3D qualitätsprüfung von getriebege-häusen für nutzfahrzeuge
ZF Friedrichshafen - Deutschland.
Kontakt
Basierend auf dem im CAD System konstruierten Gehäuse werden Druckgusswerkzeuge gefertigt, in welchen die Gehäuseteile ausgeformt werden. Bei der Herstellung selbst beeinflussen verschiedene Parameter wie Füllmenge, Druck, Temperaturverhältnisse, Zeit und Werkzeugkonstruktion die Beschaffenheit der Formteile. Um eine stabile Qualität der Druckgussteile gewährleisten zu können, muss die Einhaltung der vorgegebenen Toleranzen kontinuierlich geprüft werden.
An dieser Stelle kommt das hochauflösende 3D Vermessungs- und Inspektionssystem SmartScan zum Zug. Die optische Messtechnik der Hexagon Scanner bietet die ideale Lösung für Qualitätssicherung im Bereich Erstbemusterung oder der Serienfertigung. Die Bandbreite beginnt bei Labormesstechnik und endet bei automatisierten Prozesslösungen, wobei selbst in Werkstattumgebung eine präzise Datenerfassung gewährleistet wird.
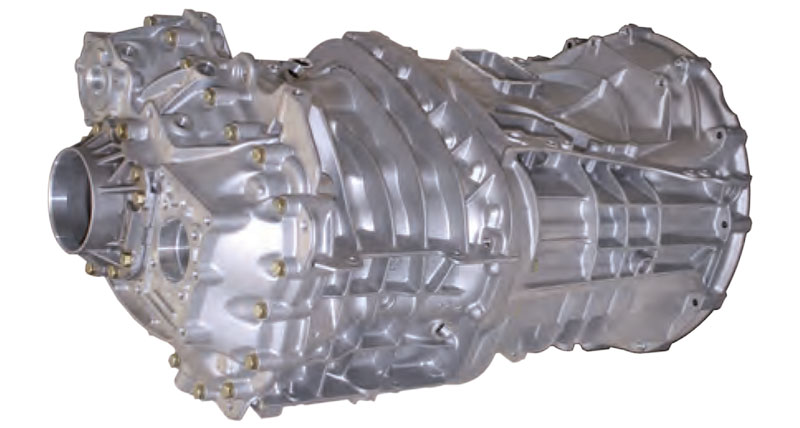
Vielfältige Aufgaben für 3D Scanner
Die Inspektionsaufgaben für den SmartScan bei der Firma ZF und ihr Getriebegehäuse aus Aluminium‑Druckguss sind vielfältig: Zuerst werden in der Prototypenphase präzise dreidimensionale Daten für die Erstbemusterung benötigt, um die geforderte Qualität zu überprüfen. Ziel der Konstruktion ist dabei die höchste Festigkeit des Gehäuses bei möglichst ausgewogenem Materialeinsatz.Während der Serienproduktion ist Präzision gefragt, wenn es um die Erhaltung des Qualitätsstandards geht: Hier wird die Inspektion des Gehäuses auf Formtreue sowie die Kontrolle der Oberfläche auf Beschädigungen und Deformationen durchgeführt. Ein besonderes Prüfmerkmal ist hierbei die Wandstärke, bei der es auf ein optimales Verhältnis von Stabilität und eingesetzter Materialmenge ankommt.
Zuletzt werden die in der Produktion eingesetzten Werkzeuge regelmäßig kontrolliert, um Abnutzungserscheinungen rechtzeitig zu erkennen und so mindere Produktqualität erst gar nicht entstehen zu lassen.
Alle Inspektionsprozesse werden entweder manuell auf einem Drehteller oder in Kombination mit einem Roboter automatisiert durchgeführt (Serienprüfung).
Detailgenaue Erfassung komplexer Bauteile
Für die Prüfung bei der Erstbemusterung kommt der SmartScan mit einer 250 Watt-Lampe sowie einem großen Messfeld zum Einsatz. Zur teilweise automatisierten Erfassung des Getriebegehäuses wird zusätzlich die für ein hohes Objektgewicht ausgelegte Rotationseinheit TurnTable-300 verwendet.Im Scanprozess werden zunächst die Einzelaufnahmen mit Hilfe der Software OptoCat erstellt, ausgerichtet und zu einem einheitlichen Dreiecksnetz verbunden. In einem zweiten Schritt werden die so erzeugten Daten mit einer Inspektionssoftware ausgewertet (im vorliegenden Fall PolyWorks® | Inspector™ von InnovMetric Software Inc.), um die Geometrien zu beurteilen.
Der Arbeitsablauf im Detail: Tiefe Rippenstrukturen sind oft mit den Standard-Triangulationswinkeln von flächenhaft messenden, optischen Sensoren nicht präzise zu erfassen. Die flexible Sensorkonfiguration der SmartScan Baureihe erlaubt Scanprozesse mit Triangulationswinkeln von 30°, 20° und 10°, wodurch auch mit herkömmlichen Sensoren schwierig zu erfassende Objektbereiche detailgenau gemessen werden.
1. Messaufbau und Digitalisierung
- Einrichten von Sensor, Drehteller und Messobjekt
- Kalibrierung der Sensorik und Verifizierung (VDI 2634/2) anhand eines Prüfkörpers (Hantelkörper)
- Vermessung des Getriebegehäuses (Scanvorgang) und Visualisierung
- Erstellen des 3D Datensatzes (Format: STL oder PLY)
2. Vergleich gegen CAD-Daten
- Erstellen der Prüfmerkmale gemäß Definition (Regel-geometrien, Schnitte, Skalierung)
- Soll-Ist-Vergleich (Falschfarbenvergleich gegen CAD)
- Erstellung und Auswertung des Prüfberichts
- Optimierung der Druckgusswerkzeuge und Anpassung der Produktionsparameter
Bei vorliegenden CAD-Werkzeugdaten werden diese direkt als Referenz geladen. Typischerweise werden die gemessenen Abweichungen zwischen dem Soll- und Ist‑Zustand durch Falschfarbenvergleich visualisiert. Damit sind die Messergebnisse schnell und direkt interpretierbar und werden umgehend zur Optimierung des Druckwerkzeugs bzw. der Prozessparameter herangezogen. Dies hilft der Produktionsabteilung, selbst unter schwierigen Bedingungen kontinuierliche Effizienz aufrecht zu erhalten und qualitativ hochwertige Getriebegehäuse im Endergebnis zu gewährleisten.
Im Vergleich zur herkömmlichen Koordinatemesstechnik ermöglicht der SmartScan vor allem bei Freiformflächen eine einfachere und schnellere Interpretation der Messergebnisse. Dem Benutzer steht eine umfassendere Datenbasis zur Weiterverarbeitung zur Verfügung, wodurch im Fall der Prototypen-Bearbeitung der „time to market“-Zyklus wesentlich verkürzt wird.
Wir danken der ZF Friedrichshafen AG für die freundliche Unterstützung bei der Erstellung dieser Fallstudie.