Messen für den Durchblick
Cosmac - Italien
Kontakt

Ein italienischer Hersteller für Spritzgießformen sorgt mit dem Messen seiner Werkstücke noch in den Bearbeitungsmaschinen für Durchblick in seiner Fertigung. Dabei kommen deutsche Messtaster und Software von m&h auf japanischen Werkzeugmaschinen zum Einsatz.
Messen auf der Werkzeugmaschine ist zwischenzeitlich Stand der Technik, weil es Zeit spart und sofortige maschinelle Nacharbeit noch in der gleichen Spannung ermöglicht. Aber darüber hinaus ergeben sich viele weitere Effekte je nach Firma und ihren Gegebenheiten im Einsatzfall.
Weltweit greift man für diese Technik vor allem auf die Messtaster und die Software des deutschen Herstellers m&h zurück. Ein Besuch beim Formenbau Cosmac, der die Software 3D Form Inspect und die Taster von m&h auf Werkzeugmaschinen von MAZAK und YASDA einsetzt, zeigt nicht nur die internationale Dimension sondern beweist auch die problemlose Funktion des deutschen Systems mit asiatischen Werkzeugmaschinen und Steuerungen.
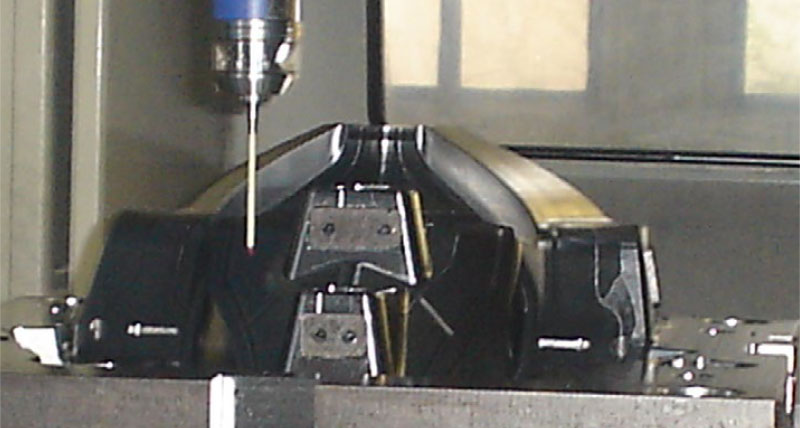
Während man seinerzeit beim Rüsten der Werkstücke herkömmliche Taster mit elektrischem Kontakt eingesetzt hat, musste mit zunehmender Komplexität der Werkstücke und immer enger werdenden Toleranzen eine Möglichkeit zum Messen der Formen und Einsätze geschaffen werden. „Wir wollten vor allem die Zeit zum Finishen deutlich abkürzen,“ sagt Alessandro Maccagnan, einer der beiden Brüder, die die junge und ambitionierte Firma führen. Vor mehr als einem Jahr bewiesen die beiden ihren Durchblick, als sie sich für die vergleichsweise günstige Nachrüstung Ihrer Bearbeitungszentren mit Messtastern von m&h und der Prüfsoftware 3D Form Inspect entschieden, statt eine Messmaschine zu kaufen. 3D Form Inspect von m&h ermöglicht die Kontrolle der Werkstücke noch in der Aufspannung in der Maschine. Die ermittelten Messergebnisse sind, dank einer integrierten, patentierten Kalibrierstrategie um die thermischen und kinematischen Abweichungen der Maschinen bereinigt, jederzeit verlässlich wiederholbar und mit denen einer Messmaschine vergleichbar.
Außerdem eröffnete sich so für Cosmac die Möglichkeit, Werkstücke sofort und ohne Genauigkeitsverlust durch eine zweite Aufspannung nacharbeiten zu können. Schließlich ist es nicht nur schwierig, ein Teil nach dem Messen auf einer Messmaschine wieder aufzunehmen und zu bearbeiten, sondern kostet teure Zeit. Oftmals wird die zur Verfügung stehende, enge Fertigungstoleranz schon allein durch den nahezu zwangsläufigen Versatz bei einer weiteren Aufspannung aufgezehrt. Im Hause Cosmac wurden die Taster durch den m&h-eigenen, italienischen Service an die vorhandenen Maschinen vom Typ MAZAK FJV250, MAZAK FJD5080 mit Mazatrol-Steuerungen und die YASDA YBM950 mit FANUC-Steuerung angebaut. Die Software 3D Form Inspect von m&h wurde auf einigen Computern in der Werkstatt, jeweils nahe der Werkzeugmaschine installiert, und direkt mit der jeweiligen CNC-Steuerung verbunden. Die Maschinenbediener wurden innerhalb eines Tages vor Ort an Ihren eigenen Werkstücken und Maschinen in den Gebrauch der Software eingewiesen. Die Bedienung wird als sehr einfach beschrieben. Alle Maschinenbediener arbeiten gerne damit und nutzen das System häufig. Zwischenzeitlich fordern die Kollegen an den Erodiermaschinen ähnliche Möglichkeiten.
„Alle unsere Wünsche und Erwartungen wurden erfüllt“, bestätigen Stefano und Alessandro Mac- cagnan unisono. An den Formen konnten die Bearbeitungsbereiche mit Problemen deutlich reduziert werden. Die Gesamtbearbeitungszeiten bezogen auf eine komplexe Form wurden kürzer, weil Nacharbeiten und Neuanfertigungen von Teilen der Formen gespart wurden. Immer wieder kam es früher vor, dass man erst beim Zusammenbau der Form Fehler gefunden hat und Teile einfach nicht zusammenpassten und noch einmal gefertigt werden mussten. „Das ist heute nicht mehr nötig.“ Weil eben alles auf Maß gearbeitet und kontrolliert ist. Wenn Ober- und Unterteil auf der gleichen Maschine gefertigt und mit m&h gemessen und kontrolliert ist, so stellt das praktisch einen geschlossenen Loop dar.
Die Teile passen dann perfekt zueinander. „Manchmal können wir einen Fehler in einer Formhälfte lassen und das Gegenstück einfach entsprechend anders bearbeiten. Das ist viel billiger als nach- oder gar neu zu bearbeiten,“ schildert Alessandro Maccagnan einen willkommenen Nebeneffekt. In vielen Fällen kann auch das Tuschieren weitgehend verkürzt werden, weil alle Teile viel besser passen. Es wird oftmals nur noch ein wenig poliert. „Bei einzelnen Formen haben wir 50 % der Zusammenbauzeit gegenüber den bisherigen Arbeitsmethoden eingespart. Das ist nicht immer so; in jedem Fall sparen wir aber im Durchschnitt 15 bis 20%“ schildert Alessandro Maccagnan den erzielten Erfolg.
Außerdem können wir jetzt unsere Qualität sofort dokumentieren und holen das Werkstück mit Messprotokoll von der Maschine,“ ergänzt Stefano Maccagnan. „Die Kunden akzeptieren die m&h Protokolle, was uns die Arbeit wesentlich erleichtert.“ Einige Kunden haben gegengeprüft und die mit m&h erstellten Protokolle für gut befunden.
Unproduktives Bearbeiten haben wir komplett eliminiert
Die gefundenen Abweichungen gegenüber den Kontrollmessungen auf der Messmaschine bewegten sich im μ-Bereich. „Manchmal ist die Werkzeugmaschine auch näher an der Wahrheit. Die Zeit zum Messen auf der Maschine ist im Vergleich zur gesamten Maschinenzeit einer Form vernachlässigbar,“ konstatiert Stefano Maccagnan. Alessandro Maccagnan ergänzt: „Das Messen dauert vielleicht 4 Minuten. Aber dann müssen wir 15 Minuten überlegen, wo die Abweichung herkommt und was zu tun ist. Aber wir erreichen Sicherheit über den gesamten Fertigungsprozess und kennen die benötigte Fertigungszeit. “Cosmac führt in seinen Arbeitsplänen, die in vielen Fällen auch zum Kunden gehen, das Messen mit m&h auf der Maschine ausdrücklich als Teil der geplanten Fertigungszeit auf. Gerne verweist man darauf, dass dies hin und wieder auch schon entscheidend war, einen Auftrag zu erhalten.
Neben diesen Effekten hat das Messen auf der Maschine noch zu ganz anderen Durchblicken im Betriebsablauf verholfen. „Wir haben die Bearbeitungen und das Verhalten der Werkzeuge ganz neu kennen gelernt,“ berichtet Stefano. „Wir verstehen jetzt den Zerspanungsvorgang viel besser.“ Aus den gefundenen Abweichungen am Werkstück konnten unmittelbar Schlüsse auf die verwendeten Werkzeuge und die Frässtrategien gezogen werden. So stellte sich schließlich heraus, das Maßabweichungen von Flächen in einem Fall dadurch verursacht waren, dass der verwendete Kugelfräser nicht wirklich Kugelform hatte. Zwischenzeitlich hat man die Werkzeuge selektiert und verwendet andere Werkzeuge als damals, zum Teil auch mit anderen Frässtrategien.
Alles in allem gibt es im Bereich der spanenden Fertigung bei Cosmac nun keine Überraschungen und keine Unsicherheiten mehr, die den Liefertermin hinausschieben. Die Fertigungszeit ist zu Beginn des Auftrags klar und kann eingehalten werden. „Unproduktives Bearbeiten haben wir komplett eliminiert,“ freut sich Alessandro Maccagnan. Auf die Frage, ob sie die Investition in Messtaster und Prüfsoftware von m&h noch einmal so tätigen würden, antworten beide Brüder einheitlich: „Sofort wieder!“