MOTOR VEHICLE UNIVERSITY OF EMILIA-ROMAGNA
In collaboration with Maserati SPA
Keywords; Multi-disciplinary, Structure-borne, CAE, Road Noise, NVH
Pretext
The electrification revolution has introduced a paradigm shift in the design and research of vehicles. The initial conjecture was that the introduction of electric cars would ultimately diminish the area of NVH analysis. However, on the contrary, it has revealed an unknown and extensive domain in this field. The differences, such as powertrain and packaging, are the most noticeable game-changers. Removal of ICE powertrain comes at the cost of the absence of the masking noise, giving rise to other noise sources. Significant noise contribution has shifted from powertrain noise (ICEV) to road noise (BEV) as shown in figure 1. It is hinted that BEV is not quieter as expected because the road noise increases with speed and now becomes the dominant noise source. The most well-known technique to handle road noise is Transfer Path Analysis (TPA). This technique identifies the critical noise paths on the chassis and car body contributing to the interior noise. This case study presents the prediction of structure-borne road noise by applying a merely new multidisciplinary methodology involving both multi-body and FEM together using a specific tire CDTire model.
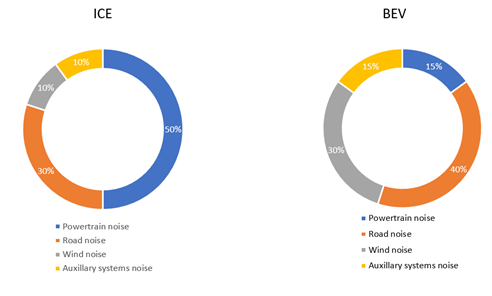
Modeling
The Multi-disciplinary methodology is based on a CAE approach that combines the finite element method and multi-body simulation and an additional postprocessing tool for the final calculations. The Multi-body simulation extracts dynamic forces induced on body structure via suspension system from the tire-road interaction. The Finite element part is used to simulate the Noise transfer function generated from the FEM model, including the vehicle cavity and trimmed body, representing the body. Moreover, FE is also used for generating flexible bodies used in multi-body simulations. The decoupling of different disciplines allows experts to focus on their domains. Hence superior simulation approach is introduced, which reduces complexity and time, and guarantees reliable accuracy.
The workflow of the methodology is presented in figure 2. To analyze the implementation and robustness of this methodology following full vehicle models as shown in figure 2 were constructed,
- Model A consists of two flexible subsystems, vehicle body and rear suspension (condensed at more than twice the frequency of interest). While all other subsystems are rigid as shown in figure 3(a).
- Model B consists of two flexible subsystems, vehicle body and rear subframes (condensed at more than twice the frequency of interest). While all other subsystems are rigid as shown in figure 3(b).
In order to further deepen the investigation, two more variants of Model B were constructed as follows,
- Model B-Flex links is a modified version of Model B consisting of identical flexible subsystems, vehicle body, rear subframes (condensed at more than twice the frequency of interest) but with an addition of flexible front and rear suspension links (condensed at more than twice the frequency of interest) as shown in figure 3(c).
- Model B-Low Upright Setting is a modified version of Model B consisting of two flexible subsystems, vehicle body and rear subframes (condensed at more than twice the frequency of interest) with the modification of front suspension hardpoints as shown in figure 3(d).

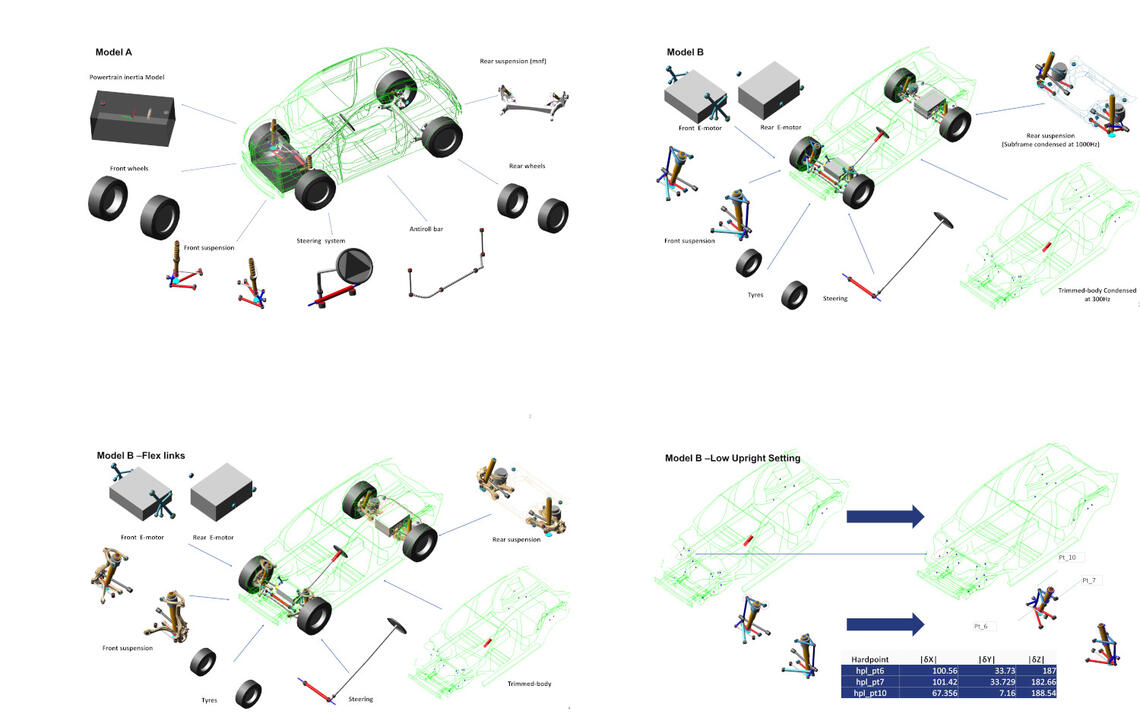
Analysis
The power-off maneuver was chosen in MB-SHARC to remain consistent with the experimental procedure. The full vehicle models consisting of MBS bushing models were simulated on two different road models, pavé and coarse road. All the parameters including maneuver set-up, output size, acquisition time, and solver settings were chosen to keep in mind the consistency with the experimental procedure, accuracy and precision requirements, computational time, and the guidelines provided in the CD-Tire manual.
Results
Both forces and P/F data were further combined in separate post-processing software to perform TPA. Following test cases were analyzed during post-processing,
1. Correlation between Simulated and Experimental results of road noise of Model A on pavé and coarse road, as shown in figure 4(a).
2. Sensitivity analysis between two NTF (Step 5 and Step C) on the road noise of Model B on pavé and coarse road, as shown in figure 4(b).
3. Correlation between Model B and Model B-flex links on pavé and coarse roads in fig 4(c).
4. Sensitivity analysis on road due to Model B- flex links having only front and rear suspension flexible links being rigid on the coarse road, as shown in figure 4(d).
5. Sensitivity analysis between Model B-Low upright Setting having flexible or rigid vehicle body and subframe on pavé road, also depicted in figure 4(d).
6. Finally, a comparison between Model B and Model B- Low Upright Setting on pavé and coarse road presented in figure 4(e).
Conclusion
In a nutshell, the case study presented a multidisciplinary CAE methodology to calculate structure-borne road noise and the techniques combined to tackle road noise with a fresh and different approach. The application of this methodology to different test cases proved its worth by showing a good correlation with experimental results and achieving meaningful results. It is recommended to apply the crawl-walk-run approach that is to initially start with a simple rigid body model and then introducing flexible bodies. High-fidelity models can be compelling at first, but they come at a greater cost therefore care should be taken. This methodology can be applied to further transfer paths test cases such as noise generated by the engine or by any other subsystem.
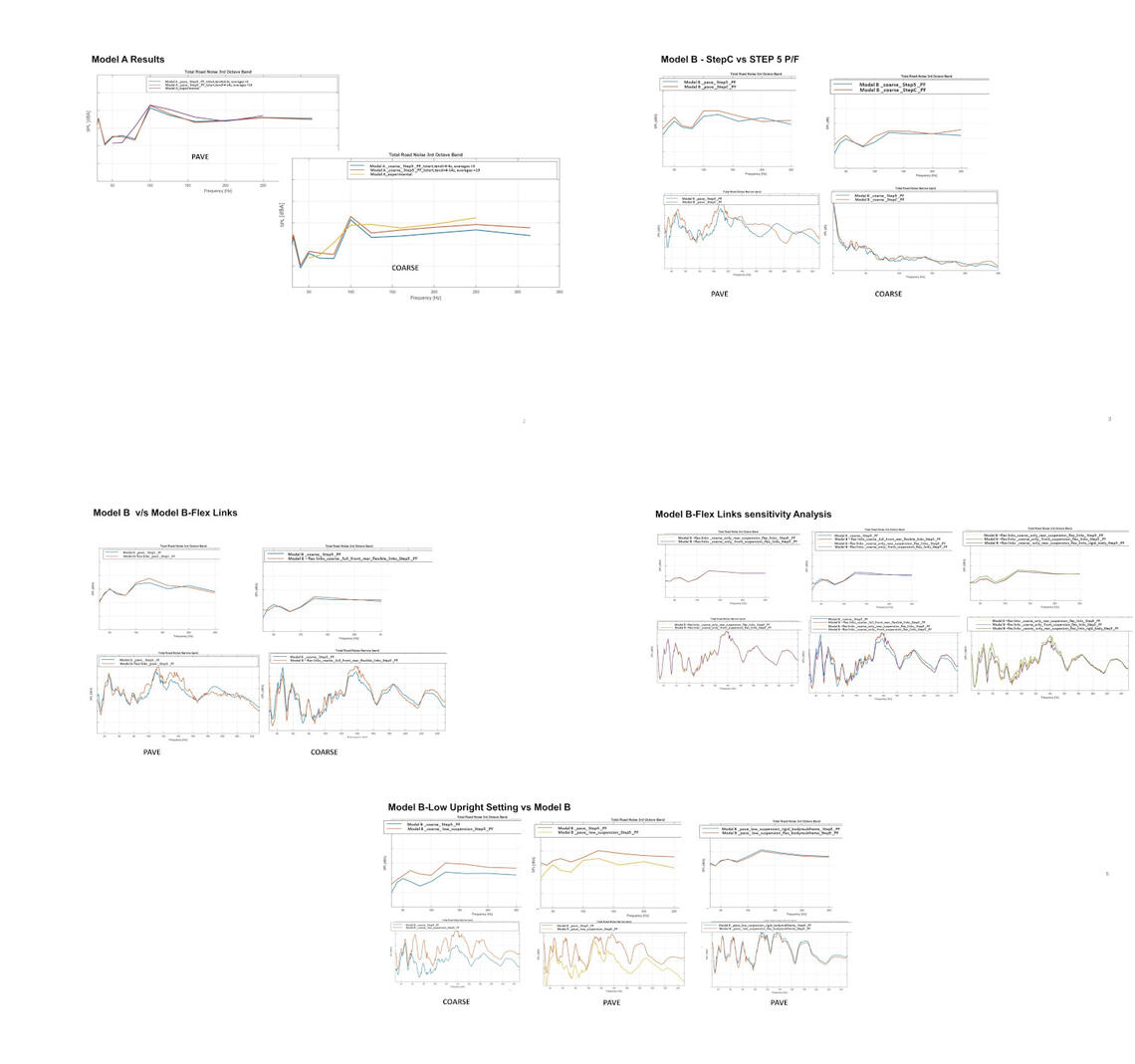
Author: Aqeab Sattar
Supervisor: Prof. Emiliano Mucchi
Company supervisors: Daniele Stanga, Antonio Scavone
Software Support: Daniel Catelani, Mauro Vesco