Den Fortschritt im Visier: Laser Tracker Technologie neuerlich auf dem Prüfstand
Weiterentwickelte Funktionen und Software sorgen dafür, dass sich Multisensor-Messungen zunehmend durchsetzen.
Kontakt
Laser Tracker sind seit jeher das mobile Messsystem der Wahl für Unternehmen in der Automobilindustrie, der Luft- und Raumfahrt und anderen Branchen, die große Werkstücke herstellen. Anwendungen in diesen Bereichen sind Inspektionen vor Ort, messtechnikgestützte Ausrichtung und Montage, Prototypenbau, Werkzeugbau in der Luft- und Raumfahrt, Messungen von Rohkarosserien, Reverse Engineering und Teilezusammenbau bei übergroßen Komponenten und Baugruppen. Laser Tracker Systeme gelten als Inbegriff der Genauigkeit, Zuverlässigkeit und Langlebigkeit bei großvolumigen Messanwendungen. Doch ihr wichtigster Vorteil ist ihre Mobilität. Manche Werkstücke können schon aufgrund ihrer enormen Größe oder ihres Gewichts nicht mit herkömmlichen Koordinatenmessgeräten (KMG) gemessen werden.
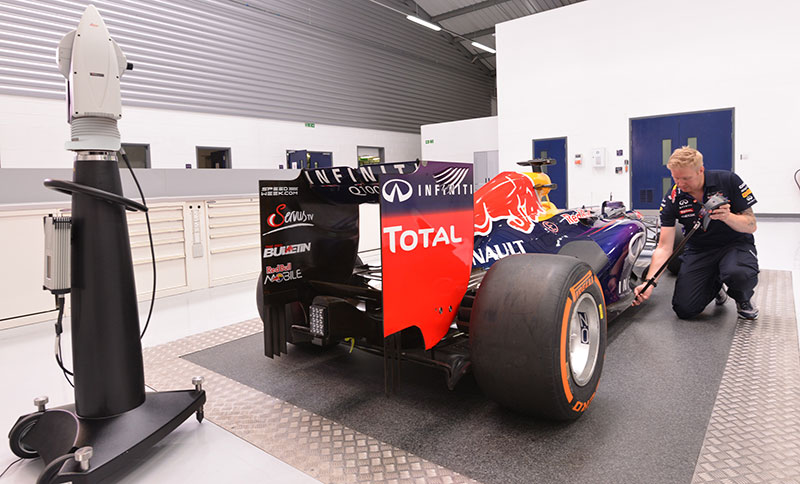
Früher stellten Laser Tracker für kleinere Unternehmen eine Investition dar, die meist nicht zu stemmen war. Ausrichtungs- und Zertifizierungsaufgaben wurden – oft mit wechselndem Erfolg – mithilfe mehr oder weniger selbst gebastelter Lösungen durchgeführt. Doch seit kundenseitig immer engere Toleranzen im Hundertstelmillimeterbereich gefordert werden, wächst das Interesse von Herstellern an Laser Trackern wieder. Ein weiterer Trend in der Branche, der Unternehmen zwingt, ihre Messverfahren zu überdenken, ist die Dokumentation von Qualitätssicherungsprozessen. Seit der Markteinführung der ersten Laser Tracker Anfang der 1990er sind die Preise infolge der Reifung des Markts stetig zurückgegangen, wodurch Laser Tracker zunehmend leistbarer werden. Technologische Fortschritte haben außerdem zu einer Erweiterung von Funktionalität und Anwendungsbereich geführt.
Ein Laser Tracker ist ein mobiles Koordinatenmessgerät zur präzisen Messung und Inspektion der Elemente eines Objekts im dreidimensionalen Raum mithilfe eines Laserstrahls. Der Laserstrahl wird zur Messung der Winkel der beiden mechanischen Achsen des Laser Trackers – der Azimutachse und der Elevations- oder Zenitachse – an einen Retroreflektor mit Kugelgehäuse (SMR) gesandt. Diese Messdaten werden dann zur Berechnung einer X-, Y- und Z-Koordinate mit einer Distanzmessung des Lasers kombiniert.
Die frühen Vorgänger unserer heutigen Laser Tracker nutzten Laserinterferometer zur Distanzmessung, was mühsam und zeitaufwendig war. Bei jeder Unterbrechung des Laserstrahls musste der Bediener mit dem Reflektor an die Ausgangsposition am Laser Tracker zurückkehren. Das kostete viel Zeit und damit Geld, insbesondere, wenn der Reflektor während des Messvorgangs über eine Entfernung von bis zu zehn Metern getrackt wurde. Es gab zwar Möglichkeiten, dieses Problem zu umgehen, doch bei der Arbeit in einer Umgebung mit vielen Hindernissen wie Personen oder Kabeln in der Sichtlinie wurde der Strahl trotzdem oft unterbrochen.
1995 wurde erstmals ein Absolutdistanzmesser (ADM) in einen Laser Tracker integriert, was die Art des Einsatzes dieser Technologie revolutionierte. Bei einer Strahlunterbrechung brauchte der Bediener nicht mehr länger in eine bekannte Position zurückzukehren, um das System zurückzusetzen. Er positionierte einfach den Strahl neu und fuhr mit der Inspektion fort. Anfangs waren ADM langsamer und deutlich weniger genau als Interferometer. Doch die Technologie entwickelte sich rasant weiter, und die heutigen ADM sind sogar noch genauer als die Interferometer, mit denen sie damals verglichen wurden. Manche Laser Tracker sind außerdem mit einer kombinierten ADM- und Interferometer-Technologie ausgerüstet, die als Absolutinterferometer, kurz AIFM, bezeichnet wird.
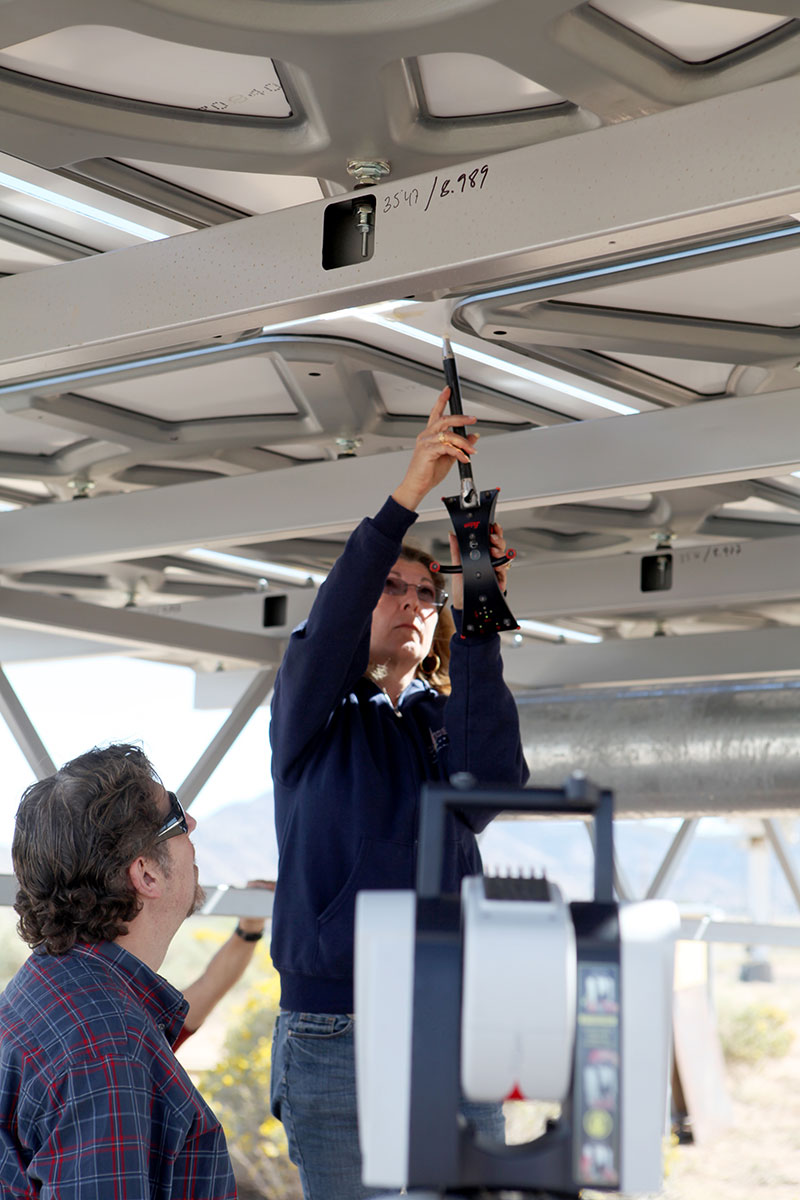
Bei bestimmten Laser Trackern, wie dem Leica Geosystems AT901 Absolute Tracker (Hexagon Manufacturing Intelligence, North Kingstown, Rhode Island) muss der Bediener nicht einmal mehr den Strahl suchen. Vielmehr findet der Strahl den Bediener. Eine in den Laser Tracker integrierte PowerLock Kamera erfasst den Reflektor innerhalb eines konischen Sichtfelds automatisch. Diese technische Verbesserung verkürzt die Inspektionszeit, da sich der Bediener nur noch an einem beliebigen Punkt irgendwo in der Nähe des Trackers aufhalten muss, damit der Laserstrahl eine Verbindung zum Reflektor herstellen kann.
Doch der Laser Tracker ist nicht auf Messungen innerhalb seiner Sichtlinie beschränkt. Allerdings bedarf es ohne freie Sichtlinie möglicherweise mehrerer Neupositionierungen des Trackers, um ein Werkzeug oder Werkstück vollständig zu prüfen. Zum einen kostet dies wertvolle Zeit, zum anderen reduziert sich mit jeder Umpositionierung die Messgenauigkeit. Dieses Problem wurde durch die Entwicklung handgeführter Messgeräte elegant gelöst.
Beim Einsatz handgeführter Messgeräte verfolgt der Laser Tracker ein bekanntes Muster von Infrarotdioden auf einem Messtaster oder einem Scanner. Beim Antasten eines Punkts berechnet der Tracker die X-, Y- und Z-Position des Messtasters und eine Kamera seine Rotationswerte RX, RY und RZ. Kombiniert ergeben sich dadurch Messungen in sechs Freiheitsgraden (6DoF). Diese handgeführten Messgeräte bieten einen erheblichen Mehrwert durch innovative Funktionen, die in Verbindung mit früheren Generationen von Laser Trackern undenkbar waren.
1. Stationsänderungen entfallen
Der Einsatz handgeführter Messgeräte erfordert keine direkte Sichtlinie zum Messpunkt. Der Laser Tracker kann daher in einer günstigen Position zur Messung des kompletten Werkstücks innerhalb eines kugelförmigen Messvolumens von bis zu 100 Metern aufgestellt werden. Wird der Tracker in seiner Ausgangsposition belassen, erhöhen sich dadurch Messgenauigkeit und Datenintegrität. Dies ist besonders günstig bei großen Objekten mit verborgenen oder schwer zugänglichen Elementen, die mit dem Messtaster oder Scanner aus unterschiedlichsten Positionen und sogar über Kopf problemlos erfasst werden können.2. Verwendung von Retroreflektoren wird optional
Retroreflektoren mit Kugelgehäuse (SMR), oft auch bezeichnet als Tripelspiegel- oder Corner-Cube-Reflektoren, werden aufgrund ihrer geringen Größe häufig verlegt oder fallen gelassen und gehen dadurch kaputt. Die Arbeit mit ihnen ist nicht einfach, besonders unter schwierigen Messbedingungen, wenn ein Bediener beispielsweise eine freie Hand benötigt, um sich irgendwo festzuhalten. Außerdem ist ihr Messbereich begrenzt. Bei der Verwendung eines Tripelspiegelreflektors muss der Strahl des Laser Trackers in einem Winkel von ±22° oder weniger auftreffen. Durch den Einsatz eines handgeführten Messtasters vergrößert sich dieser Einfallswinkel auf ±45°, was den Inspektionsvorgang vereinfacht und beschleunigt.Darüber hinaus können Zielmarken, die in Verbindung mit Retroreflektoren genutzt werden, eine potenzielle Fehlerquelle darstellen. Ein gängiger Fehler ist beispielsweise die Verwechslung von metrischen Angaben mit Maßen in Fuß und Zoll. So ist z. B. ein Reflektorhalter mit einer Größe von 25 Millimetern von einem mit 1 Zoll (25,4 Millimeter) optisch nicht zu unterscheiden.
3. Interaktion zwischen handgeführten Messgeräten und Laser Tracker
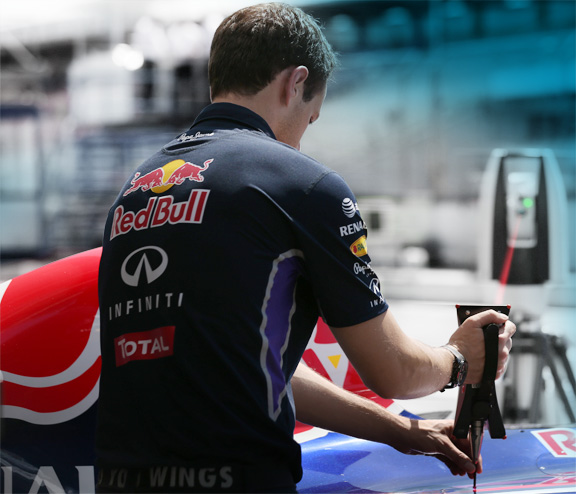
Handgeführte Taster besitzen Bedienelemente an beiden Seiten, die zur Erfassung von 3D-Koordinatendaten und zur Interaktion mit der Messsoftware dienen. Das spart Zeit, da der Bediener zur Eingabe von Daten nicht zum Computer zurückkehren muss. Gleichzeitig wird dadurch der Personalaufwand reduziert, da zur Durchführung von Messungen anders als früher heute nur noch eine Person benötigt wird.
Einige Laser Tracker Systeme erlauben auch die Eingabe von Daten über eine Fernbedienung. Allerdings ist dabei keine Rückmeldung in Echtzeit gewährleistet, die benötigt wird, um sicherzustellen, dass die Inspektion korrekt abgeschlossen wurde. Ein System mit Fernbedienung bringt darüber hinaus auch Nachteile bei der Erfassung schwer zugänglicher Messobjekte.
4. Verbesserungen bei Scanninganwendungen
Früher war die einzige Möglichkeit, ein Werkstück mit einem Laser Tracker zu scannen, einen Retroreflektor über seine Oberfläche zu bewegen. Für Anwendungen, bei denen Laserscanning sinnvoll ist, können mithilfe handgeführter Scanner Hundertausende Punkte pro Sekunde in Form riesiger Punktwolken, die auch bei großvolumigen Messungen hochgenau sind, erfasst werden. Unter Einsatz dieser Technologie kann ein sofortiger Abgleich mit dem CAD-Modell erfolgen, wodurch sich Inspektionszeiten von einigen Tagen auf wenige Stunden reduzieren lassen.5. Flexible Arbeit mit Aufspannvorrichtungen
Ist die absolute Position eines Objekts im Raum nicht bekannt, wird unter Umständen eine Aufspannvorrichtung benötigt, um ein Werkstück während der Inspektion zu fixieren. Konstruktionsänderungen können zeitaufwendige und teure Anpassungen dieser Aufspannvorrichtung erfordern. Die Möglichkeit, ein Objekt von allen Seiten zu messen, erlaubt die Erstellung mathematischer Modelle innerhalb der Software, bei denen es sich im Prinzip um virtuelle Aufspannvorrichtungen handelt. Der Bediener kann diese Modelle dann in einer virtuellen Umgebung anpassen, anstatt in der Realität neue Aufspannvorrichtungen bauen zu müssen. Entwickler profitieren von der Möglichkeit, unterschiedliche Produktvarianten in einem Montagevorgang bearbeiten zu können. Weitere Vorteile des Einsatzes von handgeführten Messgeräten sind die Messung großvolumiger Prototypen, Einsparungen bei Materialkosten und kürzere Produkteinführungszeiten.6. Automatisierung von Robotersystemen
Laser Tracker Systeme unterstützen Automatisierungsanwendungen mit Robotern und erlauben den Einsatz weniger präziser, kostengünstiger Roboter, auch für Anwendungen, die eine höhere Genauigkeit erfordern. Tripelspiegelreflektoren helfen bei der Kalibrierung eines Industrieroboters mittels Laser Tracker. Dabei werden Parameter wie Gliedlängen, Torsionswinkel, Nullpositionen, Versatzwerte der Glieder und Steifigkeit berücksichtigt.Eine andere Möglichkeit zur Automatisierung eines Roboters ist dessen Steuerung in sechs Freiheitsgraden. Diese Fähigkeit ermöglicht es Roboterherstellern, den Endeffektor des Roboters mit einem kürzeren Kalibrierzyklus zu kompensieren, der weniger Positionen erfordert. Gleichzeitig ist dadurch der Werkzeugarbeitspunkt (TCP) in Echtzeit bekannt.
Die dritte Möglichkeit zur Automatisierung des Einsatzes von Industrierobotern ist die Unterstützung der Inspektion übergroßer Werkstücke während der maschinellen Bearbeitung. Dazu kann man sich den Roboter einfach als hochgenau arbeitenden menschlichen Mitarbeiter vorstellen. Wenn der Roboter zur Inspektion ein handgeführtes Messgerät über das Werkstück bewegt, werden diese Messungen nicht von der Bearbeitungsmaschine, sondern vom Laser Tracker erfasst. So wird sichergestellt, dass die Genauigkeit der Messergebnisse auf der Präzision des Laser Trackers und nicht auf jener der weniger genauen Bearbeitungsmaschine basiert.
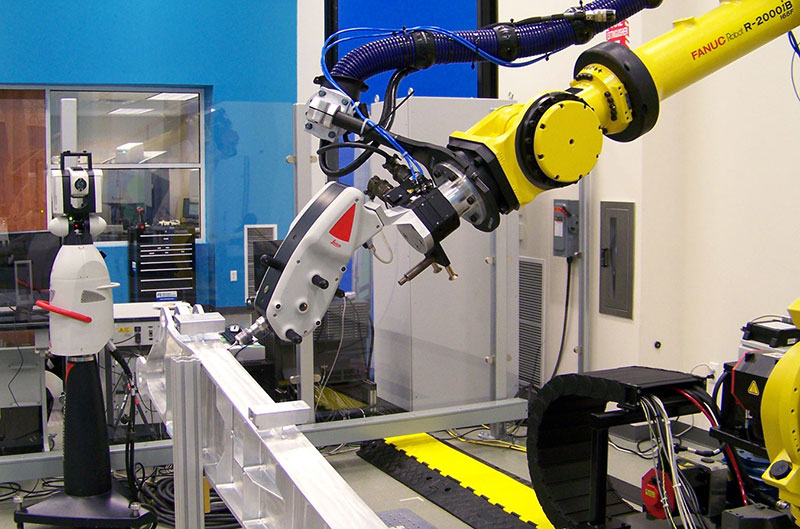
Parallel zur zunehmenden Leistbarkeit der Laser Tracker Technologie wurden die Systeme außerdem kleiner, leichter, schneller und benutzerfreundlicher. Durch handgeführte Scanner, Messtaster und Maschinensteuerungslösungen wurde die Flexibilität der Laser Tracker erhöht und ihr Anwendungsspektrum um ein Vielfaches erweitert. Optionen wie Akkubetrieb und der Schutz nach IP54 machen die Arbeit mit modernen Laser Trackern in Umgebungen möglich, von denen man noch vor wenigen Jahren nicht einmal zu träumen gewagt hätte. Hand in Hand mit der steigenden Nachfrage nach dieser Technologie geht ihre zunehmende Verfügbarkeit selbst für kleine Unternehmen. Nicht zuletzt deshalb lohnt sich ein gründlicher zweiter Blick auf die Vorteile des Einsatzes von Laser Trackern, selbst wenn in der Vergangenheit schon einmal eine Entscheidung gegen diese Investition getroffen wurde.