Controles de calidad a gran escala
Siemens examina los componentes de gran tamaño de la turbina de gas con el DPA de AICON.
Contacto

Turbinas de gas con una longitud de hasta 13 metros, 5 metros de altura y 400 toneladas de peso: los componentes de estas dimensiones forman parte de la actividad principal de la fábrica de turbinas de gas de Siemens en Moabit, Berlín. Los componentes de alta tecnología se utilizan en centrales eléctricas de todo el mundo y deben cumplir los requisitos más exigentes. Temperaturas de combustión extremadamente altas, grandes fuerzas centrífugas, así como vibraciones y cargas transitorias: las turbinas de gas están sometidas a condiciones de funcionamiento muy exigentes.
Por tanto, en la producción de las turbinas de gas y de sus componentes individuales, lo esencial es la exactitud en las medidas. Los componentes de acero deben tratarse uniformemente para que garanticen una estabilidad máxima. El DPA MoveInspect de AICON proporciona los datos para la comparación CAD.
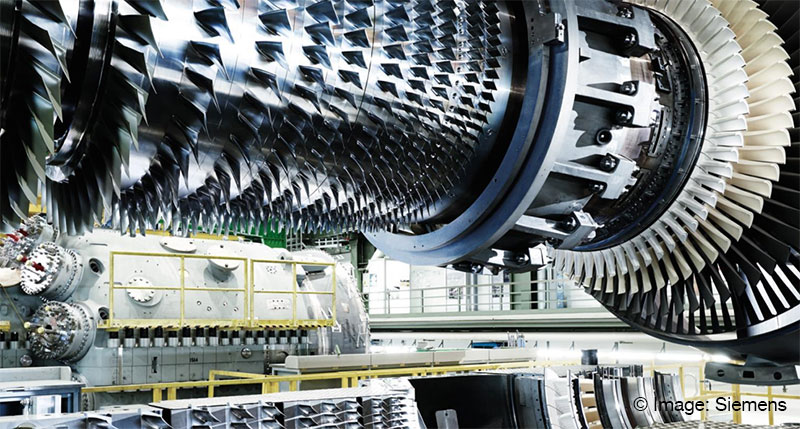
El factor de éxito eficacia energética
El camino hacia un sistema de energía sostenible va por la corriente eléctrica. Para ello se buscan tecnologías innovadoras. Siemens responde a estos requisitos del sistema completo de energía con producto innovadores, soluciones y servicios, un conocimiento técnico único y una competencia global en el mercado de la energía.
La gama de turbinas de gas para centrales eléctricas de Siemens está diseñada perfectamente a la medida de los requisitos de un mercado dinámico. Los modelos con una capacidad de 4 a 400 MW cumplen los más altos requisitos de un amplio espectro de aplicaciones y garantizan eficiencia, confianza, flexibilidad y compatibilidad medioambiental, bajos costes de ciclo de vida y una gran rentabilidad.
Medición individualizada para una tarea exigente
Los componentes de acero se elaboran mecánicamente y se ensamblan en su gran mayoría en la fábrica de turbinas de gas de Berlín. En el tratamiento surge la siguiente pregunta: ¿Hay suficiente materia bruta para el mecanizado en todos los puntos que se deben procesar? Para ellos hay que comparar el estado real con los datos CAD. Estos datos los calcula el DPA MoveInspect de AICON, que trabaja con una cámara digital de mano para registrar los datos y con el software de procesamiento de imágenes completamente automático 3D Studio de AICON.
Primero se proveerá el componente de acero de marcadores y adaptadores de medición individualizados y codificados en los puntos relevantes. Con la cámara digital se capta el objeto de medición desde distintas direcciones, de forma que se registren todas las áreas relevantes del mismo. El trabajo con marcadores codificados permite automatizar correctamente la evaluación, ya que la posición de cada punto está fijada en el componente. Cada usuario puede definir este proceso individualmente.
Las coordenadas calculadas se comparan automáticamente con los datos CAD en el SpatialAnalyzer para controlar la calidad básica del componente de fundición bruta, como p. ej. la medición y la posición de los orificios y las bridas. La medición se utiliza también para determinar la posición óptima de mecanizado (raja de juntas). ¡Una gran ventaja en cuanto tiempo y costes!
Después de la evaluación, el trabajador transfiere los valores registrados para la raja de junta al componente. Esto lo hará el trabajador conforme a un procedimiento desarrollado por Siemens. Con la ayuda de los marcadores de medición codificados, se raja la junta mediante golpes en el arco y una línea tangencial.
Siemens utiliza dos características especiales del software de AICON: Con el módulo Adapter, el usuario puede fabricar él mismo un adaptador específico y medir con el software de AICON. Siemens ha desarrollado algunos adaptadores para cantos y juntas. Están ligados a la posición del componente mediante los marcadores codificados. El módulo CodeMaker también permite al usuario crear sus propios marcadores de medición. Cada adaptador específico y cada marcador de medición puede etiquetarse en función de la tarea (p. ej. junta).
Para cada componente se crea una instrucción de medición individual. Esta contiene información sobre el montaje del componente, los dibujos a utilizar, protocolos y modelos CAD, así como la posición de los marcadores de medición. El uso de marcadores de medición y adaptadores "personalizados" permiten una evaluación altamente automatizada.

Una solución con futuro
En el pasado, Siemens utilizaba un sistema de seguimiento por láser para las tareas de medición. Pero este tipo de sistemas deben recolocarse al menos cinco veces durante la tarea de medición para detectar todos los puntos de medición relevantes. Un gran consumo de tiempo que se reduce significativamente con un sistema de fotogrametría. El DPA se sostiene con la mano, no necesita ningún punto de estacionamiento fijo y no le afectan las vibraciones ni los temblores.
En Siemens, el sistema de medición de AICON se ha impuesto sobre otros competidores del área de la fotogrametría. Bernhard Gauger, trabajador en la gestión de calidad, área de Tecnología de medición especial, está convencido del rendimiento técnico del DPA y apoya esta decisión: "Queríamos sustituir los métodos convencionales de medición para el control de calidad y la creación de rajas de junta con la fotogrametría. Nuestro objetivo era conseguir una gran precisión con una carga de trabajo reducida. Esto lo ha cumplido el DPA de AICON. Otra ventaja: La movilidad del sistema permite cualificar los procesos y los controles de calidad de los proveedores in situ".
El DPA de AICON es un sistema probado que se utiliza con éxito en diversas empresas y tareas de medición desde hace años. Gracias al diseño modular de la tecnología MoveInspect, el sistema puede adaptarse a las tareas individuales de medición de una empresa añadiendo complementos. ¡Una solución universal!