Hexagon Smart Assembly Shop: Verschmelzung von realer und virtueller Fertigung
Jeff Robertson und Dr. Ingo Hahn, Hexagon, Manufacturing Intelligence Division
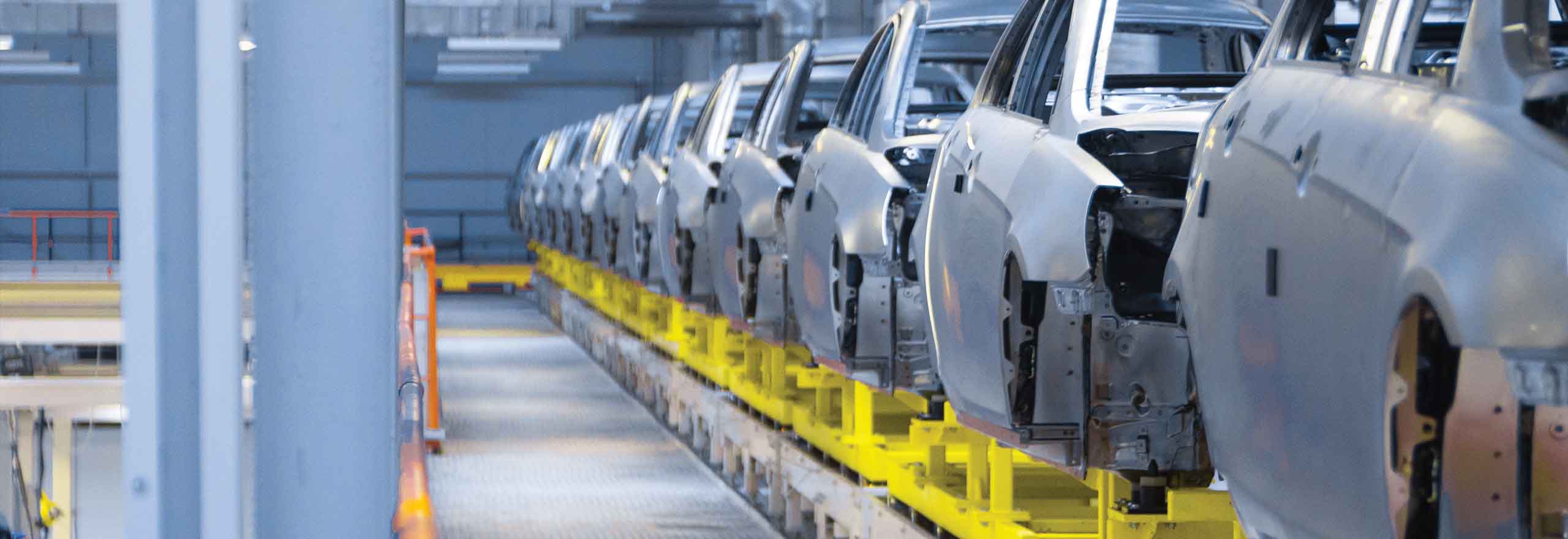
Engineering Reality 2024 Ausgabe 1
Accelerate Smart Manufacturing
Automobilhersteller und Zulieferer stehen unter permanentem Druck, sowohl Kosten als auch Zeitaufwand für Produktentwicklung und -einführung so gering wie möglich zu halten. Die Transformation hin zu Industrie 4.0 birgt neue Technologien, die zu tiefgreifenden Veränderungen bei der Entwicklung von Prototypen und für Fahrzeuge auf dem Weg zur Marktreife führen werden. Das Konzept des Digitalen Zwillings eines Fertigungsprozesses bezeichnet Hexagon als Smart Assembly Shop (SAS).
Dabei werden verschiedene Lösungen von Hexagon, wie Scanning und Messtechnik, CAD-basiertes Morphing, Schwerkraftkompensation, multiphysikalische Prozesssimulation und Qualitätsdatenmanagement in einer Plattform zusammengeführt, um aggregierte Auswirkungen des Fertigungsprozesses detailliert bewerten und mögliche Problemlösungen bereits im Vorfeld der Produktion einleiten zu können.
Einführung
Jede Karosserie und Fahrgestellstruktur wird nach strengen Spezifikationen gefertigt. Wichtige Merkmale von Bauteilen müssen korrekt positioniert sein, damit diese mit anderen Komponenten in der Baugruppe korrelieren sowie der Analyse von Spalt und Versatz standhalten. Das herkömmliche Vorgehen besteht darin, jedes einzelne Bauteil so nah wie möglich am Sollwert zu stanzen oder anderweitig herzustellen. Verschiedene Stanzteile, Gussteile und Extrusionen werden durch Punktschweißen oder andere Fügeverfahren zu Unterbaugruppen verbunden – immer mit der Vorgabe, den Sollwert einzuhalten.
Über verschiedene Stationen werden die Unterbaugruppen so lange miteinander verbunden, bis schließlich eine fertige Baugruppe entsteht – oder beiswielsweise eine komplette Rohkarosserie. Der Nachteil dabei ist, dass jedes gestanzte Bauteil minimal vom Sollwert abweicht und jeder Schritt im Montageprozess zu weiteren Maßabweichungen führt.
Auch garantiert die erreichte Konformität einzelner Detailkomponenten nicht, dass auch die Baugruppe die Spezifikationen erfüllt. Station für Station wächst die Maßabweichung gegenüber dem Nennwert, wobei die Ursachen der Abweichung immer schwieriger zu identifizieren sind. Außerdem kann es in jeder Phase des Fertigungsprozesses zu Prozesssschwankungen kommen. Diese Problematiken sind hinreichend bekannt und visualisiert. Eine adäquate Lösung gab es bislang nicht. Stattdessen stützte man sich auf Intuition, Erfahrungswerte und ‚Versuch und Irrtum‘, um die gewünschten Ergebnisse zu erzielen.
Abbildung 1. Breakout-Baugruppe einer geschweißten Karosserieseite.
Um Kosten und zeitlichen Aufwand bei der Produktentwicklung und -einführung deutlich zu senken, muß die für die dimensionelle Maßhaltigkeit bei der Endmontage erforderliche Anzahl physischer Prototypen und Iterationen als auch die Menge und Komplexität der Aufspannsysteme so gering wie möglich gehalten werden. Nachfolgend werden zwei Grundprinzipien der SAS-Lösung näher erläutert: Virtuelle Prüfung der Vorrichtung (Virtual Check Fixture) und Virtuelle Montage (Virtual Assembly).
Smart Assembly Shop – Virtuelle Montage
Der Workflow bei der virtuellen Montage ist dem Prozessablauf für die virtuelle Prüfung der Vorrichtung sehr ähnlich. Dieser fokussiert im Verlauf des Montageprozesses besonders das Spannen und die Fügeverfahren, bei denen mehrere Einzelkomponenten und Unterbaugruppen sukzessive zu größeren Baugruppen zusammengefügt werden. Mittels multiphysikalische Spann-, Schweiß- und Fügeprozesssimulationen werden Voraussagen erstellt und dabei die Realität maßabweichender Komponenten, die in den Workflow gelangen, berücksichtigt.
Anhand der Ergebnisse der virtuellen Montage erfolgt die effiziente Bewertung des Fertigungsprozesses. Das Montageverhalten einer Baugruppe lässt sich somit viel früher im Produktentwicklungszyklus bewerten. Die Workflow-Digitalisierung der virtuellen Montage hat mehrere Vorteile:
- Entwicklung und Einführung neuer Produkte in deutlich kürzerer Zeit
- Minimierung von Kosten und Aufwand für physische Prototypen, evtl. sogar kompletter Verzicht
- Höheres Vertrauensniveau in den Design- und Fertigungsprozess bereits früher im Produktentwicklungszyklus
- Identifikation erforderlicher Design- und Prozessänderungen bereits früher im Produktentwicklungszyklus
Abbildung 2. Workflow – Virtuelle Prüfung der Vorrichtung.
Abbildung 3. Beispiel Workflow – Virtuelle Montage. In diesem Fall beginnt es damit, dass mehrfache Geometrien mit Abweichungen von der Sollgestalt in den Workflow einfließen, einschließlich Komponenten/Aufspannsysteme, Messschemata und Prozessdaten, die über CAD/PLM/Unternehmenssoftwaresysteme in die Plattform eingebunden werden. Diese Daten erzeugen eine digitale Version des physischen Montageprozesses. Der virtuelle Prozess muss den realen Prozess so genau wie möglich spiegeln.
Die geometrische Darstellung der Komponenten kann auf der Sollgeometrie direkt aus dem CAD basieren. Auch Messscandaten können zum geometrischen Morphen genutzt werden, um in den virtuellen Montagemodellen die Darstellung von Geometrien, die vom Sollwert abweichen, zu erhalten. Das Simulationsmodul für den Prozess der virtuellen Montage führt dann eine diskrete Prozesssimulation für jede Stufe des Fertigungsprozesses durch, wie Metallumformung, Trimmen, Klebstoffauftrag, Spannen, mechanisches Fügen, Schweißen, Falzen usw.
Abbildung 3: Workflow –Virtuelle Montage
Ergebnisse aus jeder Phase werden sukzessive in nachfolgenden Phasen zu immer größeren Baugruppen zusammengeführt. Nach jeder Montagestufe werden die Simulationsergebnisse anhand eines Messschemas wie dem Referenzpunktsystem (RPS) ausgewertet, wie es auch während der Produktion angewendet wird. Auf dieser Grundlage können weitere Schritte zur Verbesserung/Optimierung des Prozesses in die Wege geleitet werden, einschließlich, aber nicht beschränkt auf die Modifizierung des Spannens bzw. der Spannvorrichtung, die Modifizierung des Schweiß-/Montageprozesses, der Schweißsequenz, aber auch die Anpassung früherer Stationskonfigurationen oder einzelner Bauteilgeometrien.
Flexibel im Design
Der Workflow der virtuellen Prüfung der Vorrichung sowie der virtuellen Montage ist flexibel gestaltbar. Die Lösung wurde unter Berücksichtigung verschiedener Anwendungsbereiche entwickelt. Hierbei kann der Anwender entscheiden, in welcher Form er die Software nutzen möchte. Beispielsweise anhand vordefinierter Workflows, welche Auswahlkriterien und Set-Up vereinfachen. Abbildung 4 veranschaulicht die verschiedenen Auswahlkriterien, um das gewünschte Set-Up zu definieren.
Abbildung 4. SAS-Input.
Es gibt viele potenzielle Anwendungsbereiche für diese SAS-Lösung. Im Folgenden einige Beispiele:
- Bewerten der Wechselwirkung zwischen Design und Fertigungsprozess: Wie wirkt sich die Kombination aus Spannen, Spannvorrichtung, Schweißstellen, Schweißfolge usw. auf die Makrodeformation der Baugruppe aus?
- Analyse des Einflusses von Geometrien, die vom Sollwert abweichen: Wie anders verhält sich der Prozess, wenn die Bauteil- oder Unterbaugruppengeometrie vom Sollwert abweicht?
- Durchführen der virtuellen Prüfung der Vorrichtung von Bauteilen und Unterbaugruppen: Wie passen vom Soll abweichende Bauteile und Unterbaugruppen einzeln und zusammen mit anderen Teilen in die Prüfvorrichtung?
- Durchführen von Robustheits-/Stabilitätsbewertung der Vorrichtung: Wie wiederholbar ist der Prozess zum Einspannen von Teilen in die Vorrichtung? Setzt das Bauteil jedes Mal an der gleichen Stelle auf?
- Anwenden virtueller Messtechnik, um die Auswirkungen auf die Maßtoleranz zu verstehen: Welche Auswirkungen haben die oben beschriebenen Untersuchungen auf den Mess- oder Maßkontrollplan?
Messtechnisch erweiterte Simulationslösung
Die Kombination von messtechnischer Hardware und Software, Prozesssimulation und Qualitätsdatenmanagement in einer gemeinsamen, speziell entwickelten Lösung bietet einen optimierten Workflow, um mit modernen Analysetools die Fertigung effizient und effektiv zu unterstützen. Eine integrierte Lösung gewährleistet die Kombination mehrerer Einzeltechnologien während des Smart Assembly Shop Prozesses. Daten lassen sich über die verschiedenen Prozessschritte hinweg effizient verwalten. Das gilt auch für eine große Menge an Scan- und Messdaten, Montageinformationen und Simulationsergebnissen. Über die Plattform kann dies für viele Bauteile und über verschiedene Workflow-Schritte vorgenommen werden. Daraus resultiert eine schnell Datenanalyse und Ergebnisinterpretation.
Skriptgesteuerte Software-Interfaces steuern die statistische Versuchsplanung (Design of Experiments/DoE) sowie deren Optimierung, um viele potenzielle Kombinationen des Spannens und der Spannvorrichtung, der Schweißsequenzen und vieler anderer Geometrie- und Prozesseingaben ohne menschliche Interaktion bewerten können. Dank dieser integrierten Lösung können Stakeholder auf unterschiedlichen Ebenen mit virtuellen und physischen Qualitätsdaten interagieren und Schlussfolgerungen zur Maßhaltigkeit ziehen.
Fazit
Hexagons Smart Assembly Shop kombiniert verschiedene moderne Technologien, welche die bei Produktentwicklung und -einführungen anfallenden Fertigungsprozesse deutlich verbessern. Diese Lösung trägt dazu bei, Entwicklungsschleifen im Design- und Fertigungsprozess zu minimieren, da bereits der Prototypenprozess virtuell bewertet wird. So lassen sich sowohl Kosten als auch Zeitaufwand von der ersten Designidee bis zur Produktionsfreigabe erheblich reduzieren.