Come l'analisi dei dati di tomografie computerizzate consente a TE Connectivity di raggiungere il suo obiettivo finale
Di Alexander Stokowski, TE Connectivity
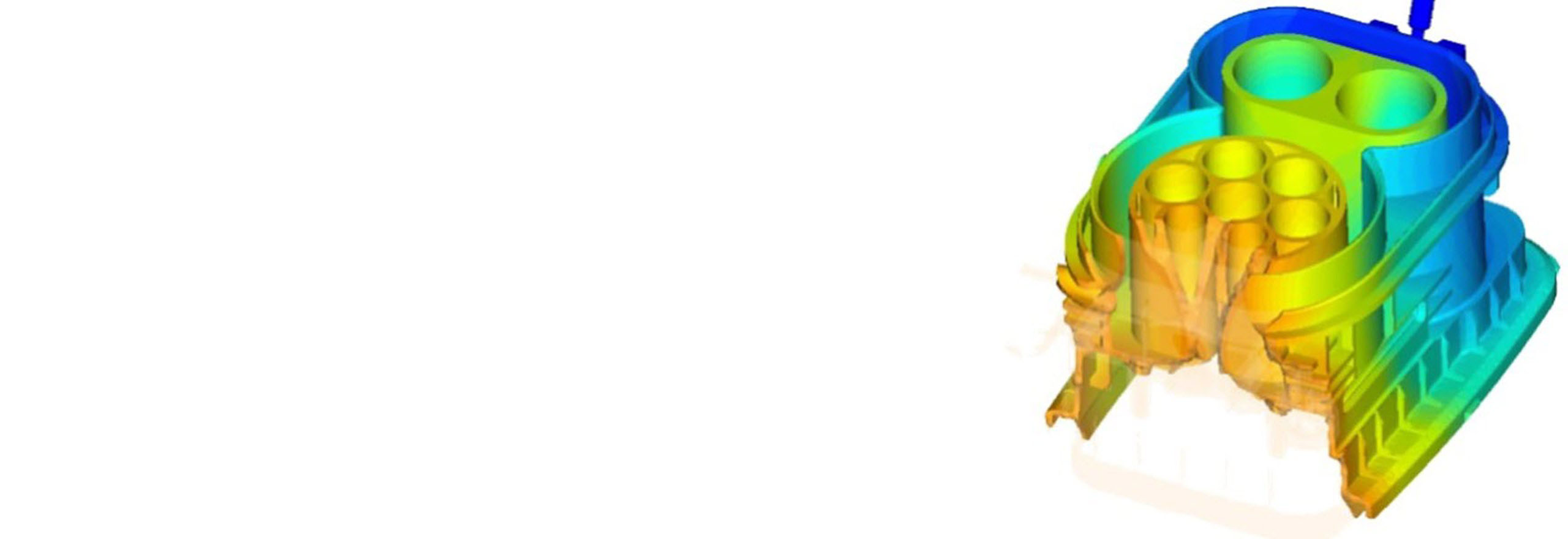
Engineering Reality 2024 Volume 1
Accelerare la produzione intelligente
L'azienda acquisisce informazioni di importanza critica utilizzando il software Volume Graphics durante la progettazione, la simulazione e la produzione.
La tendenza alla digitalizzazione si sta affermando tra le aziende che cercano maggiore automazione, connettività e affidabilità dai loro modelli e dalle loro macchine. I sondaggi condotti dal Manufacturing Leadership Council e da altri enti mostrano consistenti investimenti e importanti risultati derivanti dalla Produzione 4.0 e dalle relative iniziative di progettazione e produzione digitale. L’implementazione di un contesto operativo digitale affidabile garantisce una maggiore velocità, profondità e agilità nella creazione e nella gestione dei dati dei prodotti.
Figura 1. La simulazione consente di tenere sotto controllo la qualità fin dalle prime fasi, prevedendo il comportamento dei materiali e testando i parametri di progettazione. Una scansione tomografica di questa presa per auto elettrica permette di informare la simulazione rispetto alle nuove variazioni e distorsioni dovute alla produzione. Immagine per gentile concessione di TE Connectivity.
Per quanto i vantaggi delle piattaforme digitali interconnesse siano sorprendenti anche per le discipline CAD/CAE/CAM tradizionali, l'analisi dei dati di tomografia computerizzata (CT Scan) per il controllo qualità ha ampliato notevolmente la sua portata e il suo scopo nell'attuale panorama digitale in crescita. La sua nuova influenza sugli strumenti di progettazione, simulazione e produzione è significativa: il software di analisi dei dati di una tomografia sta rendendo questi strumenti, solitamente utilizzati a monte, ancora più efficienti nel loro ruolo.
Feedback dall'analisi tomografica sulla progettazione e sulla produzione
L'istituzione del metodo MBD (Model-Based Definition) guida sempre più l'ingegneria oltre ai disegni e agli approcci ibridi. Il passaggio dalla lettura manuale dei dati alla MBD crea flussi di informazioni più approfonditi e ampi durante tutto lo sviluppo del prodotto, dai file PMI (Product Manufacturing Information) alle macchine e ad altri programmi.
Non sono solo le annotazioni geometriche e le istruzioni di produzione a viaggiare su flussi digitali. Le aziende stanno creando canali di informazione per la progettazione, la simulazione e i test virtuali che migliorano l'accuratezza, la conformità alle specifiche e accorciano i tempi di produzione.
Questi nuovi cicli di sviluppo rinforzano una tendenza quarantennale che punta a un processo decisionale sempre più precoce e una riduzione dei casi in cui la validazione dei prodotti e dei metodi di produzione viene fatta in fase avanzata.
Definizione degli standard per il controllo qualità
È logico che un'azienda impegnata in soluzioni di connettività e rilevamento per veicoli elettrici, aeromobili, fabbriche digitali intelligenti, energia eolica e solare, cobot, IoT, connettività ad alta velocità e altro ancora investa in MBD e metodi di verifica avanzati. Con l'obiettivo dichiarato di contribuire alla realizzazione di una trasformazione tecnologica basata su prodotti elettronici affidabili e duraturi, TE Connectivity punta molto sulla qualità dei propri prodotti.
Questo percorso "ingegnerizzato" mette a confronto i vantaggi degli standard ISO Geometric Product Specification (GPS) e della metrologia virtuale con i limiti dell'utilizzo dei classici flussi di progettazione. I vecchi flussi di lavoro utilizzano disegni, sistemi digitali 2D e 3D e, sebbene siano meno complessi dell'MBD, possono spesso perdere informazioni durante le conversioni dei modelli e richiedono una programmazione manuale particolarmente impegnativa per la creazione di programmi di controllo qualità.
"Il GPS è l'unico modo per costruire veri sistemi basati su modelli e definizioni matematiche esatte", afferma Alexander Stokowski, responsabile sviluppo di TE Connectivity. Stokowski, certificato Six Sigma Black Belt e docente di tecnologia di misura e GPS presso l'Università Statale Cooperativa del Baden-Württemberg (DHBW), è impegnato da un decennio nella trasformazione digitale.
"Il GPS è importante per ricavare l'asse centrale del pezzo, per ottenere una direzione di misura di 90 gradi, per rilevare i punti - e se non si è precisi dal punto di vista matematico non si può realisticamente creare, né tanto meno automatizzare, un sistema di misura", afferma Stokowski.
Per Stokowski e TE Connectivity, il percorso verso la conformità MBD e GPS e l'integrazione con l'analisi dei dati tomografici è iniziato nella divisione prodotti automobilistici intorno al 2012. È così che sono iniziati i primi progetti pilota. "Alla fine del 2013, due anni dopo l'avvio", racconta Stokowski, "abbiamo più o meno preso la decisione di introdurre tutto ciò che riguardava lo sviluppo di nuovi prodotti nell'ambiente di misura attraverso tomografie computerizzate, con l'obiettivo di raggiungere una percentuale del 100%."
Figura 2A. (Sinistra) Campione stampato di un corpo combinato di presa di carica ad alta potenza precedentemente testato nel software Moldflow. Immagine 2B. (Destra) Modello CAD della presa con annotazioni di qualità PMI che elencano le tolleranze. Non è necessaria alcuna conversione dati da Creo; il PMI CAD dettagliato è importato in automatico direttamente in VGMETROLOGY. Immagine per gentile concessione di TE Connectivity.
Questa decisione innovativa, presa in anticipo rispetto all'implementazione dei nuovi standard ISO nel settore, ha dato vita a una stretta e intensa collaborazione tra PTC (Creo), TE Connectivity e Volume Graphics (VG) per creare un'integrazione intorno alle nuove funzionalità GPS conformi agli standard ISO.
L'integrazione completa e multi-fornitore ha consentito un maggiore utilizzo di annotazioni basate su modelli e PMI, portando a un ciclo di test virtuali e risultati di misura reali nella progettazione e nella simulazione di stampi, e poi nella prototipazione, nella verifica del primo articolo (FAI) e nella produzione.
Figura 3: Flusso di lavoro di qualità virtuale e fisico: (L-R) progettazione del pezzo e definizione delle misure di qualità; generazione di eventuali report digitali e feedback di simulazione per la progettazione; visualizzazione e valutazione del pezzo da PMI; utilizzo dell'IA all'interno dei programmi di simulazione e scansione per ottimizzare i parametri; scansione TC dei pezzi campione per verificare le deviazioni del mondo reale. Post-progettazione: preparare macro di verifica in linea, scansionare, analizzare e valutare. Post-produzione: analizzare le parti realizzate e fornire un feedback sulla progettazione, con conseguente miglioramento continuo. Immagine per gentile concessione di TE Connectivity.
"Abbiamo lasciato tutti sorpresi implementando gli standard molto prima delle date di rilascio finali", afferma Stokowski. "Perché aspettare 3-5 anni quando le indicazioni, come ad esempio la visualizzazione delle annotazioni 3D, sono già chiare nelle bozze ISO?
"Gli STEP 214 e 242 non hanno funzionato per la nostra integrazione", afferma Stokowski. "Abbiamo utilizzato l'interfaccia di programmazione dell'applicazione (API) del toolkit Creo e ISO-GPS per stabilire la nostra interfaccia diretta con i software VGMETROLOGLY e VGSTUDIOMAX. Ci sono funzionalità particolari aggiunte e personalizzate che ci consentono di riutilizzare i valori derivati da FAI. E il risultato è: funzionalità di Geometric Dimension & Tolerance (GD&T) di Creo e VGMETROLOGY, insieme all'integrazione di VARIMOS di SIMCON. Non sono necessari altri software per collegare la progettazione e la simulazione con il controllo qualità."
Il primo obiettivo del programma di misura digitale di TE Connectivity era di garantire che i componenti progettati corrispondessero ai componenti effettivamente prodotti. Nella maggior parte dei casi ciò significa lavorare con prodotti stampati con normali problemi di tolleranza al centraggio nell'utensile e con i tipici segni di espulsione e piccoli difetti. La simulazione degli stampi e la misura virtuale consentono di identificare e risolvere sia gli aspetti funzionali che quelli estetici della produzione di stampi e parti in plastica. FAI genera un ciclo di feedback in cui il modello 3D e la simulazione, lo stampo e il pezzo prodotto sono compatibili e uniformati con poche o nessuna discrepanza. Da qui vengono creati modelli di qualità dal software Volume Graphics per l'ispezione automatizzata.
"Dieci o quindici anni fa i progettisti non dedicavano molto tempo a esaminare i particolari che uscivano dallo stampo", afferma Stokowski. "E gran parte di questo problema è già stato risolto grazie al software dedicato agli utensili e al ciclo di automazione che stiamo creando. Tutti i dati sono disponibili per essere visualizzati e utilizzati rapidamente dai nostri team interdisciplinari."
Ritorno sull'investimento (ROI)
Il valore complessivo della qualità non è oggetto di discussione. La qualità costruisce il brand, attrae i clienti e riduce i costi legati alle richieste di garanzia, alla manodopera e alla revisione dei processi e dei metodi di progettazione volti a trovare la causa principale di problemi imprevisti.
D'altro canto, i responsabili finanziari spesso mettono in discussione tutti gli investimenti operativi tranne quelli essenziali e si accontentano di uno status quo redditizio. I tecnici possono trovare frustrante l'adattamento di sistemi nuovi e ancora più complessi rispetto ai programmi precedenti. Investire, apprendere e implementare aggiornamenti della qualità può mettere a dura prova un'organizzazione in molti modi.
"Il vero valore della qualità per TE Connectivity è il tempo che risparmiamo", afferma Stokowski. "Il tempo e il valore che i clienti attribuiscono a prodotti durevoli, affidabili e di qualità superiore.
"Qual è il valore di quattro-sei settimane di tempo di sviluppo risparmiate in fase di progettazione e potenzialmente guadagnate in fase di spedizione?", si chiede Stokowski. "Come si calcola il costo dei macchinari e del software? Non ci sono risposte esatte", afferma. "Ma abbiamo un Centro di eccellenza (CoE) che collabora con i clienti, forma il nostro personale e crea la nostra infrastruttura di qualità che contribuisce all'innovazione. Questa è un valore in sé".
Figura 4. Centralina motore auto (ECU) con 200 pin di collegamento elettrico. Si tratta della prima parte di prova nell'ambito dello sforzo di TE Connectivity di automatizzare il controllo qualità. Foto per gentile concessione di TE Connectivity.
Risparmio di tempo e prima centralina motore
"Puntiamo a una tempistica di dieci giorni per la progettazione, la simulazione, la scansione e la produzione di un rapporto di misura digitale", afferma Stokowski. "Ora ci sono molte cose da fare a monte. Vogliamo controllare il più possibile prima di ottenere un pezzo fisico."
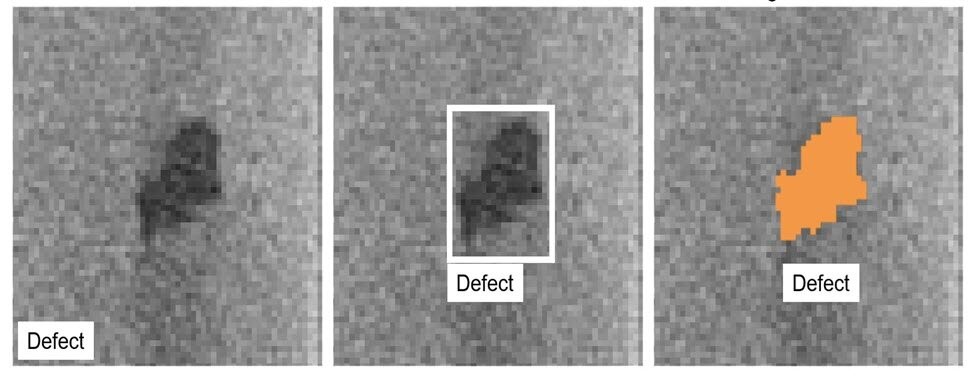
Figura 5. L'intelligenza artificiale e l'apprendimento automatico sono tecniche efficaci per etichettare, classificare i dati sulla qualità, localizzare i problemi e segmentare i difetti per identificarli e intervenire durante la verifica attraverso tomografia automatizzata. Immagine per gentile concessione di Volume Graphics
Volume Graphics ha aiutato TE Connectivity in questo processo di front-loading e looping dei dati con i suoi modelli di misura adattivi. I modelli possono classificare, localizzare e segmentare i difetti utilizzando l'IA e l'apprendimento automatico. Inoltre, automatizzano gran parte dell'analisi delle scansioni e acquisiscono le informazioni per i rapporti di misura. L'obiettivo di TE Connectivity è ridurre il tempo di analisi da 10 a cinque giorni.
Uno dei progetti del "ciclo classico di progettazione" di Stokowski era in corso poco prima dell'avvio del progetto di analisi digitale tomografica del 2014 che utilizzava il software Volume Graphics. Si trattava dello sviluppo di stampi e parti di una centralina motore. La centralina, proveniente dal settore automobilistico, contava più di 200 pin di collegamento elettrico ed era la prima del suo genere.
Stokowski afferma: "C'è voluto quasi un anno e più di dieci cicli di iterazione per raggiungere i risultati richiesti dal disegno. È stata una storia logorante e senza fine. E poi, solo tre anni e mezzo dopo, si è resa necessaria la prima sostituzione dei pezzi. Si può immaginare la reazione del team! "Oh mio Dio... avremo bisogno di un altro anno solo per effettuare il condizionamento e i loop di correzione", pensavano", sorride Stokowski.
"A quel punto avevamo già implementato il processo di misura digitale e abbiamo realizzato il progetto dello stampo in un unico ciclo", afferma.
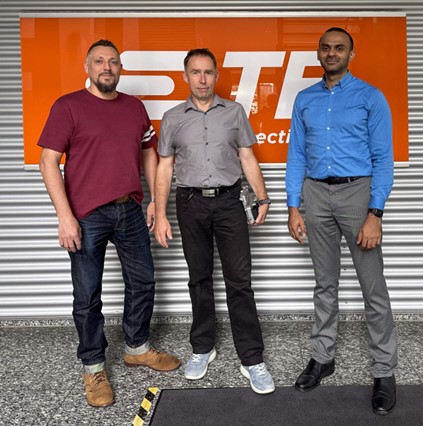
Figura 6. (Sinistra-Destra) Patrick Bertram, ingegnere capo della simulazione dello stampaggio; Alexander Stokowski, responsabile della divisione Engineering Transformation, con in mano il primo progetto di centralina misurato con la TC e digitalizzato; e Tabrez Ahmed Ajaz, responsabile COE GD metrology. Immagine per gentile concessione di TE Connectivity.
Obiettivo: riduzione dei tempi di sviluppo del 75%
Oggi TE Connectivity spera di ridurre il processo di sviluppo di stampi e pezzi al 25% del tempo impiegato in passato. Ci saranno sempre delle attività manuali, afferma Stokowski: un perfezionamento pratico del GD&T, o momenti di discussione su un problema, o la correzione di una difformità digitale nel "flusso" che collega i programmi. Non ci sono nemmeno le risorse necessarie per sottoporre ogni stampo alla Design of Experiments (DOE). Ma gli stampi più importanti dell'azienda utilizzeranno la DOE e tutti i nuovi stampi saranno elaborati con il software VGMETROLOGY.
Anche i fornitori stanno adottando questo nuovo approccio. Molti hanno acquistato propri sistemi di misura virtuali. Il 20-30% dei produttori di utensili esterni utilizza l'intero sistema digitale integrato. Altri si rivolgono alla scansione esterna e utilizzano il software internamente. Tutti i produttori di utensili eseguono il controllo della conformità dei materiali e le misure di base prima che TE Connectivity effettui un rapporto di misura completo all'interno del CoE.
Stokowski prevede che alla fine il processo di qualità di TE Connectivity sarà utilizzato da tutti i fornitori, ma questa previsione non è ancora a breve termine, poiché esistono barriere culturali e di costo sia per la misura GPS che per la misura virtuale. Nel frattempo, il suo team e il CoE lavoreranno verso un futuro processo "a pulsante", anche se si aspettano, per motivi pratici, che si applichi al "75% del nostro lavoro", afferma Stokowski.
Come risultato del loro approccio al miglioramento dei processi di qualità, TE Connectivity ha raggiunto molti progressi e traguardi:
- Tutti i nuovi pezzi stampati a iniezione sono implementati in MBD
- Il 100% dei pezzi stampati a iniezione viene scansionato e non ci sono più misure a contatto
- Le specifiche dei pezzi sono create in Creo secondo gli standard ISO-GPS e convertite
- L'integrazione tra il software Creo e VGMETROLOGY è diretta
- Il 75% di tutti i dati dei prodotti è veicolato tramite PMI
- Sono eseguite solo rilavorazioni isolate a causa dell'incompatibilità delle interfacce
Per la verifica finale dei pezzi TE Connectivity dispone di sei scanner in linea nella regione EMEA per i pezzi stampati a iniezione. Gli scanner e il software Volume Graphics cercano le dimensioni chiave e le aree target di un pezzo, piuttosto che l'intero componente, dopo il rapporto di misura. Qui entrano in gioco i costi e i tempi. Ma anche la progettazione virtuale, l'analisi e il collaudo dei pezzi in una fase così precoce della creazione, insieme ai controlli durante la verifica del primo articolo, garantiscono che la conformità sia stata rispettata e ricontrollata in fabbrica. L'azienda possiede 23 scanner in tutto il mondo, una licenza globale per Creo e suite complete del software di Volume Graphics. E gestisce un centro di competenza per l'integrazione e la distribuzione di queste tecnologie digitali.
La qualità è l'obiettivo finale
Le discussioni interne all'azienda in merito a quanto investire in tecnologia sono perenni e la contabilità che consente di analizzare i dati è raramente utilizzata appieno. Ma la qualità è il punto di arrivo per molte aziende e in particolare per il settore della produzione. La qualità è un valore di riferimento che attrae i clienti, li fidelizza e focalizza i team di tecnici su ciò che è importante e che ha un impatto così pervasivo sull'organizzazione.
"Gli strumenti di qualità e i sistemi digitali di TE Connectivity ci dicono molto sui nostri prodotti: come migliorarli, perché si comportano in un certo modo e come individuare e prevedere le variazioni", afferma Stokowski. "Nell'immediato, stiamo risparmiando tempo e costruendo ottimi prodotti che fanno progredire altri campi come quello della mobilità elettrica", afferma. "La misura virtuale e la digitalizzazione offrono uno scrigno infinito di tesori, se si sceglie di utilizzarli."