Un grupo mundial de fabricación de vehículos usa la técnica de escaneo con luz azul para mejorar la productividad
Mejores soluciones para la automoción
Contacto
Desde la introducción de la línea de ensamblado progresivo a principios del siglo XX, la industria de motores ha permanecido al frente del desarrollo industrial, acelerando los procesos e incrementando el rendimiento. Actualmente, más de cien años después, cada minuto sigue contando en el altamente competitivo mundo de la automoción.
Sin embargo, hoy en día la diferencia radica en que la seguridad y el control de calidad ya no son un lujo, sino una necesidad. Sin embargo, el tiempo invertido en el proceso de inspección tiene implicaciones de costo para los fabricantes y también para los consumidores. Como resultado, la industria de la automoción está buscando cada vez más proveedores de metrología que les ayude a mejorar la productividad.
Para un OEM líder en la automoción, cambiar a sistemas automatizados de escaneo con luz azul ha reducido en un 75% los tiempos de inspección y también ha mejorado la calidad de los datos obtenidos. La implementación de la solución WLS400A de Hexagon Manufacturing Intelligence ha acercado la inspección a la línea de producción, permitiendo una generación más rápida de informes de los problemas de calidad y reduciendo el ciclo de feedback. Como resultado, el impacto de las inspecciones en el rendimiento de la producción se minimiza y la efectividad de las mediciones de control se maximiza para asegurar la mejor calidad posible cuando los vehículos se pongan en marcha.
Efectivamente, la empresa tenía tres necesidades básicas para modernizar los departamentos de control de calidad y alcanzar la agilidad necesaria para una industria de tales dimensiones para reaccionar a la demanda del cliente sin comprometer su rendimiento:
El resultado fue la instalación de una serie de módulos de inspección cerca de la línea automatizada usando la solución de escaneo con luz azul de Hexagon Manufacturing Intelligence WLS400A.
La solución WLS400A de Hexagon Manufacturing Intelligence usa una tecnología de visión estéreo de rápida exposición digital para obtener datos dimensionales de alta precisión a partir de imágenes 2D y 3D. Con tres cámaras de 4.0 megapixeles, el escáner de luz azul tiene un campo visual de 500 mm x 500 mm, ofreciendo una superficie de cobertura de 250,000 mm2 en una sola toma. La iluminación LED azul de alto poder minimiza el impacto de los cambios en la luz ambiental. Para aplicaciones de automoción, la capacidad del escáner para medir superficies completas, características geométricas y bordes es muy importante debido a la diversa naturaleza de la carrocería del vehículo, además de que las tolerancias típicas de ± 0.5 mm para los tableros no representan problema alguno para un sistema de luz blanca.
Sin embargo, en la línea de ensamblado, la tecnología de escaneo en sí misma no es el único factor que hace una diferencia. Cuando es posible automatizar la inspección, los fabricantes obtienen ahorros de tiempo considerables. Los escáneres de luz azul se prestan para un uso robótico en un entorno industrial, debido a la distancia de trabajo que tienen, y el WLS400A está optimizado para integrarse con sistemas robóticos comunes para asegurar que las condiciones del taller no tengan efectos adversos en los resultados. La adquisición de datos toma solo 20 milisegundos, significativamente más rápido que los segundos necesarios por otros sensores de luz blanca, lo cual le otorga al WLS400A inmunidad a las vibraciones y condiciones de línea.
Para tres plantas europeas, se definió una serie de objetivos de gestión de funcionamiento que debían cumplirse. La atención se centró en la calidad de los dispositivos de cierre, asegurando que el ensamblado fuera sencillo y que la inspección de juegos y afloramientos resultara exitosa. Estas instalaciones también requerían de un elevado diseño de rendimiento que pudiera medir de forma eficiente todos los dispositivos de cierre producidos en cada vuelta. Como resultado, establecieron módulos usando dos robots. El primero cuenta con un escáner de luz azul, y el segundo tiene un dispositivo de sujeción para sostener la pieza que será medida.
En contraste, una planta en China decidió establecer dos módulos automáticos: uno para dispositivos de cierre y otro para el estampado de piezas de la carrocería lateral. Los módulos de dispositivos de cierre usan un escáner instalado en un robot sobre un riel deslizante con cuatro mesas giratorias alrededor para maximizar el uso del sistema de medición. Se usan dos mesas giratorias para inspeccionar las puertas, una para las tapas y otra para las ventanillas. Mientras se mide una pieza, es posible cargar la otra mesa giratoria, con barras de seguridad que aseguran que el operador no pueda acceder al área donde está trabajando el robot. El módulo de estampado de piezas usa solo dos mesas giratorias, cada una equipada con un dispositivo de sujeción para sujetar la parte lateral de la carrocería para la inspección.
Los módulos fueron diseñados y simulados en 3D para definir las mejores configuraciones y ubicaciones del equipo robótico y mecanismos de provisión. Después de la construcción, todos los diseños aprobaron una prueba de correlación MMC y las plantas estaban listas para medir con luz azul.
Una vez que se completa el proceso de medición, el sistema automáticamente genera informes visuales como mapas de colores, así como también los datos dimensionales. Esto ofrece la facilidad de referencia e interpretación que los operadores necesitan para reaccionar rápidamente ante los problemas. Las desviaciones del modelo se resaltan con colores cálidos sobre la imagen, por lo que las áreas en color rojo o naranja indican posibles problemas y deben ser revisadas. En caso de que ocurriera un problema, es posible analizar estas áreas usando técnicas más detalladas como el establecimiento de secciones transversales a partir del mismo conjunto de datos dimensionales.
Para este cliente, Hexagon Manufacturing Intelligence diseñó una variedad de informes personalizados, incluyendo la información general de la ‘imagen del día’, que se genera y distribuye a los equipos de gestión de producción y calidad diariamente e informa de las decisiones en el proceso de cierre. Una vez que se han medido varias piezas del mismo elemento, se comparan para identificar la estabilidad del proceso y la generación de resultados se presenta en mapas de colores para mostrar las desviación típica y el posicionamiento promedio en determinados puntos del objeto. También está disponible la información estadística, la cual satisface los exigentes requerimientos de gestión de funcionamiento de la empresa.
En promedio, el tiempo que invierte el fabricante automotriz en la inspección de calidad ha disminuido a tan solo una cuarta parte de lo invertido usando métodos tradicionales. Ya que la medición se encuentra más cerca de la línea de producción, el ciclo de feedback es más corto y las correcciones se pueden aplicar en menos tiempo. Pero quizás el impacto más sobresaliente está del lado del usuario, con diversas plantas informando que la información procesable proporcionada por CoreView agiliza la identificación de la causa del problema para el equipo. El resultado es un retorno de la inversión impresionantemente rápido gracias a la implementación de los sistemas de luz azul y una mayor productividad a través del proceso de control de calidad.
Sin embargo, hoy en día la diferencia radica en que la seguridad y el control de calidad ya no son un lujo, sino una necesidad. Sin embargo, el tiempo invertido en el proceso de inspección tiene implicaciones de costo para los fabricantes y también para los consumidores. Como resultado, la industria de la automoción está buscando cada vez más proveedores de metrología que les ayude a mejorar la productividad.
Para un OEM líder en la automoción, cambiar a sistemas automatizados de escaneo con luz azul ha reducido en un 75% los tiempos de inspección y también ha mejorado la calidad de los datos obtenidos. La implementación de la solución WLS400A de Hexagon Manufacturing Intelligence ha acercado la inspección a la línea de producción, permitiendo una generación más rápida de informes de los problemas de calidad y reduciendo el ciclo de feedback. Como resultado, el impacto de las inspecciones en el rendimiento de la producción se minimiza y la efectividad de las mediciones de control se maximiza para asegurar la mejor calidad posible cuando los vehículos se pongan en marcha.
Dejando atrás los métodos tradicionales de inspección
En el pasado, el fabricante usaba máquinas de coordenadas estacionarias para inspeccionar el estampado de piezas y los dispositivos de cierre. La medición de cada pieza generalmente tardaba cerca de dos horas, lo cual representaba una carga considerable para un grupo que producía aproximadamente 10 millones de vehículos anualmente. Los datos generados basados en puntos también podían ser difíciles de leer y analizar, y los tiempos de respuesta no eran lo suficientemente buenos para sincronizarlos de forma efectiva con la producción.Efectivamente, la empresa tenía tres necesidades básicas para modernizar los departamentos de control de calidad y alcanzar la agilidad necesaria para una industria de tales dimensiones para reaccionar a la demanda del cliente sin comprometer su rendimiento:
- Mejorar el nivel de uso y datos de calidad obtenidos
- Reducir el tiempo para garantizar la calidad del proceso de fabricación
- Reducir los costos del control de calidad dentro de la línea mientras se obtienen respuestas más rápidas
Identificación e implementación de cambios en el proceso
Con el apoyo de consultores de Hexagon Manufacturing Intelligence, la empresa mostró estos tres resultados deseados y se identificaron las mejoras al proceso necesarias para lograr dichos resultados. Para mejorar los niveles de calidad en el consejo de administración, se estableció que las fábricas requerían equipo que les permitiera medir más componentes y reunir los datos significativos para los usuarios para interpretarlos fácilmente y tomar decisiones basadas en ellos. Una planeación, medición y análisis más rápidos eran los medios centrales para reducir los tiempos para asegurar la calidad, en tanto que una indicación y un feedback más rápidos finalmente permitirían alcanzar el ahorro en los costos. A partir de la revisión del proceso, el equipo del proyecto decidió adquirir el equipo capaz de alcanzar estos cambios. Su conclusión fue migrar de una medición con MMC a un sistema de escaneo para obtener las ventajas de los datos necesarios, introducir la automatización para lograr ahorro de tiempo en todos los niveles desde la planeación hasta el análisis, y acercar el equipo a la línea de producción para reducir las implicaciones de los costos tanto de los errores de producción y del proceso de control de calidad en sí mismo.El resultado fue la instalación de una serie de módulos de inspección cerca de la línea automatizada usando la solución de escaneo con luz azul de Hexagon Manufacturing Intelligence WLS400A.
Ventajas del escaneo con luz azul
Existen diversas tecnologías y métodos que se pueden usar para medir e inspeccionar los componentes de una instalación industrial, cada uno con sus propias ventajas. Los sistemas de luz azul se encuentran entre las soluciones más rápidas y flexibles que están disponibles, lo que los convierte en una opción convincente para la inspección in-line y cerca de la línea de inspección de objetos de casi cualquier tamaño y complejidad.La solución WLS400A de Hexagon Manufacturing Intelligence usa una tecnología de visión estéreo de rápida exposición digital para obtener datos dimensionales de alta precisión a partir de imágenes 2D y 3D. Con tres cámaras de 4.0 megapixeles, el escáner de luz azul tiene un campo visual de 500 mm x 500 mm, ofreciendo una superficie de cobertura de 250,000 mm2 en una sola toma. La iluminación LED azul de alto poder minimiza el impacto de los cambios en la luz ambiental. Para aplicaciones de automoción, la capacidad del escáner para medir superficies completas, características geométricas y bordes es muy importante debido a la diversa naturaleza de la carrocería del vehículo, además de que las tolerancias típicas de ± 0.5 mm para los tableros no representan problema alguno para un sistema de luz blanca.
Sin embargo, en la línea de ensamblado, la tecnología de escaneo en sí misma no es el único factor que hace una diferencia. Cuando es posible automatizar la inspección, los fabricantes obtienen ahorros de tiempo considerables. Los escáneres de luz azul se prestan para un uso robótico en un entorno industrial, debido a la distancia de trabajo que tienen, y el WLS400A está optimizado para integrarse con sistemas robóticos comunes para asegurar que las condiciones del taller no tengan efectos adversos en los resultados. La adquisición de datos toma solo 20 milisegundos, significativamente más rápido que los segundos necesarios por otros sensores de luz blanca, lo cual le otorga al WLS400A inmunidad a las vibraciones y condiciones de línea.
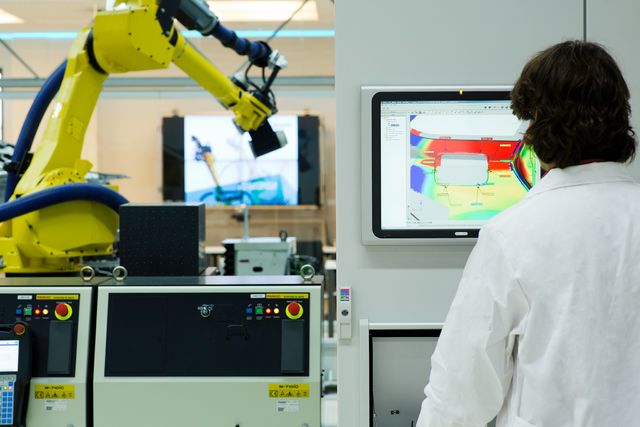
Aplicación y configuración en el grupo
La solución de tecnología y procesos fue definida, el fabricante de automotriz deseaba que se instalaran módulos de inspección en diferentes plantas de producción en todo el mundo. Con una configuración diferente en cada ubicación y con diversos modelos, cada uno con requerimientos distintos, Hexagon Manufacturing Intelligence aprovechó la flexibilidad de la tecnología de luz azul para recomendar diferentes configuraciones de módulos para el sistema WLS400A.Para tres plantas europeas, se definió una serie de objetivos de gestión de funcionamiento que debían cumplirse. La atención se centró en la calidad de los dispositivos de cierre, asegurando que el ensamblado fuera sencillo y que la inspección de juegos y afloramientos resultara exitosa. Estas instalaciones también requerían de un elevado diseño de rendimiento que pudiera medir de forma eficiente todos los dispositivos de cierre producidos en cada vuelta. Como resultado, establecieron módulos usando dos robots. El primero cuenta con un escáner de luz azul, y el segundo tiene un dispositivo de sujeción para sostener la pieza que será medida.
En contraste, una planta en China decidió establecer dos módulos automáticos: uno para dispositivos de cierre y otro para el estampado de piezas de la carrocería lateral. Los módulos de dispositivos de cierre usan un escáner instalado en un robot sobre un riel deslizante con cuatro mesas giratorias alrededor para maximizar el uso del sistema de medición. Se usan dos mesas giratorias para inspeccionar las puertas, una para las tapas y otra para las ventanillas. Mientras se mide una pieza, es posible cargar la otra mesa giratoria, con barras de seguridad que aseguran que el operador no pueda acceder al área donde está trabajando el robot. El módulo de estampado de piezas usa solo dos mesas giratorias, cada una equipada con un dispositivo de sujeción para sujetar la parte lateral de la carrocería para la inspección.
Los módulos fueron diseñados y simulados en 3D para definir las mejores configuraciones y ubicaciones del equipo robótico y mecanismos de provisión. Después de la construcción, todos los diseños aprobaron una prueba de correlación MMC y las plantas estaban listas para medir con luz azul.
Conversión de datos en información útil
La solución WLS400A se ejecuta en CoreView, un software especializado en metrología dimensional para el escaneo con luz azul. Aunque Hexagon Manufacturing Intelligence programó las rutinas iniciales, los propios empleados del fabricante ya están capacitados para la programación de nuevas piezas. El potencial de generación de información de CoreView es enorme, por lo que la estructura de generación de informes se diseñó nuevamente para satisfacer las normas y necesidades del fabricante.Una vez que se completa el proceso de medición, el sistema automáticamente genera informes visuales como mapas de colores, así como también los datos dimensionales. Esto ofrece la facilidad de referencia e interpretación que los operadores necesitan para reaccionar rápidamente ante los problemas. Las desviaciones del modelo se resaltan con colores cálidos sobre la imagen, por lo que las áreas en color rojo o naranja indican posibles problemas y deben ser revisadas. En caso de que ocurriera un problema, es posible analizar estas áreas usando técnicas más detalladas como el establecimiento de secciones transversales a partir del mismo conjunto de datos dimensionales.
Para este cliente, Hexagon Manufacturing Intelligence diseñó una variedad de informes personalizados, incluyendo la información general de la ‘imagen del día’, que se genera y distribuye a los equipos de gestión de producción y calidad diariamente e informa de las decisiones en el proceso de cierre. Una vez que se han medido varias piezas del mismo elemento, se comparan para identificar la estabilidad del proceso y la generación de resultados se presenta en mapas de colores para mostrar las desviación típica y el posicionamiento promedio en determinados puntos del objeto. También está disponible la información estadística, la cual satisface los exigentes requerimientos de gestión de funcionamiento de la empresa.
Mayor productividad en general
Para una implementación de tan gran escala que abarca fábricas en diversos continentes, los resultados comprobables y el retorno de la inversión eran de la mayor importancia. El sistema WLS400A mostró un impacto inmediato en los tiempos de medición. Por ejemplo, una unidad de puerta con 42 elementos cerrados, 427 puntos de superficie y 186 puntos de borde definidos (resultado de la digitalización de la puerta) ahora se pueden medir en menos de 20 minutos, comparados con dos horas usando el sistema MMC anterior. Una medición de una puerta típica tomará 10 minutos.En promedio, el tiempo que invierte el fabricante automotriz en la inspección de calidad ha disminuido a tan solo una cuarta parte de lo invertido usando métodos tradicionales. Ya que la medición se encuentra más cerca de la línea de producción, el ciclo de feedback es más corto y las correcciones se pueden aplicar en menos tiempo. Pero quizás el impacto más sobresaliente está del lado del usuario, con diversas plantas informando que la información procesable proporcionada por CoreView agiliza la identificación de la causa del problema para el equipo. El resultado es un retorno de la inversión impresionantemente rápido gracias a la implementación de los sistemas de luz azul y una mayor productividad a través del proceso de control de calidad.