Fiabilité et productivité des processus
Contact

Des palpeurs de mesure avec transmission de données par infrarouge, des systèmes de mesure d’outils laser et des logiciels de mesure, tous conçus par m&h, assurent la sécurité des processus et le rendement satisfaisant du centre d’usinage au sein de l’entreprise Rothe, implantée à Kitzingen, Allemagne. Il en résulte une augmentation sensible de la productivité et une réduction considérable du besoin de retouches.
Implantée dans la ville franconienne de Kitzingen, l’entreprise Rothe concentre ses activités autour des rubans porteurs à destination de diverses branches industrielles. En considérant la production de l’entreprise, on peut constater dès le premier regard que l’on a affaire à des spécialistes.
Créée en 1963, Rothe compte parmi les pionniers dans le secteur des rubans porteurs, dont la fabrication mobilise aujourd’hui près de 140 employés répartis en trois équipes. Les machines de moulage construites par l’entreprise elle-même, dans lesquelles les moules sont introduits dans les rubans porteurs, ne sont guère impressionnantes au premier abord, mais reposent pourtant sur une longue expérience et un savoir-faire sophistiqué.
Les rubans porteurs sont des rubans en plastique dotés de cavités façonnées en forme de godet destinées à recevoir des composants qui viennent alimenter les machines de placement automatiques avec un positionnement précis. Les rubans peuvent présenter des largeurs de 8 mm à 104 mm. La forme et la profondeur des blisters sont adaptées individuellement à chaque élément de placement à transporter. Une précision au centième est exigée à cet égard, car les éléments de placement ne doivent ni tomber ni glisser, mais doivent être délivrés en un point précis et placés en position de transfert pour le placement.
Ces blisters sont conçus par un type d’emboutissage dans lequel le ruban de support en plastique est d’abord préchauffé avant d’arriver à l’outil de formage en lui-même où les blisters sont façonnés. Selon la demande du client, de petits perçages peuvent encore être réalisés dans les cavités pour permettre une ventilation et une aération de celles-ci. Ces perçages doivent être vraiment très petits ; c’est pourquoi Rothe utilise partiellement des machines laser spéciales à cet effet.
Dans de nombreux cas, une série de trous est également ajoutée pour permettre un positionnement plus sûr et le transport dans les machines de placement. Pour finir, les rubans porteurs sont découpés à la largeur souhaitée et enroulés autour d’un tambour d’enroulement.
Comme les machines employées aussi bien pour la fabrication que pour l’utilisation des rubans porteurs et des blisters eux-mêmes sont des machines à fonctionnement rapide avec des cycles courts et de longues durées de service, les moules doivent en conséquence être précis et durables. C’est notamment la raison pour laquelle les moules de Rothe sont fabriqués en interne.
Cela consolide non seulement notre savoir-faire, mais permet aussi des temps de réponse courts et flexibles lorsqu’un cas de réparation se présente. Ce facteur revêt une grande importance dans une entreprise qui travaille quotidiennement avec trois équipes. « Nous pouvons réparer les défauts sur un moule en un jour ouvré, » se réjouit Bernd Gruber, responsable de la fabrication d’outillages chez Rothe.
Le centre d’usinage Mikron HEM500U est équipé d’un palpeur de mesure de m&h avec technologie de transmission par infrarouge. Le palpeur de mesure m&h IRP25.41 est doté d’un boîtier en acier inoxydable et de diodes infrarouges à grande puissance d’émission protégées par du verre naturel. Celui-ci fonctionne avec une pile 9 volts disponible dans le commerce qui peut être changée en quelques gestes et sans outil spécial. Comme tous les appareils de m&h, ce palpeur de mesure est également étanchéifié selon la norme IP68 et est idéal pour Chez les conditions difficiles dans l’espace de travail des machinesoutils. La technologie de transmission HDR développée par m&h, qui permet d’envoyer des ensembles de données complets au lieu de signaux simples, garantit que seuls les signaux destinés au palpeur de mesure sont traités, ce qui renforce la sécurité des processus et exclut toute erreur de commutation ou tout arrêt imprévu de la machine en raison de possibles signaux parasites.
La sécurité des processus des appareils m&h est également démontrée par l’utilisation irréprochable du système de mesure d’outils laser LTS35.65-160 de m&h, également installé dans cette machine. Celui-ci permet de mesurer la longueur et le diamètre des outils sous contrainte dans la machine et lors de la rotation de la broche. Comme de nombreux petits outils de diamètres inférieurs ou égaux à 0,6 mm sont utilisés chez Rothe, la mesure sans contact y a rencontré un très grand succès. « Par comparaison au modèle concurrent sur la machine précédente, le système de réglage d’outils laser de m&h fonctionne nettement mieux à bien des égards, » estime Bernd Gruber selon sa propre expérience. « La buse de soufflage élimine facilement la saleté sur les tranchants. Les verres de l’optique laser ne doivent plus être nettoyés. Les coûts d’entretien sont sensiblement réduits. C’est simple comme bonjour. »
Nous avons désormais un taux de réussite nettement plus élevé lors du premier échantillonnage et bien moins de retouches à faire. Pourtant, le laser est monté directement sur la table orientable de la machine 5 axes et exposé à des projections de liquide de refroidissement et de copeaux à longueur de temps. Mais cela n’affecte en aucune manière les systèmes de mesure d’outils de m&h. Le système de fermeture de ces appareils protège efficacement l’optique interne, même lorsque la ventilation est interrompue ou la machine est à l’arrêt. Lorsque le processus de mesure est terminé, la petite chambre antérieure de l’optique laser est hermétiquement fermée et remplie d’air comprimé pour obtenir une surpression. Cela permet d’exclure toute infiltration de particules de saleté. Si de la saleté se dépose sur l’ouverture extérieure du canal lumineux, celle-ci sera alors rapidement éliminée lors de la prochaine ouverture de l’optique par la surpression libérée de la chambre optique. En outre, il est possible de procéder à la mesure avec de l’air de soufflage, ce qui empêche l’encrassement au cours du processus de mesure. La saleté susceptible d’adhérer au tranchant est éliminée de manière fiable par soufflage avec une buse à air comprimé spécialement conçue à cet effet. Celle-ci dirige et accélère le jet d’air de manière si puissante qu’il peut atteindre une vitesse supersonique en son centre. La buse développe ainsi une puissance nettoyante extrêmement élevée. Il n’est donc pas étonnant que l’appareil de préréglage d’outils de chez Rothe ne soit plus utilisé depuis un long moment.
Outre le matériel de m&h, Rothe utilise également depuis maintenant deux ans le logiciel 3D Form Inspect pour le contrôle direct et la comparaison de l’état prévu et de l’état réel de la pièce par rapport aux données de CAO de la pièce dessinée encore dans la machine. Pour ce faire, il n’est plus nécessaire de retirer les pièces de la machine pour pouvoir les contrôler sur une machine de mesure, puis les réintroduire dans la machine, toujours synonyme d’une perte de qualité et d’une perte de temps considérable. « Nous faisons beaucoup moins de coups d’essai et nous avons sensiblement moins de retouches à faire, » témoigne Bernd Gruber. « Désormais, tout est clairement documenté et si une erreur se produit, nous savons immédiatement quels paramètres en sont responsables et nous pouvons réagir instantanément et rectifier le tir. » Facile d’utilisation, le logiciel est couramment utilisé par tous les employés, leur facilitant le travail et leur permettant d’éviter les erreurs et les incertitudes de mesure. Le logiciel 3D Form Inspect de m&h reproduit un modèle de surface de la pièce sur lequel il est possible de sélectionner les points à mesurer par simple clic. Un autre clic permet d’attribuer aux points la fonction de mesure souhaitée. Dans de nombreux cas, le logiciel détermine automatiquement les points opposés, ce qui évite les incertitudes et les erreurs de mesure. Avant que le programme de mesure généré automatiquement ne soit transmis à la machine, un contrôle de collisions avec les contours de la pièce est encore effectué, offrant une sécurité de processus maximale. Il est désormais également possible de mesurer des éléments dont la mesure était auparavant impossible ou uniquement possible avec un investissement de temps considérable. Les plus petits
contours ou dépouilles peuvent ainsi être désormais mesurés, ce qui était auparavant impossible à réaliser manuellement. « Les employés travaillent volontiers avec ce logiciel, car il permet de documenter toutes les mesures et celles-ci sont moins contestables. Notre pourcentage de résultat a considérablement augmenté, » se réjouit Bernd Gruber. « Nous avons désormais un taux de réussite nettement plus élevé lors du premier échantillonnage et bien moins de retouches à faire. Les résultats de mesure sont une validation claire de notre travail et nous offrent une garantie rassurante de la qualité. »
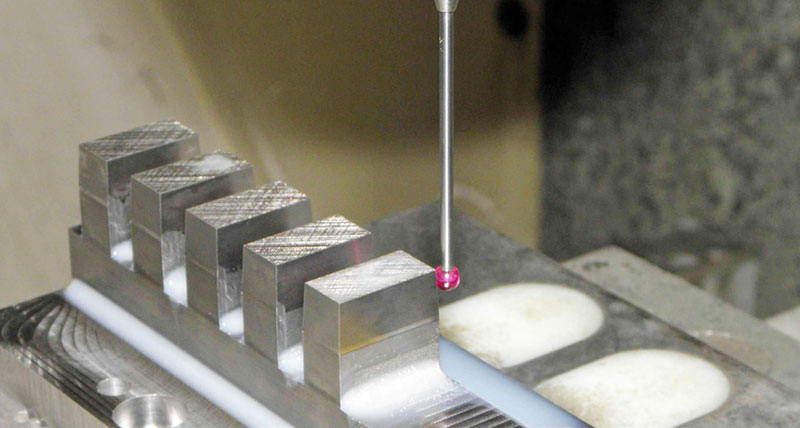
Entre-temps, Rothe ne contrôle pas uniquement chaque pièce qui est fabriquée sur le centre d’usinage, mais aussi les pièces critiques qui sont fabriquées dans les machines d’électroérosion. « Auparavant, en cas d’écart de précision, c’était souvent une parole contre une autre. Désormais, tout est clairement documenté, et ce sans grand effort. En pourcentage de la durée totale, le faible investissement en temps que demande la mesure est négligeable, » souligne Bernd Gruber. « Nous sommes ainsi certains que tout est conforme au dessin. »
Les courts temps de réponse du service des pièces de rechange de m&h sont également très appréciés. « Les stylets et les pièces de rechange sont disponibles à des prix raisonnables et sont livrés en un jour ouvré en cas de défaut, » précise Bernd Gruber sur le sujet.
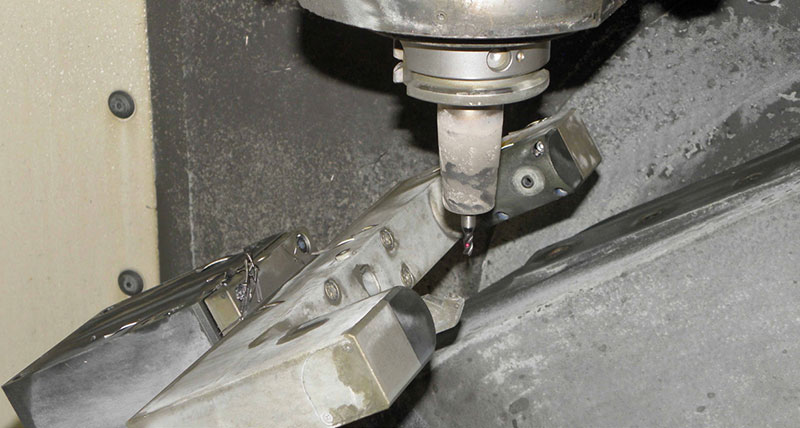
Créée en 1963, Rothe compte parmi les pionniers dans le secteur des rubans porteurs, dont la fabrication mobilise aujourd’hui près de 140 employés répartis en trois équipes. Les machines de moulage construites par l’entreprise elle-même, dans lesquelles les moules sont introduits dans les rubans porteurs, ne sont guère impressionnantes au premier abord, mais reposent pourtant sur une longue expérience et un savoir-faire sophistiqué.
Les rubans porteurs sont des rubans en plastique dotés de cavités façonnées en forme de godet destinées à recevoir des composants qui viennent alimenter les machines de placement automatiques avec un positionnement précis. Les rubans peuvent présenter des largeurs de 8 mm à 104 mm. La forme et la profondeur des blisters sont adaptées individuellement à chaque élément de placement à transporter. Une précision au centième est exigée à cet égard, car les éléments de placement ne doivent ni tomber ni glisser, mais doivent être délivrés en un point précis et placés en position de transfert pour le placement.
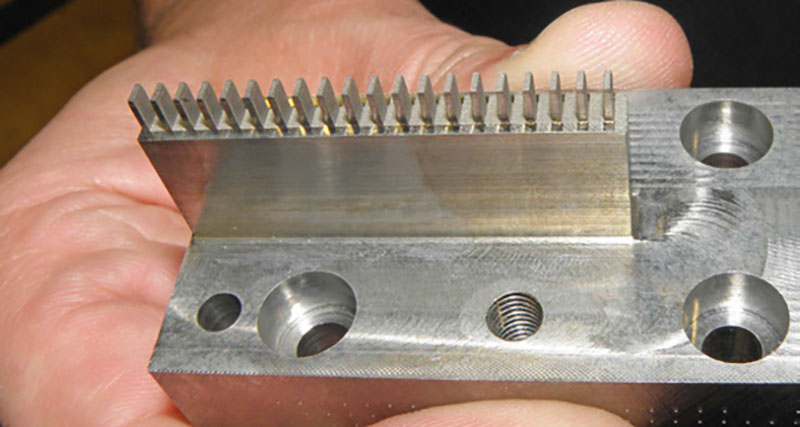
Comme les machines employées aussi bien pour la fabrication que pour l’utilisation des rubans porteurs et des blisters eux-mêmes sont des machines à fonctionnement rapide avec des cycles courts et de longues durées de service, les moules doivent en conséquence être précis et durables. C’est notamment la raison pour laquelle les moules de Rothe sont fabriqués en interne.
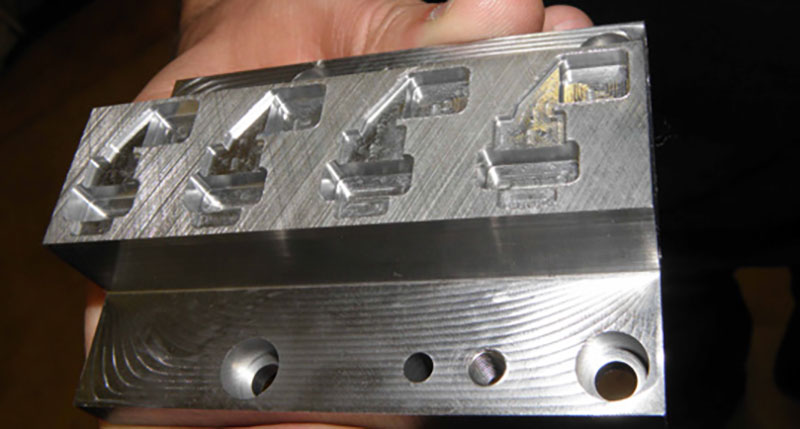
La sécurité des processus des appareils m&h est également démontrée par l’utilisation irréprochable du système de mesure d’outils laser LTS35.65-160 de m&h, également installé dans cette machine. Celui-ci permet de mesurer la longueur et le diamètre des outils sous contrainte dans la machine et lors de la rotation de la broche. Comme de nombreux petits outils de diamètres inférieurs ou égaux à 0,6 mm sont utilisés chez Rothe, la mesure sans contact y a rencontré un très grand succès. « Par comparaison au modèle concurrent sur la machine précédente, le système de réglage d’outils laser de m&h fonctionne nettement mieux à bien des égards, » estime Bernd Gruber selon sa propre expérience. « La buse de soufflage élimine facilement la saleté sur les tranchants. Les verres de l’optique laser ne doivent plus être nettoyés. Les coûts d’entretien sont sensiblement réduits. C’est simple comme bonjour. »
Nous avons désormais un taux de réussite nettement plus élevé lors du premier échantillonnage et bien moins de retouches à faire. Pourtant, le laser est monté directement sur la table orientable de la machine 5 axes et exposé à des projections de liquide de refroidissement et de copeaux à longueur de temps. Mais cela n’affecte en aucune manière les systèmes de mesure d’outils de m&h. Le système de fermeture de ces appareils protège efficacement l’optique interne, même lorsque la ventilation est interrompue ou la machine est à l’arrêt. Lorsque le processus de mesure est terminé, la petite chambre antérieure de l’optique laser est hermétiquement fermée et remplie d’air comprimé pour obtenir une surpression. Cela permet d’exclure toute infiltration de particules de saleté. Si de la saleté se dépose sur l’ouverture extérieure du canal lumineux, celle-ci sera alors rapidement éliminée lors de la prochaine ouverture de l’optique par la surpression libérée de la chambre optique. En outre, il est possible de procéder à la mesure avec de l’air de soufflage, ce qui empêche l’encrassement au cours du processus de mesure. La saleté susceptible d’adhérer au tranchant est éliminée de manière fiable par soufflage avec une buse à air comprimé spécialement conçue à cet effet. Celle-ci dirige et accélère le jet d’air de manière si puissante qu’il peut atteindre une vitesse supersonique en son centre. La buse développe ainsi une puissance nettoyante extrêmement élevée. Il n’est donc pas étonnant que l’appareil de préréglage d’outils de chez Rothe ne soit plus utilisé depuis un long moment.
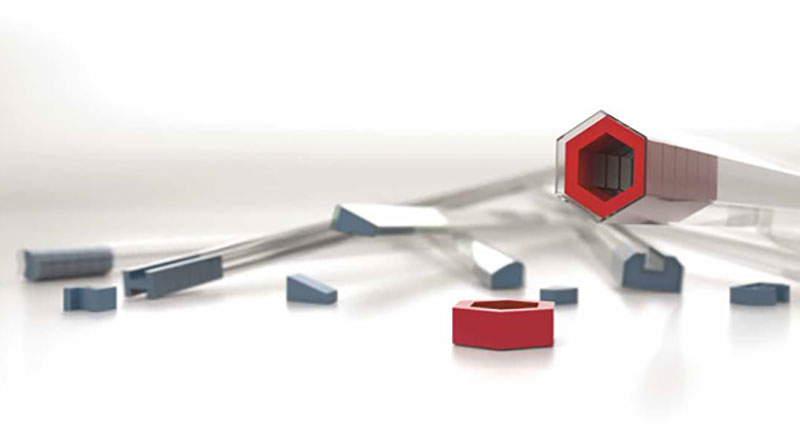
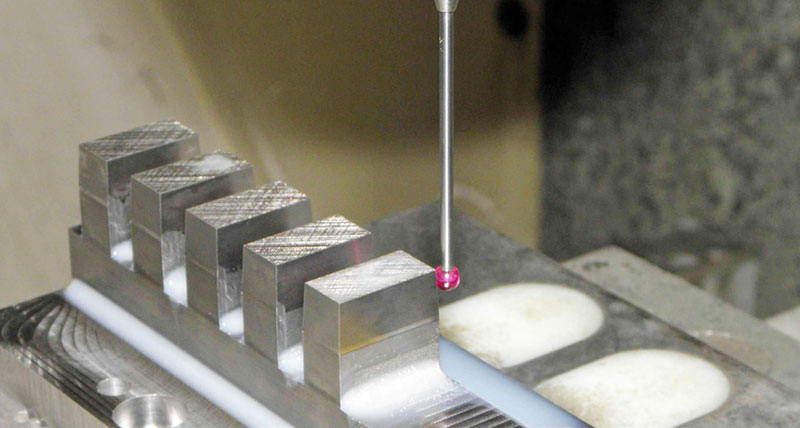
Entre-temps, Rothe ne contrôle pas uniquement chaque pièce qui est fabriquée sur le centre d’usinage, mais aussi les pièces critiques qui sont fabriquées dans les machines d’électroérosion. « Auparavant, en cas d’écart de précision, c’était souvent une parole contre une autre. Désormais, tout est clairement documenté, et ce sans grand effort. En pourcentage de la durée totale, le faible investissement en temps que demande la mesure est négligeable, » souligne Bernd Gruber. « Nous sommes ainsi certains que tout est conforme au dessin. »
Les courts temps de réponse du service des pièces de rechange de m&h sont également très appréciés. « Les stylets et les pièces de rechange sont disponibles à des prix raisonnables et sont livrés en un jour ouvré en cas de défaut, » précise Bernd Gruber sur le sujet.