간단한 콘트라스트 타겟에 직접 스캐닝하여 기존 산업 공정에 맞추기
조선업에 계측 등급 검사를 지원하기 위한 저비용 흑백 타겟의 실현 가능성 입증

준공(As-Built) 문서는 공식 설치 문서가 필수인 대다수의 산업 응용 분야의 요구 사항 중 하나로 조선업 또한 예외는 아닙니다. 정확한 검사는 선박이 제조 공정의 사소한 편차로 인해 구부러지 않고 똑바로 서는 데 필수이며, 이러한 검사에는 선박과 같은 대형 스케일을 처리할 수 있는 신뢰도 높은 검증이 필요합니다.
지상 레이저 스캐너는 건설 부문에 적합한 대형 포인트 클라우드를 제공하는, 이는 업계에서 문서화 목적으로 널리 사용하는 솔루션입니다. 그러나 이러한 장치도 조선 부문에서 필요로 하는 적절한 치수 검증을 수행하기에는 정확도가 다소 떨어집니다.
헥사곤의 엔지니어들은 다수의 업계 전문가와 논의를 가진 후 조선 공정의 고정밀 검사에 기존 방식인 반구형 지상 스캐너 문서화 프로세스와 Leica Absolute Tracker ATS600을 하나의 시스템으로 함께 사용하는 방법을 모색하기 시작했습니다.
이 개념은 ATS600 레이저 트래커의 고유한 직접 스캐닝 기능을 기반으로 하며, 측정 포인트에 타겟이 있지 않아도 최대 60m 거리에서 계측 등급의 정확도로 표면 포인트를 측정할 수 있습니다.
선박 건조에는 패널을 용접하여 하위 어셈블리를 만든 다음 용접하여 모듈을 형성하는 공정이 있습니다. 이 서로 다른 모듈들을 다 같이 용접하면 전체 선박이 만들어집니다. 이 과정에서는 선박이 똑바로 서는 것이 중요한데 현재는 이 모듈 또는 전체 선박의 최종 상태를 문서화하는 데 지상 레이저 스캐너를 주로 사용하고 있습니다. 그러나 지상 레이저 스캐너는 ATS600만큼 계측 등급 정확도가 높지 않기 때문에 검증된 품질 검사 및 보고에 사용하기 적합하지 않습니다.
헥사곤은 이러한 공정의 특성을 이해한 다음 ATS600의 직접 스캐닝 기능과 업계에서 치수 등록에 일반적으로 사용하는 간단한 콘트라스트 타겟을 결합하는 솔루션을 제안했습니다. ATS600은 기존 레이저 트래커 스타일의 반사경까지 측정할 수 있지만(모든 유형의 지상파 스캐너로는 불가능함) 반사경은 고가이므로 업계가 받아들일 수 있는 대안이 될 가능성은 낮습니다.
그래서 전문가들은 ATS600으로 측정할 수 있는 간단하고 저렴한 흑백 콘트라스트 타겟을 제시해야 했고 동시에 목표 측정 정확도 수준을 허용오차 1mm 이내로 유지해야 했습니다.
Leica GZT21 흑백 타겟은 ATS600의 반사경을 대체할 수 있는 저비용 제품으로, 1mm 이내의 정확도를 달성했습니다. 이를 위해 세 가지 테스트를 실시했습니다. 첫 번째는 타겟 회전을 다르게 한 5m, 10m 및 20m에서의 반복성 테스트, 두 번째는 다섯 가지 트래커 위치에서 다섯 가지 콘트라스트 타겟에 가장 적합한 정렬 찾기, 세 번째는 비교를 위해 동일한 트래커 위치에서 다섯 개의 1.5인치 적색 반사경(RRR)의 가장 적합한 정렬 찾기입니다.
헥사곤의 SpatialAnalyzer 소프트웨어는 자동으로 타겟의 중심점을 추출하고 스캔 경사도를 조정하여 타겟의 포인트가 균일하게 분포되도록 하는 기능을 제공합니다. 최고 정확도와 균등하게 분포된 포인트 간격을 얻으려면 45도 각도로 타겟을 스캔하는 것이 좋습니다.
테스트 결과에 따르면 반사경 측정이 확실히 더 정확하지만 Leica GZT21 흑백 타겟까지의 측정은 모든 측정 위치에서 균일한 허용오차 내에 있음을 보여주었습니다. 이는 ATS600의 직접 스캐닝 기능과 공통 타겟을 함께 사용하여 정확한 등록을 수행하면 저렴한 비용에 높은 정확도로 정확한 포인트 클라우드를 달성할 수 있다는 헥사곤의 제안이 유효한 옵션임을 입증합니다. 즉, Leica GZT21 흑백 타겟은 기존 레이저 트래커 반사경을 위한 저비용 대체안인 것입니다.
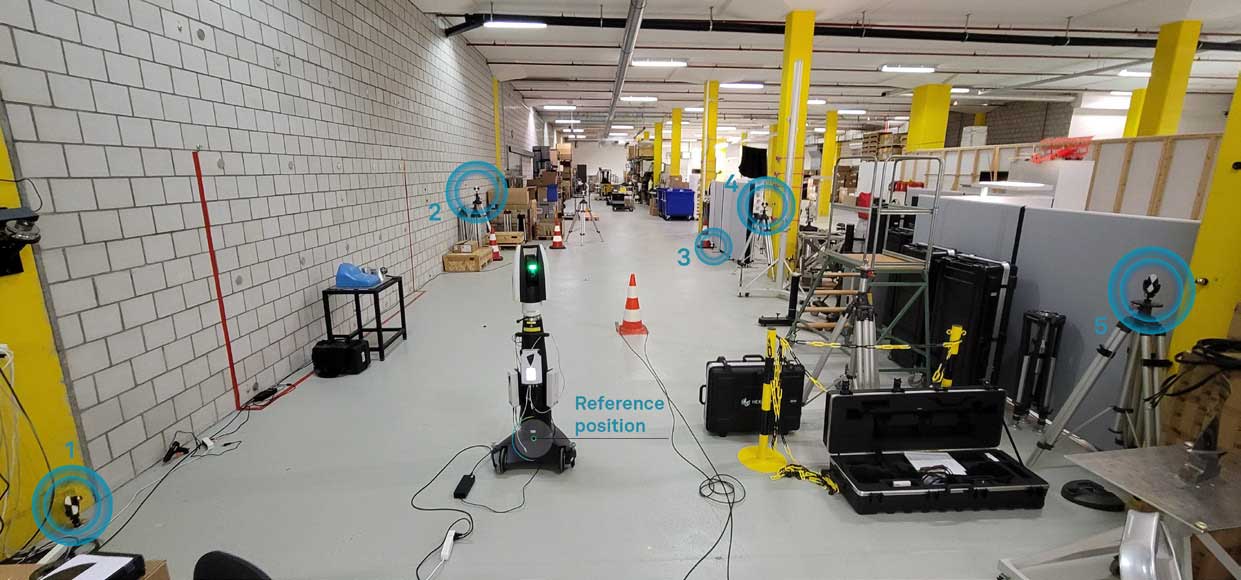
이 솔루션은 선박 건조 시 준공 문서화를 용이하게 하는 동시에 현재의 공정 표준을 크게 변경하지 않아도 검사 작업의 정확성을 보장해 줍니다.
조선 검사 및 문서화 프로세스의 일환으로 구축된 ATS600을 어셈블리 프로세스에서 직접적으로 사용하면 더 많은 기능을 제 공할 수 있습니다. 빌드 모드에서 트래커를 사용하면 시스템의 라이브 DRO를 사용하여 부품을 지정된 위치로 유도한 후 지금 의 수동 프로세스보다 훨씬 더 높은 신뢰성으로 해당 위치에 용 접할 수 있습니다.
지상 레이저 스캐너는 건설 부문에 적합한 대형 포인트 클라우드를 제공하는, 이는 업계에서 문서화 목적으로 널리 사용하는 솔루션입니다. 그러나 이러한 장치도 조선 부문에서 필요로 하는 적절한 치수 검증을 수행하기에는 정확도가 다소 떨어집니다.

이 개념은 ATS600 레이저 트래커의 고유한 직접 스캐닝 기능을 기반으로 하며, 측정 포인트에 타겟이 있지 않아도 최대 60m 거리에서 계측 등급의 정확도로 표면 포인트를 측정할 수 있습니다.
선박 건조에는 패널을 용접하여 하위 어셈블리를 만든 다음 용접하여 모듈을 형성하는 공정이 있습니다. 이 서로 다른 모듈들을 다 같이 용접하면 전체 선박이 만들어집니다. 이 과정에서는 선박이 똑바로 서는 것이 중요한데 현재는 이 모듈 또는 전체 선박의 최종 상태를 문서화하는 데 지상 레이저 스캐너를 주로 사용하고 있습니다. 그러나 지상 레이저 스캐너는 ATS600만큼 계측 등급 정확도가 높지 않기 때문에 검증된 품질 검사 및 보고에 사용하기 적합하지 않습니다.
헥사곤은 이러한 공정의 특성을 이해한 다음 ATS600의 직접 스캐닝 기능과 업계에서 치수 등록에 일반적으로 사용하는 간단한 콘트라스트 타겟을 결합하는 솔루션을 제안했습니다. ATS600은 기존 레이저 트래커 스타일의 반사경까지 측정할 수 있지만(모든 유형의 지상파 스캐너로는 불가능함) 반사경은 고가이므로 업계가 받아들일 수 있는 대안이 될 가능성은 낮습니다.
그래서 전문가들은 ATS600으로 측정할 수 있는 간단하고 저렴한 흑백 콘트라스트 타겟을 제시해야 했고 동시에 목표 측정 정확도 수준을 허용오차 1mm 이내로 유지해야 했습니다.
Leica GZT21 흑백 타겟은 ATS600의 반사경을 대체할 수 있는 저비용 제품으로, 1mm 이내의 정확도를 달성했습니다. 이를 위해 세 가지 테스트를 실시했습니다. 첫 번째는 타겟 회전을 다르게 한 5m, 10m 및 20m에서의 반복성 테스트, 두 번째는 다섯 가지 트래커 위치에서 다섯 가지 콘트라스트 타겟에 가장 적합한 정렬 찾기, 세 번째는 비교를 위해 동일한 트래커 위치에서 다섯 개의 1.5인치 적색 반사경(RRR)의 가장 적합한 정렬 찾기입니다.
헥사곤의 SpatialAnalyzer 소프트웨어는 자동으로 타겟의 중심점을 추출하고 스캔 경사도를 조정하여 타겟의 포인트가 균일하게 분포되도록 하는 기능을 제공합니다. 최고 정확도와 균등하게 분포된 포인트 간격을 얻으려면 45도 각도로 타겟을 스캔하는 것이 좋습니다.
테스트 결과에 따르면 반사경 측정이 확실히 더 정확하지만 Leica GZT21 흑백 타겟까지의 측정은 모든 측정 위치에서 균일한 허용오차 내에 있음을 보여주었습니다. 이는 ATS600의 직접 스캐닝 기능과 공통 타겟을 함께 사용하여 정확한 등록을 수행하면 저렴한 비용에 높은 정확도로 정확한 포인트 클라우드를 달성할 수 있다는 헥사곤의 제안이 유효한 옵션임을 입증합니다. 즉, Leica GZT21 흑백 타겟은 기존 레이저 트래커 반사경을 위한 저비용 대체안인 것입니다.
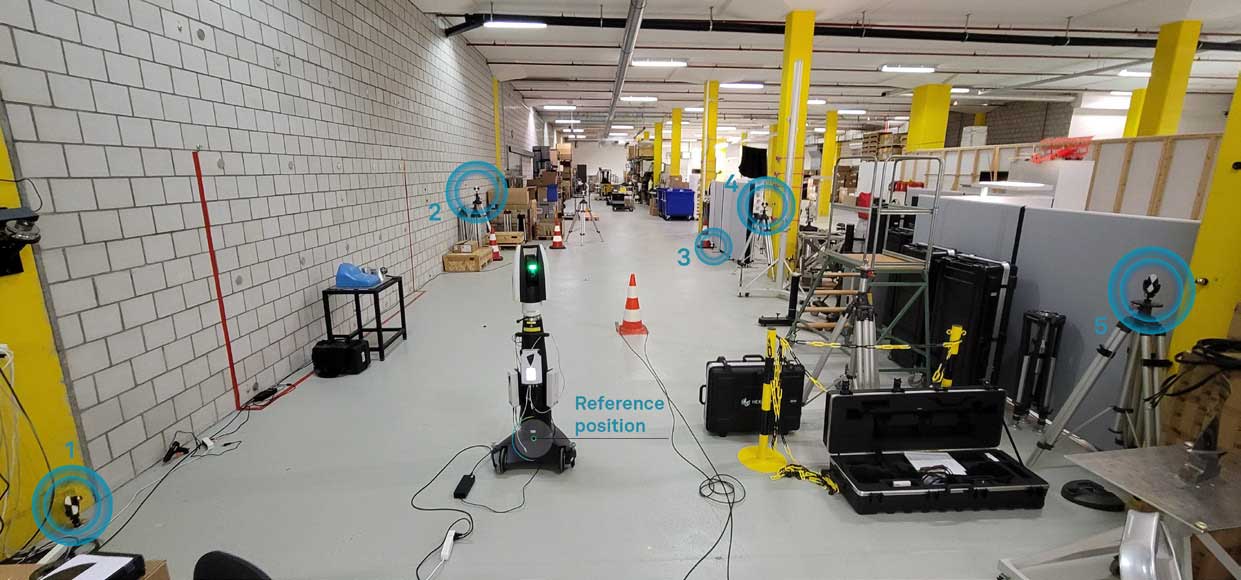
이 솔루션은 선박 건조 시 준공 문서화를 용이하게 하는 동시에 현재의 공정 표준을 크게 변경하지 않아도 검사 작업의 정확성을 보장해 줍니다.
조선 검사 및 문서화 프로세스의 일환으로 구축된 ATS600을 어셈블리 프로세스에서 직접적으로 사용하면 더 많은 기능을 제 공할 수 있습니다. 빌드 모드에서 트래커를 사용하면 시스템의 라이브 DRO를 사용하여 부품을 지정된 위치로 유도한 후 지금 의 수동 프로세스보다 훨씬 더 높은 신뢰성으로 해당 위치에 용 접할 수 있습니다.
다양한 거리에서 실시한 반복성 테스트 결과 - 위치 및 목표 회전당 20회 수행.
적합성 – 측정 위치 대비 참조 위치.