Leica Absolute Tracker AT901 überwacht Zuschnitt von Windkraft-Stativen
HGG Profiling Equipment - Niederlande
Kontakt

Weltweit erledigen HGG-Maschinen zahlreiche Schneideaufgaben. HGG, 1984 gegründet, ist der weltweit einzige Anbieter, der auf das Schneiden von Stahlprofilen spezialisiert ist und sowohl maßgeschneiderte Maschinen als auch Anwendungs-Know-how auf höchstem Standard anbietet. HGG verkauft die Maschinen an Kunden in den Bereichen Offshore, Stahlbau, Rohrleitungen, Schiffsbau und auch in andere Industrien.
HGGProfilmaschinen stehen für Qualitätsschnitte gemäss neuester Normen (ISO 9013), leichte Bedienung und Programmierung sowie industriespezifische Anpassung und Langlebigkeit. HGG stellt Schrägschneidemaschinen her, die sich für die Bearbeitung besonders großer Werkstücke eignen. „Wir mögen Herausforderungen“, sagt Peter Tool, der Entwicklungschef von HGG. „Unsere größte Stärke ist, dass wir unsere Anlagen inklusive Software von Grund auf selbst entwickeln – so bleiben wir flexibel. Dank kurzer Wege können wir uns in kurzer Zeit vollkommen neuartige Verfahren ausdenken“, so Tool weiter.
HGG installierte die neue Schneidemaschine in der Produktionshalle von EEW im norddeutschen Rostock. Auf einem 8 m hohen Podest überwacht der Leica Absolute Tracker die Bewegung der Schneidemaschine und des aufgespannten Rohrs. Die Umgebungsbedingungen, denen das Messsystem ausgesetzt ist, sind schwierig. Die extreme Grösse und das Gewicht der Bauteile sorgen häufig für Vibrationen. Peter Tool: „Der Tracker verkraftet das ohne Probleme. Auch der Staub, der beim Schneiden entsteht, stört die Messungen nicht. Wir hatten schon eine Staubschicht von mehreren Millimetern in den Reflektoren und sie haben immer noch einwandfrei funktioniert.“
HGGProfilmaschinen stehen für Qualitätsschnitte gemäss neuester Normen (ISO 9013), leichte Bedienung und Programmierung sowie industriespezifische Anpassung und Langlebigkeit. HGG stellt Schrägschneidemaschinen her, die sich für die Bearbeitung besonders großer Werkstücke eignen. „Wir mögen Herausforderungen“, sagt Peter Tool, der Entwicklungschef von HGG. „Unsere größte Stärke ist, dass wir unsere Anlagen inklusive Software von Grund auf selbst entwickeln – so bleiben wir flexibel. Dank kurzer Wege können wir uns in kurzer Zeit vollkommen neuartige Verfahren ausdenken“, so Tool weiter.
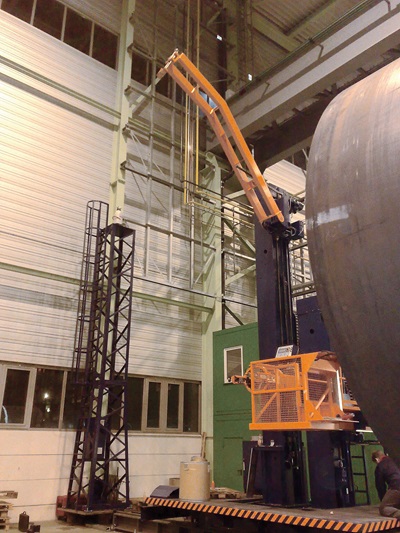
Messtechnik: Der Schlüssel zum Erfolg
Der deutsche Hersteller von Komponenten für Windanlagen EEW erteilte einen Auftrag an HGG. Für eine Offshore-Windkraftanlage plante EEW, Gründungen, sogenannte Tripods, aus hochwertigem Stahl herzustellen. Zylindrische Elemente aus 400 t schweren, 60 m langen und 6 m hohen Stahlrohren in 3D präzise zu schneiden war die Aufgabe. HGG erkannte anhand dieser Eckdaten, dass die richtige Messtechnik der Schlüssel zum Erfolg des Projekts wird. Ein Rohr, das 400 t wiegt, deformiert sich auf einer Maschine schon wegen seines eigenen Gewichts. Diese Deformation verändert den Durchmesser eines Rohrs um bis zu 20 mm und führt zu unerwünschtem Driften. Allerdings verändert sich der Durchmesser nicht konstant, wenn das Rohr auf der Schneidemaschine rotiert – die Ovalität ändert sich während der Bewegung. Ein 60 m langes aufgespanntes Rohr hängt ausserdem in der Mitte mehrere cm durch. Die Schneidemaschine selbst verändert wegen des extremen Gewichts ebenfalls ihre Struktur. Angesichts solcher Deformationen liefert selbst die genaueste Maschine keine sauberen Schnitte. „Ein Rohr kostet 100.000 €“, erklärt Peter Tool. „Bei derart teurem Material darf kein Verarbeitungsfehler passieren.“ Tool und sein Team beschlossen daher, ein Messsystem in die Schneidemaschine zu integrieren. Distanzen erreicht, da eine Hauptvoraussetzung war, das Messinstrument in Front des Rohres zu platzieren.Kein teurer Ausschuss
Die zentrale Idee: Die Benutzer sollen jederzeit die relative Position des Rohrs im Vergleich zur Schneidemaschine kennen. Wenn die genauen Koordinaten des Rohrs auf der Maschine und seine Deformation bekannt sind, ist eine Korrektur der Bewegung des Schneidekopfs jederzeit möglich. Teurer Ausschuss entsteht nicht. Peter Tool fand schnell ein geeignetes Kontrollverfahren. Auf das Potenzial von Laser Trackern war er schon früher auf einer Messe aufmerksam geworden, und für die Dimensionen des EEW-Projekts waren die Reichweiten der LaserMesstechnik alternativlos. HGG entschied sich, den Leica Absolute Tracker an die Schneidemaschine zu koppeln: Nur dieses System garantierte die geforderten Genauigkeiten und ausreichende Messdistanzen für 60 m lange Rohre – das typische Messvolumen des Leica Absolute Tracker liegt sogar bei 160 m. Kein anderer Laser Tracker hätte die gewünschte Genauigkeit und die grossenLaser Tracker überwacht Schneidekopf und Werkstück
„Wir hatten von Anfang an ein Ziel: Die Maschine soll von einer einzigen Person bedienbar sein“, sagt Peter Tool. Deshalb integrierte HGG den Leica Absolute Tracker vollständig in die Schneidemaschine – deren Anwender muss nicht wissen, wie man den Laser Tracker bedient. Der Tracker verfolgt mehrere Reflektoren auf dem Schneidekopf und dem Rohr. Jeder Abschnitt des Rohrs ist mit einem Reflektor versehen – dadurch weiss der Bediener der Schneidemaschinen, wie sich das Rohr biegt. Alle 100 Millisekunden liefert der Laser Tracker die Koordinaten eines Punktes. Die Software der Schneidemaschine steuert auch den Tracker – das Programmier-Interface emScon von Leica Geosystems macht es möglich.HGG installierte die neue Schneidemaschine in der Produktionshalle von EEW im norddeutschen Rostock. Auf einem 8 m hohen Podest überwacht der Leica Absolute Tracker die Bewegung der Schneidemaschine und des aufgespannten Rohrs. Die Umgebungsbedingungen, denen das Messsystem ausgesetzt ist, sind schwierig. Die extreme Grösse und das Gewicht der Bauteile sorgen häufig für Vibrationen. Peter Tool: „Der Tracker verkraftet das ohne Probleme. Auch der Staub, der beim Schneiden entsteht, stört die Messungen nicht. Wir hatten schon eine Staubschicht von mehreren Millimetern in den Reflektoren und sie haben immer noch einwandfrei funktioniert.“
