Führender flugzeughersteller nutzt seit mehr als 15 jahren gelenkarme
Dassault Aviation - Frankreich
Kontakt

Als großer, finanziell abgesicherter, internationaler Privatkonzern mit Standorten in mehr als 70 Ländern auf fünf Kontinenten, arbeitet Dassault Aviation schon seit seiner Gründung im Jahr 1936 gewinnbringend. Dassault Aviation ist so strukturiert, dass seine Produktion an die Marktzyklen angepasst werden kann, und kooperiert mit einem umfangreichen Netzwerk von Hightech-Unternehmen in Frankreich, Europa, den USA und anderen Ländern auf der ganzen Welt.
Rafale, Falcon, Mirage 2000, Super Etendard, Alfajet… Diese Namen sind Ikonen der zivilen und militärischen französischen Luftfahrtgeschichte, die nach dem Zweiten Weltkrieg mit der Firmengründung durch Marcel Dassault begann. Im Laufe der Jahre gelang es Dassault, sich einen verdienten Platz unter den führenden Flugzeugherstellern der Welt zu erwerben. Das Unternehmen verfügt über die größte Anzahl unterschiedlicher Flugzeugdesigns der Branche.
Aufgrund seiner Konstruktionsabteilungen, Produktions– stätten, der Kompetenz seiner Mitarbeiter und seiner starken Produktlinien kann Dassault Aviation seinen Kunden von der Entwicklung bis zum Betrieb exzellentes Know-how bieten, das auf soliden unterneh-merischen Werten basiert. In Bezug auf technologische Innovation und Fachwissen im Bereich Luftfahrt spielt Dassault Aviation eine absolute Vorreiterrolle. Die Gruppe hat es sich zum Ziel gesetzt, ihren Kunden innovative und kosteneffiziente Lösungen anzubieten. Durch den technischen Fortschritt hat sich das Flugzeugkonzept sowohl in der zivilen als auch in der militärischen Luftfahrt zu einem komplexen System entwickelt.
Weltweit sind heute nur wenige Unternehmen in der Lage, solche Systeme zu fertigen, da zur Integration und Koordination eine enorme fachliche Kompetenz von der Konstruktion über die Produktion bis zum Support erforderlich ist. Der Systemintegrator muss über extrem breit gefächerte Fähigkeiten verfügen, um allen technischen und finanziellen Aspekten einer solchen Aufgabe gerecht werden zu können. Gleichzeitig muss er die mit der Integration der Komponenten verbundenen Risiken einschätzen können.
Die CAD/CAM-Abteilung von Dassault, die sich am Flughafen Bordeaux-Merignac befindet, entwickelt und prüft Werkzeugkonzept, Werkzeugsteuerung und Nachrüstungen. Diese von Jacky Blasquez geleitete Abteilung ist der Produktion zugeordnet und spielt bei allen Projekten von Dassault eine wichtige Rolle. Blasquez begann seine Karriere vor 32 Jahren als Werkzeugmacher und arbeitete sich zum technischen Zeichner hoch. Vor der Übernahme der Leitung der Konstruktion und Fertigung stand er an der Spitze mehrerer anderer Abteilungen. “Am Anfang arbeiteten wir vor allem von Hand. Später verwendeten wir die CADAM und CATIA Software zum Zeichnen von Oberflächen und Rohren. Auch die Messgeräte waren damals sehr einfach: Theodoliten, Lote und Lineale. 3D-Messungen mussten wir von einem externen Partner durchführen lassen. Schon Ende der achtziger Jahre erwarb unsere Tochterfirma in Argenteuil ihren ersten Romer Gelenkarm, den wir uns bei Bedarf ausliehen. 1992 erhielten wir endlich einen eigenen Romer Arm, der unmittelbar in den Rohrbiegeprozess integriert wurde und nun seit mehr als 15 Jahren täglich im Einsatz ist. Die Anschaffung unseres zweiten Romer Gelenkarms erfolgte 2004. Schnell wurde er zu unserem wichtigsten Mess-instrument.”
Dassault verwendet den Gelenkarm häufig. Besonders gerne wird mit dem G-Scan Scanner gearbeitet, der mit sehr hohen Genauigkeiten Tausende von Punkten pro Sekunde erfassen kann. Dies gilt auch für die G-Tube Software mit ihrem Zubehör für Rohmessungen. “Romer deckt 100 Prozent unseres Messbedarfs ab”, erklärt Blasquez und fährt fort: “Ein besonderes Lob gebührt dem Kundendienst, der sehr kompetent und bestens erreichbar ist. Wir erhalten immer hilfreiche Antworten auf unsere Fragen.” Dassault hat einen Spezialwagen zum Transport des Arms innerhalb des Werksgeländes gebaut. So kann beispielsweise auch die Außenhaut oder der Innenraum eines Flugzeugs überprüft werden. Außerdem hat das Unternehmen eine eigene Armverlängerung konstruiert, mit der Flugzeuginnenräume in einem einzigen Arbeitsschritt gemessen werden können. Derzeit wird noch an einer weiteren Verlängerung getüftelt, mit welcher der Arm über dem Flugzeug positioniert werden soll, sodass innerhalb eines Messvorgangs noch mehr Punkte erreicht werden können. Zur Messung der Flugzeugunterseite muss der Gelenkarm auf den Kopf gestellt werden, doch das tut der Qualität der Messdaten keinerlei Abbruch.
Ein Beispiel für die zahlreichen anspruchsvollen Aufgaben ist die Messung der Triebwerksabdeckung eines Falcon- Strahltriebwerks, das von einer kanadischen Dassault- Tochter geliefert wird. Die Abdeckung besitzt eine hochglänzende Oberfläche. Dadurch sind Fehler sogar mit freiem Auge sichtbar. Durch einen kurzen Scanvorgang können diese Fehler geortet werden, sodass die Werkzeuge und Vorrichtungen entsprechend verändert werden können.
Derartige Teileprüfungen sind in der Abteilung an der Tagesordnung. Doch mit dem Produktionsstart der Rafale und der Falcon 7FX ergaben sich neue Herausforderungen in der Produktion. Für die Fertigung dieser beiden Flugzeuge hat Dassault ein neues integriertes digitales Netzwerk eingeführt. Mit der Falcon F7X wurde hinsichtlich Life Cycle Management ein neuer Standard geschaffen. Die digitalisierten Daten werden innerhalb des Produktionsstandorts häufig ausgetauscht. Dadurch kommt der Inspektion mit dem Romer Gelenkarm sowohl in Bezug auf die Werkzeug- als auch die Teileprüfung ein sehr hoher Stellenwert zu. Das fertige Flugzeug muss den CAD-Werten entsprechen. Probleme bei der Montage können mit dem Gelenkarm schnell beseitigt werden, da die Prüfung direkt während des Montagevorgangs erfolgt, was Korrekturen vereinfacht. Die Ergebnisse sind äußerst aussagekräftig und bieten keinen Raum für Fehlinterpretationen. Beispielsweise war es in der Vergangenheit recht schwierig, die Position der Innenverkleidung auf ihre Richtigkeit zu prüfen. Heute werden Referenzpunkte geprüft und ein Protokoll erstellt und sofort ist klar, wo der Fehler liegt. Dieses neue Verfahren ermöglicht Dassault eine erhebliche Reduktion der Prüfzeiten und damit eine Steigerung der Produktivität.
Auch bei verschiedensten Arten von Rohrfertigungsprozessen spielen Romer Gelenkarme eine entscheidende Rolle. Die CAD-Entwurfs- und Fertigungsabteilung unter der Leitung von Jacky Blasquez digitalisiert die Rohre und erstellt 3D-Modelle. Bei neueren Rohrtypen können Fehler leicht erkannt werden, da 3D-Daten für den Abgleich mit den gefertigten Rohren existieren. Für ältere Rohrtypen müssen erst mittels Reverse Engineering 3D-Modelle generiert werden.
Die breite Palette möglicher Anwendungen für den Romer Gelenkarm erlauben Dassault die Nutzung des Arms weit über den Standort Merignac hinaus. Vor einiger Zeit besuchte Jacky Blasquez das Werk in Little Rock, Arkansas, wo er mit Hilfe des Gelenkarms komplexe Werkzeugsysteme prüfte und justierte, die sich außerhalb der Toleranzen befanden. Bei dieser Gelegenheit stattete er auch gleich einer Militärbasis einen Besuch ab. Dort nutzte er den Arm zum Reverse-Engineering eines komplizierten Bauteils, das anschließend nachgebaut und montiert wurde, ohne dass noch irgendwelche Änderungen an der Passgenauigkeit vorgenommen werden mussten. Gleichzeitig wurden die Kosten für den Nachbau erheblich gesenkt.
Der Romer Gelenkarm hilft auch bei der Wiederinstandsetzung historischer Flugzeuge. Regelmäßig wird er in Flugzeugmuseen zur Digitalisierung von Komponenten eingesetzt. Anhand dieser Daten werden Ersatzteile gefertigt, die längst nicht mehr anderweitig erhältlich sind. Wundern Sie sich also nicht, wenn Sie Jacky Blasquez mit seinem Romer Arm in einem Museum treffen. Wahrscheinlich wartet ein Kunde bereits ungeduldig auf ein Ersatzteil für sein historisches Flugzeug. Häufig können derartige Kostbarkeiten nur durch das Reverse Engineering von Bauteilen wieder zu neuem Leben erweckt werden.
”Mit unserem Gelenkarm gelingt es uns immer, die erforderlichen Toleranzen einzuhalten. Der Reverse- Engineering-Prozess erfolgt einfach, effektiv und präzise”, zeigt sich Jacky Blasquez zufrieden. In seinen Augen gibt es nur ein Problem: ”Leider kennen zu wenige Kollegen dieses praktische Instrument. Ich bin sicher, dass unser Romer Arm in Zukunft noch häufiger eingesetzt wird.”
Rafale, Falcon, Mirage 2000, Super Etendard, Alfajet… Diese Namen sind Ikonen der zivilen und militärischen französischen Luftfahrtgeschichte, die nach dem Zweiten Weltkrieg mit der Firmengründung durch Marcel Dassault begann. Im Laufe der Jahre gelang es Dassault, sich einen verdienten Platz unter den führenden Flugzeugherstellern der Welt zu erwerben. Das Unternehmen verfügt über die größte Anzahl unterschiedlicher Flugzeugdesigns der Branche.
Aufgrund seiner Konstruktionsabteilungen, Produktions– stätten, der Kompetenz seiner Mitarbeiter und seiner starken Produktlinien kann Dassault Aviation seinen Kunden von der Entwicklung bis zum Betrieb exzellentes Know-how bieten, das auf soliden unterneh-merischen Werten basiert. In Bezug auf technologische Innovation und Fachwissen im Bereich Luftfahrt spielt Dassault Aviation eine absolute Vorreiterrolle. Die Gruppe hat es sich zum Ziel gesetzt, ihren Kunden innovative und kosteneffiziente Lösungen anzubieten. Durch den technischen Fortschritt hat sich das Flugzeugkonzept sowohl in der zivilen als auch in der militärischen Luftfahrt zu einem komplexen System entwickelt.
Weltweit sind heute nur wenige Unternehmen in der Lage, solche Systeme zu fertigen, da zur Integration und Koordination eine enorme fachliche Kompetenz von der Konstruktion über die Produktion bis zum Support erforderlich ist. Der Systemintegrator muss über extrem breit gefächerte Fähigkeiten verfügen, um allen technischen und finanziellen Aspekten einer solchen Aufgabe gerecht werden zu können. Gleichzeitig muss er die mit der Integration der Komponenten verbundenen Risiken einschätzen können.
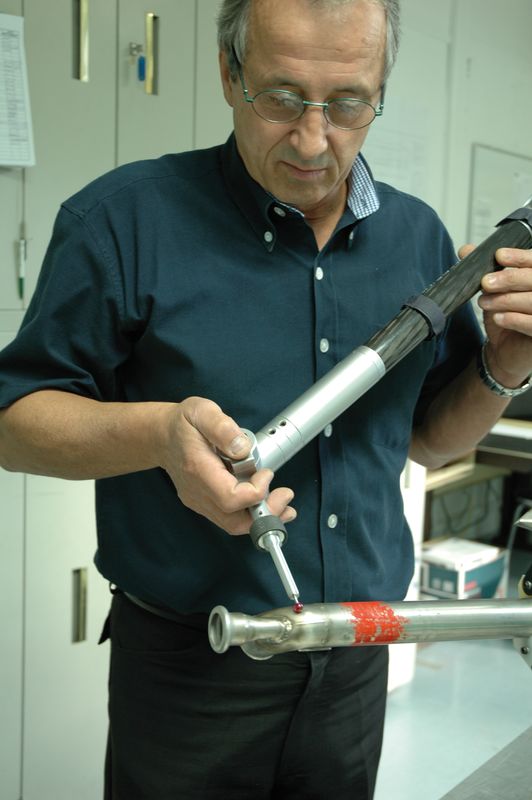
Dassault verwendet den Gelenkarm häufig. Besonders gerne wird mit dem G-Scan Scanner gearbeitet, der mit sehr hohen Genauigkeiten Tausende von Punkten pro Sekunde erfassen kann. Dies gilt auch für die G-Tube Software mit ihrem Zubehör für Rohmessungen. “Romer deckt 100 Prozent unseres Messbedarfs ab”, erklärt Blasquez und fährt fort: “Ein besonderes Lob gebührt dem Kundendienst, der sehr kompetent und bestens erreichbar ist. Wir erhalten immer hilfreiche Antworten auf unsere Fragen.” Dassault hat einen Spezialwagen zum Transport des Arms innerhalb des Werksgeländes gebaut. So kann beispielsweise auch die Außenhaut oder der Innenraum eines Flugzeugs überprüft werden. Außerdem hat das Unternehmen eine eigene Armverlängerung konstruiert, mit der Flugzeuginnenräume in einem einzigen Arbeitsschritt gemessen werden können. Derzeit wird noch an einer weiteren Verlängerung getüftelt, mit welcher der Arm über dem Flugzeug positioniert werden soll, sodass innerhalb eines Messvorgangs noch mehr Punkte erreicht werden können. Zur Messung der Flugzeugunterseite muss der Gelenkarm auf den Kopf gestellt werden, doch das tut der Qualität der Messdaten keinerlei Abbruch.
Ein Beispiel für die zahlreichen anspruchsvollen Aufgaben ist die Messung der Triebwerksabdeckung eines Falcon- Strahltriebwerks, das von einer kanadischen Dassault- Tochter geliefert wird. Die Abdeckung besitzt eine hochglänzende Oberfläche. Dadurch sind Fehler sogar mit freiem Auge sichtbar. Durch einen kurzen Scanvorgang können diese Fehler geortet werden, sodass die Werkzeuge und Vorrichtungen entsprechend verändert werden können.
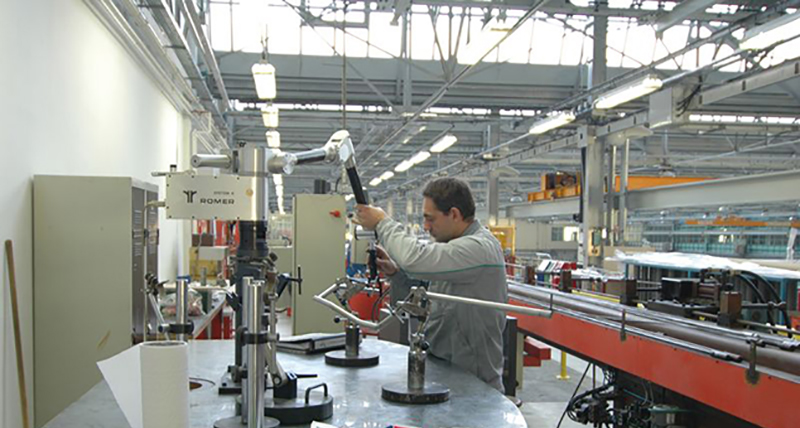
Auch bei verschiedensten Arten von Rohrfertigungsprozessen spielen Romer Gelenkarme eine entscheidende Rolle. Die CAD-Entwurfs- und Fertigungsabteilung unter der Leitung von Jacky Blasquez digitalisiert die Rohre und erstellt 3D-Modelle. Bei neueren Rohrtypen können Fehler leicht erkannt werden, da 3D-Daten für den Abgleich mit den gefertigten Rohren existieren. Für ältere Rohrtypen müssen erst mittels Reverse Engineering 3D-Modelle generiert werden.
Die breite Palette möglicher Anwendungen für den Romer Gelenkarm erlauben Dassault die Nutzung des Arms weit über den Standort Merignac hinaus. Vor einiger Zeit besuchte Jacky Blasquez das Werk in Little Rock, Arkansas, wo er mit Hilfe des Gelenkarms komplexe Werkzeugsysteme prüfte und justierte, die sich außerhalb der Toleranzen befanden. Bei dieser Gelegenheit stattete er auch gleich einer Militärbasis einen Besuch ab. Dort nutzte er den Arm zum Reverse-Engineering eines komplizierten Bauteils, das anschließend nachgebaut und montiert wurde, ohne dass noch irgendwelche Änderungen an der Passgenauigkeit vorgenommen werden mussten. Gleichzeitig wurden die Kosten für den Nachbau erheblich gesenkt.
Der Romer Gelenkarm hilft auch bei der Wiederinstandsetzung historischer Flugzeuge. Regelmäßig wird er in Flugzeugmuseen zur Digitalisierung von Komponenten eingesetzt. Anhand dieser Daten werden Ersatzteile gefertigt, die längst nicht mehr anderweitig erhältlich sind. Wundern Sie sich also nicht, wenn Sie Jacky Blasquez mit seinem Romer Arm in einem Museum treffen. Wahrscheinlich wartet ein Kunde bereits ungeduldig auf ein Ersatzteil für sein historisches Flugzeug. Häufig können derartige Kostbarkeiten nur durch das Reverse Engineering von Bauteilen wieder zu neuem Leben erweckt werden.
”Mit unserem Gelenkarm gelingt es uns immer, die erforderlichen Toleranzen einzuhalten. Der Reverse- Engineering-Prozess erfolgt einfach, effektiv und präzise”, zeigt sich Jacky Blasquez zufrieden. In seinen Augen gibt es nur ein Problem: ”Leider kennen zu wenige Kollegen dieses praktische Instrument. Ich bin sicher, dass unser Romer Arm in Zukunft noch häufiger eingesetzt wird.”