Automatisch messen in serie
Kontakt

Längst Stand der Technik in der Einzelfertigung auf Bearbeitungszentren hält nun das Messen von Werkstücken mit Messtastern noch in der Maschine zunehmend Einzug auf Dreh- und Schleifmaschinen in der Serienfertigung. Ein kleiner britischer Zulieferbetrieb schildert seine Erfahrungen.
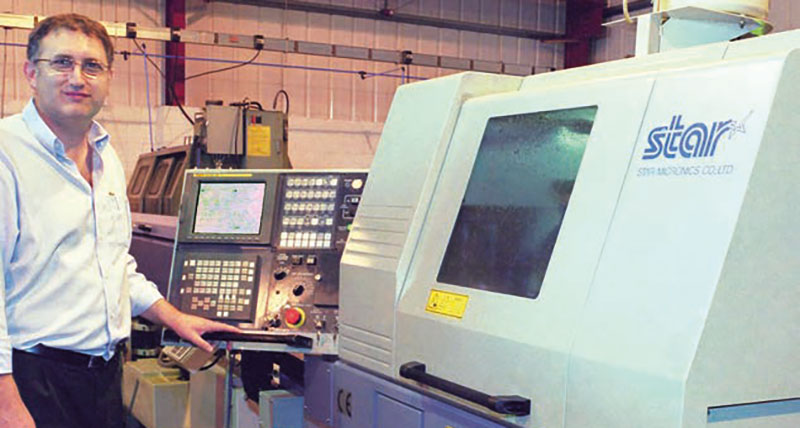
Deshalb hat man sich bei Davromatic zum Einsatz eines neuen, kabelgebundenen Messtastersystems 41.00-PP von m&h Inprocess Messtechnik GmbH, hergestellt im deutschen Waldburg, entschieden, das den Betreibern von Drehmaschinen mit einem beweglichen Spindelkopf erlaubt, gedrehte und gefräste Konturen noch in der Maschine, z.B. in der Gegenspindel, zu messen. Es dürfte sich dabei um das erste Echtzeit-Messsystem auf Drehmaschinen mit bewegtem Spindelkopf handeln, das mit einem kostengünstigen Standard-Messtaster für die Inprozess-Kontrolle kritischer Konturen an 100% der Teile realisiert wurde. Der Taster ist bei Davromatic auf einem Anschlagwinkel an passender, fester Position am Spindelstock, nahe der Hauptspindel montiert, so dass die abgetrennten Werkstücke von der Gegenspindel zum Messen der Dimensionen zum Messtaster hin bewegt werden können. Die erzielten Messergebnisse sind sehr verlässlich und weisen Genauigkeiten im μ-Bereich auf.
Im Lieferumfang seitens m&h befinden sich, neben dem Messtaster 41.00-PP selbst, auch die benötigten Schnittstellen zur Maschinensteuerung, direkt integriert in den Montagesockel. Auch Messzyklen, passend zur jeweiligen Steuerung, gehören selbstverständlich dazu. Auf Wunsch und gegen Aufpreis kann m&h auch die, auf die jeweiligen Teile bezogenen, Messprogramme liefern. So war es auch bei Davromatic der Fall.
Präzise Dreh-Frästeile mit einer Toleranz von +/- 8μ Die Tasteranordnung mit einem nahe des Spindelkopfes fest angebauten Messtaster kann auch an Maschinen mit festem Spindelkopf, an Stangenautomaten und an Zwei-Spindelmaschinen vorgenommen werden, wenn die Gegenspindel sowohl in X als auch in Z-Richtung verfahren kann, um das Werkstück zum Messtaster zu bewegen. Eine solche Ausrüstung wird sich vor allem bei Zulieferbetrieben durchsetzen, die sich mit der mannarmen Fertigung mittlerer und großer Serien von Komponenten hoher Komplexität bei gleichzeitig geforderter hoher Genauigkeit, also in engen Toleranzen, beschäftigen.
Bei Davromatic hat sich der zu bearbeitende Werkstoff als zusätzliche Hürde für eine zuverlässige und gleichmäßige Serienfertigung heraus gestellt. Der harte, aber zähe Werkstoff führt zu einem relativ unregelmäßigen, hohen Verschleiß der Wendeschneidplatten und damit zu stark schwankenden Standzeiten der Werkzeuge. Wie beim Hartdrehen und Hartfräsen verschleißen die Schneidplatten sehr schnell, sodass die gefertigten Teileabmessungen ebenso schnell außer Toleranz driften, was häufiges manuelles Eingreifen und Korrektur der Werkzeugdaten an der Steuerung erfordert, um die Serie innerhalb der geforderten Toleranzen zu halten. Dies bedeutet, neben der häufigen, manuellen Kontrolle, auch immer wieder Unterbrechungen der Produktion. Allein durch die Fähigkeit des m&h-Messtasters, alle Werkstücke permanent und automatisch im Fertigungsprozess auf der Maschine zu kontrollieren, ohne sie in die Hand nehmen zu müssen, und Verschleiß und Versatz automatisch in der Steuerung zu korrigieren, konnte die Ausbringung der Maschinen um 20 % erhöht werden. Das Messen senkt die Fertigungs-kosten, verbessert die Fertigungsgenauigkeit und vermindert den Ausschuss auf nahezu Null.
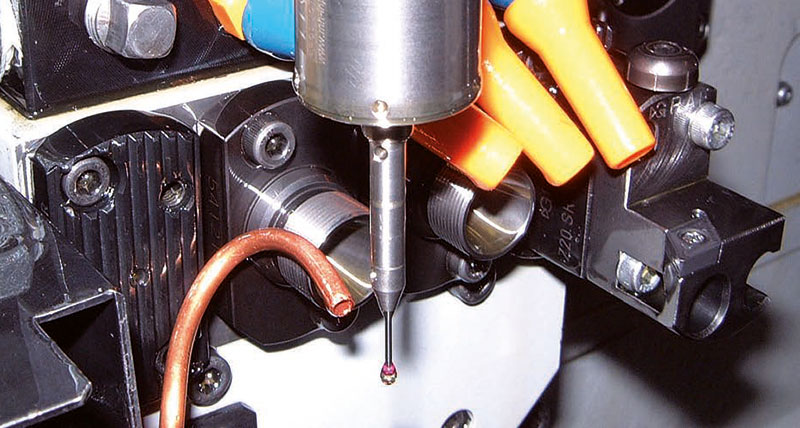
Für das Messen eines Außendurchmessers wird nur etwa 1 Sekunde benötigt. Werden mehrere Messungen kritischer Abmessungen, wie etwa Länge, Schlüsselweiten an Schraubflächen, gefräste Flächen oder ähnliches in den Messzyklus eingebunden, kann der Messvorgang dementsprechend wenig länger dauern. Üblicherweise wird der Messzyklus in das Programm für die Gegenspindel integriert, die ja unabhängig von den Bewegungen der Hauptspindel funktioniert. Deshalb geht in der Regel auch keine wertvolle Fertigungshauptzeit für das Messen verloren.
Als zusätzlicher Vorteil zeigt sich in diesem Anwendungsfall eine maßgebliche Reduktion des Aufwandes für die sonst häufigen Werkstückkontrollen parallel zur Serienfertigung. Sonst übliche Messvorrichtungen wurden gespart. Mannstunden für das Messen fallen nicht mehr an. Zusätzlich wurde der Ausschuss verringert, nicht zuletzt weil jetzt auch gelegentliches, vorzeitiges Versagen der Schneidplatten sofort erkannt wird. Insgesamt ergibt sich eine sehr schnelle Rückzahlung des Investments innerhalb von höchstens 3 Monaten!
Die Messtaster der Baureihe 41.00 sind unempfindlich gegen die nasse Umgebung in solchen Werkzeugmaschinen und werden deshalb auch in vielen Schleifmaschinen erfolgreich eingesetzt. Sie bestehen aus rostfreiem Stahl und verfügen in der, nach IP68 abgedichteten, Standardausführung bereits über Spänefang, Metall-Schutzlid und doppelte Dichtmembranen. Ihr Schraubgewinde der Größe M16 und die äußeren Abmessungen mit Durchmesser 25 mm machen sie absolut kompatibel zu vorhandenen Systemen anderer Hersteller, was ihren Ersatz auch in bestehenden Installationen erleichtert. Schließlich ist das Bessere der natürliche Feind des Guten.
Für Drehmaschinen mit fest stehenden Arbeitsspindeln hat m&h den neuen Messtaster 40.00-TX/RX mit Infrarot-Signalübertragung entwickelt, der wie ein normales Werkzeug in den Revolver eingesetzt wird. Somit kann nun auch auf herkömmlichen Drehmaschinen effizient, sicher und kostensparend produziert werden. Beide Systeme lassen sich jederzeit an vorhandenen Maschinen nachrüsten.