オペレーションを最適化する工場向けのデジタルツイン
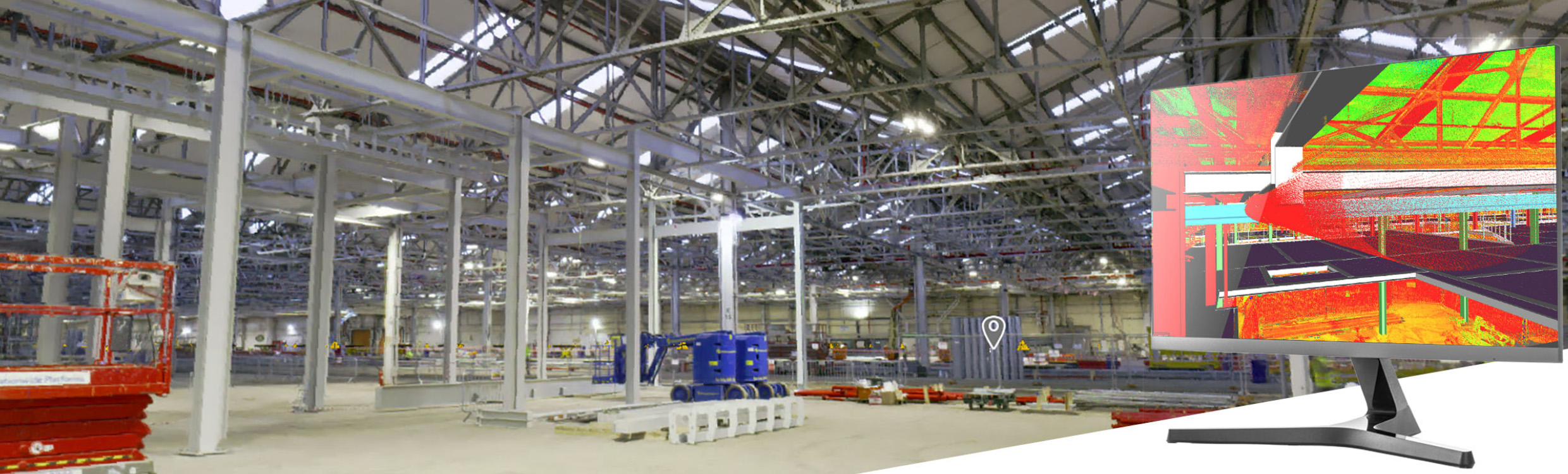
既存の施設の改修や拡張を完了するのが困難な場合があります。企業は製品ラインを拡大する際、組立ラインを定期的に再配置し、スペースを再利用して製造作業を最適化しています。これらの施設のデジタルツインがあれば、製造現場の変更の計画プロセスをスピードアップし、生産と従業員の安全基準を高め、作業員の生産性を向上させることができます。
ヨーロッパと米国で複数の企業が、1950年代と60年代に工場として建設された戦後の大規模建物を使用しています。これらの建物の多くは旧式の設備が備えられており、最新の建築基準や製造規制に適合するようにアップグレードする必要があります。古い工場はスペースが限られているため、労働の安全性と作業条件を保証し、オペレーションのダウンタイムを最小限に抑えるための建物のアップグレードや改修が難しくなっています。
同様に、最新の記録のない歴史のある工場を、英国コーベントリー市ホイットリーに本社を置く英国の多国籍自動車メーカー、 Jaguar Land Rover Automotive PLC(JLR)が保有しています。JLRの主要な業務は、アイコニックなJaguarおよびLand Roverの自動車ブランドを持つ自動車の設計、開発、製造、販売です。
JLRでは、新製品ラインが導入された際に、頻繁に施設を改修する必要があります。製造・エンジニアリングチームは、生産ライン用の新しい製造機器の開発を担当しています。これは、既存の組立ラインや建物の設備にも影響し、再設計、改修、製造施設の変更が必要です。JLRは、変更を効率的に計画し、再設計するために、既存の建物と生産ラインで最新のデジタルツインを必要としていました。
施設管理と改修のためのデジタルツイン
既存の状態について正確なデジタルツインを持つことで、エンジニアリングおよび施設管理チームは、仮想的に改修を計画し、改修を実施する前に効果を評価することができます。適切な技術を採用することで、施設管理チームは隠れた非効率性を発見してコストを削減し、建物に新しい価値を付加し、施設が最適な状態であることを確認します。
かつてJLRは、改修の際に干渉を繰り返していました。イギリスとスロバキアの既存の建物を理解し、基本的な干渉検知を行うためのソリューションを探していました。このプロセスは、チームが建設プロジェクトモデルにおける障害を特定・調査し、報告するのに役立ちます。
JLRは社内でより多くの作業を行い、外部プロバイダーに依存せず、ビジネスプロセスを容易にするためにLeica RTC360レーザースキャナーユーザーが3Dで環境をキャプチャして文書化できるリアリティキャプチャ・ソリューションとLeica Cyclone点群データ処理ソフトウェアに投資しました 。
JLRの情報担当マネジャーのAlistair Innes氏は次のように述べています。「当社は、社内調査を調査会社に依頼することがよくありましたが、その場合、調査データが業者間で共有されていないことがありました。自分たちで物件をスキャンしてデータを処理することで、プロジェクトチーム全体で情報を共有し、全員がその情報を活用できるようになりました。」
物理的世界とデジタル世界をつなぐことで、施設の管理を強化します
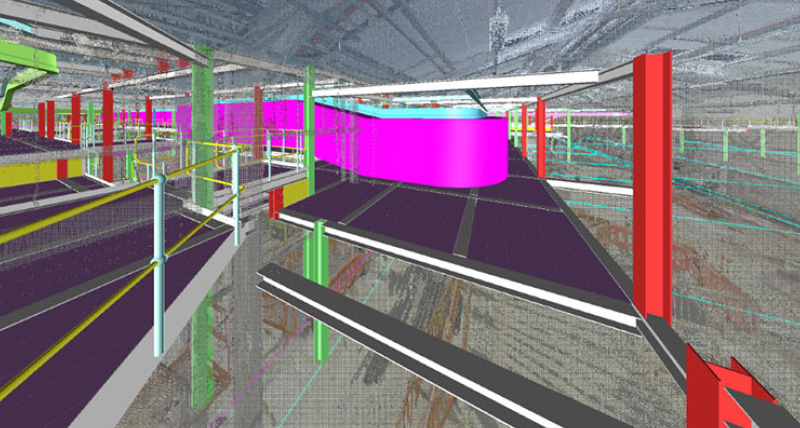
RTC360は、物理的な世界をキャプチャし、施設のデジタル3D点群を作成することを可能にしました。この3Dデジタルツインは、チームが既存の施設の様々な要素を直接モデルで分析し、修正するのに役立ちます。
JLRは、様々なアプリケーションにRTC360点群を使用しました。
1. 物理的な位置のデジタルモデル(デジタルツイン)を作成すること。
JLRのバーチャル製造エンジニアリングマネージャーであるMatt Thompson氏と彼のチームは、9000平方メートルの組立作業所をスキャンし、仮想フィジカル・アライメントのためのデジタルツインを作成しました。デジタルツインは抽出された値であり、物理的な世界と仮想世界のつながりであり、リアリティキャプチャのデータで動作するインテリジェントなソフトウェア、つまり「物理的な製品、仮想製品、両者間の接続」を通して、デジタルトランスフォーメーションにつながります。
JLRは、デジタルツインを使用して干渉検出を行い、デジタル空間で部材を設計するときに施設内の物理的条件を迅速に確認しました。デジタルツインは設計前の段階で、敷地分析、既存構造物の検討、建設コスト分析、エンジニアリング予算評価などに使用されました。
「Leica RTC360を使用することで、物理的世界とデジタル世界をこれまでになくリンクすることができました。チームは、物理的な形状を設計段階に迅速に取り入れることができるようになり、部品の製造を開始するずっと前に、設置段階での干渉を最小限に抑えることができるようになりました」とJLRの仮想製造エンジニアリングマネージャー、Matt Thompson氏は述べています。
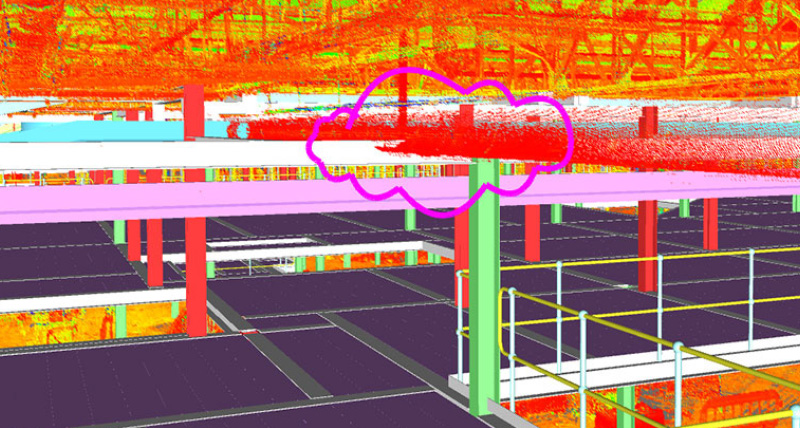
2. 確認
間違いや手戻りは建設予算を使います。JLRの情報マネージャーであるAlistair Innes氏は、RTC360の作成した竣工後の高品質な点群スキャンデータをモデルと比較し、要件を満たしているかどうかを確認するという積極的なアプローチを行っています。このプロセスにより、3D CADモデルに従って、機器を適切な場所に設置することができます。Leica CloudWorx によって、JLRはNavisworksで直接点群の効率的な作業ができるようになりました。
3. 物理的なアライメントのCADモデルを作成するには
JLRが気候室テスターシステムを導入することになったとき、点群からCADモデルを作成するのに、スキャンに2時間、合成に1時間、後処理に4時間かかったそうです。点群は実際の環境を表し、正確な3D CADモデリングプロセスを可能にします。
「RTC360を使用することで、屋内の空間を迅速にスキャンし、2-3時間でCADモデルを作成し、関係者に施設の機器の設計、修正、設置に必要な成果物を提供できます」とThompson 氏は述べます。「外部プロバイダーに頼る代わりに、当社はニーズを特定し、チームを活性化して1日で調査データを提供することができます。」
意思決定ツールへの投資
ライカジオシステムズは、英国ミルトンキーンズのJLRの2日間のトレーニングを企画し、 RTC360の可能性を最大限に引き出し、データ取得と処理についてのアフターセールスサポートをしました。
「JLRの製造エンジニアリング業務にリアリティキャプチャ機能を導入する担当エンジニアとして、ライカジオシステムズのサービスやサポートに満足しています。機器の選定から現場での機器の使用まで、あらゆる段階でサポートをしてくれました。屋内で工場をキャプチャする能力は、大きな変革をもたらし、コスト削減と運用効率改善をすでに実現しています。当社が唯一後悔していることは、もっと早く導入しなかったことです」とJLRの情報マネージャー、Alistair Innes氏は述べています。