Sous le signe de la connectivité 2.0
La fabrication des tubes requiert de plus en plus de précision et les parcours souvent complexes nécessitent des moyens de réglages importants.
Contactez-nous

ContiTech Anoflex, filiale du groupe Continental depuis 1988, est partenaire de développement et d’équipementier automobile de première monte pour les tuyaux et flexibles ainsi que les systèmes complets de conduites en élastomères, acier, inox et aluminium pour transfert de fluides.
Le site de Caluire, à coté de Lyon, est spécialisé dans les secteurs automobile – environnement moteur, lubrification et refroidissement de turbo compresseur – poids lourds et bus. Les plus grands constructeurs ainsi que les consortiums de fabriquants de moteurs comptent parmi leurs fidèles clients.
Historiquement fabricante de raccords de pompes à vélo dans les années 60, la société française a connu un bel essor et développement à travers le temps, pour devenir un leader dans la conception et la fabrication de flexibles permettant le transport des fluides.
ContiTech Anoflex compte parmi les premiers utilisateurs enthousiastes du premier bras de mesure polyarticulé Système 6 de ROMER dans les années 1990, acquit après le rachat de la société par le groupe Continental en 1988.
Installé dans un environnement climatisé, le premier bras de mesure a su répondre longtemps aux besoins de mesure tridimensionnelle de tubes, utilisant les logiciels G-Pad pour les prototypes et G-Tube pour la production. Maurice Carrier, responsable informatique industrielle se souvient: « La philosophie de notre société est l’acquisition de matériel de qualité que nous utilisons le plus longtemps possible. Lorsque le Système 6 est tombé en panne, après de nombreuses années de bons et loyaux services, Hexagon, alors encore ROMER, nous a prêté un nouveau bras dans les 48 heures.»
Proximité et réactivité sont des mots-clés dans notre relation avec Hexagon.
L’ appréciation du service offert ainsi que la connaissance des exigences des clients a motivé ContiTech Anoflex à rester fidèle à ROMER. L’acquisition d’un bras SIGMA, toujours en utilisation, une dizaine d’années après leur première machine de mesure tridimensionnelle portable suivi de deux Absolute Arm plus récemment en sont la preuve.
Robotisation des cintrages et industrie 4.0
L’arrivée de cellules de cintrage robotisées, offrant à la fois fiabilité et automation notamment pour le déchargement de tube a changé les protocoles de mesure et les conditions de travail.«Les nouvelles cintreuses électriques sont beaucoup plus fiables et nous permettent de nous éloigner des contrôles à 100% comme nous avions l’habitude de faire. Les nouveaux logiciels TubeShaper d’Hexagon communiquent dans les deux sens et on peut récupérer les réglages précédents d’une machine. On fait une pièce, même complexe, qui est quasiment bonne dès le départ. Après quelques corrections, la seconde est toujours bonne ! La machine étant plus fiable, les contrôles s’adaptent.» indique Monsieur Carrier.
Comme 80% de la production des tubes a des composants, éléments rapportés ou des embouts formés, une solution de mesure automatisée tel que TubeInspect ne s’avérait pas idéale. Un nouvel Absolute Arm, situé au milieu de l’atelier, tout proche des cintreuses, représentait la meilleure solution. De plus, comme les produits hydroformés nécessitent également des mesures en palpage, le bras offrait la flexibilité idéale, devenant un réel outil de réglage en collaboration avec les cintrages.
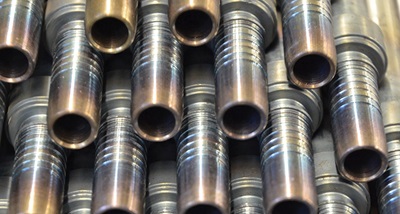
« Nos projets doivent aller toujours plus vite et sont toujours plus complexes. L’ Absolute Arm nous permet de passer du scanner au palpage de façon transparente » indique Hervé Matta, l’un des cinq utilisateurs du bras de mesure au niveau prototype, qui continue: « La combinaison de TubeShaper et palpage représente un super avantage et offre une multifonctionnalité totale de la solution. Surtout sur des tubes complexes, avec spirales par exemple, que l’on ne peut pas palper avec la sonde en V.»
«L’utilisation du protocole SV Network offre un grand avantage et rend les connections avec les cintreuses très simples. Les procédures établies nous permettent en très peu de temps de mettre une cintreuse sur réseau, d’effectuer les paramétrages et de l’intégrer dans TubeShaper.».
Le responsable informatique industrielle et l’utlisateur apprécient également la réactivité du service après-vente de Hexagon: « un bras de rechange est immédiatement fournit lorsque l’un des notres nécessite une calibration. L’Absolute Arm est vraiment autonome. On branche le remplaçant et il fonctionne immédiatement. Même le vieux bras SIGMA reçoit encore le meilleur support possible, même une fois rentré en obsolescence*».
Au fil des années ContiTech Anoflex et Hexagon ont renforcé leur partenariat afin d’améliorer les fonctionnalités de Tubeshaper, ce qui nous a permis de mettre en place une solution performante répondant aux exigences de qualité de plus en plus élevées de nos clients. Dans le service production, ce sont près de dix régleurs qui utilisent régulièrement le bras ainsi qu’une personne du service qualité. Les mesures se font toute la journée sur deux équipes. Monsieur Carrier apprécie notamment «la vitesse de changement de série. On gagne facilement 15 minutes par séries. Si on en fait dix séries par jour, on gagnera 2.5 heures ! Fini les embouteillages sur le matériel. On va vraiment plus vite.»
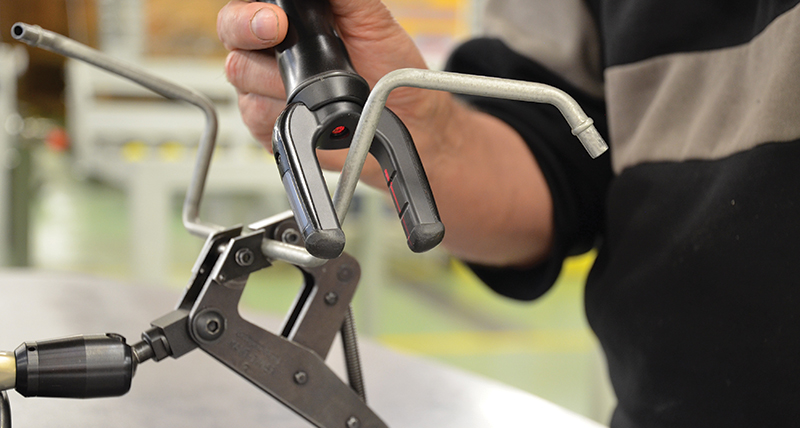
Passer simplement de G-Tube à TubeShaper
Lors du changement de bras et de logiciel, ContiTech Anoflex a pu récupérer toutes les anciennes références de G-Tube très simplement et les importer directement sur TubeShaper. Cela a représenté un gain de temps très important sur la quantité de références que ContiTech Anoflex offre. Aujourd’hui elles sont directement importées depuis le bureau d’études.Notre système de PDM (Product Data Management) inclus la génération d’un fichier qui permet de récupérer automatiquement les coordonnées du tube, directement compatible avec TubeShaper et intégré dans le système de PDM. Les designers du bureau d’étude ne génèrent qu’un plan de fabrication. Il n’y a ainsi plus aucune erreur de saisie grâce au travail directement effectué dans le repère véhicule. Tous les équipements sont en réseau via Ethernet et tous les logiciels sont compatibles. Fini les disquettes, clés USB et autres! Ceci a contribué dès à présent à la vision interconnectée de l’usine 4.0 du groupe Continental.» conclue Monsieur Carrier.
*Hexagon garantie les pièces et services liés à ses bras de mesure 10 ans après la fin de leur production.