Gratfrei, beim ersten Mal
Kontakt

Mit Messtastern und 3D Form Inspect Software von m&h prüft der Formenbau bei Vorwerk Formeinsätze und Schieber noch in der Aufspannung auf den Werkzeugmaschinen. Eine so gefertigte Form mit zwei mal zehn Schiebern war beim ersten Schuss gratfrei und erhielt beim ersten Abmustern bereits die Serienfreigabe.
Wer kennt Sie nicht, die grün-weißen Staubsauger von Vorwerk. Gefertigt werden die Geräte, die sich durch hohe Qualität und lange Lebensdauer von den Wettbewerbern zu unterscheiden suchen, in Wuppertal. Moderne Fertigungsmethoden und ständige Optimierung bilden die Grundlage, dass sich Firma und Produkte im Markt behaupten. „Mit modernen Maschinen und optimierten Abläufen haben wir die Werkzeugkosten um bis zu 40 % gesenkt,“ weiß Marc Alexander Popov, Leiter Werkzeugbau bei Vorwerk in Wuppertal, zu berichten.
„Ich will weder das billigste Werkzeug, noch das Teuerste“, erläutert er seine Strategie und bekräftigt: „Ich will das wirtschaftlichste Werkzeug.“ Dazu bedarf es allerdings einer sehr vielschichtigen Betrach tung über die gesamte Lebensdauer einer Form unter Einbeziehung vieler Faktoren inklusive der Wartungs- und Instandhaltungskosten. Deshalb hat Herr Popov mittlerweile ein ganzes Bündel von Maßnahmen ergriffen, um die Spritzwerkzeuge permanent auf höchstem Niveau zu halten. „Unsere Produkte und die Spritzgießformen werden bis zum Ende ihres Lebenszyklus permanent optimiert.“ Dazu gehören die Auswahl modernster Werkstoffe wie sogenannter ESUStähle und Toolux 44, ein verzugsfreier Stahl mit 45 HRC, die zunehmend für Formen und Einsätze verwendet werden. Bei der Konstruktion der Formen hat Vorwerk mittlerweile fast vollständig von Angüssen auf Nadelverschlussdüsen umgestellt. Um kurze Zykluszeiten und hohe Formtreue zu erreichen, werden die Formen mit Innenkühlungen versehen. Das ermöglicht eine hohe Ausbringung der Maschinen, ungestörte Produktionsprozesse und eine hohe Formtreue der Spritzlinge.
In der Fräserei des Formenbaus wird auf Maschinen von Hermle, DMG, SIP und Exeron gearbeitet. Diese Maschinen sind mit Messtastern von m&h ausgestattet.
Hinzu kommt die 3D Form Inspect Software von m&h auf einem Rechner in der Werkstatt. Diese Software ermöglicht die jederzeitige Kontrolle der gefrästen Konturen und Flächen noch während der Aufspannung in den Maschinen. Dazu werden auf einer Bildschirmdarstellung des Werkstückes per Mausklick die zu messenden Punkte festgelegt und eine dazu gehörige Messaufgabe ausgewählt. Im Hintergrund schreibt die Software automatisch das Verfahrprogramm für die Maschine, inklusive einer vorgeschalteten Kurzkalibrierung. Auch eine automatische Kollisionskontrolle des m&h Tasters mit den Werkstückkonturen ist integriert.
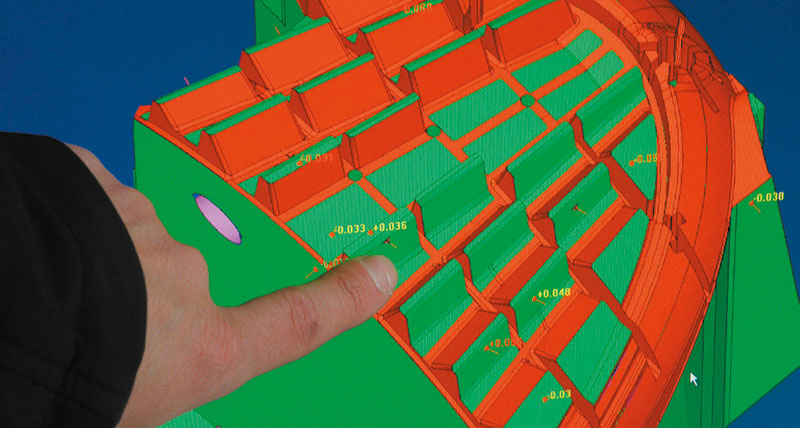
Nach der Übertragung des Programms wird dieses an der jeweiligen Werkzeugmaschine aufgerufen und wie ein normales Arbeitsprogramm abgearbeitet. Der dabei generierte Datensatz wird auf gleichem Wege an den Computer zurück übertragen und die Messwerte erscheinen als Messwert auf der Flächendarstellung oder als Protokoll wie auf einer Messmaschine. Dank der leichten Bedienbarkeit der m&h Software 3D Form Inspect war trotz kürzester Einweisung von nur einem halben Tag sofortige Akzeptanz bei allen Mitarbeitern gegeben. Berücksichtigt man den Altersdurchschnitt der betroffenen Mitarbeiter von 52 Jahren, so ist das eine sehr positive Feststellung.
„Wir haben das erstmals auf einer Ausstellung gesehen und nach einiger Prüfung sind wir sicher, dass m&h das beste System für die Werkzeugmaschine liefert“, schildert Herr Popov seinen Eindruck. „Es muss eine echte Erleichterung für die Mitarbeiter sein“, betont Herr Popov „Der Mann an der Maschine muss die Möglichkeit haben, das was die Maschine und das Werkzeug im Zusammenspiel als Ergebnis abliefern selbst zu bewerten und einzugreifen.“ Dies geht wirtschaftlich nur durch das Messen in der Maschine.
Das Tuschieren wurde um 70 – 80 % reduziert.
“Naturgemäß sind die Formen bei Vorwerk sehr komplex und bedürfen in der Regel mehrerer Optimierungs- und Anpassungsschleifen, bis sie für die Serienproduktion freigegeben werden. Im Fall eines Flügelrades wurde eine Form mit 10 Schiebern gebaut, in denen die Außenkonturen mit den Flügeln abgebildet werden. Bei dieser Form hat man erstmalig konsequent die Einsätze und Formkörper noch in den Werkzeugmaschinen mit den Messtastern und der Software von m&h gemessen. Das Ergebnis war nicht nur ein spürbar besseres Zusammenpassen beim Formaufbau und ein deutlich reduzierter Tuschieraufwand, sondern, zur Überraschung aller, ein gratfreies erstes Werkstück, schon bei der ersten Abmusterung. „Da braucht man über die wenigen Minuten Messzeit auf der Maschine nicht mehr nachdenken“, freut sich Herr Popov.
„Im Formenbau haben wir erst durch das Messen der Konturen auf den Maschinen die Möglichkeit erhalten, frühzeitig zu reagieren. Das ist nicht nur bei Neuwerkzeugen wichtig, sondern auch bei Ersatzteilen und Reparaturen.“ Viele Kunststoffe, die Vorwerk verarbeitet, sind sehr abrasiv, weil sie hohe Faseranteile aufweisen, um langlebig zu sein. Umso wichtiger sind gleichbleibende Passgenauigkeit und Konturtreue der Formeinsätze, da sie im Leben einer Form immer wieder erneuert werden.
„Wir haben die Wartungskosten der Werkzeuge drastisch gesenkt“, resümiert Herr Popov. „Den Ausschuss in der Produktion haben wir teilweise von 7 – 8 % auf unter 1 % gesenkt“, berichtet er nicht ohne Stolz. Die Einführung des Messens in der Maschine hat viel zum internen wie zum externen Erfolg beigetragen.
„Nun wissen wir immer, was wir tun und lernen unsere Werkzeuge viel besser kennen“, sagt Herr Popov. „Wir haben gelernt, die Lebensdauer der Einsätze zu verlängern. Übergänge an den Produktwänden können deutlich verbessert werden. Wir fräsen jetzt auf Null und unsere Tuschierflächen sehen völlig anders aus“, berichtet er. Das Tuschieren wurde um 70 – 80 % reduziert. Es ist viel mehr Ruhe eingekehrt, weil die Qualität schon auf der Maschine geprüft wird. „Wir halten heute unsere Termine alle ein oder sind sogar früher dran“, freut sich Herr Popov.
Wer kennt Sie nicht, die grün-weißen Staubsauger von Vorwerk. Gefertigt werden die Geräte, die sich durch hohe Qualität und lange Lebensdauer von den Wettbewerbern zu unterscheiden suchen, in Wuppertal. Moderne Fertigungsmethoden und ständige Optimierung bilden die Grundlage, dass sich Firma und Produkte im Markt behaupten. „Mit modernen Maschinen und optimierten Abläufen haben wir die Werkzeugkosten um bis zu 40 % gesenkt,“ weiß Marc Alexander Popov, Leiter Werkzeugbau bei Vorwerk in Wuppertal, zu berichten.
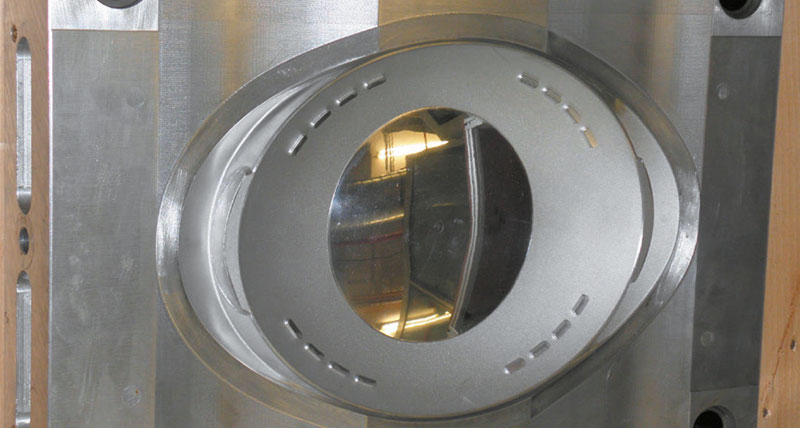
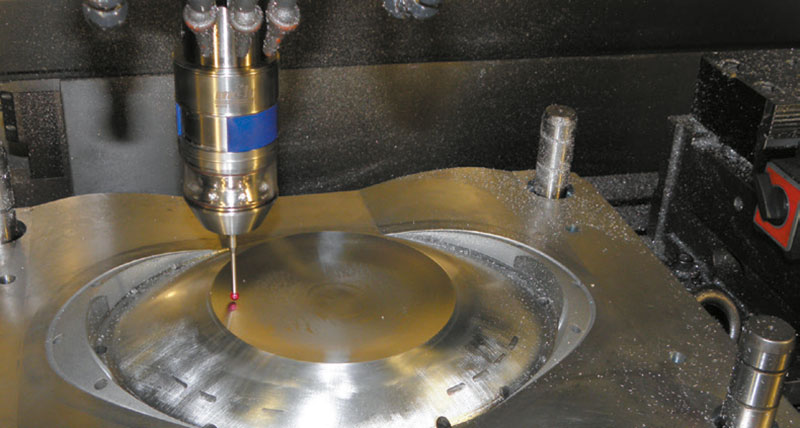
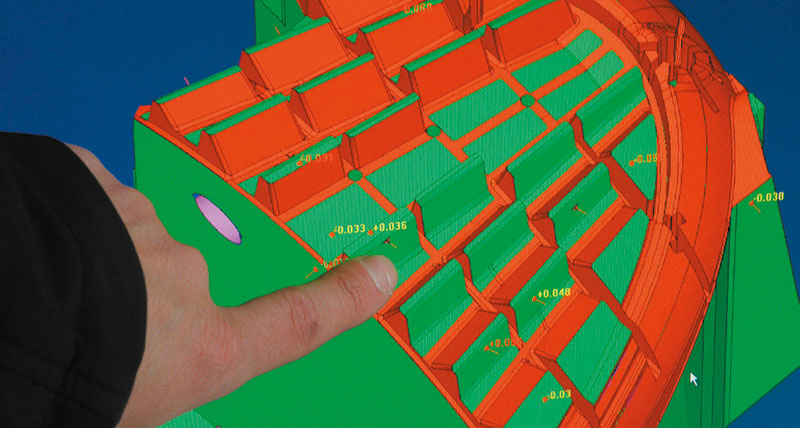
Nach der Übertragung des Programms wird dieses an der jeweiligen Werkzeugmaschine aufgerufen und wie ein normales Arbeitsprogramm abgearbeitet. Der dabei generierte Datensatz wird auf gleichem Wege an den Computer zurück übertragen und die Messwerte erscheinen als Messwert auf der Flächendarstellung oder als Protokoll wie auf einer Messmaschine. Dank der leichten Bedienbarkeit der m&h Software 3D Form Inspect war trotz kürzester Einweisung von nur einem halben Tag sofortige Akzeptanz bei allen Mitarbeitern gegeben. Berücksichtigt man den Altersdurchschnitt der betroffenen Mitarbeiter von 52 Jahren, so ist das eine sehr positive Feststellung.
„Wir haben das erstmals auf einer Ausstellung gesehen und nach einiger Prüfung sind wir sicher, dass m&h das beste System für die Werkzeugmaschine liefert“, schildert Herr Popov seinen Eindruck. „Es muss eine echte Erleichterung für die Mitarbeiter sein“, betont Herr Popov „Der Mann an der Maschine muss die Möglichkeit haben, das was die Maschine und das Werkzeug im Zusammenspiel als Ergebnis abliefern selbst zu bewerten und einzugreifen.“ Dies geht wirtschaftlich nur durch das Messen in der Maschine.
Das Tuschieren wurde um 70 – 80 % reduziert.
“Naturgemäß sind die Formen bei Vorwerk sehr komplex und bedürfen in der Regel mehrerer Optimierungs- und Anpassungsschleifen, bis sie für die Serienproduktion freigegeben werden. Im Fall eines Flügelrades wurde eine Form mit 10 Schiebern gebaut, in denen die Außenkonturen mit den Flügeln abgebildet werden. Bei dieser Form hat man erstmalig konsequent die Einsätze und Formkörper noch in den Werkzeugmaschinen mit den Messtastern und der Software von m&h gemessen. Das Ergebnis war nicht nur ein spürbar besseres Zusammenpassen beim Formaufbau und ein deutlich reduzierter Tuschieraufwand, sondern, zur Überraschung aller, ein gratfreies erstes Werkstück, schon bei der ersten Abmusterung. „Da braucht man über die wenigen Minuten Messzeit auf der Maschine nicht mehr nachdenken“, freut sich Herr Popov.
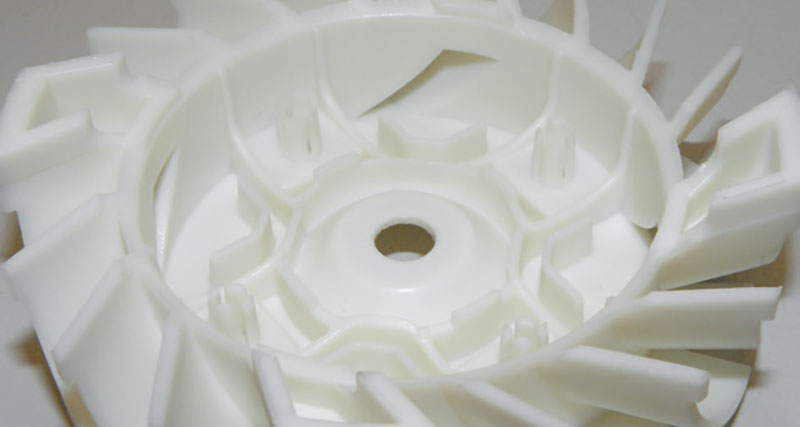
„Nun wissen wir immer, was wir tun und lernen unsere Werkzeuge viel besser kennen“, sagt Herr Popov. „Wir haben gelernt, die Lebensdauer der Einsätze zu verlängern. Übergänge an den Produktwänden können deutlich verbessert werden. Wir fräsen jetzt auf Null und unsere Tuschierflächen sehen völlig anders aus“, berichtet er. Das Tuschieren wurde um 70 – 80 % reduziert. Es ist viel mehr Ruhe eingekehrt, weil die Qualität schon auf der Maschine geprüft wird. „Wir halten heute unsere Termine alle ein oder sind sogar früher dran“, freut sich Herr Popov.