Smart Assembly Shop di Hexagon: collegare il mondo fisico e quello virtuale della produzione
Di Jeff Robertson e Dr. Ingo Hahn, divisione Manufacturing Intelligence di Hexagon
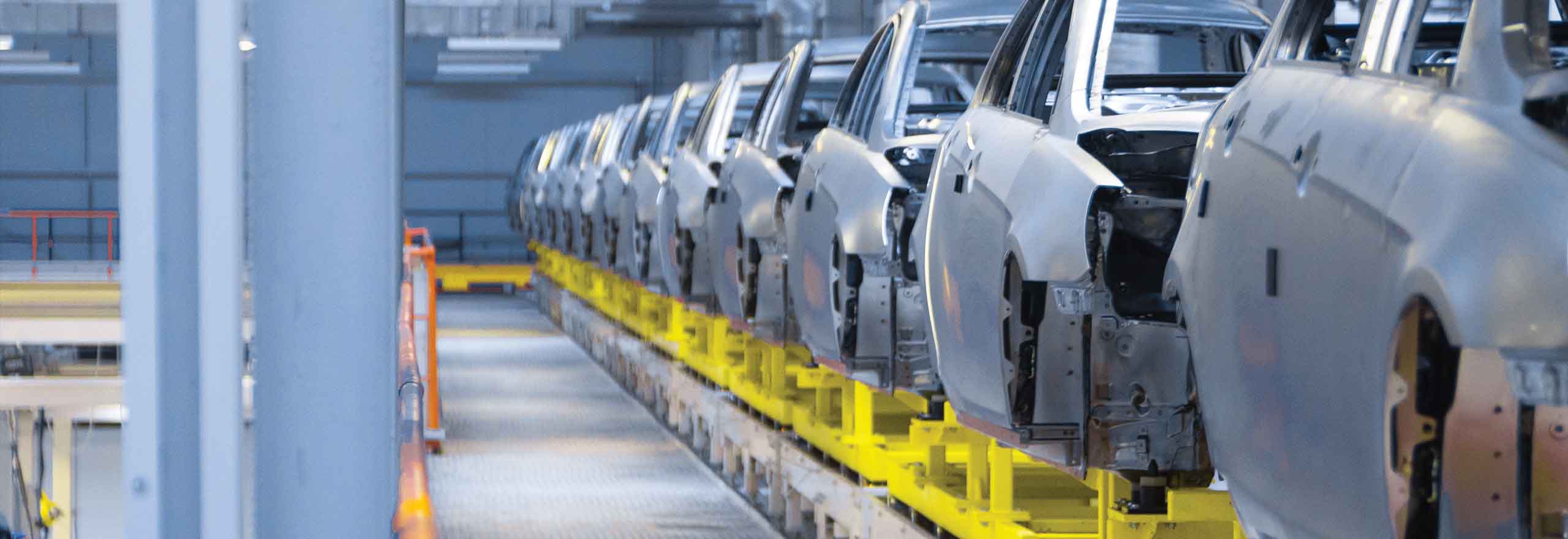
Engineering Reality 2024 volume 1
Accelerare la produzione intelligente
OEM e fornitori del settore automobilistico sono costantemente sollecitati a ridurre i costi e i tempi di sviluppo e lancio dei prodotti. Nell'ambito della trasformazione dell'Industria 4.0 emergono tecnologie che possono consentire cambiamenti radicali nell'approccio di base utilizzato per la prototipazione e il lancio dei veicoli. Il concetto di gemello digitale del processo di produzione è ciò che Hexagon chiama Smart Assembly Shop (SAS).
Grazie all'integrazione di diverse soluzioni, tra cui la scansione e la misura, il morphing CAD, la compensazione della gravità, la simulazione multifisica del processo e la gestione dei dati sulla qualità, Hexagon ha creato una piattaforma che consente ai team di tecnici di valutare in dettaglio gli effetti aggregati del processo di produzione e di adottare misure per mitigare le problematiche prima che sia realizzato il primo utensile e anche dopo che siano riscontrate delle non conformità.
Introduzione
Ogni carrozzeria e struttura del telaio è prodotta seguendo rigide specifiche dimensionali. Gli elementi chiave devono essere posizionati correttamente per allinearsi con gli altri componenti dell'assemblaggio o per superare la verifica visiva del consumatore, comunemente chiamata "giochi e profili". Nel corso degli ultimi 100 e più anni la metodologia tradizionale consisteva nello stampare o produrre singolarmente ogni componente (dettaglio) in modo che si avvicinasse il più possibile ai valori nominali relativi. Vari stampi, fusioni ed estrusioni erano poi assemblati in sottogruppi utilizzando la saldatura a punti o altre tecniche di giunzione, sempre nel tentativo di rispettare i valori nominali.
Questo processo si ripeteva, fase dopo fase, unendo i sottoinsiemi, finché non si otteneva un assemblaggio completo o, nel caso più articolato, un assemblaggio completo della scocca. Tuttavia il problema di questo approccio consiste nel fatto che ogni componente stampato si può discostare lievemente dai valori nominali e ogni fase del processo di assemblaggio può contribuire ulteriormente ad alimentare tale differenza dimensionale.
Inoltre, il raggiungimento della conformità dei singoli dettagli dei componenti non garantisce che l'assemblaggio soddisfi le specifiche. Fase dopo fase la differenza dimensionale rispetto ai valori nominali aumenta e le cause principali della variazione diventano sempre più difficili da identificare. Occorre inoltre considerare l'effetto dei diversi processi in ogni fase di produzione. Sebbene questo effetto fosse noto e studiato da tempo, mancava una soluzione che affrontasse adeguatamente la natura complessa del problema. I tecnici si affidavano invece all'intuizione, alle conoscenze pregresse e ai tentativi e agli errori per ottenere i risultati desiderati.
Figura 1. Sezione del lato carrozzeria saldato.
Per ridurre in modo significativo i costi e i tempi nel processo di sviluppo e lancio del prodotto, dobbiamo ridurre al minimo il numero di prototipi fisici e iterazioni necessarie per ottenere la conformità dimensionale dell'assemblaggio finale, nonché la quantità e la complessità dei fissaggi. Qui sono descritte due discipline di base della soluzione SAS: Dispositivo di controllo virtuale (VCF) e Assemblaggio virtuale (VA).
Smart Assembly Shop - Assemblaggio virtuale
Il processo di assemblaggio virtuale è un flusso di lavoro analogo che sfrutta molti degli stessi sistemi e principi del dispositivo di controllo virtuale (VCF). Il flusso di lavoro dell'assemblaggio virtuale SAS si concentra sui passaggi per fissare, bloccare e unire fisicamente più componenti singoli e sottogruppi in assemblaggi sempre più grandi man mano che il processo di assemblaggio procede lungo la produzione. L'obiettivo è prevedere il comportamento del processo di assemblaggio attraverso simulazioni multifisiche di serraggio, saldatura e giunzione, tenendo conto delle realtà dei componenti di dimensioni non nominali che entrano nel flusso di lavoro.
Il risultato del processo di assemblaggio virtuale è una valutazione efficiente del processo di produzione che consente ai tecnici di valutare rapidamente il comportamento di assemblaggio risultante già nelle prime fasi del ciclo di sviluppo del prodotto. La digitalizzazione del flusso di lavoro dell'assemblaggio virtuale consente di ottenere diversi vantaggi:
- Sveltimento dello sviluppo e del lancio di nuovi prodotti
- Riduzione e potenzialmente eliminazione dei costi e degli sforzi necessari per la prototipazione fisica
- Miglioramento del grado di fiducia nel processo di progettazione e produzione all'inizio del ciclo di sviluppo del prodotto
- Capacità di identificare le modifiche necessarie alla progettazione e al processo già nelle prime fasi del ciclo di sviluppo del prodotto
Figura 2: Flusso di lavoro del dispositivo di controllo virtuale
Un esempio di flusso di lavoro di assemblaggio virtuale è illustrato nella Figura 3. In questo caso inizia con diverse geometrie non nominali che entrano nel flusso di lavoro, inclusi componenti/attrezzaggi, schema di misura e dati di processo che fluiscono dai sistemi CAD/PLM/software aziendali nella piattaforma. Questi dati generano una versione digitale del processo di assemblaggio fisico. Il processo virtuale deve rispecchiare il più possibile il processo fisico.
La rappresentazione geometrica dei componenti si può basare sulla geometria nominale ricavata direttamente dal CAD. Può anche sfruttare i dati di scansione di misura (STL) per eseguire il morphing della geometria come descritto in precedenza per ottenere rappresentazioni delle geometrie non nominali nei modelli di assemblaggio virtuale. Il modulo di simulazione del processo di assemblaggio virtuale esegue quindi una simulazione di processo separata per ogni fase del processo di produzione, che può includere la formatura del metallo, la rifilatura, l'applicazione dell'adesivo, il serraggio, l'assemblaggio meccanico, la saldatura, la piegatura, ecc.
Figura 3: Flusso di lavoro di assemblaggio virtuale
I risultati di ogni fase confluiscono nelle fasi successive per poi essere integrati in assemblaggi sempre più grandi. Dopo ogni fase di assemblaggio, i risultati della simulazione sono valutati applicando uno schema di misura come il Sistema di Punti di Riferimento (RPS), proprio come avverrà durante la produzione. Sulla base di questi risultati il team di progettazione può adottare iniziative per migliorare/ottimizzare il processo in vari modi, tra cui, a titolo esemplificativo ma non esaustivo, la modifica dell'approccio di serraggio e fissaggio, la modifica del processo di saldatura/assemblaggio, la modifica della sequenza di saldatura, la modifica delle configurazioni precedenti della stazione o la modifica delle geometrie dei singoli componenti.
Design flessibile
I flussi di lavoro del dispositivo di controllo virtuale e dell'assemblaggio virtuale sono progettati per essere flessibili. La soluzione è stata sviluppata tenendo conto di diversi utilizzi. Spetta all'utente e al suo team decidere come utilizzare il software selezionando flussi di lavoro standardizzati che semplificano la selezione e il setup. La Figura 4 illustra le diverse selezioni che un utente può effettuare per definire il Process Setup desiderato.
Figura 4: Ingressi SAS
Esistono molti potenziali utilizzi che gli utenti SAS possono realizzare con la soluzione. Di seguito sono riportati alcuni esempi di utilizzi/studi identificati dai nostri clienti:
- Valutare l'interazione tra progettazione e processo di produzione: in che modo la combinazione di morsetti, dispositivi di fissaggio, posizioni di saldatura, sequenza di saldatura, ecc. influisce sulla macrodeformazione dell'assemblaggio?
- Comprendere l'impatto delle geometrie non nominali nel processo: come si comporta il processo quando le geometrie dei pezzi o dei sottogruppi si discostano da quelle nominali?
- Eseguire il fissaggio di controllo virtuale di parti e sottogruppi: come si inseriscono le parti e i sottogruppi non nominali nel dispositivo di controllo singolarmente e con altre parti?
- Eseguire la valutazione della solidità/stabilità del fissaggio: quanto è ripetibile il processo di fissaggio dei pezzi nell'attrezzatura? Il componente si assesterà sempre nella stessa posizione?
- Eseguire la misura virtuale per comprendere l'impatto sulla tolleranza dimensionale: qual è l'impatto degli studi sopra descritti riguardanti il piano di controllo di misura o dimensionale?
Soluzione di simulazione migliorata per la misura
La combinazione di hardware di misura, software, simulazione di processo e gestione dei dati di qualità in una soluzione coerente e appositamente progettata offre ai tecnici un flusso di lavoro semplificato che rende questa analisi avanzata efficiente ed efficace in un ambiente di produzione. Una soluzione integrata collega tra loro diverse tecnologie individuali per supportare il processo Smart Assembly Shop. Controlla i dati attraverso le varie fasi del processo, consentendo una gestione efficiente di grandi quantità di dati di scansione, dati di misura, informazioni di assemblaggio e risultati di simulazione. La piattaforma può farlo per molti componenti attraverso le varie fasi del flusso di lavoro. Di conseguenza i tecnici possono analizzare rapidamente i dati e interpretare i risultati invece di perdere tempo a cercare di capire come funziona il software.
Utilizzando una soluzione integrata i tecnici possono dedurre facilmente le cause dei comportamenti indesiderati e identificare l'approccio ottimale per mitigarli. Le interfacce software basate su script possono guidare la progettazione e l'ottimizzazione automatizzata di esperimenti su larga scala (DoE), consentendo così ai tecnici di valutare molte potenziali combinazioni di serraggio, fissaggio, sequenza di saldatura e molti altri parametri geometrici e di processo senza interazione umana. Infine, la soluzione integrata consente a vari operatori con ruoli diversi all'interno dell'organizzazione di interagire con i dati sulla qualità virtuale e fisica e di trarre conclusioni sui fattori che determinano la qualità dimensionale.
Conclusione
Lo Smart Assembly Shop di Hexagon combina diverse tecnologie avanzate in modo da migliorare drasticamente il modo in cui l'industria esegue lo sviluppo e il lancio dei prodotti. Questa soluzione aiuterà a ridurre i cicli di sviluppo del processo di progettazione e produzione valutando virtualmente le fasi di lavorazione dei prototipi. In questo modo, si ridurranno anche significativamente i costi e le tempistiche necessari per portare un progetto dalla fase iniziale al processo di produzione approvato.