Wissenschaftler forschen mit 3D-Messtechnik nach Fertigungsmethoden für Metallbauteile
BIMAQ - Deutschland
Kontakt
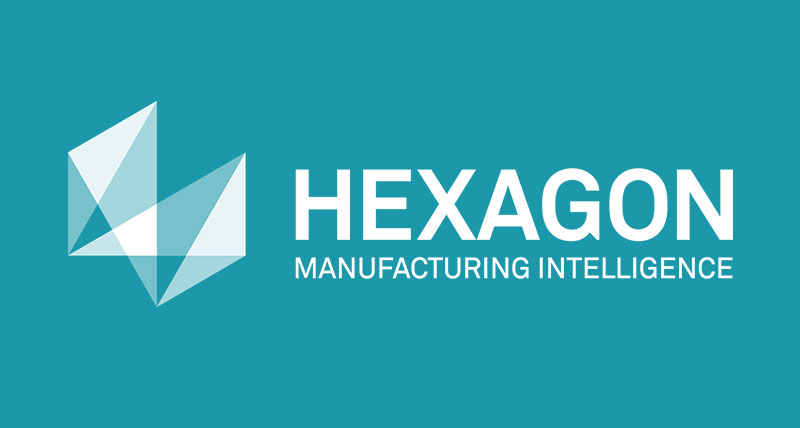
Gemeinhin gelten die Stadtmusikanten als Wahrzeichen von Bremen. Passionierte Ingenieure wissen jedoch: Distortion Engineering ist die neue Brand der Hansestadt. Geprägt hat diesen Begriff die Universität Bremen, die 2001 den gleichnamigen Sonderforschungsbereich 570 ins Leben gerufen hat, gefördert durch die Deutsche Forschungsgemeinschaft (DFG). Daran beteiligt ist das Bremer Institut für Messtechnik, Automatisierung und Qualitätswissenschaft (BIMAQ). Das Institut ist mit einer Leitz Reference den Gründen für Verzug an automobiltypischen Bauteilen auf der Spur. Ein weiteres Projekt des BIMAQ widmet sich der Windkraft: Zukünftig sollen Messungen von großvolumigen Getriebekomponenten wertvolle Informationen zur Fertigungsoptimierung liefern.
Ein gut ausgestattetes Messlabor kann das BIMAQ sein Eigen nennen. Im 160 m2 großen klimatisierten Messraum des Instituts finden sich hochpräzise Koordinaten-, Verzahnungsund Rauheitsmessgeräte jeglicher Couleur. Auch mehrere Messsysteme für die In-ProzessPrüfung und die zerstörungsfreie Randzonenanalyse mit taktilen, optischen, thermischen, magnetischen und akustischen Tastsystemen und Sensoren stehen im Dienst der Wissenschaft. Mittendrin eine Leitz Reference mit einem Messbereich von 1.000 x 700 x 600 mm und der Messsoftware QUINDOS 7.
Versuchsobjekte: automobiltypische Verzahnungen
Die Wissenschaftler nutzen das KMG, um Verzug an automobiltypischen Verzahnungen genauer unter die Lupe zu nehmen. „Seit 2001 besteht der Sonderforschungsbereich Distortion Engineering. Wir befinden uns jetzt in der letzten von drei Phasen und widmen uns nun den Verzahnungen“, sagt Institutsleiter Prof. Dr.-Ing. Gert Goch. „Wir gehen davon aus, dass Verzug das Ergebnis mehrerer ineinandergreifender Prozesse ist. Daher betrachten wir bei der Untersuchung der Verzahnungen die gesamte Produktionskette – also jeden Schritt von der Schmelze über das Weichverzahnen und das Härten bis hin zum Schleifen.“ Dazu messen die Wissenschaftler 1.800 Zahnräder, die jeweils einen Zustand im mehrstufigen Fertigungsprozess markieren. Sie stammen alle vom gleichen Stahlstrang, sie weisen alle einen Durchmesser von 120 mm und eine Bohrung mit einem Durchmesser von 45 mm auf. Das Institut für Werkstofftechnik unterstützt das BIMAQ bei dem Vorhaben. Es verfügt über das notwendige Equipment und Know-how, um diese Zahnräder herzustellen. Die „Geschichte“ der Räder wird fein säuberlich dokumentiert und in einer Datenbank festgehalten. Auf diese Weise können die Mitarbeiter im Messlabor später genau nachvollziehen, an welchem Punkt in der Fertigung Verzug auftritt.
„Entsprechend den Versuchsplänen messen wir die Zahnräder möglichst umfassend und genau“, sagt Martina Fuhrmann, wissenschaftliche Mitarbeiterin am BIMAQ. Pro Sekunde sammelt die Leitz Reference 750 Messpunkte, die volumetrische Längenmessabweichung des Koordinatenmessgerätes liegt bei 0,9 + L/350 μm – gute Voraussetzungen für das Vorhaben der Wissenschaftler. „Wir nehmen eine große Zahl von Messpunkten an den Zahnrädern mittels High-Speed-Scanning auf. An allen Zähnen messen wir 9 x 3 Linien, um die Topographie der Zahnflanken darzustellen. Akribisch gehen wir auch bei der Stirnseite des Zahnrades vor. Am Ende erhalten wir eine vollständige Beschreibung des Objektes. Mit den Messpunkten nehmen wir eine möglichst umfangreiche Auswertung vor und bestimmen so Abweichungen und Verzug. In einem weiteren Schritt können wir dann auch neue Strategien für die Fertigung und Messung von Verzahnungen entwickeln.“
Zukunftsvision: stabilere Getriebekomponenten für die Windkraft
Während das Projekt noch in der Anfangsphase steckt, stößt das Team mit der Leitz Reference bereits in neue, vielversprechende Gefilde vor. Enormes Potenzial für Verbesserungen liefert die Fertigung von Großgetrieben für Windenergieanlagen. Die Anlagen sind auf eine Betriebszeit von 20 Jahren ausgelegt. Die meisten Getriebe müssen jedoch früher, einige schon nach etwa sechs Jahren ausgetauscht werden. Ersatzteile sind zudem schwer zu beschaffen. Die Auftragsbücher der Hersteller sind zum Zerbersten voll, die Lieferzeiten von Ersatzteilen entsprechend lang.
Anlagenbetreiber treten daher bereits mit Anfragen zu Lohnmessungen an das Institut heran. „Steht das Planetenrad eines Getriebes im Verdacht, Unregelmäßigkeiten zu verursachen, sind wir am Zug. An die Konstruktionszeichnungen kommt man nicht heran. Um also die Konstruktion des Planetenrades nachzuempfinden, bleibt den Anlagenbetreibern nur klassisches Reverse Engineering. Mit der Leitz Reference und der Messsoftware QUINDOS 7, die sich speziell für Verzahnungen eignet, können wir Komponenten bis zu einem bestimmten Durchmesser messen.“ An einem Planetenrad mit einem Durchmesser von 530 mm hat das BIMAQ bewiesen, dass es das Messen unbekannter Geometrien meistert. Das Rad wies Fressstellen auf und musste so schnell wie möglich ersetzt werden. Mit der Leitz Reference und der Messsoftware QUINDOS 7 haben die Mitarbeiter des BIMAQ verschiedene Parameter wie Teilkreisdurchmesser, Profilform, Eingriffs- und Schrägungswinkel gemessen und damit auf die Geometrie des Zahnrades geschlossen.
Die Anlagenbetreiber drängen aufgrund der enormen Wartungskosten darauf, die Qualität der Getriebe zu verbessern und so die Schadenshäufigkeit zu minimieren. Für das BIMAQ stellen sich die folgenden Fragen: Wie kann man bei großen Zylinderrädern sinnvolle Messungen unter Industrieaspekten durchführen, die eine Vorhersage über die Funktionseigenschaften und die Lebensdauer des Zahnrades zulassen? Wo liegen die Fehlerquellen, die später zu Schäden führen – neben Verzug? Und welche Maßnahmen müssen ergriffen werden, damit Hersteller von Großgetrieben den Fertigungsprozess beherrschen und verbessern können? Antworten soll in Zukunft ein Koordinatenmessgerät der Reihe Leitz PMM-F mit einem Messbereich von 2.500 x 2.000 x 700 liefern, das auf die Messung großvolumiger Komponenten ausgelegt ist.
Hochgenaue Informationsquelle: Leitz PMM-F
„Sobald die neue Maschine im Messraum steht, kann es auch mit dem Windkraft-Projekt richtig losgehen“, sagt Prof. Goch. „Hexagon Metrology hat ein Konzept ausgearbeitet, das zu unseren Bedürfnissen passt. Die neue Maschine soll in den Boden versenkt werden. So befindet sich der Messtisch auf gleichem Niveau wie der Fussboden. Die Komponenten aus den Windkraftanlagen werden über eine Rampe angeliefert und dann mit einem Luftkissenfahrzeug bis zur Leitz PMM-F transportiert. Das Handling der Komponenten ist dadurch sehr einfach.“ Auch bei der Messung der Windkraftkomponenten mit der Leitz PMM-F möchte das BIMAQ die gleiche Messstrategie verfolgen: Zahnradsätze, die die gesamte Produktionskette repräsentieren, sollen vollständig gemessen werden. Periodisch auftretende Geometrieabweichungen wie Rundlauffehler und Teilungsfehler werden den Wissenschaftlern wertvolle Informationen liefern.
Rückschlüsse auf die Ursachen für Beschädigungen und Ausfälle von Windkraftanlagen lassen sich jedoch nur in Kombination mit Informationen ziehen, die von Sensoren in den Anlagen herrühren. Die Sensoren messen in der Windkraftanlage den Zustand verschiedener physikalischer Größen wie z. B. Schwingungen. Aussagekräftig genug sind diese Informationen nicht. Notwendig wären Sensoren, die über Jahrzehnte hinweg dynamische Kräfte, Spannungen und Momente messen können. Bei der Optimierung dieser Sensoren ist das BIMAQ mit am Ball. Vieles gibt es also zu tun. Mit Leitz Koordinatenmessgeräten packt es das BIMAQ an.