Kontrola jakości bloku skrzyni biegów pojazdów komercyjnych
ZF Friedrichshafen - Niemcy.
Kontakt
Bazując na kształcie zaprojektowanym w CAD, matryce mają za zadanie nadać kształt zgodnie z oczekiwaniami. W czasie produkcji weryfikowanych jest szereg parametrów takich jak kształt, dopasowanie, ciśnienie, warunki temperaturowe. Kształt narzędzie ma bezpośredni wpływ na jakość wyrobu końcowego. W celu zapewnienia stałej wysokiej jakości elementów, należy przeprowadzać stałą kontrolę geometrii względem zadanych tolerancji.
W takiej sytuacji naturalnym jest sięgnięcie po SmartScanskaner 3D. Optyczna technika pomiarowa stworzona przez Hexagon oferuje idealne rozwiązanie w zapewnieniu jakości w przypadku pełnej pierwszej kontroli w produkcji seryjnej. Zakres zastosowania tego systemu sięga od laboratorium po procesy automatyczne w warunkach produkcyjnych.
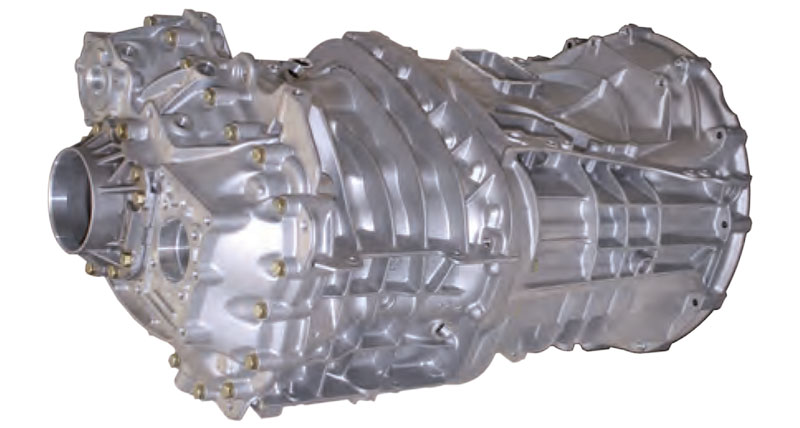
Różnorodne zadania dla skanerów 3D
Zadanie pomiarowym w ZF dla bloku skrzyni biegów jest następujące: najpierw, w celu upewnienia się co do jakości na etapie prototypu, przeprowadzenie precyzyjnej trójwymiarowej kontroli dla pierwszej próbki. Celem jest osiągnięcie konstrukcji o dużym stopniu sztywności przy optymalnie zbalansowanym materiale.Podczas produkcji seryjnej, precyzja jest elementem kluczowym przy rozważaniu w aspekcie jakości wyrobu. Kontrola taka polega na kontroli konturu i powierzchni pod względem potencjalnych uszkodzeń i odkształceń, Należy zweryfikować specjalne parametry kontrolne, grubość ścianek, co ma znaczący wpływ w ujęciu sztywności konstrukcji przy założonych wykorzystanych materiałach.
W efekcie końcowym, narzędzie wykorzystane do stałej kontroli w procesie produkcji, musi być poddawana stałej kontroli, pozwalając na szybką lokalizację otarć i zniekształceń na wczesnym etapie produkcji, zapobiegając pogorszeniu jakości produktu końcowego.
Cały proce kontrolny może być przeprowadzony manualnie lub z wykorzystaniem stolika obrotowego sterowanego numerycznie, lub robota przemysłowego.
Szczegółowy pomiar złożonych elementów
W celu przeprowadzenia pierwszej kontroli próbki wykorzystano system Hexagon o nazwie SmartScan wyposażony w duże pole pomiarowe. W celu częściowej automatyzacji procesu weryfikacji, system doposażono w automatyczny stolik obrotowy turnTABLE-300, specjalnie zaprojektowany do dużych obciążeń.
Podczas procesu skanowania, najpierw generowane są indywidualne skany, dopasowane i połączone w jedną siatkę trójkątów. Cały ten proces odbywa się automatycznie z wykorzystaniem oprogramowania o nazwie OPTOCAT. W drugim kroku, tak utworzone dane, są importowane przez zaawansowane oprogramowanie metrologiczne (w tym przypadku PolyWorks®/Inspector™ firmy Innovmetric), zapewniając kontrolę geometrii mierzonego obiektu.Podczas procesu skanowania, najpierw generowane są indywidualne skany, dopasowane i połączone w jedną siatkę trójkątów. Cały ten proces odbywa się automatycznie z wykorzystaniem oprogramowania o nazwie OPTOCAT. W drugim kroku, tak utworzone dane, są importowane przez zaawansowane oprogramowanie metrologiczne (w tym przypadku PolyWorks/Inspector firmy Innovmetric), zapewniając kontrolę geometrii mierzonego obiektu.
Wykorzystując standardowe kąty triangulacyjne systemu skanowania, głębokie struktury często nie mogą być zeskanowane z pożądaną dokładnością. Dzięki elastycznej konfiguracji systemu SmartScan skany można wykonywać dla zróżnicowanych kątów triangulacyjnych wynoszących 30°, 20° i 10°. Rozwiązanie takie pozwala na uzyskiwanie precyzyjnych danych dla cech osadzonych głęboko i trudnodostępnych do skanowania.
1. Ustawienia i digitalizacja
- Ustawienie skanera, stolika i obiektu na stoliku
- Kalibracja systemu i jego weryfikacja zgodnie z VDI 2634/2
- Pomiar odlewu bloku (proces skanowania oraz wizualizacja obiektu)
- Generowanie danych 3D (format: STL lub PLY)
2. Porównanie względem danych 3D
- Określenie parametrów kontroli (cechy, przekroje, skalowanie itp.)
- Porównanie Nominał/ Aktualny (kolorowa mapa odchyłek)
- Generowanie oraz analiza raportu pomiarowego
- Optymalizacja form oraz adaptacja parametrów procesu wytwarzania
Jeśli dysponujemy danymi CAD, są one bezpośrednio ładowane jako dane referencyjne. Typowo rozbieżności pomiędzy wyrobem a danymi nominalnymi są przedstawiane za pomocą kolorowej mapy odchyłek. W ten sposób można łatwo zinterpretować wyniki pomiaru. To pozwala wydziałowi kontroli jakości na optymalizację parametrów procesu matrycy, a tym samym wpływać na efektywność przy założonych parametrach jakościowych.
W porównaniu do standardowych metod pomiarowych z wykorzystaniem maszyn współrzędnościowych, skaner o nazwie SmartScan-HE pozwala na łatwiejsze interpretowanie wyników pomiarowych w szczególności w aspekcie kształtów swobodnych. Ponadto użytkownik otrzymuje znacznie większy zakres danych pozwalając na wykorzystanie ich do dalszych analiz chociażby dla działu projektów.
Chcielibyśmy podziękować dla załogi ZF Friedrichshafen AG za współpracę przy realizacji projektu.