Bosch-Gruppe senkt Kosten und verkürzt Kalibrierzeit mit ODYSSEE CAE
Camilo Cruz, Research Scientist für Plastics Engineering, Robert Bosch GmbH, und Sandra Saad, Development Engineer, Robert Bosch GmbH
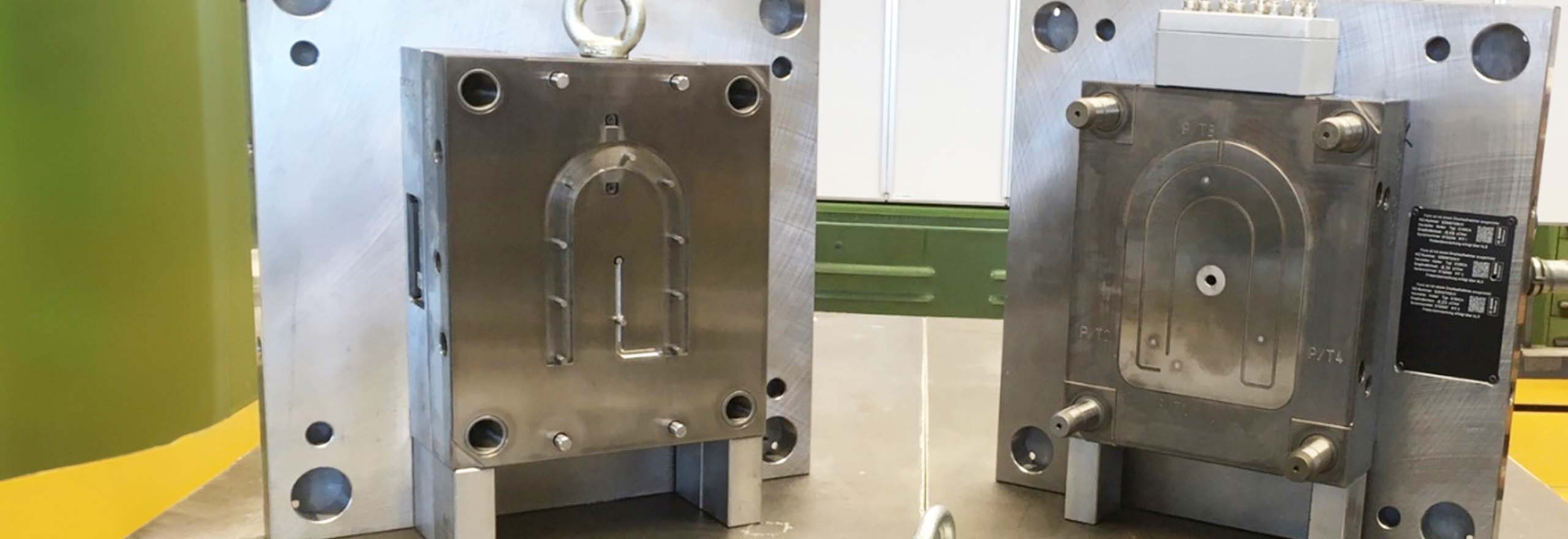
Engineering Reality 2024 Ausgabe 1
Accelerate Smart Manufacturing
Die Bosch-Gruppe ist ein international führendes Technologie- und Dienstleistungsunternehmen mit einem Umsatz von 88,2 Mrd. EUR und 421.300 Mitarbeitenden weltweit. Mit innovativen und inspirierenden Produkten sowie Dienstleistungen verbessert Bosch weltweit die Lebensqualität von Menschen. Über seine 468 Tochter- und Regionalgesellschaften ist Bosch in über 60 Ländern präsent.
Die Aktivitäten des Unternehmens gliedern sich in vier Bereiche: Mobility, Industrial Technology, Consumer Goods sowie Energy and Building Technology. Strategisches Ziel sind Lösungen und Produkte für das vernetzte Leben, die entweder über künstliche Intelligenz (KI) verfügen oder mit deren Einsatz entwickelt oder hergestellt werden.
Bosch Research arbeitet in einem globalen Netzwerk und füllt die Innovationspipeline der Geschäftsbereiche von Bosch. Das Unternehmen setzt über alle Geschäftsbereiche hinweg Kunststoffkomponenten ein, wie beispielsweise Zahnräder für E-Bikes oder Mähroboter. Ein aktuelles Projekt von Bosch Research konzentrierte sich auf die Industrialisierung von Engineering-Verfahren für das virtuelle Design von Kunststoffspritzguss. Bosch hat seine zentrale Forschungsabteilung damit beauftragt, akkurate Simulationsworkflows zu entwickeln, die für alle Teams im Bereich Engineering weltweit einfach zu nutzen sind.
Die Kristallisation von teilkristallinen Thermoplasten erschwert die Simulation von Schwindung und Verzug
Im herkömmlichen Engineering-Designprozess wird die Simulation zur Prognose hinsichtlich der Auswirkungen von Designparametern wie z. B. dem Anspritzpunkt sowie von Prozessparametern wie z.B. der Werkzeugtemperatur auf den Einspritzdruck und den Spritzverzug nach dem Spritzguss eingesetzt.
Bei den Polymermaterialien setzt Bosch vorwiegend hochleistungsfähige technische Thermoplaste ein, die meisten davon teilkristallin. Beim Spritzgießen von teilkristallinen Thermoplasten findet eine strömungsinduzierte Kristallisation statt, welche die Viskosität und das Erstarrungsverhalten des Materials während der Verarbeitung beeinflusst. Dieses Verhalten wirkt sich entscheidend auf den Druckbedarf während des Spritzgussverfahrens sowie auf Schwindung und Verzug des produzierten Bauteils aus.
Die Art der Kristallisation, die während des Spritzgussverfahrens auftritt, ist komplex und schwierig mathematisch zu modellieren. Auch sind die verfügbaren Modelle in der Spritzgusssoftware schwierig experimentell zu kalibrieren, da es viele Variablen gibt, die für jedes einzelne Material aufwändig zu ermitteln sind. Es bedarf einer Lösung, teilkristalline Materialien zu simulieren, ohne die Kristallisation zu sehr zu vereinfachen.
Deren Vernachlässigung oder Vereinfachung wirkt sich auf die Simulationsergebnisse aus. Das Team von Bosch Research suchte deshalb ein robusteres Simulations-Framework für teilkristalline Thermoplaste.
Implementierung eines strömungsinduzierten Kristallisationsmodells in die Spritzgusssimulation
Eine Vorgehensweise zur Verbesserung der Genauigkeit der virtuellen Engineering-Aufgaben für teilkristalline thermoplastische Teile ist die Implementierung eines Kristallisationsmodells in die Software-Tools der Spritzgusssimulation. Eine Herausforderung dabei ist, dass ein solches Modell in der Lage ist, den Kristallisationsprozess unter den thermomechanischen Bedingungen des Spritzgussprozesses zu beschreiben, der hohe Kühlraten (bis zu mehreren Hundert K/s) und hohe Scherraten (bis zu Tausend 1/s) aufweist. Insbesondere die Verformungsbedingungen der Schmelze haben nicht zu vernachlässigende Auswirkungen auf die Kristallisationskinetik eines teilkristallinen Polymers. Dies wird als strömungsinduzierte Kristallisation bezeichnet.
An dieser Stelle mussten wir zwischen zwei Modellierungsansätzen wählen: Dem phänomenologischen Modell, das die Keimbildung und das Wachstum der kristallinen Phase beschreibt, oder dem thermomechanischen Modell, das im Rahmen von generalisierten Standardmaterialien entwickelt wurde. Der erste Modellierungsansatz ist in der Forschung gut etabliert, erfordert jedoch eine kostspielige und zeitaufwändige Parameteridentifikation. Darüber hinaus erhöht auch der Effekt der strömungsinduzierten Kristallisation die Anzahl der Materialparameter, und die Identifikation der Materialparameter erfolgt unter Bedingungen, die weit von denen des tatsächlichen Spritzgießens entfernt sind. Der zweite Modellierungsansatz, der auf irreversibler Thermodynamik basiert, ist in der Polymerverarbeitung eher ungewöhnlich, weist aber einige Vorteile gegenüber dem phänomenologischen Ansatz auf: Er schließt den Effekt der strömungsinduzierten Kristallisation mit ein und weist eine wesentlich geringere Anzahl materialabhängiger Parametern auf.
Aus den genannten Gründen haben wir beschlossen, das thermomechanische Modell als benutzerdefinierte Routine in eine kommerzielle Software zur Spritzgusssimulation zu implementieren. Die Implementierung umfasste auch einen neuen Term in der Energiegleichung, der die latente Wärme der Kristallisation sowie kristallisationsabhängige Modelle für Viskosität, Dichte (oder PVT) und Erstarrung berücksichtigt. Zu diesem Zeitpunkt bestand die noch offene Aufgabe darin, eine verlässliche Methode zur Identifikation der materialabhängigen Parameter zu etablieren. ODYSSEE hat diese Aufgabe mit Bravour gemeistert.
Genaue Ersatzmodelle für die Parameteridentifikation
Wie bereits erwähnt, tritt die strömungsinduzierte Kristallisation beim Spritzgießen unter thermomechanischen Bedingungen auf, die selbst mit modernster Ausstattung zur Materialcharakterisierung äußerst schwer nachzubilden sind. Deshalb plante unser F&E-Team, die Parameteridentifikation anhand von Daten durchzuführen, die direkt aus Spritzgussversuchen gewonnen wurden. Konkret haben wir vorgeschlagen, In-Mould-Drucksignale als indirekten Deskriptor des Kristallisationseffektes und als Referenzdaten für die Kalibrierung der implementierten Modelle zu verwenden.
Eine Parameterkalibrierung ist grundsätzlich ein Optimierungsproblem, das über eine mathematische Funktion gelöst wird. Die Aufgabe besteht darin, die Werte der Eingangsvariablen herauszufinden, die den Fehler zwischen der Funktionsausgabe und einem Referenzwert dieser Ausgabe minimieren, der typischerweise experimentell oder durch alternative Modellansätze entsteht. In unserem Fall ist die Funktion das High-Fidelity-Simulationsmodell mit unseren benutzerdefinierten Implementierungen, die Eingangsvariablen sind die unbekannten Materialparameter des strömungsinduzierten Kristallisationsmodells, die Ausgaben sind die an den Sensorpositionen berechneten In-Mould-Drucksignale und die Referenz ist das tatsächliche Drucksignal, das von den Formsensoren erfasst wird.
Optimierungsalgorithmen erfordern normalerweise die wiederholte Bewertung der Funktion in einer Schleife, um ein akzeptables lokales Minimum oder Maximum zu erreichen. Andererseits nimmt die Anzahl der erforderlichen Iterationen mit der Anzahl der zu optimierenden unabhängigen Variablen erheblich zu. Gerade hier ist das Problem, dass unsere High-Fidelity-Spritzgusssimulation eine rechnerisch aufwändige Funktion ist, die Minuten (oft sogar Stunden) benötigt, um ein Output zu erzeugen, sodass die Optimierung leicht zu einem extrem zeitaufwändigen Prozess werden kann. Um dieses Problem zu lösen, kommt ODYSSEE CAE ins Spiel. Grundsätzlich können wir mit Hilfe von ODYSSEE Ersatzmodelle (oder Metamodelle) erzeugen, die in der Lage sind, die Ergebnisse der High-Fidelity-Simulation zu emulieren, jedoch mit einem wesentlich geringeren Rechenaufwand. Statt der High-Fidelity-Simulation können wir diese Ersatzmodelle innerhalb der Optimierungsroutine verwenden und die Materialparameter des strömungsinduzierten Kristallisationsmodells in Sekundenschnelle identifizieren.
Der Mehrwert von ODYSSEE liegt im reibungslosen und robusten Workflow zur Erstellung von Ersatzmodellen auf der Grundlage von Input/Output(I/O). Für unseren Fall bietet ODYSSEE sogar Tools zur Erstellung eines geeigneten Design of Experiments (DoE), das die Grundlage für die Stichprobe der Ausgangsdaten durch Auswertung der High-Fidelity-Simulation innerhalb der Eingabevariablen bildet. Die Generierung von Ersatzmodellen ist im Prinzip ein Problem des überwachten maschinellen Lernens, das ODYSSEE mithilfe der klassischen Technik der Aufteilung von I/O-Daten in Schulungs- und Validierungsdatensätze zur Bewertung der Leistung des Ersatzmodells implementiert hat. Sobald die Eingabe-/Ausgabedaten in ODYSSEE geladen sind, erfolgt der Abgleich aller Ersatzmodellierungen, einschließlich reduzierter Ordnungsmodelle (ROM) und erweiterte Interpolationsmethoden, wodurch die Auswahl der am besten geeigneten Ersatzmodelltechnik vereinfacht wird.
Schließlich können wir mithilfe der tatsächlichen Drucksignale, die von den Formsensoren als Ziel erfasst werden, auch Optimierungsaufgaben in ODYSSEE mit den zuvor erstellten Ersatzmodellen ausführen. Interessanterweise konnten wir mit Hilfe des Hexagon-Teams den Optimierungsalgorithmus für diese spezielle Anwendung der Materialidentifikation anpassen. Mit den auf der Ersatzmodellebene identifizierten materialabhängigen Parametern können wir nun auf der High-Fidelity-Simulationsebene jede andere Geometrie mit demselben Material berechnen. Die obige Abbildung zeigt die verbesserte Genauigkeit bei der Druckschätzung der High-Fidelity-Simulation mit Kristallisationsmodell (kalibriert mit ODYSSEE) im Vergleich zur Standard-High-Fidelity-Simulation (ohne Kristallisationsmodell). Die mittlere quadratische Abweichung sollte für die höchste Genauigkeit Null betragen, während das Bestimmtheitsmaß bei steigender Genauigkeit gegen 1 tendieren sollte.
Abbildung 1: Leistung des Defaults im Vergleich zum kalibrierten Kristallisationsmodell (Optimierung) bei der Druckabschätzung in der High-Fidelity-Spritzgusssimulation
Metamodellbasierte Parameteridentifikation reduziert Entwicklungszeit und -kosten
Mithilfe der ODYSSEE-Metamodelloptimierung haben wir eine intelligente Methode zur Identifikation materialabhängiger Parameter aus Daten gefunden, die unter realen Spritzgussbedingungen erfasst wurden. Diese effiziente Kalibrierung von Parametern leistet einen wesentlichen Beitrag zur Implementierung unseres strömungsinduzierten Kristallisationsmodells in einer industriellen High-Fidelity-Spritzguss-Simulationssoftware. Das ist ein großer Schritt nach vorne hinsichtlich der genaueren Schätzung des Druckbedarfs und des Verzugs in der Spritzgusssimulation.
Mit diesem neuen Ansatz der Parameteridentifikation konnten Zeit und Kosten im Unternehmen gespart werden. Das Ersetzen der traditionellen Methode zur Materialcharakterisierung und -identifikation durch den neuartigen Ansatz der Kalibrierung auf Basis von Ist-Prozessdaten mithilfe eines Metamodells reduziert den Zeitaufwand um 90 % und senkt die Kosten um 60 %. Durch die Berücksichtigung eines strömungsinduzierten Kristallisationsmodells in der Spritzgusssimulation treten deutlich weniger Probleme in der Fertigung auf, wie etwa die unvollständige Befüllung der Form.
Anhand dieser verbesserten Prozesssimulation lassen sich Entwurfsgeometrien besser anpassen und/oder die Maschinendruckanforderungen genauer definieren, um kostspielige und zeitaufwändige Rekursionen oder 'Trial-and-Error-Verfahren' in der Fertigung zu vermeiden. Kurz gesagt, Bosch erzielt eine Reduzierung der Entwicklungszeit von Spritzgussteilen dank einer robusteren und genaueren virtuellen Designphase.
Eine anwenderfreundliche Bedienoberfläche erleichtert die Industrialisierung
Um einen industriellen Einsatz der metamodellbasierten Parameteridentifikation zu gewährleisten, benötigen wir Softwaretools mit einem hohen UX-Reifegrad. ODYSSEE unterstützt durch sein benutzerfreundliches Interface zum Laden von Daten, zum Trainieren und Auswerten verschiedener Surrogat-Modellierungsansätze und schließlich zur Durchführung von Optimierungsläufen unsere Workflows ideal.
Nach der Validierung des Konzepts der metamodellbasierten Parameteridentifikation mit einem POM-Material haben wir einen industriellen Workflow eingerichtet, der die Kalibrierung jedes anderen teilkristallinen thermoplastischen Materials sicherstellt. Damit wird eine industrielle Pipeline zur effizienten Bereitstellung von Materialdaten für das gesamte Spektrum des Bereiches Plastics Engineering der Bosch-Gruppe weltweit erreicht.
Der industrielle Einsatz der High-Fidelity-Simulation mit strömungsinduziertem Kristallisationsmodell ist in Abbildung 2 dargestellt. Die ersten drei Schritte entsprechen der von ODYSSEE unterstützten Identifikation der Materialparameter. Diese Schritte finden für alle neuen Materialien bei Bosch Research (zentrale F&E-Abteilung) statt. In dieser Offline-Phase erhalten wir grundsätzlich Materialkarten für unser strömungsinduziertes Kristallisationsmodell, die dann allen Simulationsingenieuren der Bosch-Gruppe zur Verfügung gestellt werden.
Schritt 4 stellt im Wesentlichen die tägliche Spritzgusssimulation inklusive strömungsinduzierter Kristallisation dar, für welche die mit Hilfe von ODYSSEE identifizierten Materialkarten benötigt werden. Für die Simulationsingenieure innerhalb der Bosch-Gruppe beschränkt sich der zusätzliche Aufwand auf die Aktivierung der benutzerdefinierten Solver-API und das Laden der jeweiligen Materialkarte. Nur noch wenige Klicks und Sie profitieren von einer zuverlässigeren Schätzung der Druckentwicklung und des finalen Verzugs beim Spritzgießen.
Abbildung 2: Vom Konzept bis zur Industrialisierung – Spritzgusssimulation mit strömungsinduziertem Kristallisationsmodell bei Bosch
Diese erfolgreiche Case Study der metamodellbasierten Optimierung markiert einen Meilenstein, was die Anwendung dieser Techniken auf für andere Forschungsprozesse betrifft. Bosch hat sich zum Ziel gesetzt, neue Anwendungsbereiche hinsichtlich des Einsatzes von Ersatzmodellen, maschinellem Lernen und künstlicher Intelligenz zu erschliessen.