Ahorro de tiempo y dinero con un brazo de medición con sistema de instalación repetible de sensor
Absolute Arm technical article

Contacto
1. Introducción
Uno de los avances más importantes en los sistemas de metrología portátil en los últimos años ha sido la introducción de un sistema de instalación repetible para sensores táctiles y escáneres 3D. La gama de productos de Absolute Arm de Hexagon utiliza una unión cinemática que permite instalar sensores y escáneres en el brazo rápidamente y (lo más importante) sin comprometer la precisión de la medición.En este artículo se explican los beneficios para los operarios de usar brazos de medición portátil en la industria, además de analizar las características técnicas que ofrecen estos beneficios.
2. La creciente importancia de la versatilidad
Ahora los usuarios de equipo de metrología en todo el mundo desean ‘medir más con menos’. En vez de incurrir en el gasto de usar diferentes sistemas de medición para cada aplicación específica, existe una demanda creciente de usar un solo sistema que se pueda aplicar en una gama más amplia de aplicaciones. Por lo tanto, las exigencias sobre los sistemas de medición son mucho mayores que nunca: la clave está en la versatilidad.El actual sistema Absolute Arm ofrece una amplia gama de diversos sensores y palpadores para satisfacer estas necesidades. Mientras que los sensores táctiles y escáneres láser convencionales son los más populares, los sensores tubulares infrarrojos y los sensores ópticos también se pueden usar en el mismo brazo e intercambiarlos según las necesidades de medición.
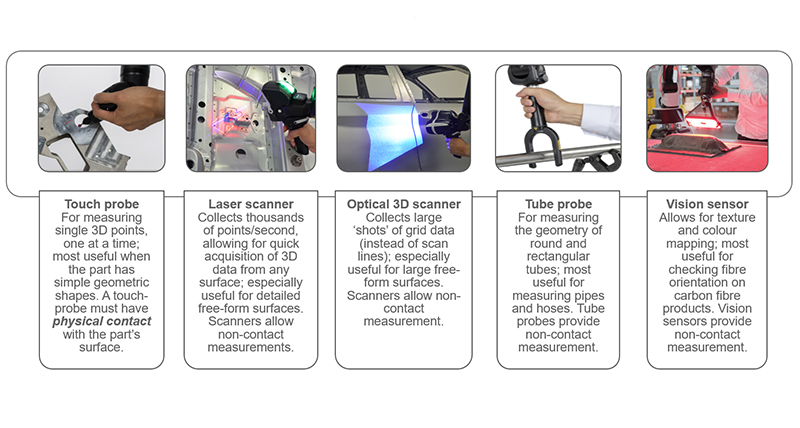
Figura 1: Diferentes palpadores y sensores del Absolute Arm
A continuación se presentan algunos ejemplos que ilustran la necesidad de versatilidad en la producción industrial moderna:
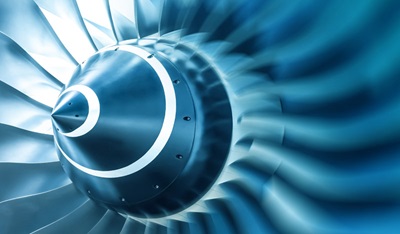
Mantenimiento de turbinas
Los álabes de las turbinas pueden sufrir daños durante el vuelo, por lo que es posible que sea necesario obtener piezas de repuesto rápidamente. Una forma rápida de lograrlo consiste en crear un escaneo 3D de un álabe ‘correcto’ para su posterior mecanizado, aunque pueden existir áreas con tolerancias demasiado elevadas para un escáner láser (como el eje de la turbina, por ejemplo). Aquí se usaría un sensor táctil para garantizar una máxima precisión.Número de sensores necesarios: 2
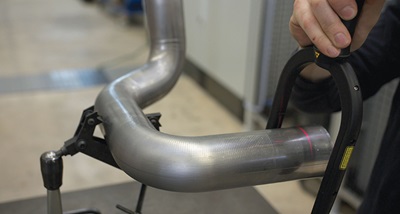
Fabricación de tubos de escape para automoción
Los sistemas de tubos de escape a menudo ocupan la longitud completa de un automóvil. Es importante que no toquen pieza móvil alguna para que sea posible revisar su ‘ruta’. Un sensor tubular infrarrojo permite medir con precisión el perfil del tubo, mientras que un sensor táctil permite al usuario medir las piezas más complejas del sistema como los soportes y las suspensiones.Número de sensores necesarios: 2

Fabricación de componentes aeroespaciales de composites
Con materiales de composite, no solo importa la forma de la pieza, sino también la orientación de las fibras que le dan fortaleza a la pieza. Para comprobar una pieza de este tipo, generalmente sus superficies sin forma definida serán escaneadas con un escáner láser, y previamente se instala un sensor óptico para analizar la orientación. También es posible usar un sensor táctil para áreas de muy alta tolerancia.Número de sensores necesarios: 3

Fabricación de piezas mecanizadas (sección del adaptador del cuerpo de la bomba)
Generalmente una sección de un adaptador del cuerpo de la bomba tiene varios elementos para distribuir el flujo del líquido. La inspección del elemento del cuerpo interior se lleva a cabo fácilmente utilizando una extensión de sensor o un sensor angular (sensor de gancho) para alcanzar los puntos ocultos de medición. El resto de la pieza se puede analizar fácilmente con un sensor táctil de longitud estándar.Número de sensores necesarios: 2
Todos estos ejemplos muestran qué tan común resulta para los operarios la necesidad de intercambiar entre diversas mediciones con palpadores y/o sensores para terminar el trabajo.
3. Intercambio de palpadores y sensores: ¿Qué puede salir mal?
Cuando un palpador (o sensor) del sistema se intercambia a mitad del trabajo, es muy importante que el que reemplaza se coloque exactamente en el mismo lugar del brazo donde fue calibrado originalmente. Si no fuera posible, los usuarios deben elegir entre una menor precisión o una menor productividad.Pérdida de precisión
Si el nuevo palpador o sensor se instala en el brazo en una posición que no coincide exactamente con la posición original de calibración, cualquier lectura proveniente del palpador o sensor será errónea y posiblemente provocará una fabricación de piezas defectuosas.Pérdida de tiempo
La única forma de asegurar precisión en esta situación consiste en recalibrar el sistema de medición para ofrecer datos precisos nuevamente. Para ello, sería necesario detener el trabajo de medición para que el operario pudiera llevar a cabo una calibración. Si las mediciones se efectúan en un taller, podría ser necesario mover el equipo a un entorno más estable.Sin embargo, esto no garantiza recuperar el nivel de precisión obtenido antes del cambio de palpador o sensor; la calibración es un proceso muy variable, con algunos operarios más experimentados que otros.
4. La unión cinemática
La unión cinemática fue desarrollada originalmente para máquinas de medición por coordenadas (MMCs) estacionarias de alta precisión. Fue diseñada con el objetivo de garantizar que los sensores táctiles de la MMC conserven su precisión, aún al intercambiarlos en la MMC. Desde entonces, se ha ganado su lugar entre diversos productos de Hexagon y ha sido un elemento clave para el Absolute Arm desde 2010.En el Absolute Arm, esta unión cinemática se compone de dos interfaces: una en el brazo en sí mismo y la otra en el palpador o sensor que será instalado. La interface del brazo es el enchufe y la interface del palpador es la clavija. Al conectar ambas partes, el operario activa un mecanismo de leva en el brazo al girar una palanca. Esto fija el palpador en su posición en la empuñadura del brazo. De forma inversa, para retirar el palpador el operario puede girar la palanca en la dirección contraria para liberar las levas y desbloquearlo del brazo.
En la Figura 2 también se observan tres pares de ‘pernos de sujeción’. Garantizan que el palpador se pueda instalar en una sola ‘posición correcta’ – el operario no puede instalarlo de forma incorrecta.
Como beneficio adicional, cada palpador o sensor compatible con el Absolute Arm contiene un chip de ID único que, combinado con los contactos electrónicos que se muestran en la imagen, garantizan que la ‘identidad’ del palpador (por ejemplo su tipo de láser escáner o diámetro de punta) sea detectado automáticamente por el brazo al instalarlo. Gracias a este proceso, todo el software de medición se actualiza en consecuencia con las compensaciones dimensionales correctas. No se requiere intervención alguna del operario.

Figura 2: Elementos principales de la unión cinemática patentada por Hexagon.
Estos elementos aseguran la conservación de tres principios principales, para garantizar la precisión y la versatilidad mientras se ahorra tiempo también:
La instalación del palpador siempre es repetible
Al garantizar que el palpador o el sensor se instale en una posición estandarizada que siempre es la misma en el orden de unas cuantas micras, la recalibración no es necesaria al instalar el sensor y la precisión de la medición queda garantizada. Gracias a esto, también se ahorra tiempo y es posible completar la medici´ón más rápidamente.El palpador siempre se identifica automáticamente
Gracias a los contactos electrónicos y el chip de ID incrustado, el brazo ‘reconocerá’ automáticamente el palpador o el sensor en cuanto se instale. Esto significa que el usuario no necesita seleccionar un sensor particular en el software antes de medir con él. Esto reduce el riesgo del error humano.En los casos de algunos software de medición, también significa que el palpador o sensor ‘ideal’ para la aplicación en cuestión se puede recomendar al usuario a la mitad de la medición.
Posibilidad de agregar en cualquier momento nuevos palpadores y sensores
Gracias a la unión cinemática, una sola calibración del brazo es suficiente. Esto significa que es posible agregar nuevos sensores a cualquier brazo existente en el campo con un mínimo de intervención. Es posible ampliar la funcionalidad de un brazo durante su vida útil.5. La unión cinemática y el Absolute Arm
La unión cinemática fue promovida primero por TESA (parte del grupo Hexagon) en Suiza para asegurar que los palpadores pudieran ser intercambiados fácilmente en las MMCs estacionarias. Actualmente, todos los palpadores y sensores para el Absolute Arm tienen incorporada la tecnología de unión cinemática de TESA (TKJ) como estándar. Gracias a un catálogo de más de cientos de palpadores y sensores disponibles, la unión cinemática es un pilar central del carácter multifuncional del Absolute Arm.La versatilidad permitida para la unión cinemática es una de las principales razones por la que el Absolute Arm a menudo es reconocido como la navaja suiza de la metrología: la mayor multiherramienta para la medición, equipado para manejar casi cualquier aplicación de inspección industrial.
La unión cinemática también ofrece una plataforma para el futuro que permite la rápida implementación de nuevos tipos de palpadores y tecnologías de medición, garantizando que cualquier palpador o sensor nuevo será compatible con cualquier Absolute Arm de la generación actual.
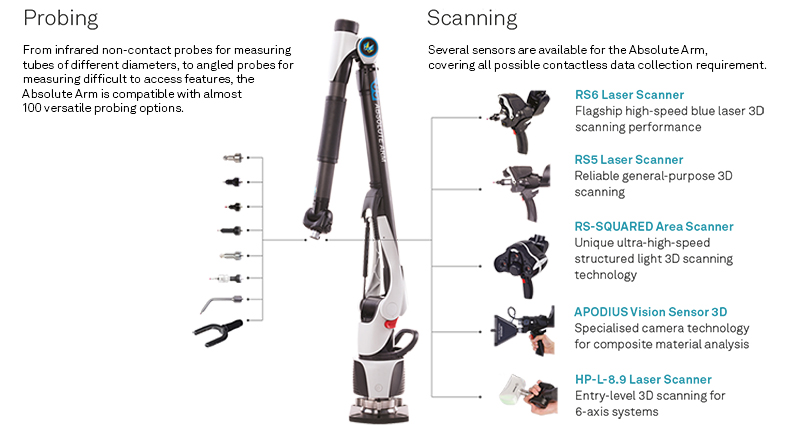
Figura 3: El Absolute Arm: la navaja suiza de la metrología.
Touch probe
A touch-probe, for measuring single 3D points. Most useful when the part has simple geometric shapes (mechanical parts). A touch-probe must have physical contact with the part’s surface.
Laser scanner
A laser scanner, collects thousands of points/second, allowing for quick acquisition of 3D data from any surface; especially useful for free-form surfaces. Scanners allow non-contact measurements.
Structured light scanner
A structured light scanner, collects large ‘shots’ of grid data (instead of scan lines); especially useful for large free-form surfaces. Scanners allow non-contact measurements.
Tube probe
A tube probe, for measuring round and rectangular tubes, such as pipes and hoses. Tube probes provide non-contact measurements.