Volvoが手に入れた計測の自由
AT960、LAS-XLおよびT-Scan 5で プロトタイプ製造における生産性を向上
お問い合わせ先
約2,400人の従業員が勤務するオロフストロムのVolvo Car Body Components (VCBC)は、毎年数百万台にものぼる車体部品を生産する自動車関連生産工場です。フード、ルーフからドア、サブアセンブリまで、世界中のVolvo自動車工場に向けて完成品または半完成品として出荷され、組み立てに使用される重要な自動車構成部品の板金プレス加工に特化しています。
オロフストロムの先端技術を使用した環境にやさしい最新鋭工場には、およそ300年の歴史があります。当初鉄工所として1735年に設立され、1927年以来Volvoのすべての自動車用本体部品を納品してきました。1969年にVolvoによって買収されて以来、過去50年にわたって、Volvo車両の全種類の取り扱いに加え、Volvoトラック、フォードおよびランドローバーをはじめとする外部顧客向け車体部品のプレス加工、半完成品組み立て工程を引き受けてきました。
Volvoの自動車設計過程で最も初期の生産ステージは、オロフストロムのツールとダイ加工チームによって設計・製造された板金加工ツールの開発が非常に大きな役割を果たしてきました。チームは、当初ツールプロトタイプ生産を行っていました。車両には80点あまりのツールが必要とされ、業務には4~5か月をかけていました。プロジェクトは典型的には一年間で、残りの期間は、数十万もの車体構成部品のプレスに使用される最終ツーリングの生産に特化しています。
2018年には、生産性の改善を目指して、ツールプロトタイプ政策と生産に最新鋭の計測ソリューションを導入することが決定されました。まず、設計、生産および品質保証プロセスで高度な計測ツールの導入が潜在的に役立つと考えられる主なステップを識別しました。チームには既に充実した大規模な品質保証室があり、水平アームCMMから、ストラクチャーライトスキャナーまで、広範囲の計測ハードウェアに精通していました。現在市場で利用可能な多くのソリューションの検討が行われ、特に現場でも品質保証室でも利用できることが、重要な問題でした。
オロフストロムプラントの主要部品製造エリアではAbsolute Trackerシステムがすでに使用されていました。社内技術者は、Absolute Trackerシステムで評判のポータビリティと柔軟性を活用しており、Hexagonのレーザートラッカーシステムを追加したことはきわめて自然な流れでした。
最初の鋳造加工作業の改善
設計されたプロトタイプや最終ツールを製造するための最初のステップは、原材料の鋳造ブロックの精密ミーリング加工です。 鋳造は精密プロセスではなく、鋳造部品は通常、フライス加工で余分な材料部分を削り落としてから、CNCフライス盤で正確なサイズと形を整えます。
設定の重要なステップは、鋳造部品のミーリング加工が始まる前に部品を移動するにあたってミーリングマシンと部品の間に衝突がないことを保証することです。こうした衝突から結果としてCNCミーリングマシンへの損害が生じる場合があり、こうした損害はコストも時間も浪費してしまいます。したがって、オペレーターはセットアップの時点で、安全係数を導入することが必要となります - これは、機械のポジショニングで衝突が生じないよう距離を十分にとることを意味します。この作業を目視で行うことは容易ではなく、またミーリングマシンが加工プログラムを開始する前にアイドル運転を行うため、多くの余分な時間がかかってしまいます。
「最初にデータスキャンを行うことは、時間の浪費を回避できます。」VCBC オロフストロムツールのダイオペレーター、キム・ティングステルト(Kim Tingstedt)氏はこう話します。「ミーリングプログラムを材料の実寸に合わせて最適化できるため、大きな時間の節約になります。また同じ速度ですが、アイドル運転ではなく実際の加工を行うことができます。 現在ではミーリングマシンのリードタイムが改善され、より多くの部品やツールを生産できます。」
この最適化は以前に行なわれたものですが、LAS-XLによって包括的なスキャンデータが提供されることで、作業はこれまでよりも遥かにやりやすくなっています。「スキャン作業によって『点』の情報のみだった以前のCMMソリューションと比較してより多くのデータが得られ、情報量が増しています。」キム・ティングステルト氏はさらに続けます。「このデータはCNC機に取り込み、また実際に部品を見ることができるので、ミーリング部品を遥かに容易に最適化できるようになっています。」
現在では、ミーリングマシンのリードタイムは大きく改善されています。この鋳造スキャンデータは、さまざまな方法で生産を改善するために役立てられています。 鋳造ツールは、きわめて重く移動は非常に困難です。したがって、軽量化によって大きく使いやすさが改善され、必要な原料の量を減らせます。これは、ツールができるだけ小さいほうが望ましいことを意味します - どんなに小さくても小さすぎることはありません。ツールの外部と、精密型の内側に十分な材料が残っていないと、高性能の打ち抜き加工の繰り返しに耐える強度は期待できません。
鋳造後のスキャンデータを使用することで、次のプロトタイプの鋳造と最終ツールは大幅に洗練させることができます。ツールの構造の完全性を損なうことなく、重量を最小化し、材料の消費を削減できます。これにはさらにミーリング加工の作業の各サイクルで最終部品形状に近い状態で作業を始めることができ、各ステップで時間を節約できる利点もあります。
Leica Absolute Scanner LAS-XLは、こうしたスキャンプロセスに最適なツールです。広いスキャンラインと大きなスタンドオフで、鋳造部品をきわめて迅速にスキャンすることができます。これは、ミーリング加工で、安全係数を実装するのではなく、スキャンによってより迅速にプロセスを進められることを意味しています。
LAS-XLの市場をリードするスタンドオフ測定なら、ツーリングで設計されたキャビティ内の隠れたポイントを測定し、材料消費と最終重量を削減することができます。 LAS-XLのような大型スタンドオフスキャナーは、これらのキャビティを正確にに測定し、ツールとダイ加工チームは、材料を節約しツールの機能に妥協せず軽量化を図り、可能性を広げます。
最終ツール品質検査
生産プロセスのミーリング加工後、最終ツールの精度チェックが行われます。これは、LAS-XLによるより高精度の測定を要求します。しかし多くの互換性をもつスキャンソリューションを提供するAbsolute Tracker AT960と合わせることで、チームで新たに必要となったものはハイエンドダイナミックスキャナーだけでした。
Leica T-Scan 5なら、フライスツーリングの型エリアとテストプレスの両方で、迅速な検査スキャンとCADとの比較を行うことができます。インライン生産部品でプロトタイプ設計の反復作業が減り、プロトタイプ生産の繰り返しが削減されたことで、以前と比較してプロセスははるかに高速化されました。
「ツールはまず型押し加工が行われる」と品質管理部のジョアンナ・ぺルソン(Johanna Persson)氏は言います。「部品はスキャンによって精度が検査されます。また許容範囲を外れた場合は原因を調査します。トラッカーとスキャナーによって、問題をより簡単に突き止められるようになりました。スキャンデータがあれば問題が初期の段階で判明するため、再構築の必要がなくなります。
さらに、スキャナーは生産ラインの下流のチェックにもツール・メンテナンスにも役立っています。部品は、定期的にツールとダイ加工チームによる品質検査が行われていますが、この作業もT-Scan 5の高速スキャンによって容易に行なうことができるようになっています。また、進行中のツール・メンテナンスは別のチームが担当していますが、このチームも、問題を分析する場合ツールとダイ加工チームの新しい機器を大いに活用しています。Absolute TrackerおよびT-Scan 5は持ち運びやすいため、すでに生産ライン上にあるツーリングが十分な品質の部品を出力していない場合も、現場ですぐに検査することができます。特に自動車の板金ツールのように移動が困難な部品では、品質保証室から動かせない検査ソリューションと比較して、製造上の欠陥の原因を迅速に識別することで、大きく時間を節約できます。
スキャナー間でさまざまな機能を切り替えて、かつこれらのシステムを広範囲の検査アプリケーションに適用できることが、オロフストロムのツールとダイ加工チームがAbsolute Trackerシステムを選んだ重要な利点のうちの1つでした。「私たちは多くのスキャンシステムで、使用方法の柔軟性を検証しました。さまざまな目的に使えることが重要な条件の一つだったのです」と、VolvoグループのITアーキテクト開発および調達チームを率いるハーカン・ニルソン(Håkan Nilsson)氏は言います。
ツールとダイ加工チームでは、Absolute Tracker AT960を大型プレスマシンの最初のアラインメントにも使います。トラッカーとリフレクター、そしてAT960の指向性-重力機能を活用することで、一度だけのこのプロセスは非常にシンプルになっています。
実践から学ぶ
トラッカーとスキャナー・システムの納品を受けて、チームは迅速に運用を開始しました。Hexagonサポートチームの支援はほとんど必要としませんでした。「Absolute TrackerはVolvo社内でも有名です。Volvoで非常に長い間使われてきており、ユニットではすでに専門知識を持っていました。」Volvo Car社のプロトタイプ構築技術者、フレデリック・シェーベリ(Fredrik Sjöberg)氏はこう話しています。
「Hexagonは基本的な研修を準備しましたが、私たちはすでに最初から操作方法をかなり詳しく把握していました。これまでも、私たちはハンドスキャナーとPolyWorksを使用していました。今回は新しいシステムとはいえ、その概念は既に私たちもよく知っているものだったのです。」
新しいチーム・メンバーが機器を使い始めるのに必要だったものは、社内研修資料だけでした。システムの使い方は非常にシンプルで、チームに正式な研修の必要はありませんでした- 操作方法を実際に示し、初心者には熟練者が側について、実際に機器を使いながら操作を覚えていくことができます。
測定の未来
オロフストロムにあるVolvo Car車体部品センターのツールとダイ加工チームは、新しいHexagonスキャナーシステムの実装に非常に感銘を受け、部門内でより高度な計測ツールの導入に向けた検討も既に進行中です。
品質管理室では多くの大型CMMを操作し、多くのアプリケーションで、プログラム可能な自動システムのアップグレードにさまざまなポテンシャルを見いだしています。ストラクチャーライトスキャナーからAbsolute TrackerによるロボットシステムまでHexagonには、生産性の向上につながる幅広いオプションがあります。
オロフストロムの先端技術を使用した環境にやさしい最新鋭工場には、およそ300年の歴史があります。当初鉄工所として1735年に設立され、1927年以来Volvoのすべての自動車用本体部品を納品してきました。1969年にVolvoによって買収されて以来、過去50年にわたって、Volvo車両の全種類の取り扱いに加え、Volvoトラック、フォードおよびランドローバーをはじめとする外部顧客向け車体部品のプレス加工、半完成品組み立て工程を引き受けてきました。
Volvoの自動車設計過程で最も初期の生産ステージは、オロフストロムのツールとダイ加工チームによって設計・製造された板金加工ツールの開発が非常に大きな役割を果たしてきました。チームは、当初ツールプロトタイプ生産を行っていました。車両には80点あまりのツールが必要とされ、業務には4~5か月をかけていました。プロジェクトは典型的には一年間で、残りの期間は、数十万もの車体構成部品のプレスに使用される最終ツーリングの生産に特化しています。
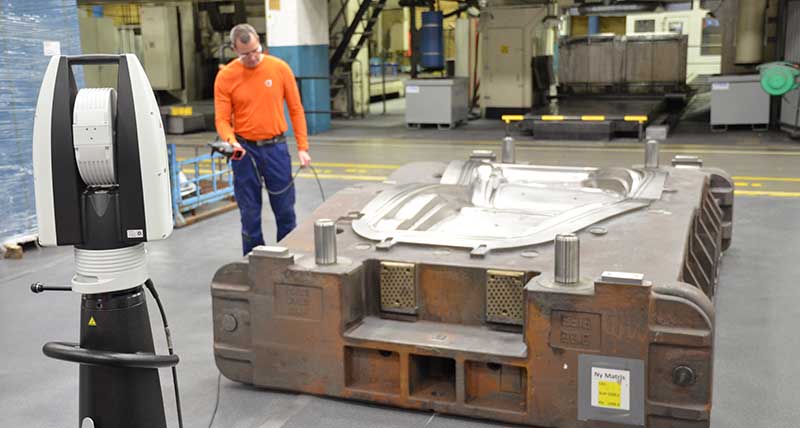
オロフストロムプラントの主要部品製造エリアではAbsolute Trackerシステムがすでに使用されていました。社内技術者は、Absolute Trackerシステムで評判のポータビリティと柔軟性を活用しており、Hexagonのレーザートラッカーシステムを追加したことはきわめて自然な流れでした。
最初の鋳造加工作業の改善
設計されたプロトタイプや最終ツールを製造するための最初のステップは、原材料の鋳造ブロックの精密ミーリング加工です。 鋳造は精密プロセスではなく、鋳造部品は通常、フライス加工で余分な材料部分を削り落としてから、CNCフライス盤で正確なサイズと形を整えます。
設定の重要なステップは、鋳造部品のミーリング加工が始まる前に部品を移動するにあたってミーリングマシンと部品の間に衝突がないことを保証することです。こうした衝突から結果としてCNCミーリングマシンへの損害が生じる場合があり、こうした損害はコストも時間も浪費してしまいます。したがって、オペレーターはセットアップの時点で、安全係数を導入することが必要となります - これは、機械のポジショニングで衝突が生じないよう距離を十分にとることを意味します。この作業を目視で行うことは容易ではなく、またミーリングマシンが加工プログラムを開始する前にアイドル運転を行うため、多くの余分な時間がかかってしまいます。
「最初にデータスキャンを行うことは、時間の浪費を回避できます。」VCBC オロフストロムツールのダイオペレーター、キム・ティングステルト(Kim Tingstedt)氏はこう話します。「ミーリングプログラムを材料の実寸に合わせて最適化できるため、大きな時間の節約になります。また同じ速度ですが、アイドル運転ではなく実際の加工を行うことができます。 現在ではミーリングマシンのリードタイムが改善され、より多くの部品やツールを生産できます。」
この最適化は以前に行なわれたものですが、LAS-XLによって包括的なスキャンデータが提供されることで、作業はこれまでよりも遥かにやりやすくなっています。「スキャン作業によって『点』の情報のみだった以前のCMMソリューションと比較してより多くのデータが得られ、情報量が増しています。」キム・ティングステルト氏はさらに続けます。「このデータはCNC機に取り込み、また実際に部品を見ることができるので、ミーリング部品を遥かに容易に最適化できるようになっています。」
現在では、ミーリングマシンのリードタイムは大きく改善されています。この鋳造スキャンデータは、さまざまな方法で生産を改善するために役立てられています。 鋳造ツールは、きわめて重く移動は非常に困難です。したがって、軽量化によって大きく使いやすさが改善され、必要な原料の量を減らせます。これは、ツールができるだけ小さいほうが望ましいことを意味します - どんなに小さくても小さすぎることはありません。ツールの外部と、精密型の内側に十分な材料が残っていないと、高性能の打ち抜き加工の繰り返しに耐える強度は期待できません。
鋳造後のスキャンデータを使用することで、次のプロトタイプの鋳造と最終ツールは大幅に洗練させることができます。ツールの構造の完全性を損なうことなく、重量を最小化し、材料の消費を削減できます。これにはさらにミーリング加工の作業の各サイクルで最終部品形状に近い状態で作業を始めることができ、各ステップで時間を節約できる利点もあります。
Leica Absolute Scanner LAS-XLは、こうしたスキャンプロセスに最適なツールです。広いスキャンラインと大きなスタンドオフで、鋳造部品をきわめて迅速にスキャンすることができます。これは、ミーリング加工で、安全係数を実装するのではなく、スキャンによってより迅速にプロセスを進められることを意味しています。
LAS-XLの市場をリードするスタンドオフ測定なら、ツーリングで設計されたキャビティ内の隠れたポイントを測定し、材料消費と最終重量を削減することができます。 LAS-XLのような大型スタンドオフスキャナーは、これらのキャビティを正確にに測定し、ツールとダイ加工チームは、材料を節約しツールの機能に妥協せず軽量化を図り、可能性を広げます。
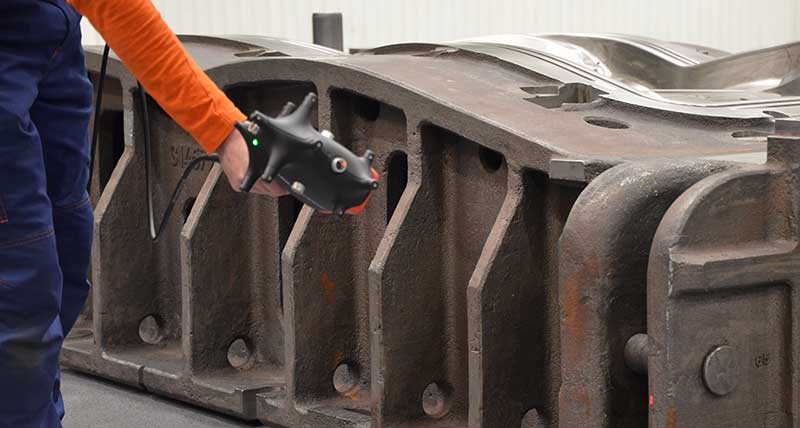
生産プロセスのミーリング加工後、最終ツールの精度チェックが行われます。これは、LAS-XLによるより高精度の測定を要求します。しかし多くの互換性をもつスキャンソリューションを提供するAbsolute Tracker AT960と合わせることで、チームで新たに必要となったものはハイエンドダイナミックスキャナーだけでした。
Leica T-Scan 5なら、フライスツーリングの型エリアとテストプレスの両方で、迅速な検査スキャンとCADとの比較を行うことができます。インライン生産部品でプロトタイプ設計の反復作業が減り、プロトタイプ生産の繰り返しが削減されたことで、以前と比較してプロセスははるかに高速化されました。
「ツールはまず型押し加工が行われる」と品質管理部のジョアンナ・ぺルソン(Johanna Persson)氏は言います。「部品はスキャンによって精度が検査されます。また許容範囲を外れた場合は原因を調査します。トラッカーとスキャナーによって、問題をより簡単に突き止められるようになりました。スキャンデータがあれば問題が初期の段階で判明するため、再構築の必要がなくなります。
さらに、スキャナーは生産ラインの下流のチェックにもツール・メンテナンスにも役立っています。部品は、定期的にツールとダイ加工チームによる品質検査が行われていますが、この作業もT-Scan 5の高速スキャンによって容易に行なうことができるようになっています。また、進行中のツール・メンテナンスは別のチームが担当していますが、このチームも、問題を分析する場合ツールとダイ加工チームの新しい機器を大いに活用しています。Absolute TrackerおよびT-Scan 5は持ち運びやすいため、すでに生産ライン上にあるツーリングが十分な品質の部品を出力していない場合も、現場ですぐに検査することができます。特に自動車の板金ツールのように移動が困難な部品では、品質保証室から動かせない検査ソリューションと比較して、製造上の欠陥の原因を迅速に識別することで、大きく時間を節約できます。
スキャナー間でさまざまな機能を切り替えて、かつこれらのシステムを広範囲の検査アプリケーションに適用できることが、オロフストロムのツールとダイ加工チームがAbsolute Trackerシステムを選んだ重要な利点のうちの1つでした。「私たちは多くのスキャンシステムで、使用方法の柔軟性を検証しました。さまざまな目的に使えることが重要な条件の一つだったのです」と、VolvoグループのITアーキテクト開発および調達チームを率いるハーカン・ニルソン(Håkan Nilsson)氏は言います。
ツールとダイ加工チームでは、Absolute Tracker AT960を大型プレスマシンの最初のアラインメントにも使います。トラッカーとリフレクター、そしてAT960の指向性-重力機能を活用することで、一度だけのこのプロセスは非常にシンプルになっています。
実践から学ぶ
トラッカーとスキャナー・システムの納品を受けて、チームは迅速に運用を開始しました。Hexagonサポートチームの支援はほとんど必要としませんでした。「Absolute TrackerはVolvo社内でも有名です。Volvoで非常に長い間使われてきており、ユニットではすでに専門知識を持っていました。」Volvo Car社のプロトタイプ構築技術者、フレデリック・シェーベリ(Fredrik Sjöberg)氏はこう話しています。
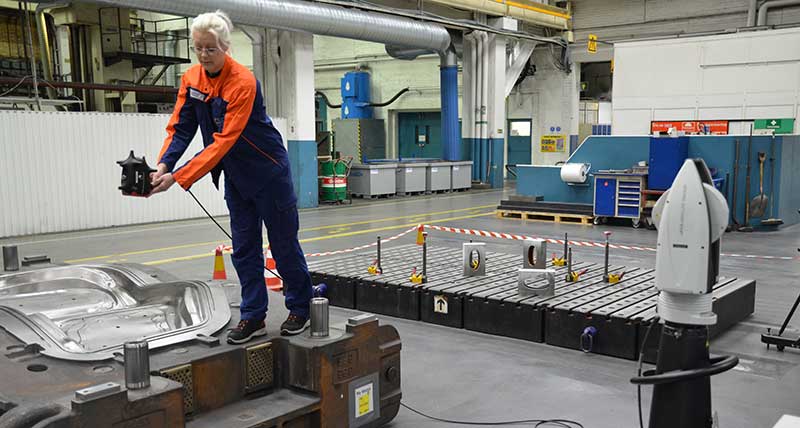
新しいチーム・メンバーが機器を使い始めるのに必要だったものは、社内研修資料だけでした。システムの使い方は非常にシンプルで、チームに正式な研修の必要はありませんでした- 操作方法を実際に示し、初心者には熟練者が側について、実際に機器を使いながら操作を覚えていくことができます。
測定の未来
オロフストロムにあるVolvo Car車体部品センターのツールとダイ加工チームは、新しいHexagonスキャナーシステムの実装に非常に感銘を受け、部門内でより高度な計測ツールの導入に向けた検討も既に進行中です。
品質管理室では多くの大型CMMを操作し、多くのアプリケーションで、プログラム可能な自動システムのアップグレードにさまざまなポテンシャルを見いだしています。ストラクチャーライトスキャナーからAbsolute TrackerによるロボットシステムまでHexagonには、生産性の向上につながる幅広いオプションがあります。