Il Gruppo Bosch abbatte i costi e riduce i tempi di calibrazione con ODYSSEE CAE
Di Camilo Cruz, ricercatore in ingegneria delle materie plastiche, Robert Bosch GmbH, e Sandra Saad, ingegnere responsabile dello sviluppo, Robert Bosch GmbH
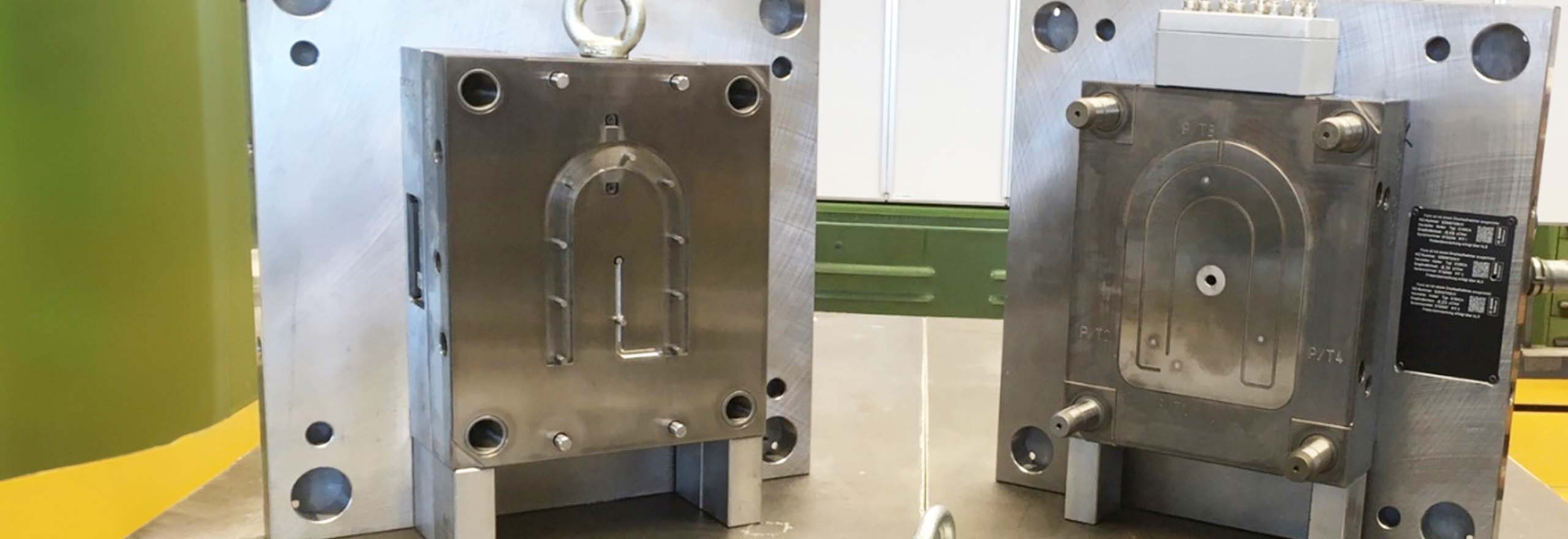
Engineering Reality 2024 volume 1
Accelerare la produzione intelligente
Il Gruppo Bosch è un'azienda internazionale leader nel settore della tecnologia e dei servizi, con un fatturato di 88,2 miliardi di euro e 421.300 collaboratori in tutto il mondo. Con prodotti e servizi innovativi Bosch migliora la qualità della vita delle persone in tutto il mondo. Attraverso le sue 468 filiali e società a livello regionale, Bosch è presente in più di 60 Paesi.
Le attività dell'azienda si articolano in quattro divisioni: Soluzioni per la mobilità, Tecnologia industriale, Beni di consumo e Tecnologia per l'energia e l'edilizia. Il suo obiettivo strategico è quello di creare soluzioni e prodotti per rendere la vita più connessa, che siano dotati di intelligenza artificiale (IA) oppure che siano sviluppati o prodotti grazie al suo contributo.
Attraverso una rete globale Bosch Research alimenta il processo di innovazione dei settori di attività di Bosch. L'azienda utilizza componenti in plastica in tutti i settori di attività, tra cui ruote dentate per biciclette elettriche o tosaerba robotizzati. Un recente progetto di Bosch Research si è concentrato sull'industrializzazione dei metodi di progettazione virtuale di materie plastiche stampate a iniezione. Bosch ha incaricato la propria divisione centrale di ricerca di creare processi di simulazione affidabili e facilmente utilizzabili da tutti i team di progettazione nel mondo.
La cristallizzazione dei materiali termoplastici semicristallini rende difficile la simulazione del restringimento e della deformazione.
Nel processo di progettazione tradizionale nei diversi reparti tecnici, la simulazione è utilizzata per prevedere l'impatto dei parametri di progettazione come la posizione del gate e i parametri di processo, come la temperatura dello stampo, sulla pressione di iniezione e sulla deformazione post-stampaggio.
Per quanto riguarda i materiali polimerici Bosch utilizza principalmente materiali termoplastici tecnici ad alte prestazioni, la maggior parte dei quali sono semicristallini. Nel processo di stampaggio a iniezione di materiali termoplastici semicristallini si verifica una cristallizzazione indotta dal flusso che influisce sulla viscosità e sulla solidificazione del materiale durante la lavorazione. Questo comportamento è fondamentale in quanto incide sulla pressione necessaria durante il processo di stampaggio a iniezione e sul restringimento e sulla deformazione del pezzo finale.
Il tipo di cristallizzazione che si verifica durante il processo di stampaggio a iniezione è complesso e difficile da modellare a livello matematico. Inoltre, i modelli disponibili nel software di stampaggio a iniezione sono difficili da calibrare sperimentalmente, con molte variabili che sono costose da identificare per ogni singolo materiale. Ai fini della progettazione, tuttavia, i tecnici hanno bisogno di un modo per simulare materiali semicristallini senza semplificare eccessivamente la cristallizzazione.
Poiché trascurare o semplificare il fenomeno della cristallizzazione influisce sui risultati della simulazione, il nostro team di Bosch Research era interessato a colmare il divario e a ottenere un quadro di simulazione più efficace per i materiali termoplastici semicristallini.
Implementazione di un modello di cristallizzazione indotta dal flusso nella simulazione dello stampaggio a iniezione
Un modo per migliorare l'accuratezza delle attività di progettazione virtuale per i componenti termoplastici semicristallini consiste nell'implementare un modello di cristallizzazione negli strumenti software di simulazione dello stampaggio a iniezione. Una problematica riguarda il fatto che un modello di questo tipo deve essere in grado di descrivere il processo di cristallizzazione nelle condizioni termomeccaniche del processo di stampaggio a iniezione, che presenta elevate velocità di raffreddamento (fino a centinaia di K/s) ed elevate velocità di taglio (fino a migliaia di 1/s). In particolare, le condizioni di deformazione della fusione hanno effetti non trascurabili sulla cinetica di cristallizzazione di un polimero semicristallino. Questo fenomeno è noto come cristallizzazione indotta dal flusso.
A questo punto, abbiamo dovuto scegliere tra due tipi di approcci di modellazione: un modello fenomenologico che descrive la nucleazione e la crescita della fase cristallina e un modello termomeccanico sviluppato nell'ambito di materiali standard generalizzati. Il primo approccio di modellazione si è affermato nella comunità di ricerca, ma richiede un'identificazione dei parametri costosa e dispendiosa in termini di tempo. Inoltre, tenere in considerazione l'effetto della cristallizzazione indotta dal flusso aumenta il numero di parametri dei materiali, e l'identificazione di tali parametri è eseguita in condizioni ben diverse da quelle effettive dello stampaggio a iniezione. Il secondo approccio di modellazione, basato sulla termodinamica irreversibile, non è molto diffuso nella comunità di ricerca sulla lavorazione dei polimeri, ma presenta alcuni vantaggi rispetto all'approccio fenomenologico: comprende intrinsecamente l'effetto della cristallizzazione indotta dal flusso e ha un numero notevolmente inferiore di parametri dipendenti dal materiale.
Per questi motivi abbiamo deciso di implementare il modello termomeccanico come routine definita dall'utente in un software professionale per la simulazione dello stampaggio a iniezione. L'implementazione includeva anche un nuovo termine nell'equazione energetica che tiene conto del calore latente della cristallizzazione, nonché modelli dipendenti dalla cristallizzazione per viscosità, densità (o PVT) e solidificazione. In questa fase la sfida principale era di stabilire un metodo affidabile per l'identificazione dei parametri in funzione del materiale. ODYSSEE si è inserito qui per svolgere questa operazione in modo intelligente.
Modelli surrogati accurati per l'identificazione dei parametri
Come menzionato in precedenza, la cristallizzazione indotta dal flusso nello stampaggio a iniezione si verifica in condizioni termomeccaniche estremamente difficili da ricreare anche con strumenti di caratterizzazione dei materiali all'avanguardia. Per superare questo ostacolo, il nostro team di ricerca e sviluppo ha pianificato di eseguire l'identificazione dei parametri utilizzando i dati acquisiti direttamente dai test di stampaggio a iniezione. In concreto abbiamo proposto di utilizzare i valori di pressione nello stampo come descrittore indiretto del fenomeno di cristallizzazione e come dati di riferimento per la calibrazione dei modelli implementati.
La calibrazione di un parametro è fondamentalmente un problema di ottimizzazione eseguito su una funzione matematica. L'attività consiste nell'individuare i valori delle variabili in ingresso che riducono al minimo l'errore tra l'uscita della funzione e un riferimento di tale uscita, che viene in genere ottenuto sperimentalmente o tramite approcci di modello alternativi. Nel nostro caso, la funzione è il modello di simulazione con le implementazioni definite dall'utente, le variabili di ingresso sono i parametri sconosciuti del materiale del modello di cristallizzazione indotta dal flusso, le uscite sono i valori di pressione nello stampo calcolati nelle posizioni dei sensori e il riferimento è il segnale di pressione effettivo acquisito dai sensori dello stampo.
Gli algoritmi di ottimizzazione normalmente richiedono di ripetere la valutazione della funzione in un ciclo per raggiungere un minimo o massimo locale accettabile. D'altra parte, il numero di iterazioni richieste aumenta sostanzialmente con il numero di variabili indipendenti da ottimizzare. Il problema è che la nostra simulazione di stampaggio a iniezione è una funzione computazionale impegnativa, che richiede minuti (persino ore) per generare un risultato, quindi l'ottimizzazione potrebbe facilmente diventare un processo estremamente dispendioso in termini di tempo. Per risolvere questo problema, entra in gioco ODYSSEE CAE. In sostanza con l'aiuto di ODYSSEE possiamo generare modelli surrogati (o metamodelli), che sono in grado di emulare i risultati della simulazione, ma con un costo di calcolo notevolmente inferiore. Al posto della simulazione , possiamo utilizzare questi modelli surrogati all'interno della routine di ottimizzazione e identificare i parametri dei materiali del modello di cristallizzazione indotta dal flusso in pochi secondi.
ODYSSEE consente un flusso di lavoro fluido e affidabile per la generazione di modelli surrogati basati su dati in ingresso/uscita (I/O). Nel nostro caso, ODYSSEE fornisce persino uno strumento per la creazione di un Design of Experiment (DoE) adeguato, che è la base per il campionamento dei dati in uscita. La generazione di modelli surrogati è in linea di principio una questione di apprendimento automatico supervisionato che ODYSSEE ha implementato utilizzando la tecnica classica di suddivisione dei dati I/O in set di dati di formazione e convalida per valutare le prestazioni del modello surrogato. Una volta caricati i dati in ingresso/uscita in ODYSSEE, lo strumento consente di confrontare tutti gli approcci di modellazione surrogata, che includono modelli di ordine ridotto (ROM) e metodi di interpolazione avanzati, rendendo più semplice la selezione della tecnica di modello surrogato più pertinente.
Infine, utilizzando i segnali di pressione effettivi acquisiti dai sensori dello stampo come target, possiamo anche eseguire attività di ottimizzazione all'interno di ODYSSEE utilizzando i modelli surrogati creati in precedenza. È interessante notare che, con l'aiuto del team Hexagon, abbiamo potuto personalizzare l'algoritmo di ottimizzazione per questo particolare caso d'uso di identificazione dei dati dei materiali. Con i parametri dipendenti dal materiale identificati al livello del modello surrogato, ora possiamo utilizzarli al livello di simulazione per calcolare qualsiasi altra geometria utilizzando lo stesso materiale. La figura sopra mostra la migliore precisione nella stima della pressione della simulazione con modello di cristallizzazione (calibrata utilizzando ODYSSEE) rispetto alla simulazione predefinita (senza modello di cristallizzazione). L'errore rms alla radice deve essere pari a zero per la massima precisione, mentre il coefficiente di determinazione deve tendere a 1 quando la precisione aumenta.
Figura 1: Prestazioni del modello di cristallizzazione predefinito rispetto a quello calibrato (ottimizzazione) nella stima della pressione della simulazione di stampaggio a iniezione ad alta fedeltà
L'identificazione dei parametri basata su metamodelli riduce i tempi e i costi di sviluppo
Utilizzando l'ottimizzazione del metamodello ODYSSEE, abbiamo trovato un metodo intelligente per identificare i parametri dipendenti dal materiale dai dati acquisiti in condizioni reali di stampaggio a iniezione. Questa efficiente calibrazione dei parametri è un contributo significativo per l'implementazione del nostro modello di cristallizzazione indotta dal flusso all'interno di un software industriale di simulazione dello stampaggio a iniezione ad alta fedeltà. In questo modo compiamo un grande passo avanti verso una stima più accurata delle esigenze di pressione e di deformazione nella simulazione dello stampaggio a iniezione.
Questo nuovo approccio all'identificazione dei parametri ha aiutato l'azienda a risparmiare tempo e denaro. Sostituendo il tradizionale percorso di caratterizzazione e identificazione dei materiali con il nuovo approccio della calibrazione data-driven basata sul processo reale utilizzando un metamodello, si riduce il tempo necessario del 90% e i costi del 60%. Considerando il modello di cristallizzazione indotta dal flusso nella simulazione dello stampaggio a iniezione, Bosch si aspetta di ridurre in modo sostanziale i problemi in officina correlati a piccoli colpi o riempimento incompleto dello stampo.
Con l'aiuto di questa simulazione di processo migliorata, i reparti tecnici saranno in grado di regolare le proprie geometrie di progettazione con maggiore affidabilità e/o di definire con maggiore precisione i requisiti di pressione della macchina per evitare costose e lunghe procedure di ricreazione dello stampo o tentativi ed errori in officina. In breve, Bosch mira a ridurre il tempo di sviluppo dei componenti stampati a iniezione consentendo una fase di progettazione virtuale più affidabile e accurata.
Un'interfaccia intuitiva semplifica la produzione
Per garantire una diffusione a livello industriale dell'identificazione dei parametri basata sui metamodelli, abbiamo bisogno di strumenti software con un alto livello di maturità UX. ODYSSEE rappresenta una buona scelta per il nostro flusso di lavoro perché ha un'interfaccia intuitiva per il caricamento dei dati, la formazione e la valutazione di diversi approcci di modellazione surrogata e infine l'esecuzione di prove di ottimizzazione.
Dopo aver convalidato il concetto di identificazione dei parametri basata su metamodelli con un materiale in poliossimetilene, abbiamo messo in atto un flusso di lavoro a livello industriale per garantire la calibrazione di qualsiasi altro materiale termoplastico semicristallino. Questo garantisce un sistema industriale per fornire in modo efficiente i dati sui materiali all'intero spettro dei reparti di ingegneria delle materie plastiche del gruppo Bosch in tutto il mondo.
L'implementazione industriale della simulazione ad alta fedeltà con modello di cristallizzazione indotta dal flusso è illustrata nella Figura 2. Le prime 3 fasi corrispondono all'identificazione dei parametri del materiale assistita da ODYSSEE. Queste fasi avvengono all'interno di Bosch Research (divisione centrale R&S) per tutti i nuovi materiali. In questa fase offline otteniamo essenzialmente schede dei materiali per il nostro modello di cristallizzazione indotta dal flusso, che vengono quindi messe a disposizione di tutti i tecnici di simulazione del gruppo Bosch.
La fase 4 rappresenta essenzialmente la simulazione quotidiana dello stampaggio a iniezione, compresa la cristallizzazione indotta dal flusso, che necessita delle schede dei materiali identificate con l'aiuto di ODYSSEE. Per i tecnici di simulazione delle diverse divisioni di Bosch, lo sforzo aggiuntivo si limita all'attivazione del solutore API definito dall'utente e al caricamento della rispettiva scheda materiale. Bastano pochi clic in più per beneficiare di una stima più affidabile dello sviluppo della pressione e della deformazione finale nello stampaggio a iniezione.
Figura 2: Dal concetto al prodotto - Simulazione dello stampaggio a iniezione con modello di cristallizzazione indotta dal flusso presso Bosch
Questo caso di successo di ottimizzazione basata su metamodelli è un traguardo importante da cui partire per estendere l'applicazione di queste tecniche ad altri processi di ricerca. Bosch ha stabilito un mandato che prevede che l'azienda cerchi nuovi campi di applicazione in cui l'utilizzo di modelli surrogati, apprendimento automatico e intelligenza artificiale offra un vantaggio tecnico.