Digitale Zwillinge für Produktionsstätten zur Optimierung der Abläufe
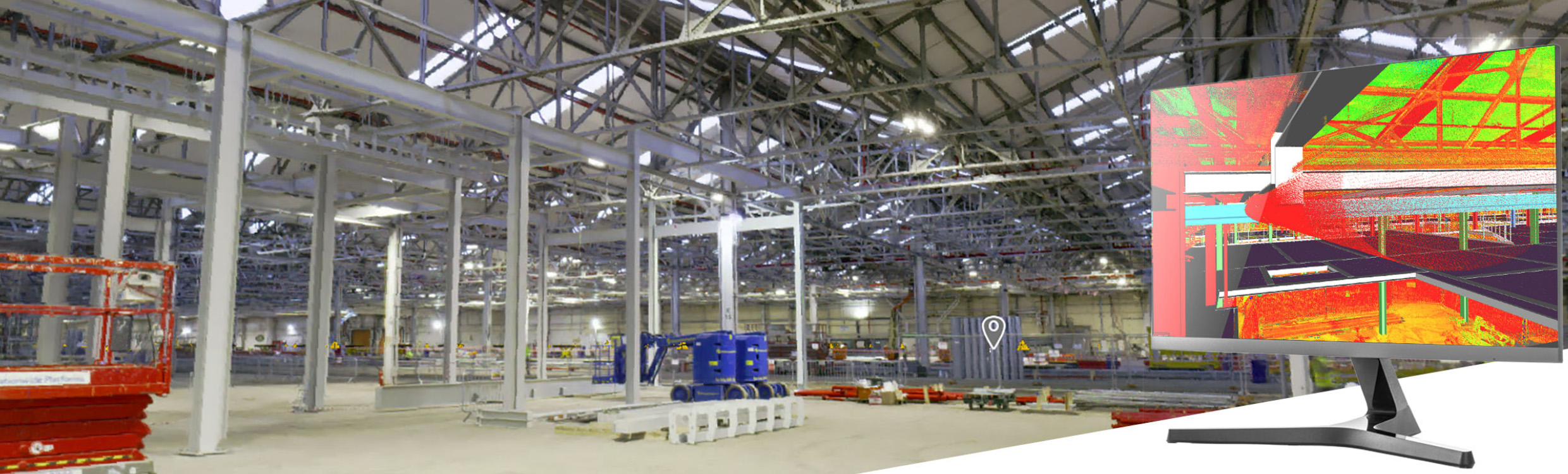
Es kann schwierig sein, eine bestehende Anlage zu renovieren oder zu erweitern. Wenn Firmen ihre Produktlinien erweitern, ordnen sie Montagelinien immer wieder neu an und nutzen Räume neu, um Produktionsabläufe zu optimieren. Ein Digitaler Zwilling beschleunigt den Planungsprozess für den Umbau von Produktionsstätten, erhöht die Sicherheitsstandards für Produktion und Mitarbeiter und steigert die Produktivität der Mitarbeiter.
Mehrere Unternehmen in Europa und den USA nutzen große Nachkriegsgebäude, die in den 1950er und 60er Jahren errichtet wurden, als Produktionsstätten. Viele dieser Immobilien verfügen über eine veraltete Infrastruktur und müssen aufgerüstet werden, um den neuesten Bau- und Produktionsvorschriften zu entsprechen. Begrenzte Platzverhältnisse in diesen älteren Produktionsstätten machen es schwierig, das Gebäude aufzurüsten und zu renovieren, um sichere Produktions- und Arbeitsbedingungen zu gewährleisten und Betriebsstillstände zu minimieren.
Ähnliche historische Produktionsstätten gehören Jaguar Land Rover Automotive PLC (JLR), einem multinationalen Automobilunternehmen mit Sitz in Whitley, Coventry, Großbritannien. Leider existieren kaum historische und aktuelle Aufzeichnungen über Planung, Bau und frühere Umbaumaßnahmen der Gebäude. Die Haupttätigkeiten von JLR sind Design, Entwicklung, Herstellung und Vertrieb von Fahrzeugen der legendären Automarken Jaguar und Land Rover.
JLR muss die Grundstücke häufig umgestalten, wenn neue Produktlinien auf den Markt kommen. Das Produktions- und Engineering-Team ist für die Entwicklung neuer Produktionsanlagen für ihre Produktionslinien verantwortlich. Dies kann sich auch auf ihre bestehenden Montagelinien und die Gebäudeinfrastruktur auswirken und erfordert Neugestaltungen, Renovierungen und Änderungen an den Produktionsstätten. JLR benötigte einen aktuellen Digitalen Zwilling des bestehenden Gebäudes und der Produktionslinien, um alle Änderungen effizient zu planen und neu zu gestalten.
Digitale Zwillinge für Gebäudemanagement und Renovierung
Ein genauer Digitaler Zwilling der bestehenden Bedingungen ermöglicht es dem Team für Konstruktion und Gebäudemanagement, ihre Renovierungen virtuell zu planen und Änderungen zu evaluieren, bevor sie durchgeführt werden. Durch den Einsatz der richtigen Technologien decken Gebäudemanagementteams versteckte Ineffizienzen und Kosten auf, schaffen neue Werte für Gebäude und stellen sicher, dass die Immobilien vollständig optimiert sind.
In der Vergangenheit kam es bei JLR bei Renovierungen zu Konflikten. Das Unternehmen suchte nach einer Lösung, um die bestehenden Gebäude in Großbritannien und der Slowakei besser verstehen zu können und eine grundlegende Kollisionsermittlung durchzuführen. Dieser Prozess würde dem Team helfen, Störungen im Bauprojektmodell zu erkennen, zu überprüfen und zu melden.
Im Bestreben, mehr Arbeit intern zu erledigen, weniger von externen Dienstleistern abhängig zu sein und die Geschäftsprozesse zu vereinfachen, investierte JLR in den Leica RTC360 Laserscanner, eineReality-Capture-Lösung, mit der Anwender ihre Umgebung in 3D erfassen und dokumentieren können, sowie in die Leica Cyclone-Software zur Verarbeitung von Punktwolken.
„Wir haben oft Vermessungsunternehmen mit der Durchführung unserer internen Vermessungsprojekte beauftragt, aber wir mussten feststellen, dass die Vermessungsdaten nicht zwischen den Anbietern ausgetauscht wurden. Indem wir die Grundstücke selbst scannen und die Daten verarbeiten, können wir die Informationen an ein größeres Projektteam weitergeben, so dass wir alle davon profitieren können“, sagte Alistair Innes, Informationsmanager bei JLR.
Vernetzung der physischen und digitalen Welt, um die Kontrolle über Ihre Anlage zu erlangen
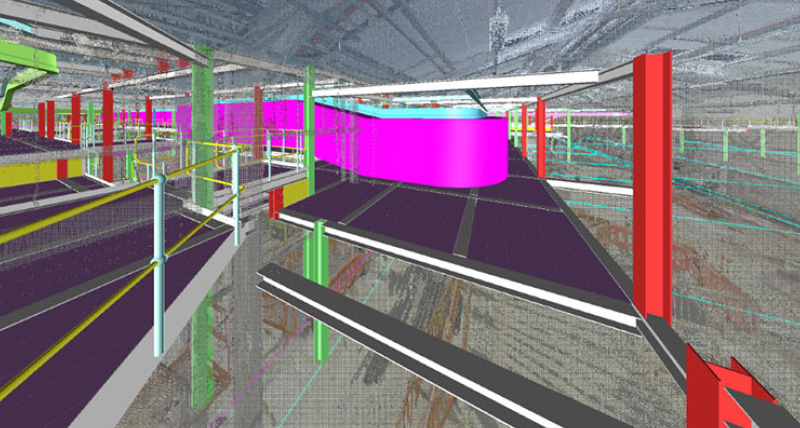
Der RTC360 ermöglichte es ihnen, die physische Welt zu erfassen und eine digitale 3D-Punktwolke ihrer Anlagen zu erstellen. Dieser digitale 3D-Zwilling unterstützte das Team bei der Analyse und Modifikation verschiedener Elemente der bestehenden Anlage direkt im Modell.
JLR nutzte die RTC360-Punktwolke für verschiedene Anwendungen:
1. Erstellen von digitalen Modellen (Digitaler Zwilling) physischer Standorte.
Matt Thompson, Virtual Manufacturing Engineering Manager bei JLR, und sein Team scannten eine 9.000 m2 große Montagehalle, um einen Digitalen Zwilling für den Abgleich zwischen virtueller und physischer Realität zu erstellen. Der Digitale Zwilling ist der extrahierte Wert, die Verbindung zwischen der physischen und der virtuellen Welt, die zur digitalen Transformation führt, indem intelligente Software an den Daten einer Umgebungserfassung arbeitet – mit anderen Worten: „das physische Produkt, das virtuelle Produkt und die Verbindung zwischen den beiden“.
JLR nutzte den Digitalen Zwilling, um eine Kollisionserkennung durchzuführen und schnell zu bestätigen, was sich in der Anlage befindet, wenn es um die Gestaltung von Elementen im digitalen Raum geht. Der Digitale Zwilling wurde während der Vorplanungsphase für die Standortanalyse, die Überprüfung bestehender Bauwerke, die Baukostenanalyse und die Evaluierung des technischen Budgets verwendet.
„Die Nutzung des Leica RTC360 hat es uns ermöglicht, unsere physische und unsere digitale Welt zu verbinden wie nie zuvor. Das Team kann nun die physische Geometrie schnell in unsere Entwurfsphase integrieren und so sicherzustellen, dass wir Konflikte in der Installationsphase minimieren, lange bevor wir anfangen, Bauteile zu konstruieren“, sagte Matt Thompson, Leiter Virtuelle Fertigungstechnik bei JLR.
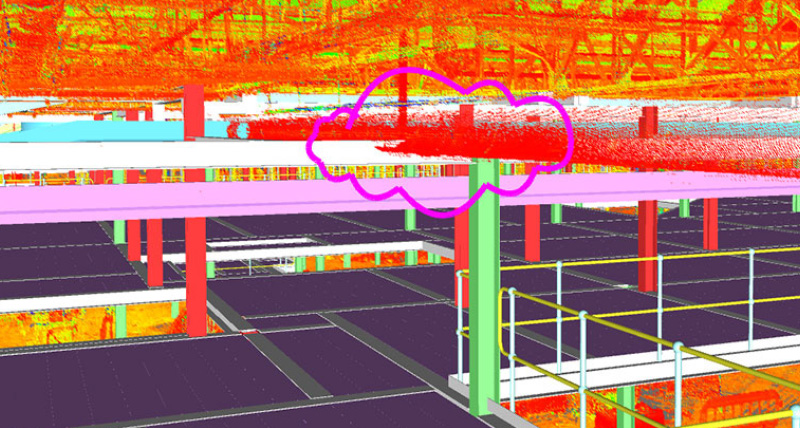
2. Verifizierung
Fehler und Nacharbeiten können das Baubudget belasten. Alistair Innes, Informationsmanager bei JLR, vergleicht die hochwertigen Punktwolken-Scandaten des RTC360 mit dem Modell, um festzustellen, ob es den Anforderungen entspricht. Der Prozess stellt sicher, dass die Ausrüstung an der richtigen Stelle und gemäß dem 3D-CAD-Modell installiert wird. Leica CloudWorx ermöglichte JLR ein effizientes Arbeiten mit der Punktwolke direkt in Navisworks.
3. Erstellen von CAD-Modellen für physische Ausrichtungen
Als JLR ein Klimakammerprüfsystem installieren musste, benötigte das Unternehmen zwei Stunden für das Scannen, eine Stunde für die Registrierung und vier Stunden für das Post-Processing, um die CAD-Modelle aus der Punktwolke zu erstellen. Die Punktwolke stellt die reale Umgebung dar und ermöglicht einen genauen 3D-CAD-Modellierungsprozess.
„Mit dem RTC360 können wir Räume im Haus schnell scannen, CAD-Modelle innerhalb weniger Stunden erstellen und den Beteiligten die erforderlichen Ergebnisse für das Design, die Änderung und Installation der Ausrüstung in der Anlage liefern", sagte Thompson. „Anstatt uns auf externe Dienstleister zu verlassen, können wir den Bedarf ermitteln und ein Team einsetzen, das die Erhebungsdaten innerhalb eines Tages bereitstellt.“
Investition in Entscheidungsinstrumente
Leica Geosystems organisierte eine zweitägige Schulung für JLR in Milton Keynes, Großbritannien, um das volle Potenzial des RTC360 auszuschöpfen und bietet Kundensupport während der Datenerfassung und -verarbeitung.
„Als Ingenieure, die bei JLR für die Implementierung der Reality-Capture-Lösung in der Produktion verantwortlich ist, waren wir vom Service und Support durch Leica Geosystems begeistert. Sie unterstützten uns in jeder Phase, von der Auswahl der Ausrüstung bis hin zur ihrer Anwendung vor Ort. Die Möglichkeit, unsere Produktionsstätten im eigenen Haus zu erfassen, hat die Welt verändert und führt bereits zu Kosteneinsparungen und betrieblicher Effizienz.Wir bedauern nur, dass wir dies nicht schon früher getan haben“, sagte Alistair Innes, Informationsmanager bei JLR.