Senza Burr, la prima volta
Contattateci

Lo stabilimento Vorwerk veri ca gli inserti e le parti mobili degli stampi quando ancora sono staffati in macchina, utilizzando i tastatori m&h e il software 3D Form Inspect. Uno stampo costruito in questo modo, con due serie di dieci slitte, si è rivelato senza bave per la prima volta ed è stato omologato per la produzione in grande serie già dopo il primo pezzo campione.
E’ improbabile trovare qualcuno che non conosca gli aspirapolvere verdi & bianchi prodotti da Vorwerk. Queste macchine, che cercano di distinguersi dalla concorrenza per la loro qualità elevata e la lunga durata, sono fabbricati a Wuppertal.Tecniche produttive all’avanguardia unite ad una continua ottimizzazi- one costituiscono una solida base che consente alle aziende e ai pro- dotti di conservare il loro posto nel mercato. “Con macchine moderne e cicli produttivi ottimizzati siamo riusciti a ridurre i costi di attrezza- mento no al 40%,” riferisce Marc Alexander Popov, responsabile della costruzione stampi presso la Vorwerk in Wuppertal.
“Non voglio né lo stampo più costoso né il più economico,” così egli spiega la sua strategia e conferma: “Voglio lo stampo più ef ciente.” Tuttavia, questo richiede un esame molto complesso dell’intera vita di uno stampo, prendendo in considerazione molti fattori che comp- rendono i costi di assistenza e di manutenzione. Questo è il motivo per cui il Signor Popov ha analizzato una vasta gamma di misure af nché gli stampi per iniezione plastica siano sempre conformi agli standard più elevati. “Sia i nostri prodotti sia gli stampi a iniezione sono continu- amente ottimizzati no alla ne del loro ciclo di vita.” Ciò comprende la scelta di materiali di ultima generazione come, ad esempio, i cosiddetti acciai ESU e il Toolux 44, acciaio esente da deformazione a durezza 45 HRC, che sono sempre più usati per stampi e inserti. Per la fabbricazi- one degli stampi, Vorwerk ha quasi completamente sostituito il canale di colata con ugelli dotati di valvole a spillo. Per ottenere brevi tempi ciclo ed elevata precisione di forma , gli stampi sono dotati di sistema di raffreddamento ‘ lm cooling’ Ciò consente alta produttività delle macchine, processi produttivi esenti da inconvenienti e grande precisi- one di forma sulle parti stampate a iniezione.
L’of cina di fresatura del reparto costruzione stampi utilizza macchine della Hermle, DMG, SIP e Exeron.
Queste macchine sono equipaggiate con tastatori m&h. Inoltre, il software 3D Form Inspect è installato su un computer in of cina. Questo software consente la veri ca dei pro li e delle super ci fresati in qualsiasi momento, mentre il componente è ancora staffato in macchina. I punti che devono essere misurati sono individuati sulla rappresentazione gra ca sullo schermo del computer con un clic del mouse e a ciascuno viene assegnata la funzione di misura necessaria. Il software genera automaticamente il program- ma appropriato per la macchina interes- sata, compresa una breve calibrazione che precede il processo di misura. E’ inoltre integrato un controllo di collisione automatico tra il tastatore m&h ed il pezzo.
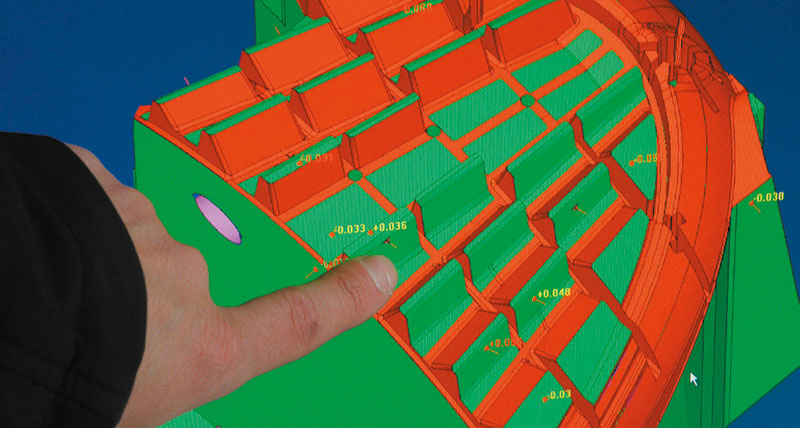
Dopo essere stato trasferito, il programma è richiamato dalla relativa macchina utensile ed è eseguito come qualsiasi altro programma di lavorazione. I dati generati sono rinviati al computer ed i punti misurati sono mostrati come valori sulla rappresentazione gra ca o sotto forma di protocollo come su una macchina di misura. Dopo una breve presen- tazione di mezza giornata, tutto lo staff ha iniziato ad utilizzare il programma grazie alla facile gestione del software. Considerando l’età media dei componenti dello staff, che è 52 anni, questa è un’afferma- zione molto positiva.
““Lo abbiamo visto per la prima volta ad una era e dopo alcune veri che siamo ora certi che m&h fornisce il miglior sistema per le macchine utensili,” il Signor Popov spiega le sue scoperte. “E’ un vero aiuto per il personale. All’operatore in macchina deve essere data la possibilità di veri care autonomamente che cosa ha prodotto e di in- tervenire se necessario.” L’unico modo ef ciente di fare ciò è misurare in macchina.
La prova stampi si è ridotta del 70-80%!
Alla Vorwerk gli stampi sono molto complessi e generalmente necessitano di varie prove volte all’ottimizzazione e alla messa a punto prima di essere distribuiti per la produzione in grande serie. Nel caso di una girante, è stato costruito uno stampo con 10 slitte con i contorni esterni delle pale. Questo è stato il primo stampo in cui, durante la produzione, tutti gli inserti e gli stampi sono stati ripe- tutamente misurati mentre ancora staffati sulla macchine utensile utilizzando tastatori e software m&h. Il risultato non è stato solo un accoppiamento decisamente migliore nell’assemblaggio dello stampo con provastampi ridotta in modo signi cativo ma, con grande sorpresa di tutti, anche uno stampo senza bave al primo tentativo. “Con risultati come questo, non c’è bisogno di considerare i pochi minuti persi per misurare in macchina,” è lieto di riferire il Signor Popov.
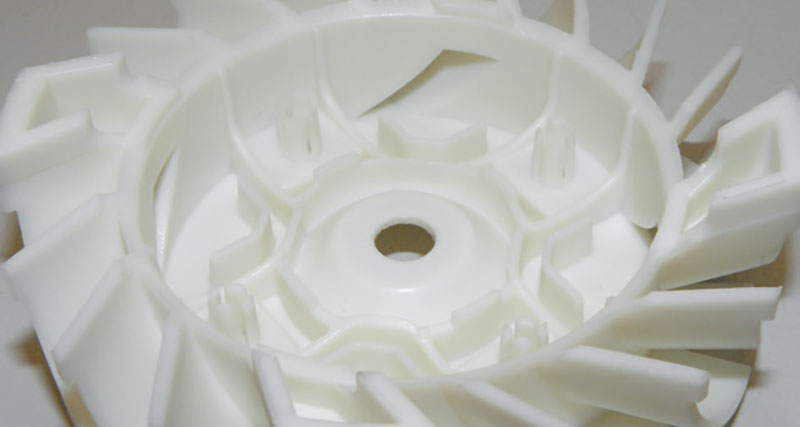
L’implementazione della misura in macchina ha dato un contributo essenziale al successo sia all’interno sia all’esterno.
“Ora sappiamo sempre che cosa stiamo facendo e conosciamo i nostri stampi molto meglio,” afferma il Signor Popov. “Abbiamo imparato come allungare la vita degli utensili. Ora lavoriamo le dimensioni nite e le nostre super ci prova stampi appaiono completamente differenti,” egli riferisce. La prova stampi si è ridotta del 70 – 80%. Le cose sono notevolmente migliorate dal momento che la qualità è già controllata in macchina. “O”ggi, rispettiamo i termini o niamo prima,” è lieto di riferire il Signor Popov.
E’ improbabile trovare qualcuno che non conosca gli aspirapolvere verdi & bianchi prodotti da Vorwerk. Queste macchine, che cercano di distinguersi dalla concorrenza per la loro qualità elevata e la lunga durata, sono fabbricati a Wuppertal.Tecniche produttive all’avanguardia unite ad una continua ottimizzazi- one costituiscono una solida base che consente alle aziende e ai pro- dotti di conservare il loro posto nel mercato. “Con macchine moderne e cicli produttivi ottimizzati siamo riusciti a ridurre i costi di attrezza- mento no al 40%,” riferisce Marc Alexander Popov, responsabile della costruzione stampi presso la Vorwerk in Wuppertal.
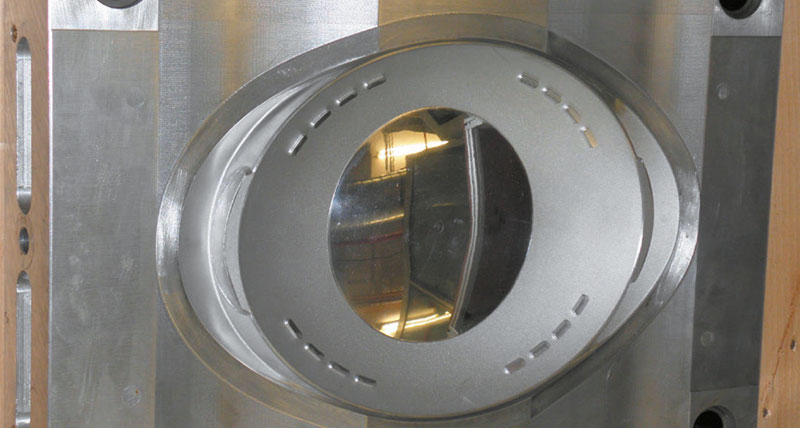
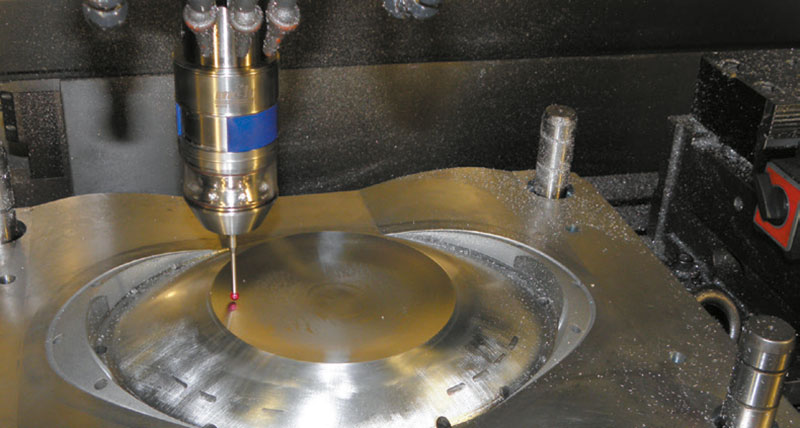
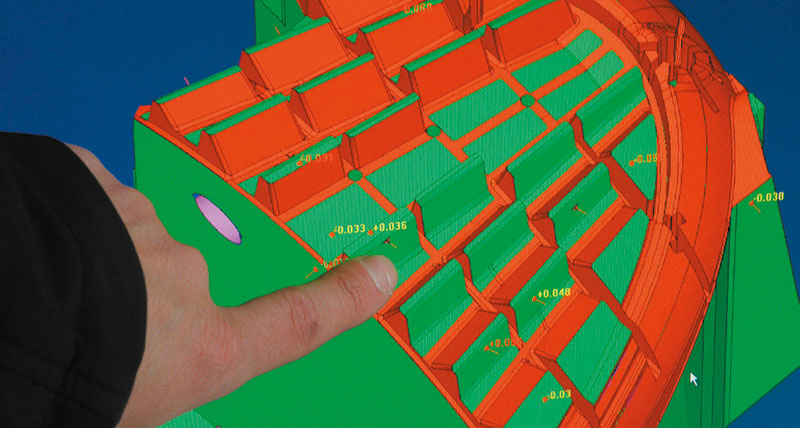
Dopo essere stato trasferito, il programma è richiamato dalla relativa macchina utensile ed è eseguito come qualsiasi altro programma di lavorazione. I dati generati sono rinviati al computer ed i punti misurati sono mostrati come valori sulla rappresentazione gra ca o sotto forma di protocollo come su una macchina di misura. Dopo una breve presen- tazione di mezza giornata, tutto lo staff ha iniziato ad utilizzare il programma grazie alla facile gestione del software. Considerando l’età media dei componenti dello staff, che è 52 anni, questa è un’afferma- zione molto positiva.
““Lo abbiamo visto per la prima volta ad una era e dopo alcune veri che siamo ora certi che m&h fornisce il miglior sistema per le macchine utensili,” il Signor Popov spiega le sue scoperte. “E’ un vero aiuto per il personale. All’operatore in macchina deve essere data la possibilità di veri care autonomamente che cosa ha prodotto e di in- tervenire se necessario.” L’unico modo ef ciente di fare ciò è misurare in macchina.
La prova stampi si è ridotta del 70-80%!
Alla Vorwerk gli stampi sono molto complessi e generalmente necessitano di varie prove volte all’ottimizzazione e alla messa a punto prima di essere distribuiti per la produzione in grande serie. Nel caso di una girante, è stato costruito uno stampo con 10 slitte con i contorni esterni delle pale. Questo è stato il primo stampo in cui, durante la produzione, tutti gli inserti e gli stampi sono stati ripe- tutamente misurati mentre ancora staffati sulla macchine utensile utilizzando tastatori e software m&h. Il risultato non è stato solo un accoppiamento decisamente migliore nell’assemblaggio dello stampo con provastampi ridotta in modo signi cativo ma, con grande sorpresa di tutti, anche uno stampo senza bave al primo tentativo. “Con risultati come questo, non c’è bisogno di considerare i pochi minuti persi per misurare in macchina,” è lieto di riferire il Signor Popov.
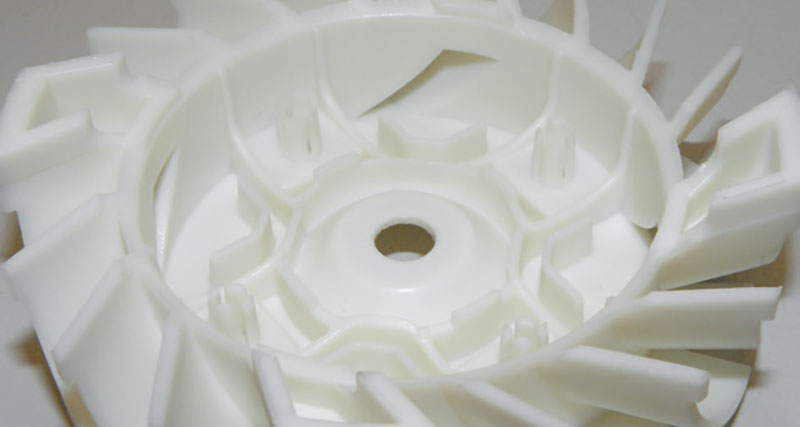
L’implementazione della misura in macchina ha dato un contributo essenziale al successo sia all’interno sia all’esterno.
“Ora sappiamo sempre che cosa stiamo facendo e conosciamo i nostri stampi molto meglio,” afferma il Signor Popov. “Abbiamo imparato come allungare la vita degli utensili. Ora lavoriamo le dimensioni nite e le nostre super ci prova stampi appaiono completamente differenti,” egli riferisce. La prova stampi si è ridotta del 70 – 80%. Le cose sono notevolmente migliorate dal momento che la qualità è già controllata in macchina. “O”ggi, rispettiamo i termini o niamo prima,” è lieto di riferire il Signor Popov.