem großen Sicherheitsfaktor beim Fräsen an.
Mit dem marktführenden Messabstand des LAS-XL lassen sich sogar verborgene Punkte in den Hohlräumen messen, die sich konstruktionsbedingt innerhalb der Werkzeuge befinden, um sowohl den Materialverbrauch als auch das endgültige Gewicht zu verringern. Ein Scanner mit großem Messabstand wie der LAS-XL vermisst diese Hohlräume hochpräzise. So kann das Team im Werkzeug- und Formenbau bei Materialeinsparungen und Gewichtsreduzierungen bis an die Grenzen gehen, ohne die Funktionalität des Werkzeugs zu beeinträchtigen.
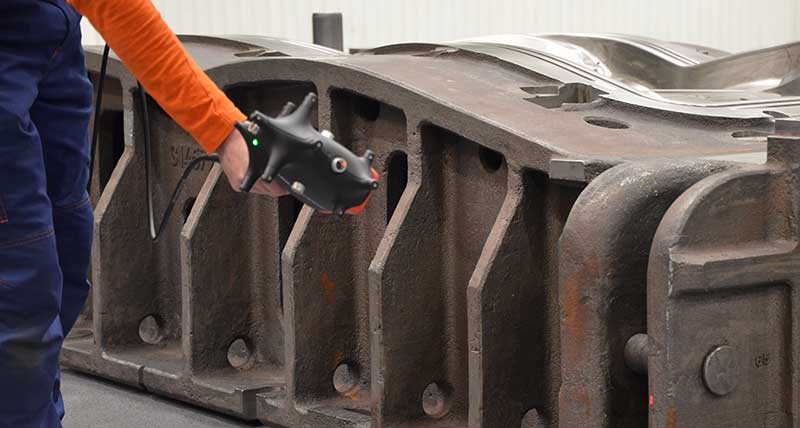
Abschließende Kontrolle der Werkzeugqualität
Nach dem Beenden des Fräsprozesses gilt es, die Qualität des gefertigten Werkzeugs zu prüfen. Dies erfordert einen noch feineren Grad der Messung als es mit dem LAS-XL möglich ist. Da der Absolute Tracker AT960 jedoch eine Reihe kompatibler Scanninglösungen bietet, musste das Team zum Erfüllen dieser Anforderung lediglich in einen zusätzlichen hochdynamischen Scanner investieren.Mit dem Leica T-Scan 5 lassen sich sowohl die Genauigkeit der Formfläche des gefrästen Werkzeugs als auch alle gepressten Testbauteile rasch prüfen sowie mit dem CADModell vergleichen. Dieser Prozess verläuft wesentlich schneller als bisher, da er das Hin und Her bei der wiederholten Herstellung von Prototypen reduziert und das produzierte Teil in weit weniger Prototypen-Iterationen mit dem Design in Einklang bringt.
„Das Werkzeug geht in die Produktion, um das erste Teil zu stanzen“, beschreibt Johanna Persson aus der Qualitätsabteilung. „Das Bauteil wird gescannt und auf seine Genauigkeit hin geprüft. Weicht es von den Vorgaben ab, stellt sich die Frage nach dem Warum. Der Tracker und der Scanner erleichtern es uns, das jeweilige Problem zu erkennen – bereits in den frühen Prozessphasen wissen wir dank der Scandaten wesentlich mehr und das Werkzeug muss nicht erneut gefertigt werden.”
Der Scanner kommt auch später in der Fertigungslinie zum Einsatz: sowohl für die Genauigkeitsprüfung der Teile als auch in der Werkzeuginstandhaltung. Regelmäßig werden Teile zur Qualitätsprüfung in den Werkzeug- und Formenbau gebracht. Dort erledigt das Personal mithilfe eines einfachen raschen Scans mit dem T-Scan 5 diese wichtige Aufgabe. Ein weiteres Team ist für die laufende Werkzeugwartung zuständig – und verlässt sich jetzt bei der Fehlerdiagnose ebenfalls auf die neue Ausrüstung der Kollegen vom Werkzeugbau: Ein in der Fertigung bereits eingesetztes Werkzeug, das jedoch mangelhafte Teile produziert, ist nun dank der Mobilität des Absolute Trackers mit dem T-Scan 5 rasch vor Ort überprüfbar.
Diese schnelle Identifizierung der Ursachen von Fertigungsfehlern sorgt für deutliche Zeitersparnisse im Vergleich zu einer Prüflösung, die ausschließlich im Messraum einsetzbar ist – insbesondere bei schwierig transportierbaren Teilen wie Blechstanzwerkzeugen in der Fahrzeugfertigung.
Die Möglichkeit, zwischen Scannern mit unterschiedlichen Funktionen wechseln und diese Systeme für ein breites Spektrum an Prüfanwendungen nutzen zu können, war einer der ausschlaggebenden Vorteile, der das Werkzeugbauteam in Olofström dazu bewegte, in ein Absolute Tracker-System zu investieren. „Wir haben eine ganze Reihe von Scanningsystemen geprüft. Die Anwendungsflexibilität war für uns der wichtigste Faktor, der uns letztendlich auch überzeugt hat“, berichtet Håkan Nilsson, Leitender ITArchitekt F&E und Einkauf bei der Volvo Group.
Das Werkzeug- und Formenbauteam nutzte den Absolute Tracker AT960 darüber hinaus sogar für die Erstausrichtung seiner großen Umformpresse. Dieser einmalig durchzuführende Prozess verlief mithilfe des Trackers und der Reflektoren sowie der Nivellierfunktion des AT960 unglaublich einfach.
Learning by doing
Nach Erhalt der Tracker- und Scannersysteme war das Team ohne viel Unterstützung vom Hexagon-Supportteam schnell mit der Ausrüstung vertraut. „Der Absolute Tracker ist bei Volvo bereits seit Langem bestens bekannt, sodass wir auf vorhandenes Fachwissen zurückgreifen konnten“, berichtet Fredrik Sjöberg, Prototypenbauingenieur bei Volvo Car.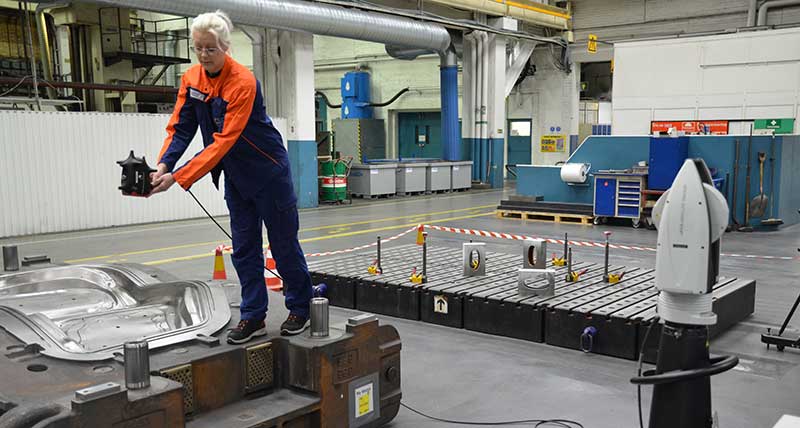
Seitdem arbeiteten sich auch neue Teammitglieder problemlos in die aktuelle Ausrüstung ein. Hierbei kamen ausschließlich interne Schulungsressourcen zum Einsatz. Das System ist so einfach zu bedienen, dass die Teammitglieder keinen festgeschriebenen Schulungsablauf benötigen: Sie demonstrieren neuen Nutzern einfach die Handhabung des Systems und dann lernen die Neulinge am Objekt – immer an ihrer Seite ein erfahrener Nutzer, der sie beaufsichtigt und bei Fragen unterstützt.
Die Zukunft des Messens
Das Werkzeug- und Formenbauteam im Volvo Car Body Components Zentrum in Olofström ist überaus zufrieden mit den neu implementierten Scannersystemen von Hexagon. Darüber hinaus führen die Verantwortlichen bereits Gespräche, weitere moderne Messsysteme in der Abteilung einzuführen.Die Werkzeug- und Formenbauer betreiben eine ganze Reihe großer KMGs im Messraum und sehen für einige ihrer Anwendungen erneut Potential in der Aufrüstung mit programmierbaren, automatisierten Systemen. Von Streifenlichtscannern bis hin zu Robotersystemen auf Basis eines Absolute Trackers: Hexagon bietet auf jeden Fall eine breite Palette an Optionen für weitere Produktivitätssteigerungen an.